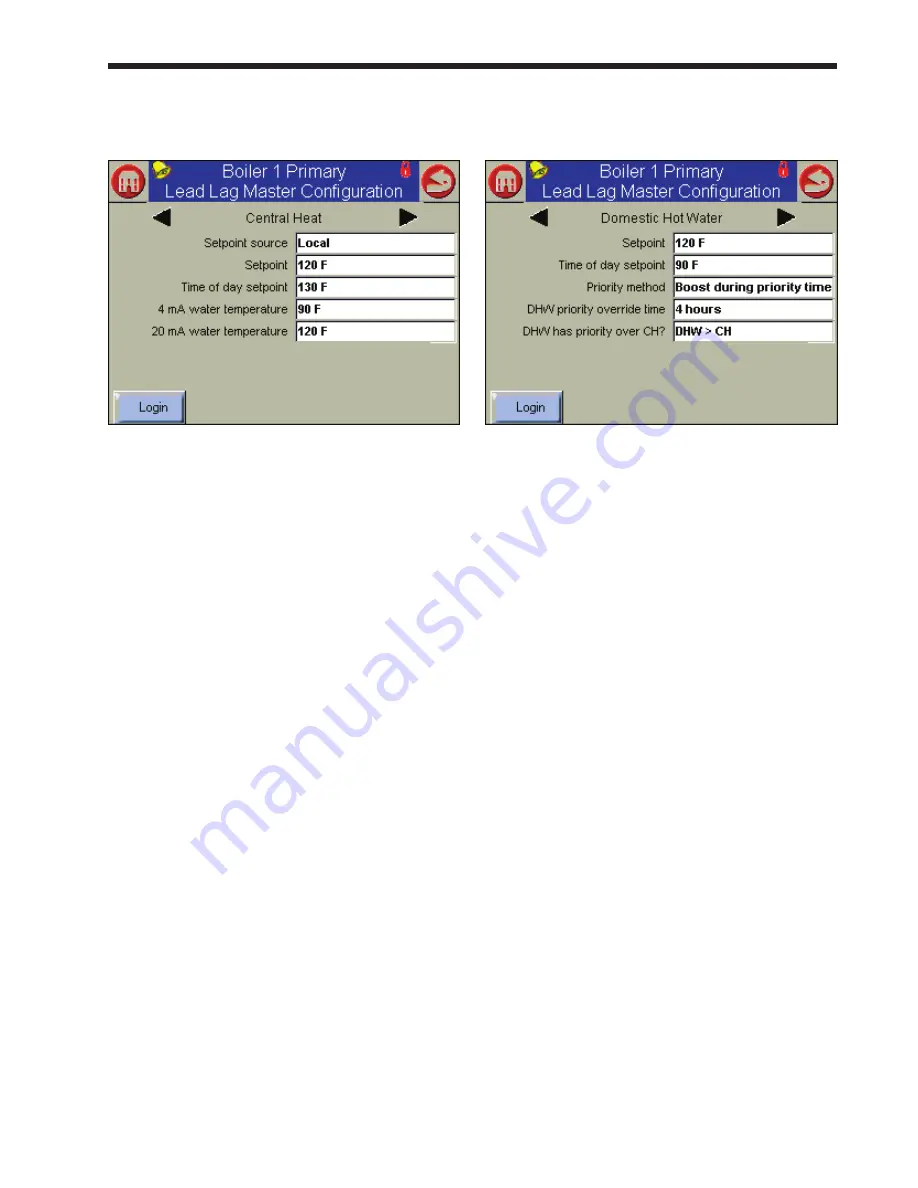
NeoTherm Boilers and Water Heaters
Page 69
8. Press the left-arrow or right-arrow until you see
the Central Heat screen (Fig. 87).
fig. 87 – Central Heat
Setpoint source -
This sets the source of the System sensor
input used to control the system. The
options here are Local and 4-20 mA.
(For instructions on setting up for a 4-20
mA input, see Job #5 in the section on
“Installation Options.”)
Setpoint -
This is the same as the LL CH Setpoint on
the Lead/Lag Master Configuration screen
(Fig. 85).
Time of day setpoint -
This is the same as the LL CH Time-Of-
Day Setpoint on the Lead/Lag Master
Configuration screen (Fig. 85). (See the
material on “About the ‘Time of Day’
Function at the end of this section)
4 mA water temperature -
If a 4 – 20 mA input is used to adjust the
setpoint, this entry sets the low limit of the
control range. (In the example shown here,
an input of 4 mA would result in a setpoint of
90°F.)
20 mA water temperature -
If a 4 – 20 mA input is used to adjust the
setpoint, this entry sets the high limit of the
control range. (In the example shown here,
an input of 20 mA would result in a setpoint
of 120°F.)
9. Press the left-arrow or right-arrow until you see
the Domestic Hot Water screen (Fig. 88).
fig. 88 – Domestic Hot Water
The arrangement for Domestic Hot Water can
be set up in several ways. For details, see the
section on “Lead/Lag Domestic Hot Water.”
DHW Setpoint -
This is the same as the DHW Setpoint on the
Lead/Lag Master Configuration screen.
DHW Time of day setpoint -
This is the same as the DHW Time-Of-
Day Setpoint on the Lead/Lag Master
Configuration screen. (See the material on
“About the ‘Time of Day’ Function at the end
of this section.)
DHW Priority method -
This determines the way the system gives
priority to the DHW demand (if DHW is
given priority on the bottom line of the
screen.)
DHW priority override time -
If Domestic Hot Water has priority (see
the next line below), this sets how long the
DHW loop will have priority before returning
to control by the Lead/Lag Central Heat
setpoint.
DHW has priority over CH? -
Choose Central Heating priority or Domestic
Hot Water priority.
Содержание NTV1000
Страница 2: ......
Страница 35: ...NeoTherm Boilers and Water Heaters Page 31 Fig 20 Ladder Diagram...
Страница 36: ...LAARS Heating Systems Page 32 Fig 21 Wiring Diagram...
Страница 37: ...NeoTherm Boilers and Water Heaters Page 33...
Страница 51: ...NeoTherm Boilers and Water Heaters Page 47 Fig 52 Connection Terminals...
Страница 130: ...LAARS Heating Systems Page 126 Fig 140 Machine Frame and Rear Panel 13 3 PARTS ILLUSTRATIONS...
Страница 131: ...NeoTherm Boilers and Water Heaters Page 127 Fig 141 Front Panel and Covers...
Страница 132: ...LAARS Heating Systems Page 128 Fig 142 Burners and Combustion Chambers...
Страница 133: ...NeoTherm Boilers and Water Heaters Page 129 Fig 143 Heat Exchanger Components Fig 144 Burner Detail...
Страница 134: ...LAARS Heating Systems Page 130 Fig 145 Electronic Components...
Страница 135: ...NeoTherm Boilers and Water Heaters Page 131 Fig 146 Condensate Trap Fig 147 Control Bezel...
Страница 136: ...LAARS Heating Systems Page 132 Fig 148 Flow Switch...
Страница 137: ...NeoTherm Boilers and Water Heaters Page 133 This page intentionally left blank...