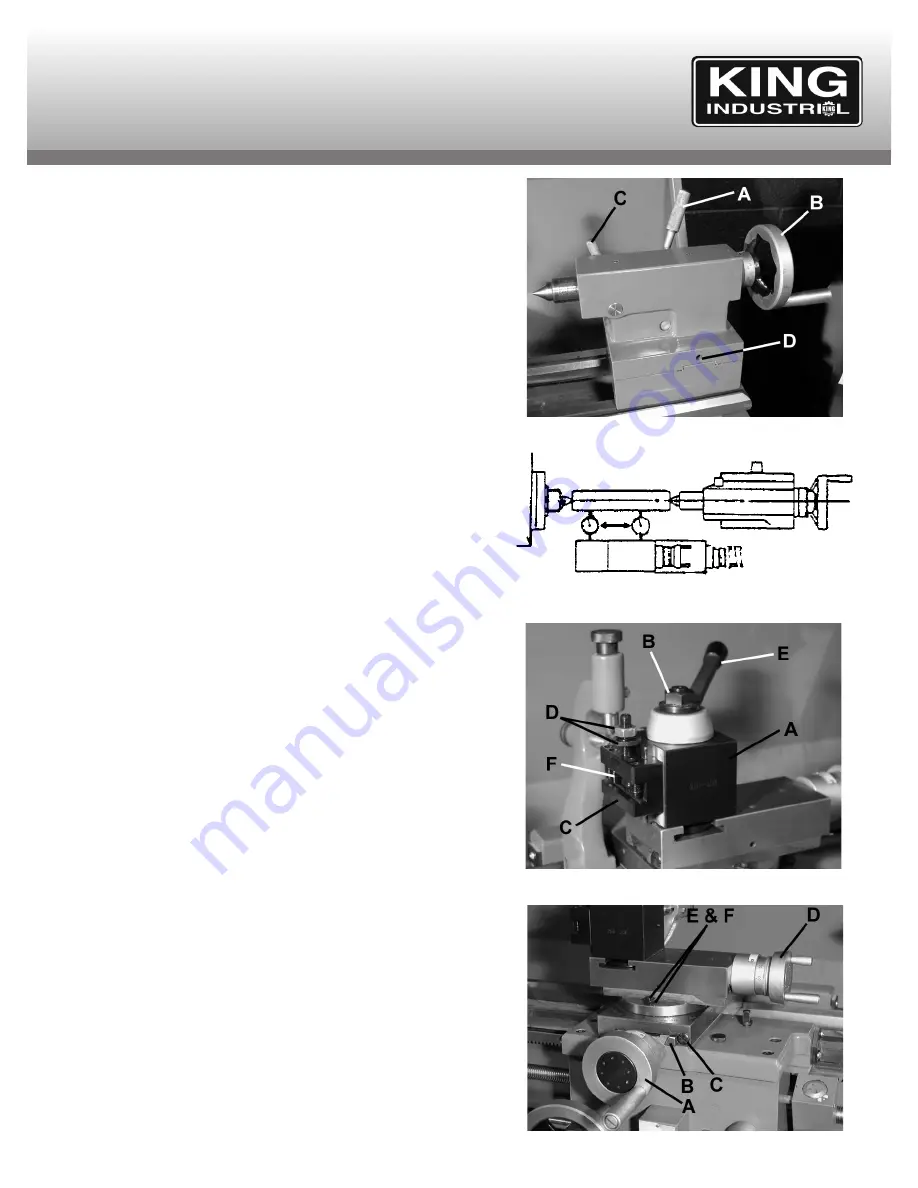
ADJUSTMENTS & OPERATION
Tailstock Adjustments & Operation
The tailstock can be moved freely on the bedway and fastened at any
position by locking tailstock lever (A) Fig.11. The tailstock quill can be
moved in and out by using handwheel (B) and then fastened in place using
quill locking lever (C). Dead centers or drill chucks are normally installed
in the tailstock quill.
An important adjustment and verification must be done in order to obtain
the best results using your tailstock. The tailstock must be perfectly
aligned with the chuck. Fix a ground steel bar inbetween the chuck center
and the tailstock center. Using a precise measuring tool (dial indicators),
make sure the distance at both ends of the ground steel bar are the same
using the top slide as starting reference point, see Fig.12. If the distance
is not the same, then an crosswise adjustment to the tailstock is
necessary.
Unlock tailstock lever (A) Fig.11 and adjust set screws (D) on both sides
of the tailstock until the distance at both ends of the ground steel bar are
the same.
Tool Post Adjustments & Operation
The tool post assembly (A) Fig.13 is used to lock the cutting tool into place
at the desired height and angle. The tool post can pivot 360
0
for various
cutting situations. To pivot the tool post assembly, loosen lock nut (B) and
pivot tool post, retighten lock nut. The tool post comes with a tool holder
(C) which can be adjusted to a desired height using the shaft and nuts
mechanism (D) to raise or lower the tool holder. Once the height of the tool
holder is determined, use tool post lock handle (E) to lock tool holder in
place. The tool holder has 4 locking set screws (F) which lock the cutting
tool in place.
Cross & Top Slide Adjustments & Operation
The cross slide handwheel (A) Fig.14 is used to feed the cross slide, top
slide and tool post with cutting tool towards the workpiece. After time the
cross slide gib (B) may become loose or too tight and an adjustment may
be necessary. To adjust the gib (B), tighten or loosen the flat head bolt (C)
until the cross slide moves freely without play.
The top slide handwheel (D) feeds the top slide and tool post with cutting
tool towards the chuck or the tailstock end of the lathe. After time the top
slide gib may become loose or too tight and an adjustment may be
necessary. The top slide can be pivoted to a desired angle, to adjust the
angle the top slide simply loosen hex. nuts (E) and set screws (F) on both
sides of the top slide base.
FIGURE 11
FIGURE 12
FIGURE 13
FIGURE 14