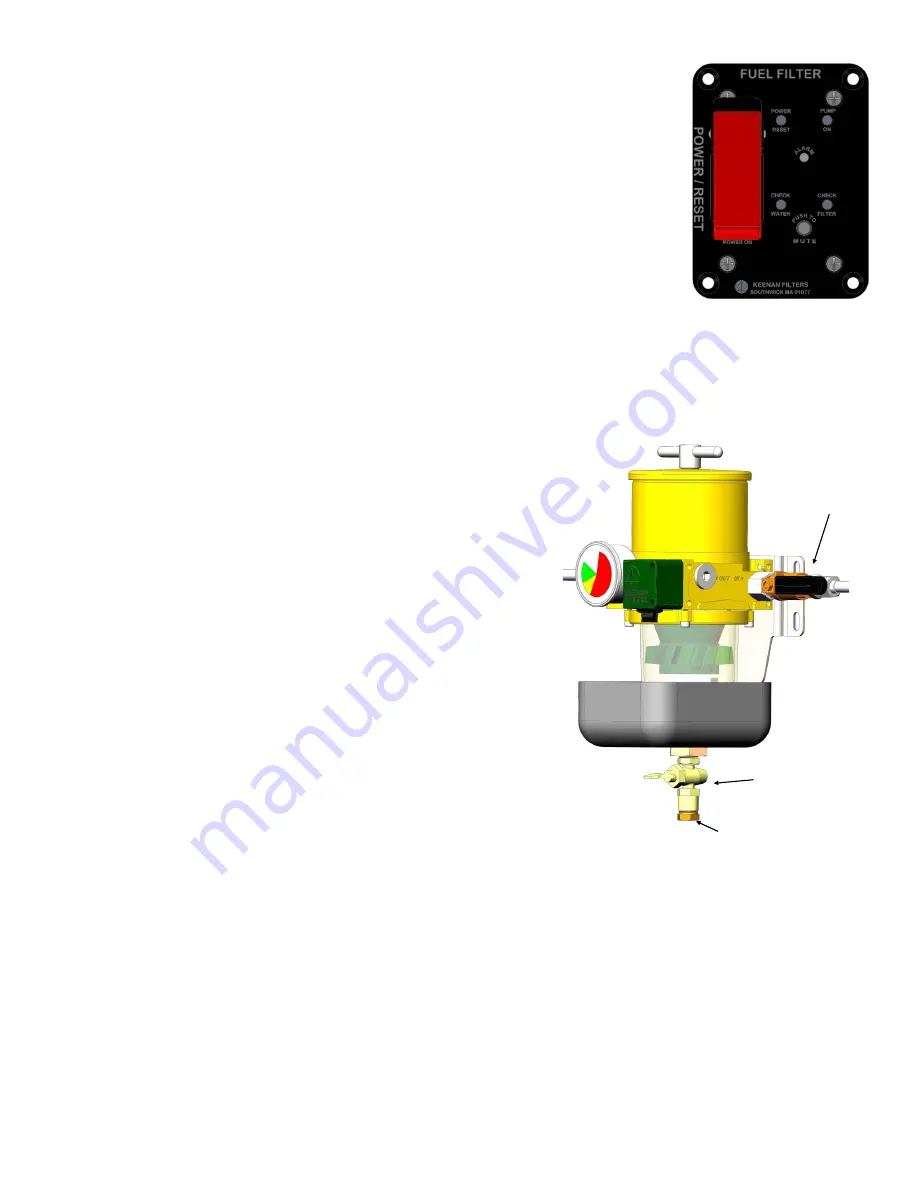
MK60SP 12/10/20 KEENAN FILTERS® by KTI Systems, Inc. www.keenanfilters.com
INLET SHUT OFF
VALVE
DRAIN VALVE
PLUG
MAINTENANCE AND INSPECTION
•
Routinely inspect the filter for leakage, damage and corrosion.
•
Change the filter element minimally on an annual basis, or when vacuum starts to increase.
•
Perform the OPERATIONAL TEST before operation or during routine inspections. The
OPERATIONAL TEST checks the warning system for operation and also the integrity of the fuel
system for air leaks.
KP300 CONTROL PANEL OPERATION
The control panel will give the operator indication and audible warning if the filter
is starting to clog (high vacuum) or more than 5.5 ounces of water is present in
the online fuel bowl. The operator can also MUTE the audible so it is not
distracting.
Normally a clogged filter or water warning will take many hours of operation to
trip the alarm, so an engine shut down will not happen immediately. This gives
the operator some time to prepare for shutting down the engine and servicing
the filter. You may need to reset the system after draining water, this can
be done from the panel using the power reset switch.
Note: If the water alarm sounds after fueling or switching tanks the operator may need to shut down the
engine quickly because of possible water contamination. Check the fuel bowl for a rising water level.
DRAINING WATER FROM BOWL
1. Engine must be off to service filter.
2. Close fuel inlet shut-off valve or tank supply.
3. Draining Procedure:
•
GRAVITY METHOD
Remove drain valve plug and remove lid assembly. Position
a container to catch the water and fuel.
Slowly open the filter drain valve until water is drained.
Close drain valve and re-install drain valve plug.
Fill filter with clean fuel. Reinstall lid assembly. Open fuel
inlet shut-off valve.
4. Perform OPERATIONAL TEST.
PAGE 17