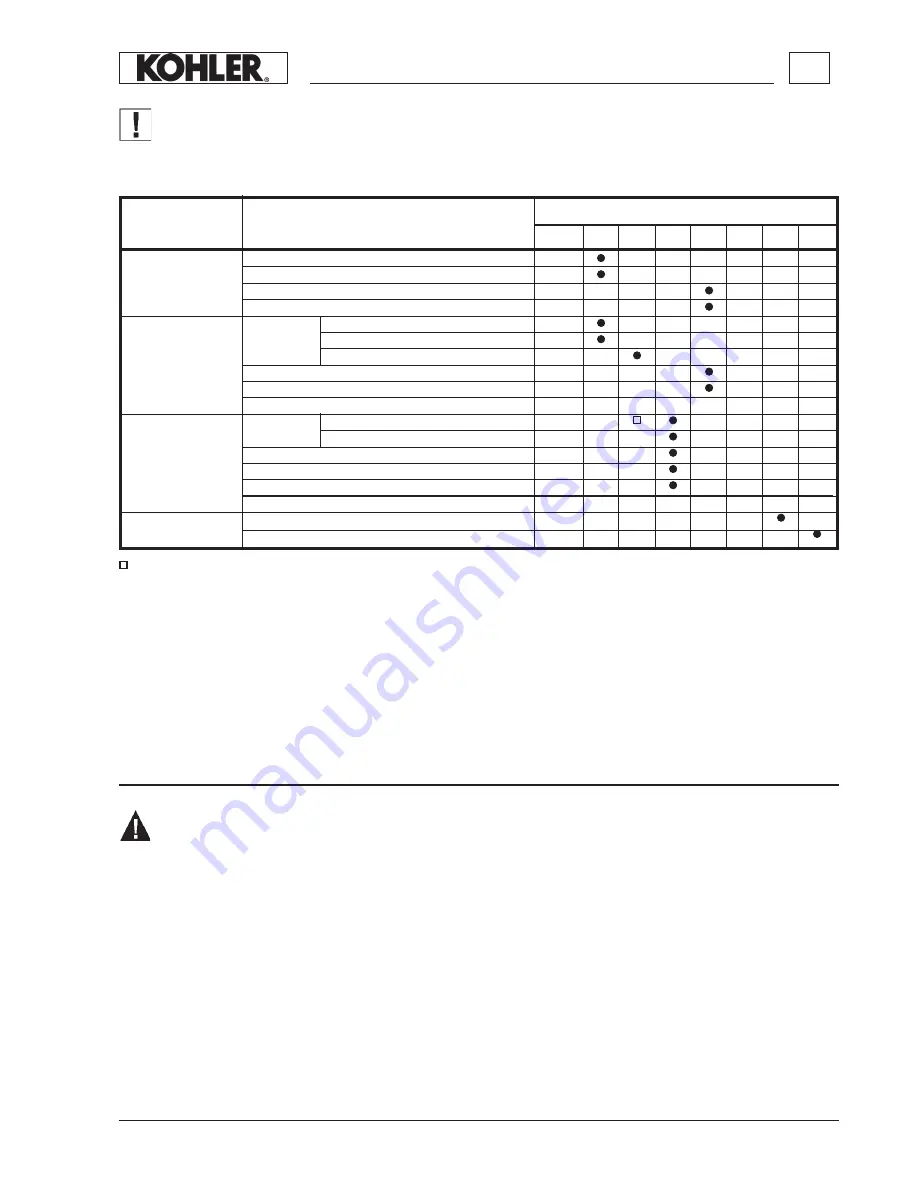
- 15 -
KD 477-2 Workshop Manual_cod. ED0053029370_
1° ed
_ rev.
00
VIII
(*)
(*)
(**)(***)
(x)
(xx)
8
50 200 300 500 2500 5000
Failure to carry out the operations described in the table may lead to technical damage to the machine and/
or system
First replacement
(*)
Under severe working conditions, clean daily.
(**)
Under extremely dusty conditions, change every 4-5 hours.
(***) See recommended oil type.
(x)
The partial overhaul includes the following operations: valve and seat lapping, injector and injection pump overhaul,
injector projection check, fuel injection spark advance check, check of the harmful area between head and piston,
camshaft and crankshaft end float check, tightening of bolts.
(xx) The general overhaul includes - in addition to all partial overhaul - the following procedures: cylinder and piston repla-
cement, seat, guide and valve refacing, crankshaft replacement or grinding, bench bearing and connecting rod replace-
ment.
To avoid explosions or fire outbreaks, do not smoke or use naked flames during the operations.
Fuel vapours are highly toxic. Only carry out the operations outdoors or in a well ventilated place.
Keep your face well away from the plug to prevent harmful vapours from being inhaled. Dispose of fuel in the correct
way and do not litter as it is highly polluting.
FUEL
When refuelling, it is advisable to use a funnel to prevent fuel from spilling out. The fuel should also be filtered to prevent dust or
dirt from entering the tank.
Use the same type of diesel fuel as used in cars. Use of other types of fuel could damage the engine. The cetane rating of the
fuel must be higher than 45 to prevent difficult starting. Do not use dirty diesel fuel or mixtures of diesel fuel and water since this
would cause serious engine faults.
The capacity of the standard tank is: lt. 7.0
The maintenance operations listed above refer to an engine operating in normal conditions (temperature, degree of humidity,
dust in the working environment). They may vary significantly according to the type of use.
MANUTENANCE
INTERVAL (HOURS)
COMPONENT
OPERATION
CLEANING
CHECK
OVERALL
INSPECTION
REPLACEMENT
OIL-BATH AIR CLEANER
HEAD AND CYLINDER FINS
FUEL TANK
INJECTOR
AIR CLEANER OIL
LEVEL OIL SUMP
BATTERY FLUID
VALVE/ROCKER ARM CLEARANCE
INJECTOR SETTING
AIR CLEANER
SUMP
EXTERNAL OIL FILTER CARTRIDGE
FUEL FILTER CARTRIDGE
DRY AIR CLEANER CARTRIDGE
PARTIAL
COMPLETE
OIL
MAINTENANCE - RECOMMENDED OIL TYPE - REFILLING