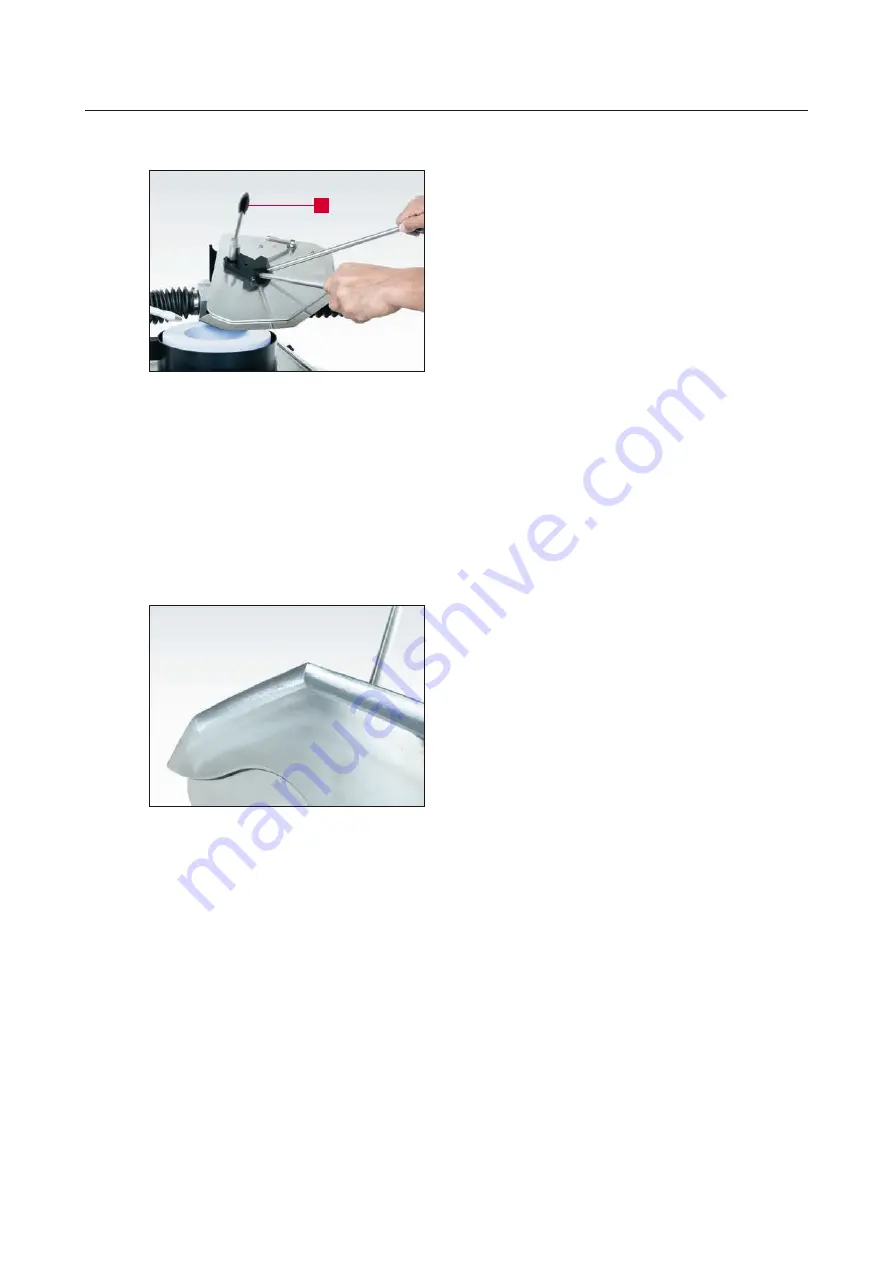
35
Figure 7-25
Swiveling the cutter knife to the
next cutting segment
Figure 7-26
Convex pre-ground cutter knife
1
When the first segment is completely ground,
loosen the clamping lever (7-25/1) and swivel the
knife to the next segment.
Adjust the grinding angle (see chapter 7.1.5),
align the cutter knife on the grinding wheel (see
chapter 7.1.4), and tighten the clamping lever
(7-25/1).
Grind all cutting segments as described
below:
Adjust grinding angle (see chapter 7.1.5).
Align the cutter knife on the grinding wheel
(see chapter 7.1.4).
Grind cutter knives (see chapter 7.1.7).
Repeat process for each cutting segment.
The cutter knife is now pre-ground.
Before it can be deburred and polished, the fine
grinding must be carried out on the HV 262
Universal Belt Grinding Unit (see chapter 9.1).
7. Operating the HV 203