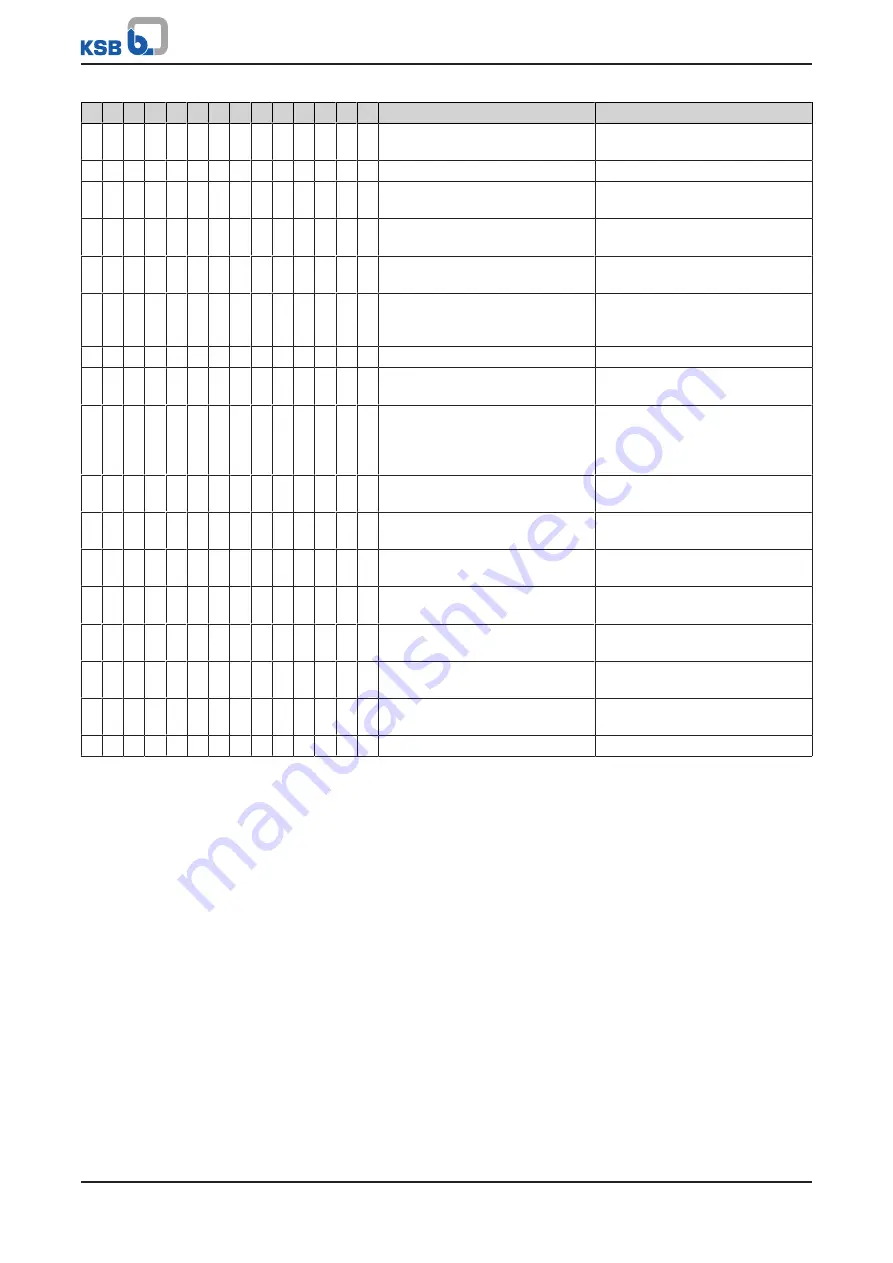
9 Trouble-shooting
35 of 44
Hya-Duo D FL
A B C D E
F G H
I
J
K L M N Possible cause
Remedy
2)
-
-
-
-
-
-
-
✘
-
-
✘
-
-
- Defective accumulator
Check integrity. Replace if
necessary.
-
-
-
-
-
-
✘
-
-
-
-
-
-
- Defective mechanical seal
Replace.
✘
-
-
-
-
-
-
-
-
-
-
-
-
- Suction-side pressure switch set
incorrectly or defective
Check setting.
-
-
✘ ✘ ✘
-
-
✘ ✘ ✘
-
-
-
- Check valve defective
Check. Replace sealing element if
necessary.
-
-
-
-
✘
-
-
-
✘ ✘ ✘
-
-
- Water extraction higher than
stated in the purchase order
Contact the manufacturer.
-
-
-
-
-
-
-
-
✘
-
-
-
-
- Motor protection switch
triggered or set incorrectly /
pump seized
Compare setting with the
motor's rating plate data.
-
-
-
-
-
-
-
-
-
-
✘
-
-
- Delay setting too short
Check setting.
-
✘
-
-
-
-
-
-
-
-
-
-
-
- Mains supply interrupted
Check. Remedy defect. Check
fuse.
-
✘
-
-
-
-
-
-
-
-
-
-
-
- Main fuse on (owner-supplied)
distribution board loose or
blown; fuses possibly too small or
too fast
Check fuses. Replace if necessary.
Measure the motor current.
-
✘
-
-
-
-
-
-
-
-
-
-
-
- Phase failure
Check individual phases; replace
fuse if necessary.
✘
-
-
-
-
-
-
-
-
-
-
-
-
- Accumulator empty / float switch
defective or not connected
Check. Remedy defect if
applicable.
-
-
-
-
-
-
-
-
-
✘
-
✘
-
✘
Broken wire in the input line of
the pressure switch
Check. Remedy defect if
applicable.
-
-
-
-
-
-
-
-
-
✘
-
✘
-
✘
Broken wire in the input line of
the remote ON/OFF system
Check. Remedy defect if
applicable.
-
-
-
-
-
-
-
-
-
✘
-
-
✘ ✘
Short circuit in the input line of
the pressure switch
Check. Remedy defect if
applicable.
-
-
-
-
-
-
-
-
-
✘
-
-
✘ ✘
Short circuit in the input line of
the remote ON/OFF system
Check. Remedy defect if
applicable.
-
-
-
-
-
-
-
✘
-
-
-
-
-
- Solenoid valve for minimum flow
not actuated
Check. Remedy defect if
applicable.
-
-
-
-
-
-
-
-
-
-
✘
-
-
- Leakage on the discharge side
Check
Содержание Hya-Duo D FL Series
Страница 1: ...Fire fighting System Hya Duo D FL From series 2014w33 Installation Operating Manual...
Страница 43: ......