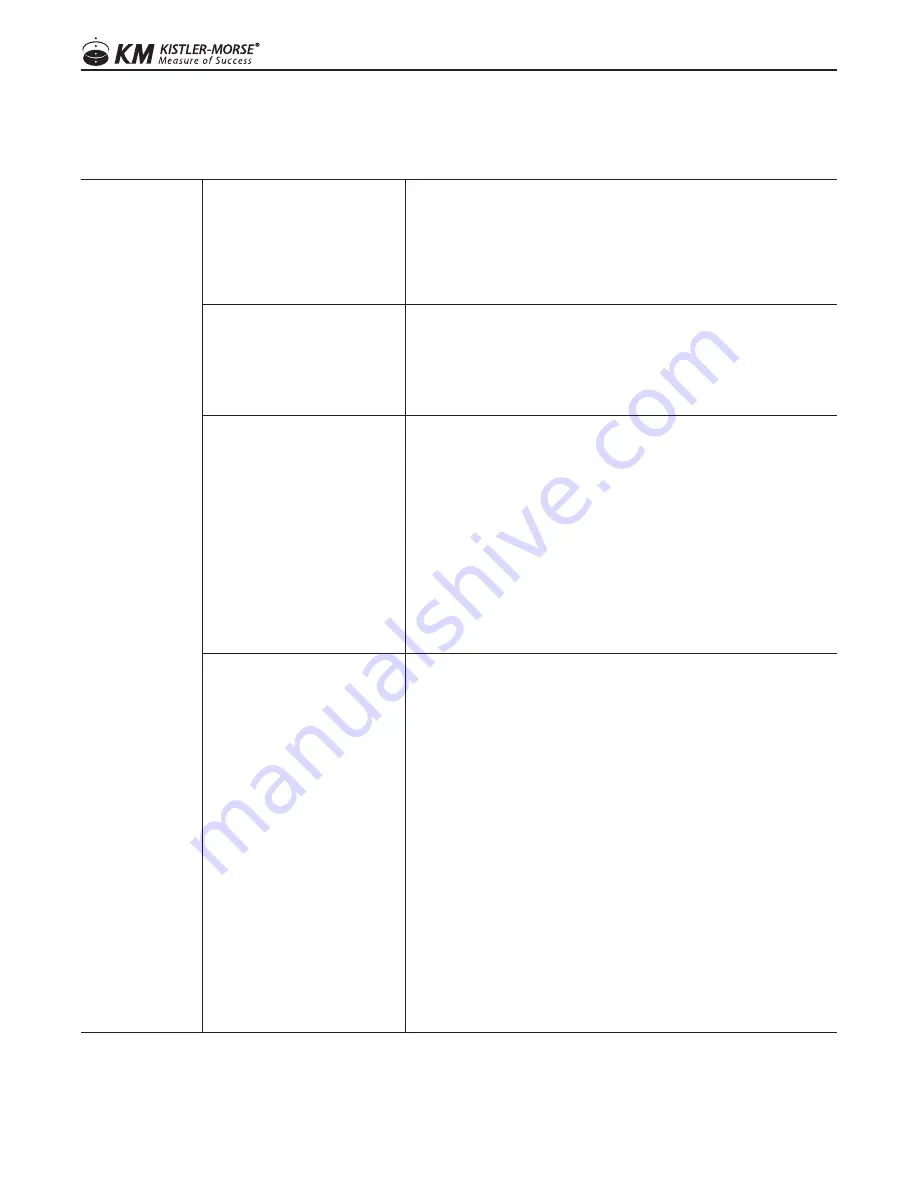
21
www.kistlermorse.com
97-1100-01 Rev. J
VII. TROUBLESHOOTING
SYMPTOM
POSSIBLE CAUSE
SOLUTION
Small Amplitude
Changes or Erratic
Fluctuations in
Display Readings
Fluctuations can be caused
by small amplitude drift or
oscillation, with peak-to-peak
disturbance of 0.1% to 0.5% of
full scale, is normal.
