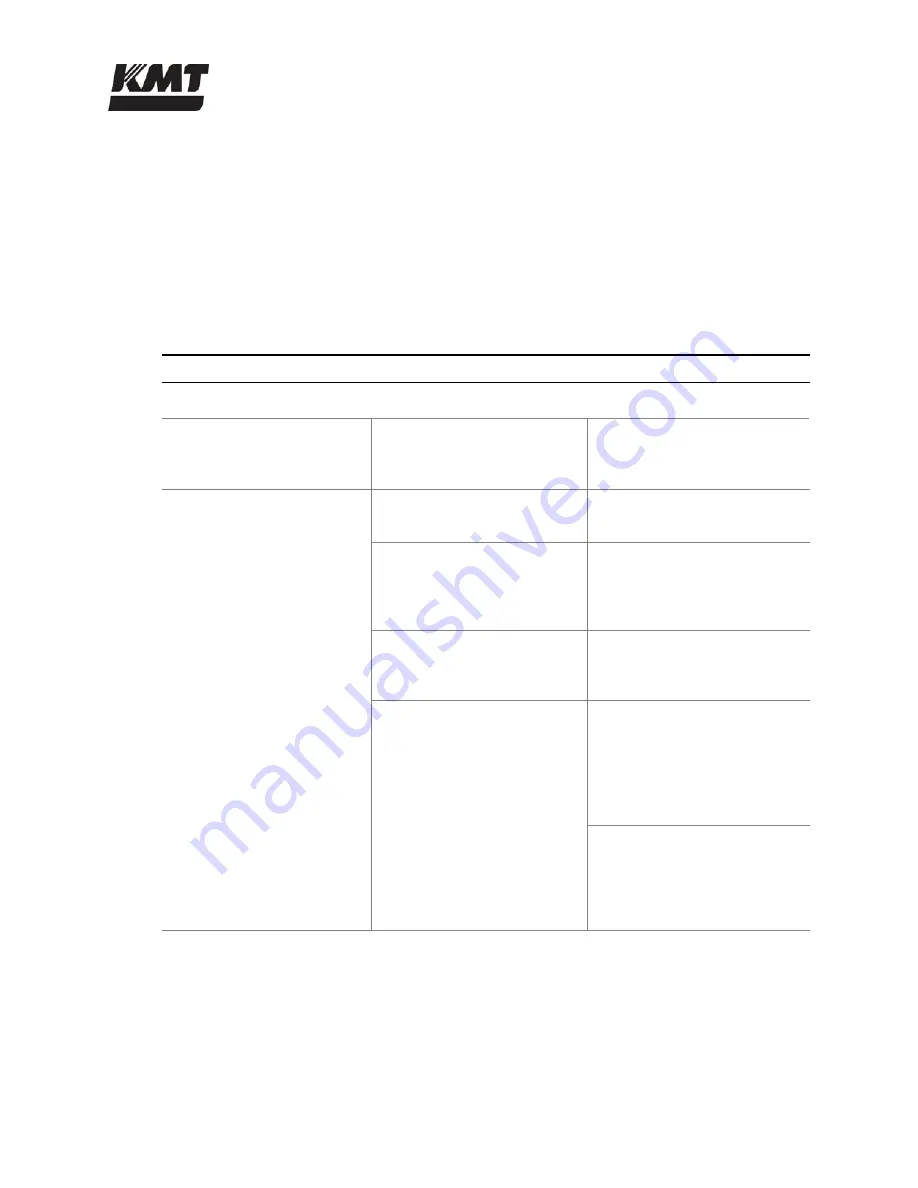
Section 8
High Pressure Water System
20479291
2-2012/Rev 04
8-34
8.15
Weep Holes
High pressure seals and connections fail gradually and begin leaking slowly. Weep holes are
located at every threaded high pressure connection to provide a vent for internal leaks. Water or
oil dripping from a weep hole indicates one or more internal components are beginning to fail.
