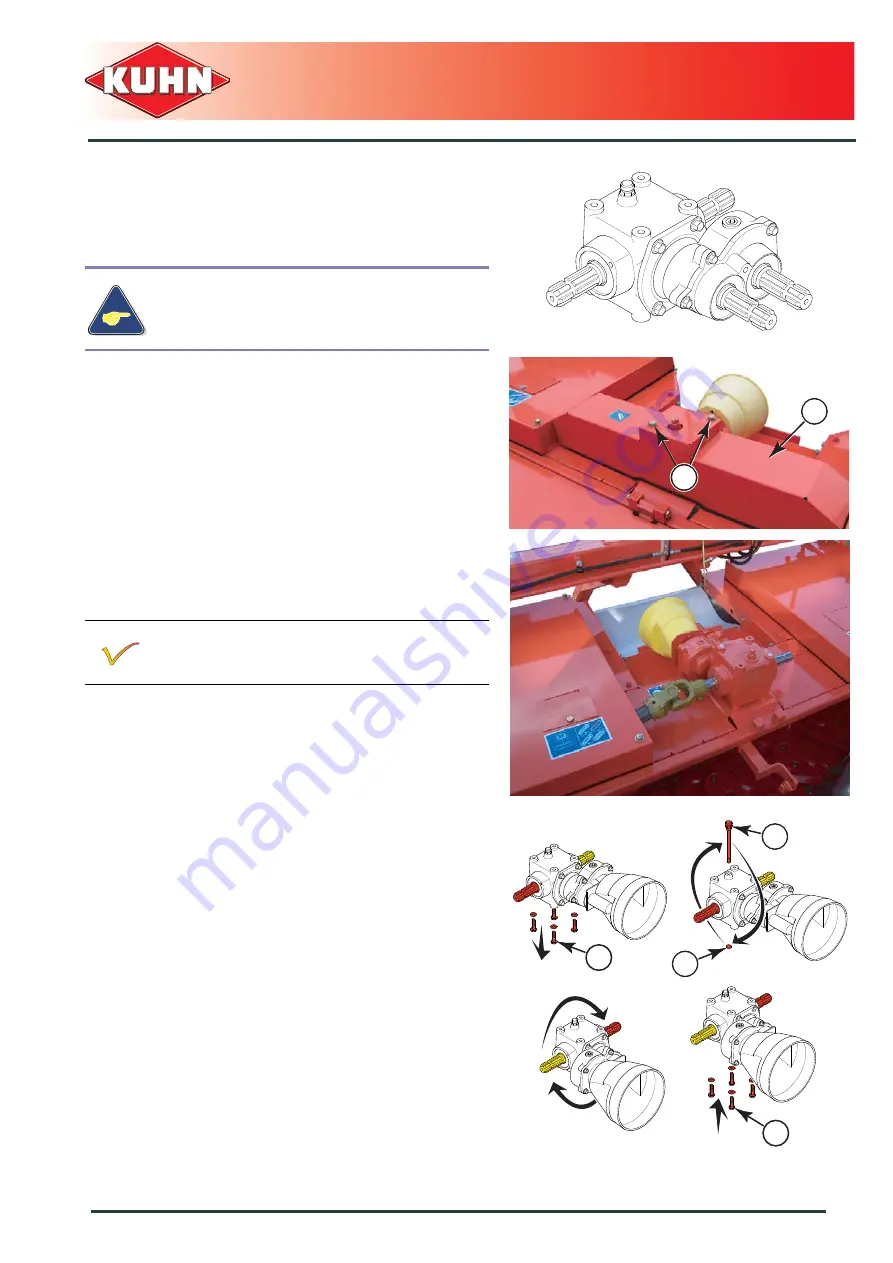
Putting into service
Disc mower
GMD702F
25
Central gearbox (540 min
-1
and 1000 min
-1
)
The machine can be driven with a PTO stub rotating
clockwise or counterclockwise.
If the outer disks of the cutterbar do not rotate inwards,
invert the central gearbox:
- Lower the mowing unit using the machine lift
cylinders.
- Lower the tractor's lift linkage to tension the check
chains.
- Remove 2 bolts (2)
- Remove guard (1).
- Remove the secondary PTO shaft from the central
gearbox.
- Remove the mounting bolts (3).
- Invert drain plug (4) and vent plug (5).
- Pivot central gearbox 180°.
- Reinstall the 4 mounting bolts (3):
• Torque to 12 daN m (89 lbf ft).
- Fit guard (1).
- Fit the 2 bolts (2).
The two outer disks of the cutterbar must
rotate inwards.
Tilt gearbox to prevent oil loss.
1
2
3
4
5
3