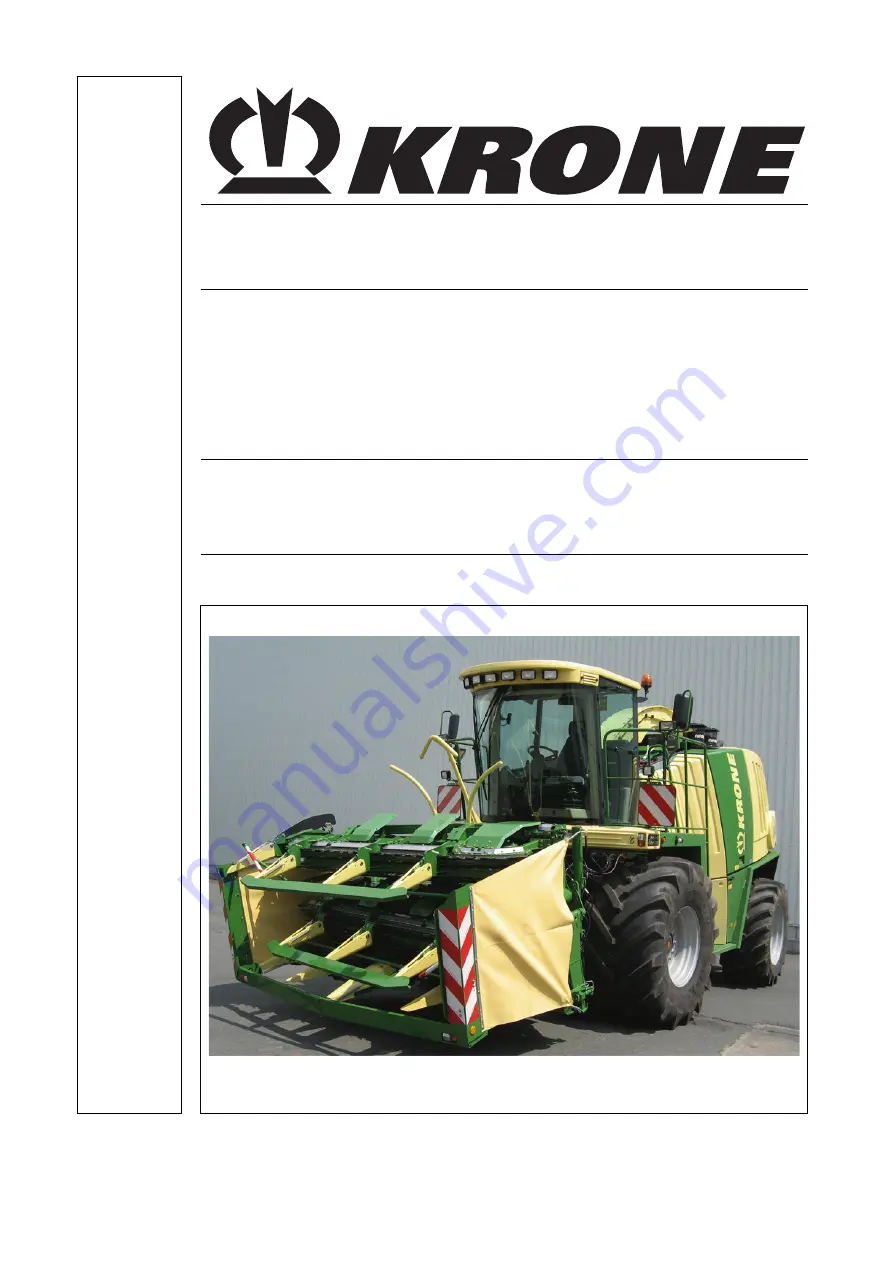
O
r
ig
in
a
l
o
p
e
r
a
t
in
g
i
n
s
t
r
u
c
t
io
n
s
Maize header
<v>T - Typ1</v>
EasyCollect 753
</v>
<v>T - Typ2</v>
EasyCollect 903
</v>
<v>T - Typ3</v>
EasyCollect 1053
</v>
<v>T - Typ4</v> </v>
<v>T - Typ5</v> </v>
<v>T - Typ6</v> </v>
<v>T - Typ7</v> </v>
<v>T - Typ8</v> </v>
<v>T - Typ9</v> </v>
<v>T - Typ10</v> </v>
(
<v>T - ab Masch.-Nr.</v>
from serial no.
</v>
: 798 561)
<v>T - Bestell-Nr.</v>
Order no.
</v>
: 150 000 106 02 us
<v>B - Titelbild</v>
</v>
07.04.2010
Содержание EasyCollect 1053
Страница 31: ...Commissioning 31 4 5 Attaching the discharge extension Fig 16 ...
Страница 52: ...Operation 52 This page has been left blank deliberately ...
Страница 83: ......