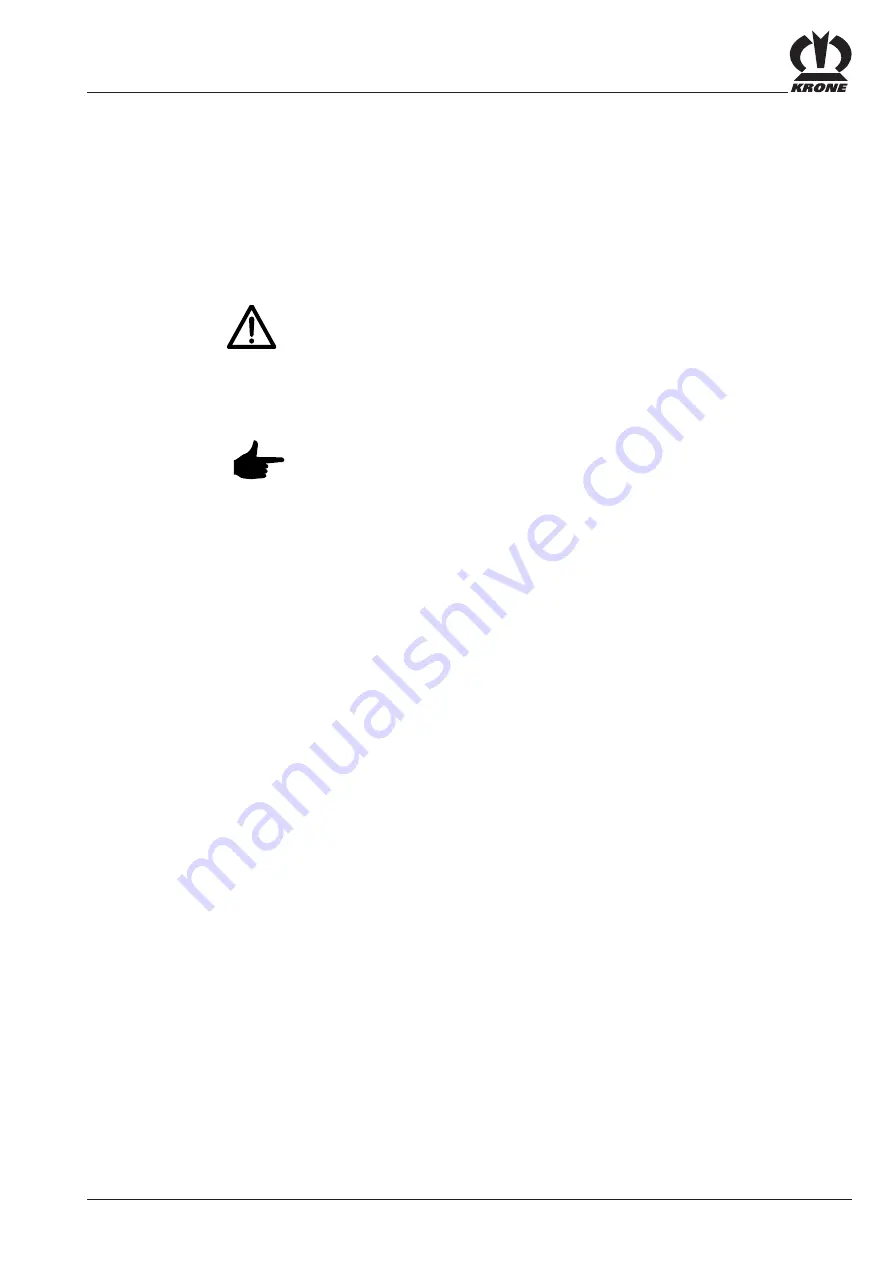
II - 1
Safety
2
Safety
2.1 Identifying Safety Instructions in
the Operating Manual
The safety instructions contained in this manual, which
could result in personal injury if not followed, are identified
by the general danger sign:
safety sign in accordance with DIN 4844 - W9
General function instructions are indicated as follows:
Instructions which are attached to the machine need to be
followed and kept fully legible.
2.2 Safety Instructions and Accident
Prevention Regulations
2.2.1 Personnel Qualification and Training
The rotary swather must only be used, maintained and
repaired by personnel who are acquainted with the
machine and have been informed of the dangers involved.
The operator must precisely define the areas of
responsibility and competence and monitor the personnel.
Should personnel lack the required know-ledge they must
receive the required training and instruction. The operator
must also ensure that the contents of this operating
manual have been fully understood by the personnel.
Repair work not described in this operating manual should
be completed by authorized service centers only.
2.2.2 Failure to Follow the Safety
Instructions
Failure to follow the safety instructions could result in
personal injury and environmental hazards as well as
damage to the machine. Failure to follow the safety
instructions could result in the forfeiture of any claims for
damages.
Failure to follow the safety instructions could, for
example, result in the following hazards:
– risk to persons by failure to secure the working area
– breakdown of important machine functions
– failure of prescribed methods for repair and
maintenance
– risk to persons due to mechanical and chemical
effects
– damage to the environment due to leaking hydraulic
oil
2.2.3 Working in a Safety Conscious
Manner
Follow the safety instructions included in this operating
manual, existing accident prevention rules and any
internal work, operating and safety rules set out by the
operator.
The safety and accident prevention regulations of the
responsible professional associations are binding.
Observe the safety instructions provided by the vehicle
manufacturer.
Observe the applicable traffic laws when using public
roads (for example, in Germany, the Road Traffic Type
Approval Law and Road Traffic Law).
2.3
Safety Instructions and Accident
Prevention Regulations
1. Please follow all generally applicable safety and
accident prevention regulations in addition to the
safety instructions contained in this manual!
2. The attached warning and safety signs provide
important information for safe operation. Pay
attention to these for your own safety!
3. When using public roads, make sure to observe
the applicable traffic regulations!
4. Make sure that you are familiar with all equipment
and controls as well as their functions before you
begin working with the machine. It is too late to
learn this when you are operating the machine!
5. The user should wear tight fitting clothes. Avoid
wearing loose or baggy clothing.
6. Keep the machine clean to prevent danger of fire!
7. Before starting or moving the machine, make
certain that nobody is in the vicinity of the
machine! (Watch for children!) Make sure that you
have a clear view!
Содержание Swadro 35
Страница 4: ...Foreword ...
Страница 20: ...III 6 Operating preparations ...
Страница 32: ...VIII 2 Winter storage ...
Страница 34: ...IX 2 Start up after winter storage ...
Страница 37: ...X 3 ...