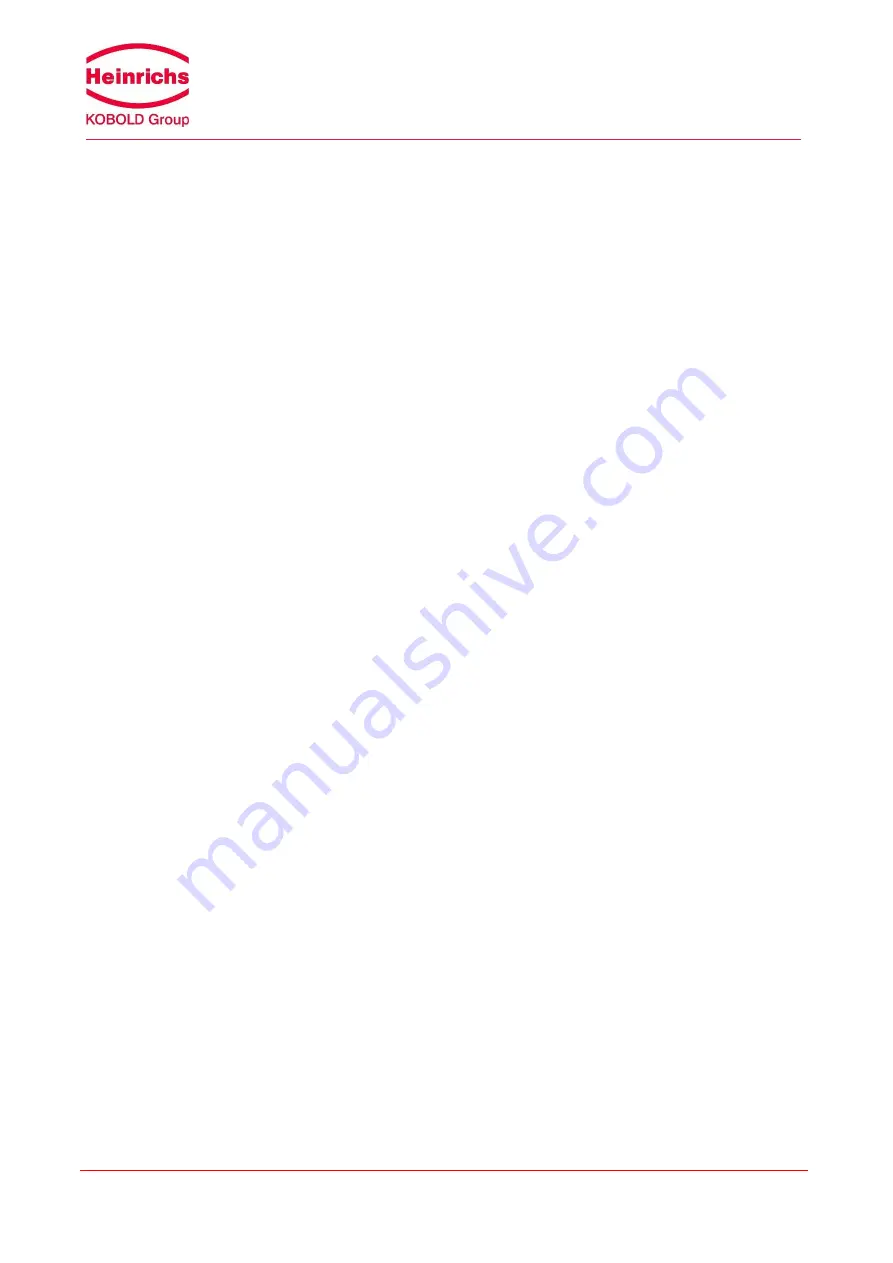
Heinrichs Messtechnik GmbH
Page 14 of 20
TM/TMU/TM-SH Supplement Manual
For Explosion Flow-meters
e)
When mounted separately (remote mount configuration), equipotential bonding between the sensor
and transmitter is essential to guarantee conformity of the intrinsically safe circuits. Terminals are
provided on the outside of the sensor and transmitter for this purpose
f)
It is to be ensured that the intrinsically safe circuits of the sensor cable are not laid together with non-
intrinsically safe circuits.
g)
When using a connection cable other than the manufactures specified cable, the intrinsic safety of the
cable is to be validated using the cables nominal parameters. Field wiring using multi-conductor cable
shall either have each conductor pair enclosed in a grounded metal shield, or each conductor shall have
a minimum of 0.25mm (0.01”) insulation thickness.
The following maximum values apply:
Wire to wire
-
C
L
= 100pF/m
L
L
= 0.7mH/km
Wire to shield -
C
L
= 170pF/m
L
L
= 0.5mH/km
h)
If the sensor is used at an ambient temperature of less than -20 °C or greater 60 °C, suitable cables,
cable entries and conduit entries are to be used.
i)
The operational wall thickness of the stainless steel flow tubes may be < 1 mm. In this case, the
operator is to ensure that in the area of these tubes, no risk of damage by the medium or through
mechanical damage shall occur.
j)
The sensor may be used in such a way that in the measuring tubes an explosive atmosphere may be
present occasionally or for a long period of time.
k)
Seized screws or adhering joints (e.g by frost or corrosion) are not to be opened with force in the
presence of a potentially explosive atmosphere.
l)
Where substances of explosion group “A” or “IIC” are present and the presence of an Ex-atmosphere is
considered possible, only non-sparking tools shall be used.
m)
The electrical connections from the sensor to the junction box are made by means of a connection
flange. Care must be taken to guarantee the IP protection class.
4.2
Ex relevant screw and bolt torques
Potential Equalisation fixation
6 Nm
Nuts sensor-neck/J-box (PE)
6 Nm
Screws J-box lid (Aluminium)
2 Nm
Screws J-box lid (Polyester)
1.2 Nm
Cable glands to J-box adapter
12 Nm
Cable gland caps
8 Nm