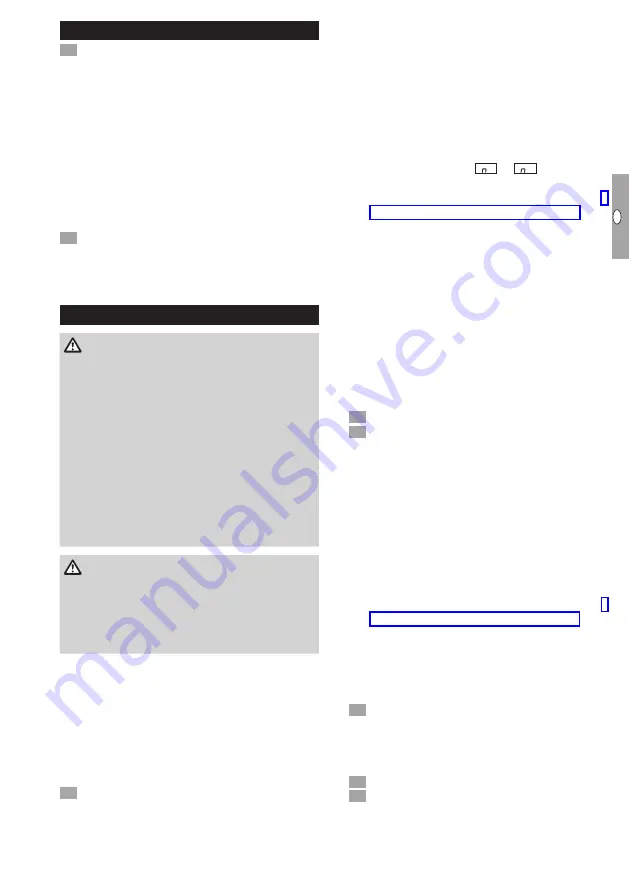
GB-3
GB
F
NL
I
E
Wiring
Disconnect the system from the electrical power
supply.
▷
Use only cable and plug components which
comply with the appropriate fieldbus specifica-
tions.
▷
Use shielded RJ45 plugs.
▷
Cable length: max. 100 m between 2 subscribers.
▷
PROFINET installation guidelines, see
www.profibus.com.
▷
Ethernet installation guidelines, see
www.odva.org.
▷
Installation of the communications network pur-
suant to IEC 61918.
Connect the BCM 400 to the fieldbus on an
automation system.
▷
Protect the communications network against
unauthorized access.
Commissioning
WARNING
Risk of explosion! Do not enable the BCM and
control unit (BCU) for operation until the parameter
settings and wiring are correct and the faultless
processing of all input and output signals has been
ensured.
In the event that the bus communication is faulty or
interrupted, or the communications data is invalid,
or during initialization, the signals received by the
controller are interpreted as “0”. If the control unit
is activated using the inputs at the terminals dur-
ing this time, the normal program runs. Be sure
to take the settings of parameters A085 to A089
into account.
WARNING
Danger through uncontrolled burner start.
The control signals for start and external air valve
have an OR link between the bus and input termi-
nals. The BCU may start the burner if there is an
active signal on the bus or terminal.
Depending on the bus module version (BCM..B2 or
BCM..B3), fieldbus communication can be config-
ured using the engineering tool of the automation
system or using BCSoft.
BCM..S
can only be commissioned using BCSoft.
Further information can be found in TI BCU 46x or
BCU 480.
▷
The BCSoft operating instructions and software
can be downloaded from www.docuthek.com.
Check the code switch settings (001 to FEF) on
the BCM for communication between BCSoft
and the control unit via Ethernet.
▷
Each code switch setting combination may only
exist once within the fieldbus system.
▷
Each device name/network name and each IP
address may only be allocated once within the
fieldbus system.
▷
PROFINET:
a device within the fieldbus system
can be identified using the subscriber flash test
(display shows
00
with alternately highlighted
segments).
▷
For instructions on commissioning the control
unit, see operating instructions “Burner control
unit BCU 46x, 480”.
▷
If the fault message
1
to
4
flashes in the
control unit’s display, fieldbus communication
cannot be commissioned, see also page 4
(Assistance in the event of malfunction). The
control unit can continue to be operated via its
digital inputs. Be sure to take the settings of
parameters A085 to A089 into account.
BCM..B (PROFINET)
▷
All the device-specific parameters for the control
unit (BCU) are saved in the device master data
file (GSD): download the device master data file
(GSD) from www.docuthek.com.
▷
Read the GSD file into the engineering tool of the
automation system and complete the network
configuration.
▷
The steps required for this are described in the
instructions for the engineering tool.
Connect voltage to the BCU.
Configure the bus communication.
▷
Using the engineering tool of the automa-
tion system:
enter the device name for the
control unit.
▷
Using BCSoft:
enter the network name, IP ad-
dress, subnet mask and standard gateway for
the control unit.
▷
Only when the device name/network name
has been entered, does the control unit receive
unique identification in the PROFINET IO system.
▷
On the control unit, parameter A080 must be set
to 1 or 2 so that a device name/network name
can be entered for the BCM, see also page 4
(Fieldbus configuration (parameter A080)).
BCM..B (EtherNet/IP)
▷
All the device-specific parameters for the con-
trol unit (BCU) are saved in the electronic data
sheet file (EDS): download the EDS file from
www.docuthek.com.
Read the EDS file into the engineering tool of the
automation system and complete the network
configuration.
▷
The steps required on the controller are described
in the instructions for the engineering tool.
Connect voltage to the BCU.
4
Configure the bus communication.
▷
Enter the following data via the engineering tool
of the automation system or BCSoft: network
name, IP address, subnet mask and standard
gateway for the control unit.