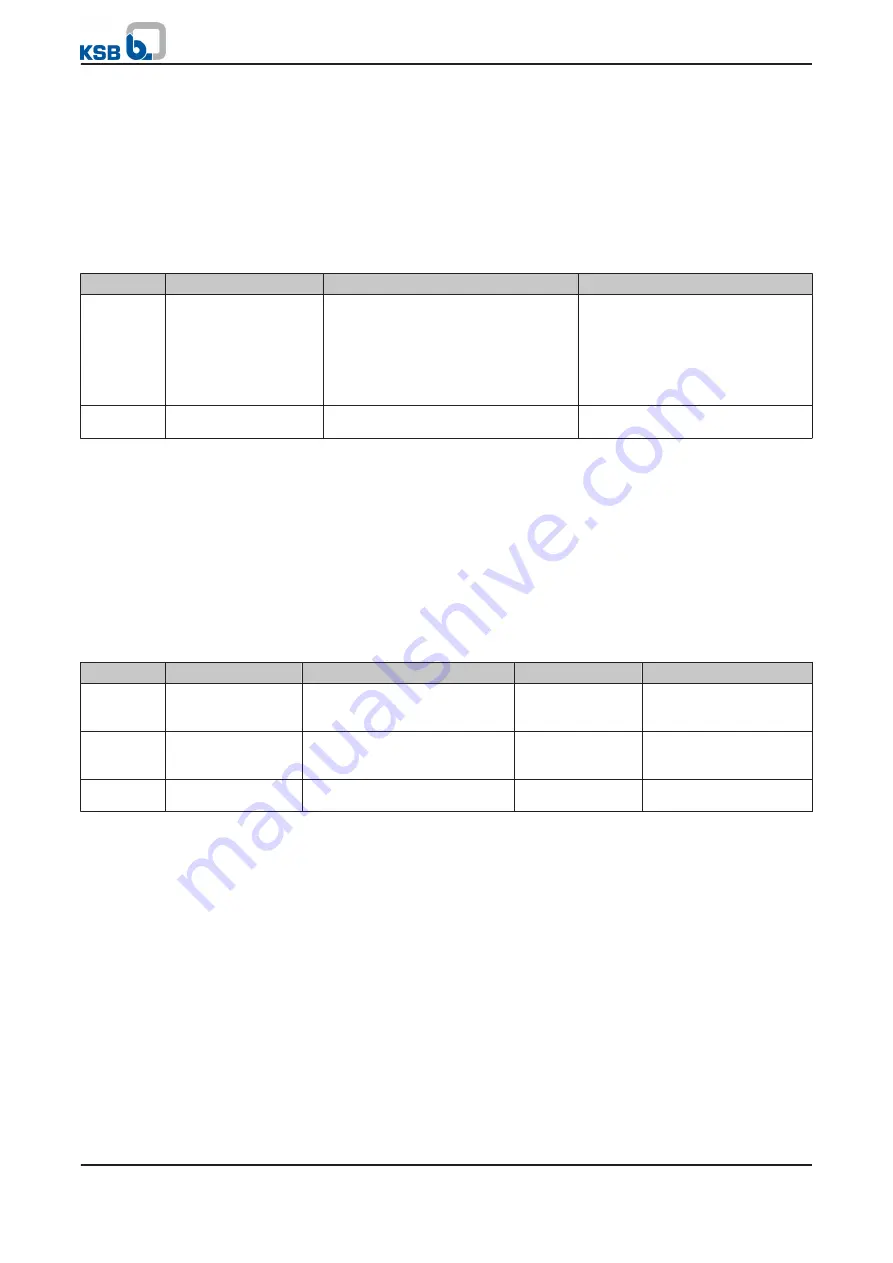
In a multiple pump configuration, only the No Function and Stop & Trip functions are
supported. If another function is selected all the same, this will have the same effect
as No Function. This applies only to the respective pumps and not to the entire
system. If two separate sensors are used, the system automatically switches to the
sensor of the auxiliary main pump when the sensor of the main pump fails.
▪
The failure of the first sensor is not indicated.
▪
The auxiliary main pump automatically becomes the main pump.
▪
The previous main pump automatically becomes the auxiliary main pump.
Table 71: Parameters for cable integrity monitoring
Parameter Description
Possible settings
Factory setting
3-8-1-2
Live zero function
No Function
Stop
Min. Motor Speed
Max. Motor Speed
Freeze Output
Warning
Stop & Trip
No Function
3-8-1-1
Time delay after live
zero detection
0, 1..60 (s)
3 s
7.2.1.7
Suppressing a frequency range
In the case of critical system conditions, a frequency range can be suppressed to
prevent resonance. An upper and a lower frequency limit value can be parameterised
for this purpose. During (closed-loop or open-loop) operation, the system jumps to
the upper value once it has reached the lower frequency. In closed-loop control
mode, the suppressed frequency should lie outside the PumpDrive's correction
frequency range. Otherwise sudden PumpDrive speed changes can lead to pressure
fluctuations. First the upper limit to prevent resonant frequencies Hi Bypass Freq
(
3-3-7-2
) and then the lower limit to prevent resonant frequencies Lo Bypass Freq
(
3-3-7-1
) have to be entered.
Table 72: Parameters for suppressing a frequency range
Parameter Description
Possible settings
Reference to
Factory setting
3-3-7-1
Lower limit to
prevent resonant
frequencies
0 to Hi Bypass Freq
(3-3-7-2)
[%]
3-11-4-1
0
3-3-7-2
Upper limit to
prevent resonant
frequencies
Lo Bypass Freq
(3-3-7-1)
up to
Maximum Output Frequency
(3-11-4-1)
(%)
3-11-4-1
0
3-11-4-1
Maximum Output
Frequency
1..70 (Hz)
-
50 Hz
7.2.1.8
Characteristic curve control based on the effective motor power
Using the power measurement function of PumpDrive, the pump characteristic curves
can be monitored based on the motor input power. Limit values for activation of the
monitoring function referred to pump characteristics and pump input power must be
defined. Characteristic curve control is used for starting and stopping pumps in a
multiple pump configuration.
Monitoring the effective power (pump off-design conditions)
Parameters
(3-6-4-1)
to
(3-6-4-10)
and parameters
(3-6-1-2)
and
(3-6-1-3)
can be used
to define frequency-dependent power limit values in order to protect the pump(s)
against impermissible low flow and high flow (overload) conditions and limit the
speed range. The frequency dependency of the upper/lower limit value is described
via two points in the frequency/power diagram which can be derived directly from
the H/Q selection chart. A linear, square or cubic limit value characteristic curve can
be selected between these points. This selection is made via parameters
(3-6-4-3)
and
(3-6-4-8)
Characteristic curve
control (P
min
, P
max
)
7 Commissioning/shutdown
74 of 162
PumpDrive