Problem likely to be noticed
shortly after initial installation.
Reduce drift or oscillation by setting ‘count by’ and ‘averaging’ appropriately
on signal processor (refer to signal processor manual).
Fluctuations can be caused by
moisture in the cable conduit,
junction boxes, or PCBs.
Problem likely to be noticed on
system that previously functioned
correctly.
Check conduit, junction boxes and PCBs for water contamination. Find
water entry source and correct problem. Dry with a hair drier. Remove/
replace corroded parts and materials.
CAUTION: If using sealant to eliminate water entry, use Sikaflex 1A
polyurethane sealant or Dow Corning RTV 739 or RTV 738. Other sealants
may contain acetic acid, which is harmful to sensors and electronics.
Fluctuations can be caused by
jammed bolts or heat radiation/
conduction.
Problem likely to be noticed
shortly after initial installation
or on system that previously
functioned correctly in cool or
overcast weather.
Loosen nuts on top bolts and inspect top bolts.
• Top bolts free to move in holes: If vessel is heated, it may be radiating or
conducting heat through vessel legs and affecting Load Stand sensors.
• To reduce head radiation/conduction:
a. Insulate vessel.
b. Contact K-M to discuss adding a high temperature insulating pad.
• Top bolts jammed: Jammed top bolts indicate undersized bolt holes on
vessel mounting flange and/or vessel support movement beyond limits of
Load Stand clearance holes. Resulting side loads affect Load Stand
sensors.
• To reduce side loads:
a. Enlarge vessel mounting flange bolt holes to provide additional
clearance.
Fluctuations can be caused by
damaged Load Stand sensor.
Problem likely to be noticed
shortly after initial installation
or on system that previously
functioned correctly.
Using Digital Multimeter (DMM), check resistance for individual Load Stands:
1. Set meter resistance scale to accommodate measured range up to
20,000 ohms.
2. At the suspect Load Stand junction box, remove wiring at TB1 and TB2,
which connects to other Load Stands and signal processors.
3. Put one DMM lead on W and other lead on R terminal on TB1 of Load
Stand junction box. Record resistance, and verify it is 7,660 ± 200 ohms.
If reading is outside this range, one or more Load Stand sensors are
damaged and must be replaced— go to Step 7 to identify which sensor
is damaged.
4. Put one DMM lead on W and other lead on B terminal on TB1 of Load
Stand junction box. Record resistance, and verify it is 7,660 ± 200 ohms.
If reading is outside this range, one or more Load Stand sensors are
damaged and must be replaced — go to Step 7 to identify which sensor
is damaged.
5. Verify readings from Steps 3 and 4 are within 200 ohms of each other. If
not, one or more Load Stand sensors are damaged and must be
replaced — go to Step 7 to identify which sensor is damaged.
6. Repeat Steps 2 through 5 for each suspect Load Stand, until Load Stand
with damaged sensor is located.
7. Continued on next page.
Содержание Load Stand II
Страница 2: ......
Страница 15: ...11 www kistlermorse com 97 1100 01 Rev J FIGURE 2 CONCRETE MOUNTING ...
Страница 16: ...97 1100 01 Rev J 12 www kistlermorse com FIGURE 3 SUPPORT BEAM MOUNTING ...
Страница 19: ...15 www kistlermorse com 97 1100 01 Rev J FIGURE 4 SIGNAL CABLE LAYOUT ...
Страница 20: ...97 1100 01 Rev J 16 www kistlermorse com 1 2 2 3 4 5 6 FIGURE 5 INTERCONNECT DIAGRAM ...
Страница 28: ...97 1100 01 Rev J 24 www kistlermorse com VIII DIMENSIONAL DRAWINGS ...
Страница 29: ...25 www kistlermorse com 97 1100 01 Rev J NOTES ...
Страница 30: ...97 1100 01 Rev J 26 www kistlermorse com NOTES ...
Страница 31: ...27 www kistlermorse com 97 1100 01 Rev J NOTES ...