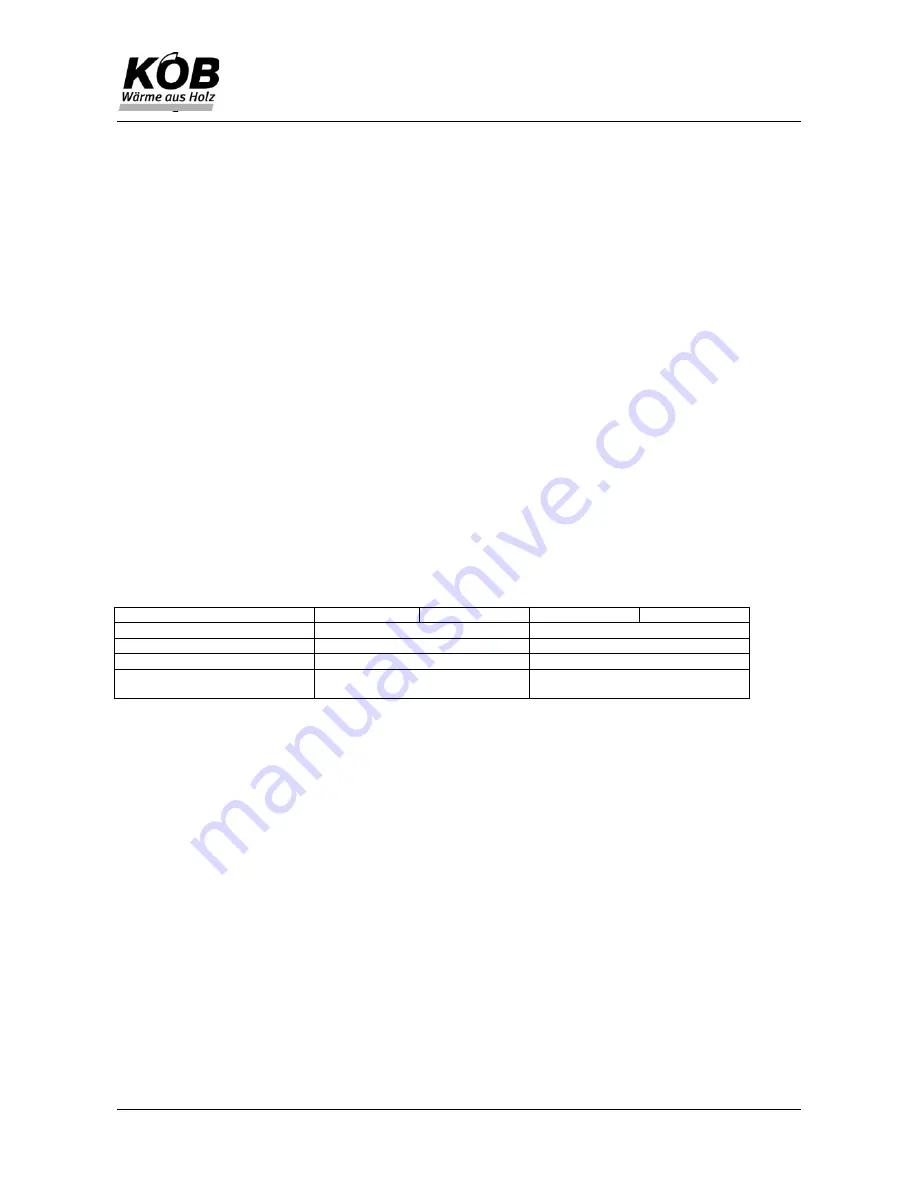
Spec
Sheet
PYRTEC Grate Firing System
De-ashing & Cleaning Systems
KÖB & SCHÄFER GmbH, Flotzbachstr. 33, A-6922 Wolfurt, Tel. +43/5574/6770-0, Fax 65707, E-Mail: [email protected]
Subject to technical changes.
7120-2
2006-03-06_E
Pneumatic cleaning system
[Item No. KPT-W720-S]
Pneumatic cleaning system
[Item No. KPT-W1250-S]
The complete pipe-type heat exchanger is cleaned off by periodic blasts of compressed air while the system is in regular
operation. The process of cleaning itself takes place in blasting of the individual sections carried out one after another.
The ash on the heat exchanger pipes is detached by very short but strong blasts of pressure.
The particles detached are conducted by the flow of gas to the de-duster, where most are eliminated.
The system is built into the furnace door.
The compressor should preferably be installed in a cool spot in the heating room.
Function of the control system:
The number of cleaning cycles within one unit of time (e.g. per hour) is adjusted according to the loading of the furnace.
One single, complete cleaning cycle consists of one sequence of blasts over all the sections of the heat exchanger.
The following items come with the system:
-
Nozzle element built into the furnace door, incl. connecting piece with heat dissipation plate
-
Compressed air distributor with tank and valves; with heat-resistant hoses connected to nozzle element
-
Compressor; model 362-100, special-purpose design for municipal uses
Delivery capacity of 202 l/min.; tank: 100-l; pressure: max. 10 bar; motor: 2.2 kW, 1450 RPM, 230V,
incl. pressure controller, pressure switch and operating time limiter; plug and play; sound level of normal design:
75 dBA
-
Compressed air hose up to max. of 4.0 m in length
-
Valves wired tight to terminal strip
-
Software component in the control system
To be carried out by customers:
-
Provide a mains socket, 230V/ 16A
Technical data:
PYRTEC
KPT-530
KPT-720
KPT-950
KPT-1250
[Item No.]
KPT-W720-S
KPT-1250-S
Number of zones/valves
10
12
Size of the valves
6/4“
6/4“
Max. air consumption, full load
[l/h] 4400
5300
Compressor soundproofed, 64dBA
[Item No. KT-WK]
-
Compressor in Special design for municipal use with soundproof hood (model 362-100);
delivery capacity: 202 l/min
-
Tank: 100 l; pressure: max. 10 bar; motor: 2.2 kW, 1450 RPM, 230V; incl. pressure controller and pressure switch,
plug and play; sound level: 64 dBA.
When this item is used, the compressor listed in the item "Pneumatic Cleaning System" is omitted.
Reduced charge with compressed air provided by the customer
[Item No. KT-WL]
As a result, the compressor listed in the item "Pneumatic Cleaning System" is omitted. The compressor provided by the
customer has to deliver at least the amount and quality of air specified and have an adjustable pressure controller as well
as a protective device against hose rupture (e.g. operating time limiter).
Содержание KOB PYRTEC SERIES
Страница 1: ...Assembly and Installation Instructions 530 to 1250 ID 104661 F english ...
Страница 15: ......
Страница 16: ......
Страница 39: ......