Table 8-3 lists the location of the weep hole, the possible source of the leak and the corrective
action required.
Table 8-3
Weep Holes
High Pressure Water System
Location Indication Comments
Hydraulic Cylinder Head
Hydraulic oil leaking from the
weep hole in the hydraulic
cylinder head
Failed hydraulic cartridge seal
Replace the cartridge seal. If the
leak persists, check the plunger
for linear scratches or scoring.
Water leaking from the weep
hole on the hydraulic cylinder
head flange
Failed high pressure seal
assembly
Replace the high pressure seal
assembly.
Damaged plunger
Check the plunger for
longitudinal scratches or flaws. If
detected, replace the plunger or
return to KMT for evaluation.
Seal material buildup on plunger
Polish the plunger surface
following the procedure, Plunger
Maintenance.
Damaged high pressure cylinder
Check for scratches, grooves or
material buildup on the inside
diameter of the cylinder. If
detected, polish the bore
following the procedure, High
Pressure Cylinder Maintenance.
Check the inside diameter of the
cylinder for expansion where the
high pressure seal assembly is
located. If detected, replace the
cylinder.
Содержание STREAMLINE S50
Страница 1: ...MANUAL 20479050 R04 STREAMLINE S50 WATERJET INTENSIFIER OPERATION AND MAINTENANCE MANUAL ...
Страница 20: ......
Страница 22: ......
Страница 125: ...Section 11 Parts List 20479307 2 2012 Rev 04 11 4 Figure 11 1 Streamline S50 Intensifier Unit ...
Страница 127: ...Section 11 Parts List 20479307 2 2012 Rev 04 11 6 Figure 11 2 Intensifier Assembly ...
Страница 131: ...Section 11 Parts List 20479307 2 2012 Rev 04 11 10 Figure 11 5 Hydraulic Piston Assembly ...
Страница 133: ...Section 11 Parts List 20479307 2 2012 Rev 04 11 12 Figure 11 6 High Pressure Piping ...
Страница 135: ...Section 11 Parts List 20479307 2 2012 Rev 04 11 14 Figure 11 7 Hydraulic Power Package ...
Страница 137: ...Section 11 Parts List 20479307 2 2012 Rev 04 11 16 Figure 11 8 Motor Pump Assembly ...
Страница 139: ...Section 11 Parts List 20479307 2 2012 Rev 04 11 18 Figure 11 9 Hydraulic Manifold Assembly ...
Страница 141: ...Section 11 Parts List 20479307 2 2012 Rev 04 11 20 Figure 11 10 Hydraulic Hose Connections ...
Страница 143: ...Section 11 Parts List 20479307 2 2012 Rev 04 11 22 Figure 11 11 Reservoir Assembly ...
Страница 145: ...Section 11 Parts List 20479307 2 2012 Rev 04 11 24 Figure 11 12 Bulkhead Pipe Assembly ...
Страница 147: ...Section 11 Parts List 20479307 2 2012 Rev 04 11 26 Figure 11 13 Electrical Assembly ...
Страница 149: ...Section 11 Parts List 20479307 2 2012 Rev 04 11 28 Figure 11 14 Junction Box ...
Страница 151: ...Section 11 Parts List 20479307 2 2012 Rev 04 11 30 Figure 11 15 Pneumatic Valve Actuator Assembly Normally Open ...
Страница 153: ...Section 11 Parts List 20479307 2 2012 Rev 04 11 32 Figure 11 16 Low Pressure Water Filter Assembly ...
Страница 155: ...Section 11 Parts List 20479307 2 2012 Rev 04 11 34 Figure 11 17 Heat Exchanger Kit Oil to Water ...
Страница 157: ...Section 11 Parts List 20479307 2 2012 Rev 04 11 36 Figure 11 18 Heat Exchanger Kit Oil to Air ...
Страница 158: ......
Страница 159: ......