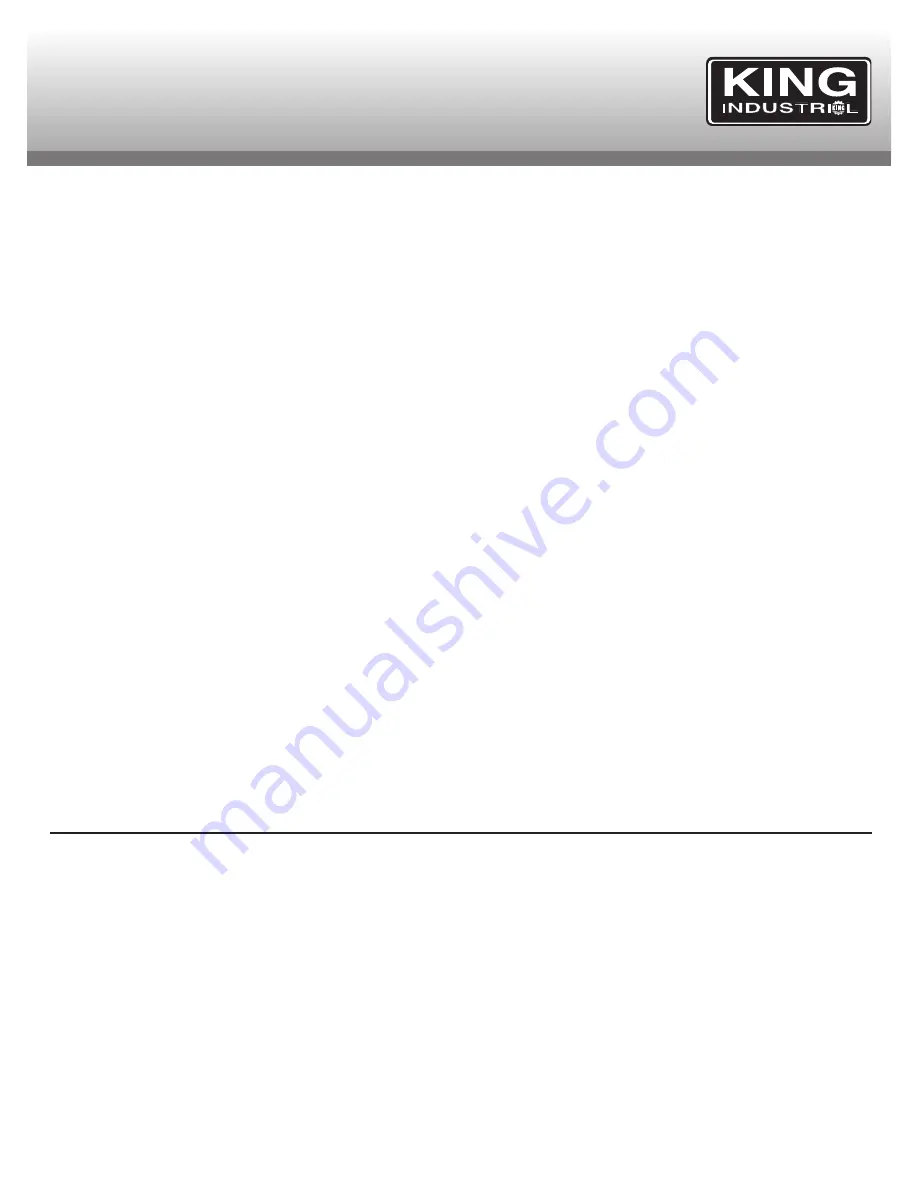
GENERAL & SPECIFIC SAFETY
INSTRUCTIONS FOR METAL LATHES
GENERAL SAFETY INSTRUCTIONS
1. KNOW YOUR TOOL
Read and understand the owners manual and labels affixed to
the tool. Learn its application and limitations as well as its
specific potential hazards.
2. GROUND THE TOOL.
This tool is equipped with an approved 3-conductor cord. The
green conductor in the cord is the grounding wire.
NEVER
connect the green wire to a live terminal.
3. KEEP GUARDS IN PLACE.
Keep in good working order, properly adjusted and aligned.
4. REMOVE ADJUSTING KEYS AND WRENCHES.
Form habit of checking to see that keys and adjusting
wrenches are removed from tool before turning it on.
5. KEEP WORK AREA CLEAN.
Cluttered areas and benches invite accidents. Make sure the
floor is clean and not slippery due to wax and sawdust
build-up.
