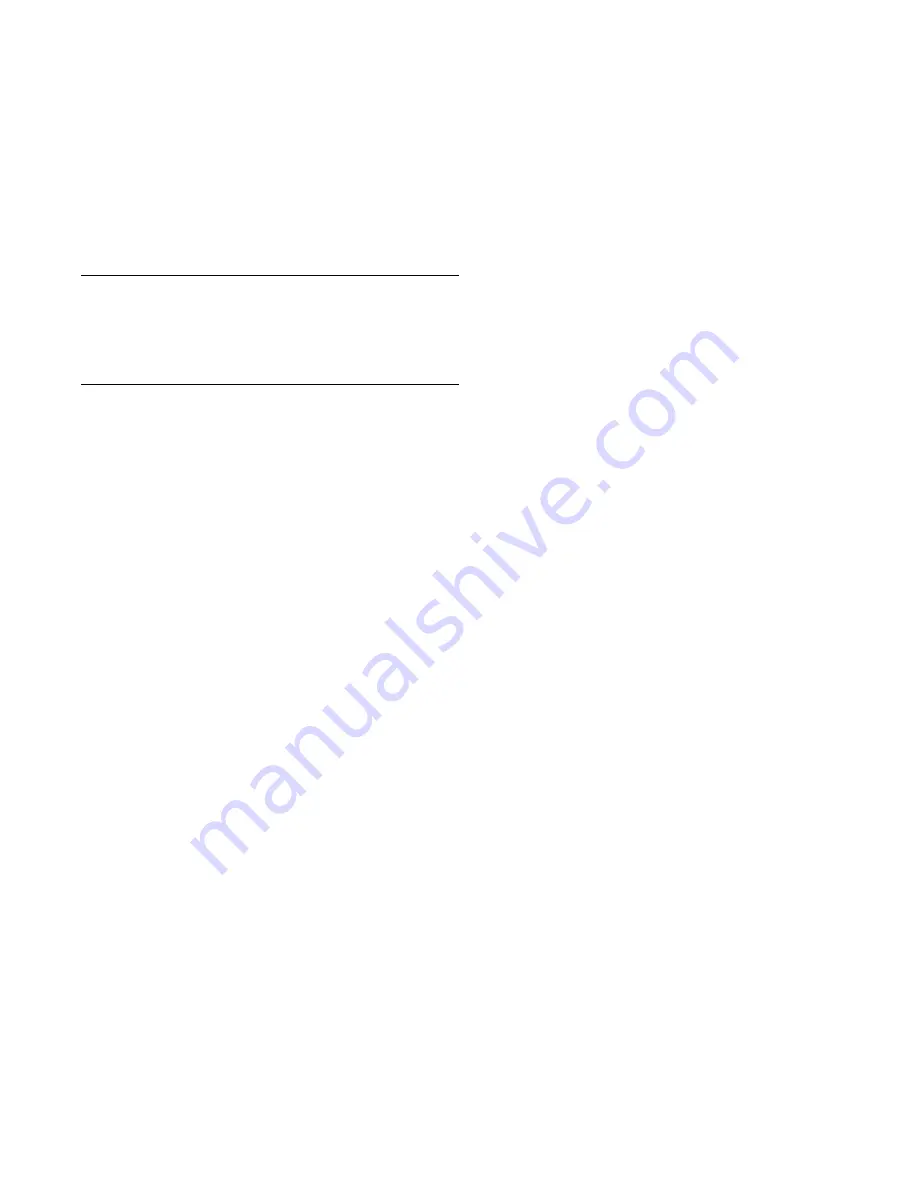
Lubrication System
29
24 690 37 Rev. B
KohlerEngines.com
OIL SENTRY
™
(if equipped)
This switch is designed to prevent engine from starting
in a low oil or no oil condition. Oil Sentry
™
may not shut
down a running engine before damage occurs. In some
applications this switch may activate a warning signal.
Read your equipment manuals for more information.
Oil Sentry
™
pressure switch is installed in breather cover.
On engines not equipped with Oil Sentry
™
installation
hole is sealed with a 1/8-27 N.P.T.F. pipe plug.
Installation
1. Apply pipe sealant with Teflon
®
(Loctite
®
PST
®
592™
Thread Sealant or equivalent) to threads of switch.
2. Install switch into tapped hole in breather cover.
3. Torque switch to 4.5 N·m (40 in. lb.).
Testing
Compressed air, a pressure regulator, pressure gauge,
and a continuity tester are required to test switch.
Normally Closed Switch
1. Connect continuity tester across blade terminal and
metal case of switch. With 0 psi pressure applied to
switch, tester should indicate continuity (switch
closed).
2. Gradually increase pressure to switch. As pressure
increases through range of 2-5 psi, tester should
indicate a change to no continuity (switch open).
Switch should remain open as pressure is increased
to 90 psi maximum.
3. Gradually decrease pressure through range of 2-5
psi. Tester should indicate a change to continuity
(switch closed) down to 0 psi.
4. Replace switch if it does not operate as specified.
Normally Open Switch
1. Connect continuity tester across blade terminal and
metal case of switch. With 0 psi pressure applied to
switch, tester should indicate no continuity (switch
open).
2. Gradually increase pressure to switch. As pressure
increases through range of 2-5 psi, tester should
indicate a change to continuity (switch closed).
Switch should remain closed as pressure is
increased to 90 psi maximum.
3. Gradually decrease pressure through range of 2-5
psi. Tester should indicate a change to no continuity
(switch open) down to 0 psi.
4. Replace switch if it does not operate as specified.