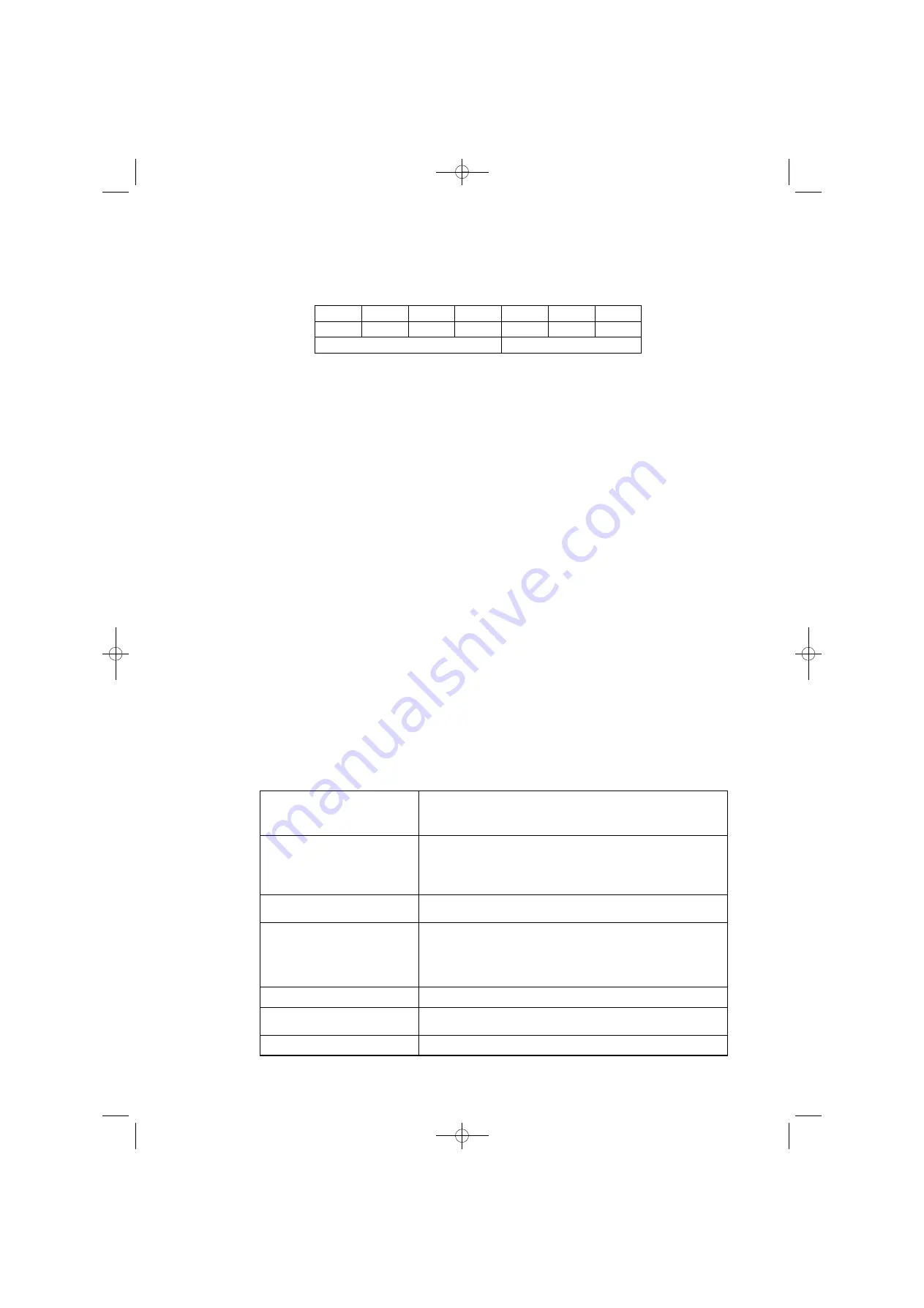
32
•
Schematic overviews of the CG32 numbers can be found in paragraph 4.2 (non-Ex i signal
I/O connections) and 4.3 (Ex i signal I/O connections). The overviews do not show all details.
The exact connection diagram for a specific MFC 300 converter can be found on the sticker
inside the cover of the connection compartment.
•
F
Fo
orr u
us
se
e iin
n G
Ga
as
s H
Ha
azza
arrd
do
ou
us
s A
Arre
ea
as
s:: The chosen cable glands must have the appropriate type
of protection for the terminal compartment, that is increased safety (Ex e) or flameproof
enclosure (Ex d). They MUST be suitable for the conditions of use and correctly installed.
•
The flowmeter with an Ex e terminal compartment is supplied ex-factory with two Ex e cer-
tified cable glands and one Ex e stopping plug.
•
The flowmeter with an Ex d terminal compartment is supplied ex-factory one Ex d stopping
plug and two temporarily plugs. The two temporarily plugs – only for transport and storage
– must be replaced by suitable Ex d certified glands, plugs or conduit accessories before
the flowmeter is taken into service.
•
Unused openings must be closed by suitable certified plugs
•
The wiring of the compact flowmeter has to conform to the requirements specified in the
relevant national or regional standard for electrical installations in hazardous areas, e.g.
IEC/EN 60079-14. From this standard section 9 (Wiring systems) is valid for all types of
protection. Section 10 (additional requirements for type of protection “d” – Flameproof
enclosures), section 11 (additional requirements for type of protection “e” – Increased safe-
ty) and section 12 (additional requirements for type of protection “I” – Intrinsic safety) are
valid for Ex e, Ex d or Ex i connection compartments respectively.
•
Tighten teriminals to a torque setting of 0.7 Nm.
•
The compact flowmeter must always be included in the equipotential bonding system of the
hazardous area. This can be achieved internally – by means of the PE conductor of the
mains system connected to the internal PE clamp – or externally – by means of a separate
equipotential bonding conductor connected to the external PE clamp under the converter
housing. A separate bonding conductor must have a cross sectional area of at least 4 mm
2
.
4.2 Non-Ex i signal I/O connections
The following non-intrinsically safe signal inputs/outputs are available:
The exact I/O-configuration for circuits A, B, C and D is order-specific and can be determined by the
CG32 number shown on the converter - check the data on the back of the MFC300 electronic unit.
The CG32 number contains 10 characters of which the last three (XYZ) determine the I/O con-
figuration (I/O circuits):
CG32
*
*
*
X
Y
Z
pos 1.. 4
5
6
7
8
9
10
determine I/O circuits
I/O PCB
Input/output functions,
Un
<
32 V DC, In
<
100 mA
Um = 253 V
Basic I/O
Current Output active and passive, with HART
Status Output / Control Input
Status Output
Pulse / Status Output
Modular I/O
Current Output, active or passive, with HART
Pulse / Status Output, active or passive, highC or Namur
Modular carrier with 1 or 2 I/O
modules
Each module: 1 out of following 3 in/output functions:
•
Current Output, active or passive
•
Status / Pulse Output, active or passive, highC or Namur
•
Control Input, active or passive, highC or Namur
Profibus DP I/O
Profibus-DP, active
Fieldbus I/O
Profibus-PA or
Foundation Fieldbus
RS485 Modbus
Modbus with or without termination
AD OPTIMASS 300_010 Haz Areas Rev 01.qxp 05/03/2014 13:25 Page 32