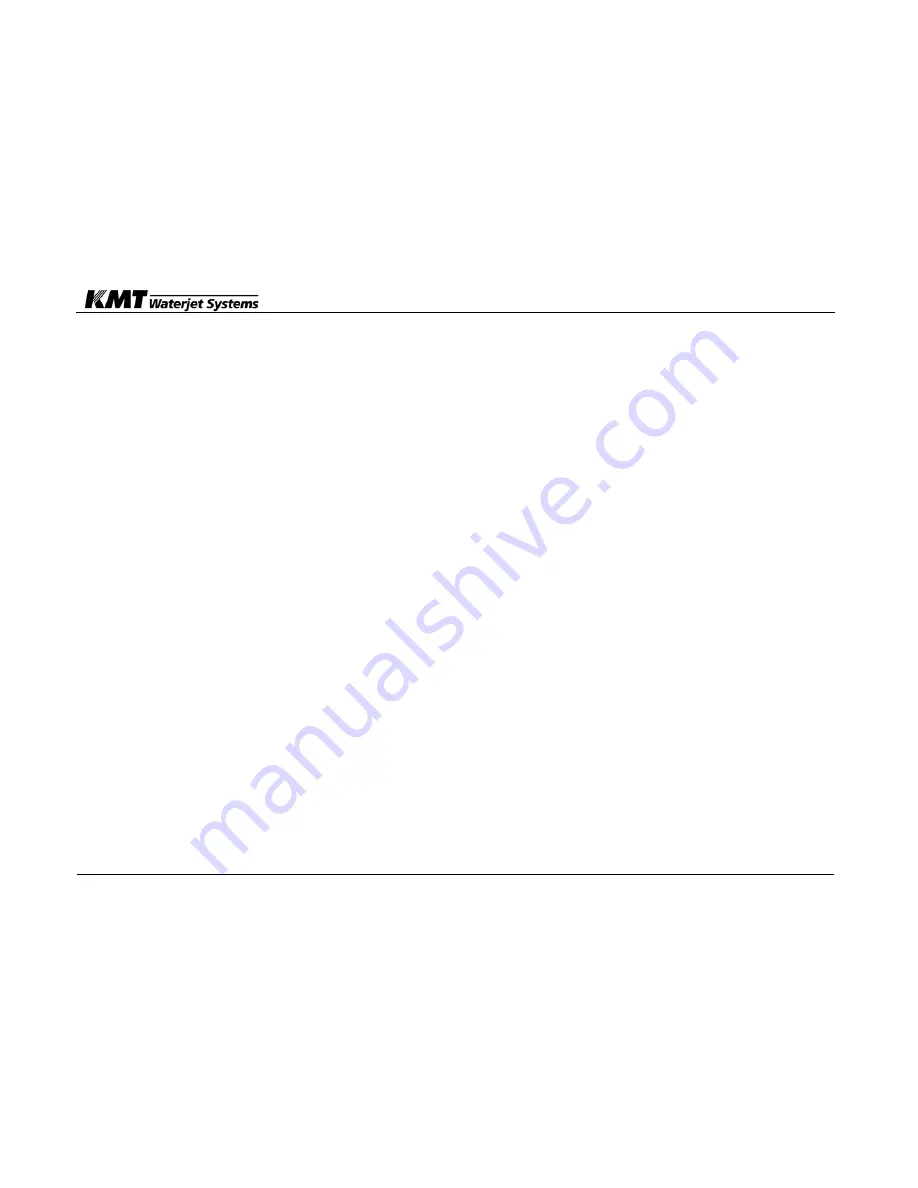
SECTION 12 PARTS LISTS
Figure 12-8 BULKHEAD PIPING ASSEMBLY, 80080179
ITEM No QTY PART No.
DESCRIPTION
1
1
10091866
Valve,
Modulating
2
4
10078194
Bulkhead Adapter, ½-1-1/2 NPT
3
-
10127348
Hose, Push-On, .50-in. ID
4
1
10073823
Tee, Male Run, ½-NPT, Brass
5
1
05126289
Filter Assembly, LP Water
6
1
49834328
Adapter, .25 OD Tube x ½ - NPT
7
1
10077055
Adapter, Bulkhead, 4-15
8
1
10189900
Tee, Male Run, ¼ x 1/8 NPT,
9
-
10079903
Tube, Polyethylene, .25-in. OD
10
1
10145829
Nipple, Close, ½-NPT, Brass
11
2
49834302
Adapter, Tube/Pipe, .50
12
2
05128947
Adapter, 1/4 NPT x .-8 JIC,
13
5
10079713
Barb, .50, NPT
14
3
10173805
Barb, Hose, 0.50 x –8JIC
15
5
05113964
Grommet
16
1
10147460
Elbow, ½-NPT x –8 JIC, 90 degree
17
1
10100477
Bushing, ¼ x1/8 NPT, Brass
18
1
05128715
Valve, Solenoid, 24vdc
19
1
05112271
Muffler, Pneumatic, 1/8-NPT
20
2
05143508
Screw, Machine, #4-40 x 1-1/2
21
2
10118214
Lockwasher #5-40
22
2
10078095
Coupling, Poly, ¼ x 1/8 NPT
23
1
10077030
Elbow, 90-deg, M, .25 x .13
24
2
95146403
Hex Nut, #4-40
25
1
49834310
Adapter, Tube/Pipe, .50
26
3
49831480
Grommet
p. 12-18
05139159
Содержание Streamline SL-IV
Страница 103: ...SECTION 12 PARTS LISTS p 12 5 05139159 ...
Страница 105: ...SECTION 12 PARTS LISTS p 12 7 05139159 ...
Страница 107: ...SECTION 12 PARTS LISTS p 12 9 05139159 ...
Страница 109: ...SECTION 12 PARTS LISTS p 12 11 05139159 ...
Страница 111: ...SECTION 12 PARTS LISTS p 12 13 05139159 ...
Страница 113: ...SECTION 12 PARTS LISTS p 12 15 05139159 ...
Страница 115: ...SECTION 12 PARTS LISTS p 12 17 05139159 ...
Страница 117: ...SECTION 12 PARTS LISTS p 12 19 05139159 ...
Страница 119: ...SECTION 12 PARTS LISTS p 12 21 05139159 ...
Страница 121: ...SECTION 12 PARTS LISTS p 12 23 05139159 ...
Страница 123: ...SECTION 12 PARTS LISTS p 12 25 05139159 ...
Страница 125: ...SECTION 12 PARTS LISTS p 12 27 05139159 ...
Страница 128: ...SECTION 12 PARTS LISTS p 12 30 05139159 ...
Страница 129: ...Date 3 21 2003 Time 09 31 40 AM Title J cad Release 0512 05129507 DWG ...
Страница 130: ...Date 3 27 2003 Time 11 25 52 AM Title J cad Release 0514 05141015 dwg ...
Страница 131: ...Date 3 27 2003 Time 11 26 31 AM Title J cad Release 0514 05141015 dwg ...
Страница 132: ...Date 3 27 2003 Time 11 26 54 AM Title J cad Release 0514 05141015 dwg ...