6. AVOID DANGEROUS ENVIRONMENT.
Don’t use power tools in damp or wet locations or expose
them to rain. Keep work area well lit and provide adequate
surrounding work space.
7. KEEP CHILDREN AWAY.
All visitors should be kept a safe distance from work area.
8. MAKE WORKSHOP CHILD-PROOF.
Use padlocks, master switches or remove starter keys.
9. USE PROPER SPEED.
A tool will do a better and safer job when operated at the
proper speed.
10. USE RIGHT TOOL.
Don’t force the tool or the attachment to do a job for which it
was not designed.
11. WEAR PROPER APPAREL.
Do not wear loose clothing, gloves, neckties or jewelry (rings,
watch) because they could get caught in moving parts. Non-
slip footwear is recommended. Wear protective hair covering
to contain long hair. Roll up long sleeves above the elbows.
12. ALWAYS WEAR SAFETY GLASSES.
Always wear safety glasses (ANSI Z87.1). Everyday eye-
glasses only have impact resistant lenses, they are
NOT
safety glasses. Also use a face or dust mask if cutting opera-
tion is dusty.
13. DON’T OVERREACH.
Keep proper footing and balance at all times.
14. MAINTAIN TOOL WITH CARE.
Keep tools sharp and clean for best and safest performance.
Follow instructions for lubricating and changing accessories.
15. DISCONNECT TOOLS.
Before servicing, when changing accessories or attachments.
16. AVOID ACCIDENTAL STARTING.
Make sure the swich is in the ‘’OFF’’ position before plugging
in.
17. USE RECOMMENDED ACCESSORIES.
Consult the manual for recommended accessories. Follow the
instructions that accompany the accessories. The use of
improper accessories may cause hazards.
18. NEVER STAND ON TOOL.
Serious injury could occur if the tool tips over. Do not store
materials such that it is necessary to stand on the tool to reach
them.
19. CHECK DAMAGED PARTS.
Before further use of the tool, a guard or other parts that are
damaged should be carefully checked to ensure that they will
operate properly and perform their intended function. Check for
alignment of moving parts, breakage of parts, mounting, and
any other conditions that may affect its operation. A guard or
other parts that are damaged should be properly repaired or
replaced.
20. NEVER LEAVE MACHINE RUNNING
UNATTENDED.
Turn power ‘’OFF’’. Don’t leave any tool running until it comes
to a complete stop.
SPECIFIC SAFETY INSTRUCTIONS FOR METAL LATHES
1. CLEANING MACHINE:
To avoid entanglement and lacerations,
do not clear chips by hand. Use a brush, and never clear chips
while the lathe is operating.
2. USING CORRECT TOOLING:
Always select the right cutter for
the job, and make sure cutters are sharp. The right tool
decreases strain on the lathe components and reduces the risk
of unsafe cutting.
3. ELIMINATING PROJECTILE HAZARDS:
Always remove the
chuck key, and never walk away from the lathe with the chuck
key installed. Always make sure workpiece is securely held in
chuck before starting lathe. A workpiece thrown from the chuck
could cause severe injury.
4. AVOIDING OVERLOADS:
Always use the appropriate feed and
speed rates.
5. PREVENTING A CUTTING TOOL/CHUCK CRASH:
Always
release automatic feeds after completing a job, and never leave
lathe unattended while it is running.
6. AVOIDING STARTUP INJURIES:
Make sure workpiece, cutting
tool, and tool post have adequate clearance before starting
lathe. Check chuck clearance and saddle clearance before
starting the lathe. Make sure spindle RPM is set correctly for part
diameter before starting the lathe. Large parts can be ejected
from the chuck if the chuck speed is set too high.
7. CHUCK SAFETY:
Chucks are surprisingly heavy and awkward
to hold, so protect your hands and the lathe ways. Always use a
chuck cradle or piece of plywood over the lathe ways.
8. WORKPIECE SUPPORT:
Support a long workpiece if it extends
from the headstock so it will not wobble violently when the lathe
is turned ON. If workpiece extends more than 2.5 times its
diameter from the chuck, support it by a center or steady rest, or
it may deflect and fall out of the chuck while cutting.
9. AVOIDING ENTANGLEMENT INJURIES:
Never attempt to slow
or stop the lathe chuck by hand. Tie back long hair, ponytails,
loose clothing, and sleeves so they do not dangle.