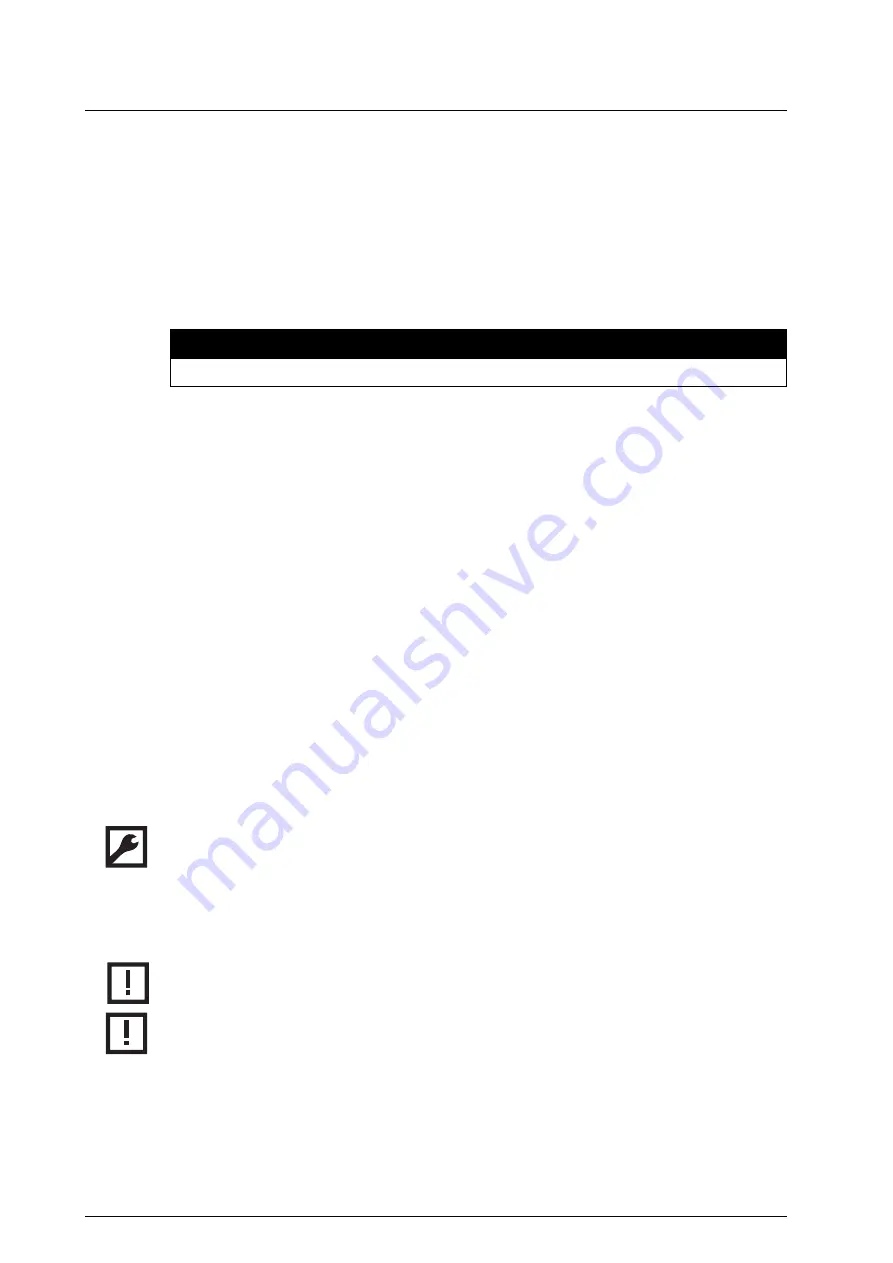
Operating Instructions
OIO 15en Edition 2020-05
19
Unpacking and checking the state of delivery
Transportation, storage and disposal
Transportation, storage and disposal
Unpacking and checking the state of delivery
1. On delivery unpack the KRAL flowmeter and check for damage during transportation.
2. Report damage during transportation immediately to the manufacturer.
3. Store the supplied pick ups and temperature sensors for the installation.
4. Dispose of packing material in accordance with the locally applicable regulations.
Transportation
Safety instruction for transportation
Transporting the flowmeter
Depending on the locally applicable regulations, Series OME flowmeters can be transported either
manually or using suitable lifting gear.
Storage
As a result of the calibration, the internal components of the flowmeter are wetted with calibration fluid
that has a preservative effect. In addition, a special anticorrosive agent is sprayed onto the interior of the
devices before being dispatched. The connections of the flowmeter are fitted with protective caps.
Unless otherwise specified, the external parts of the flowmeters are anodized. The preservation applied
at the factory will protect the flowmeter for up to six weeks, if it is stored in a dry and clean location. The
manufacturer offers a long-term preservation for storage times of up to 60 months: The flowmeter is
additionally packed in hermetically sealing anti-corrosion paper.
Preservation
Preservation has to be carried out in the following cases:
□
Standard delivery:
For storage periods exceeding six weeks and in case of adverse storage
conditions such as high humidity, salty air, etc.
□
Delivery with long-term preservation:
If the packaging has been opened or damaged
Preserving the flowmeter
1. Close a connection of the flowmeter with a blind flange.
2. Place the flowmeter vertically.
3. Fill non-corrosive and resin-free oil up to approx. 1 cm under the connection at the top, while turning
the measuring unit slowly, that also the measuring unit is wetted.
4. Close the connection with a blind flange.
After about 6 months storage check the oil level in the flowmeter and if necessary top up oil.
Notice:
Store the preserved flowmeter cool and dry and protect it against direct sunlight.
Notice:
After a longer storage time we recommend a re-calibration of the flowmeter, see "Re-calibration of the
flowmeters", page 28.
Pay attention to the following when transporting the flowmeter:
□
Lift and transport the flowmeter in accordance with the locally applicable regulations.