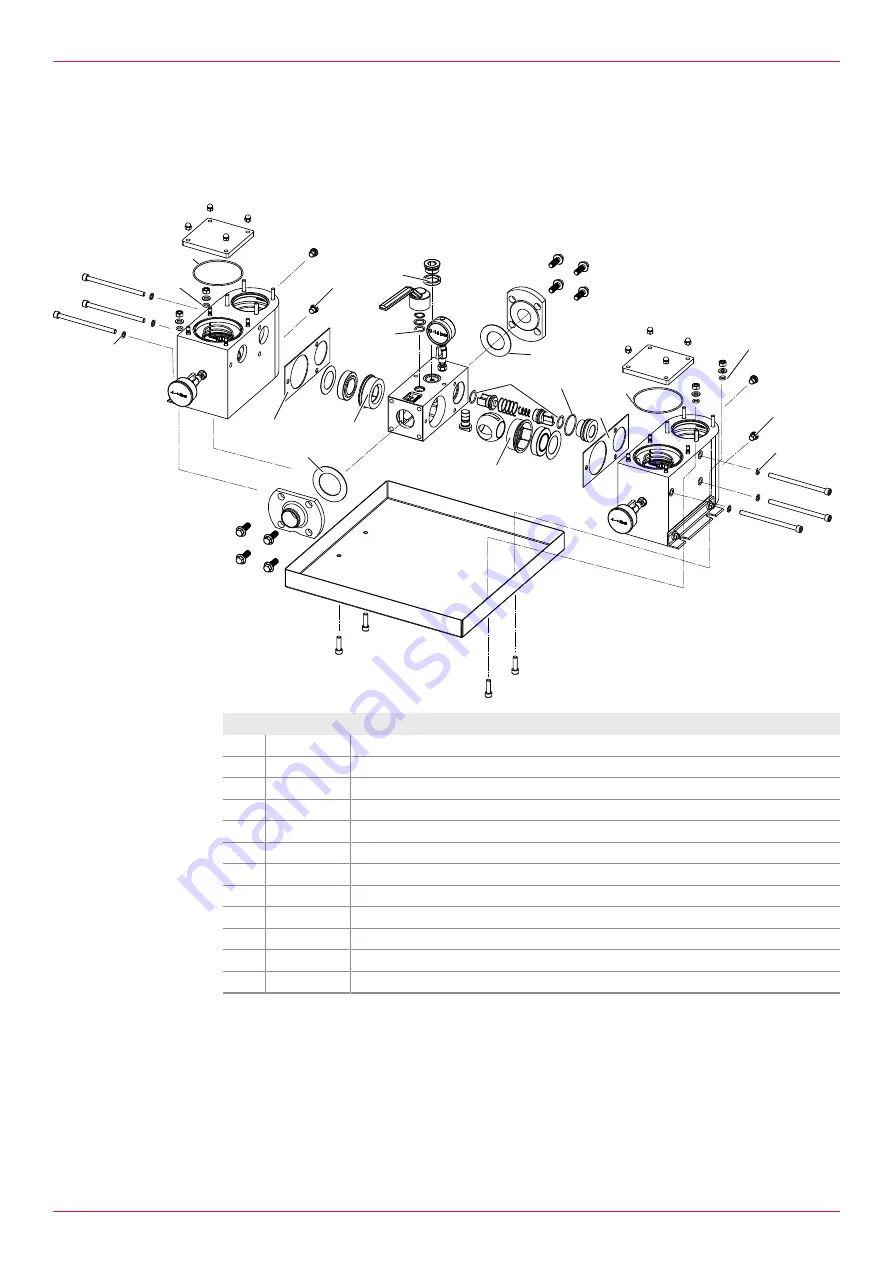
16 Spare parts
16.2 Maintenance kits
16.2 Maintenance kits
16.2.1
Maintenance kit sealing kit pump station (DL3/DL4/DS3/DS4)
Notice
The maintenance kit contains only the numbered parts and is only supplied complete.
055.2
222
456
735.1
739.5
739.1
739.2
739.4
739.3
729.1
729.2
739.2
908.1
908.1
735.1
739.1
456
222
Qty.
Item No.
Part
1
055.2
Seal ring
2
222
Flat gasket
2
456
Molded gasket
1
729.1
Flat gasket
1
729.2
Flat gasket
6
735.1
Copper seal
2
739.1
O-ring
4
739.2
O-ring
2
739.3
O-ring
1
739.4
O-ring
1
739.5
O-ring
4
908.1
Screw plug
Tab. 21: Maintenance kit sealing kit pump station (DL3/DL4/DS3/DS4)
50
OID 06en-GB Edition 2019-11
Operating instructions