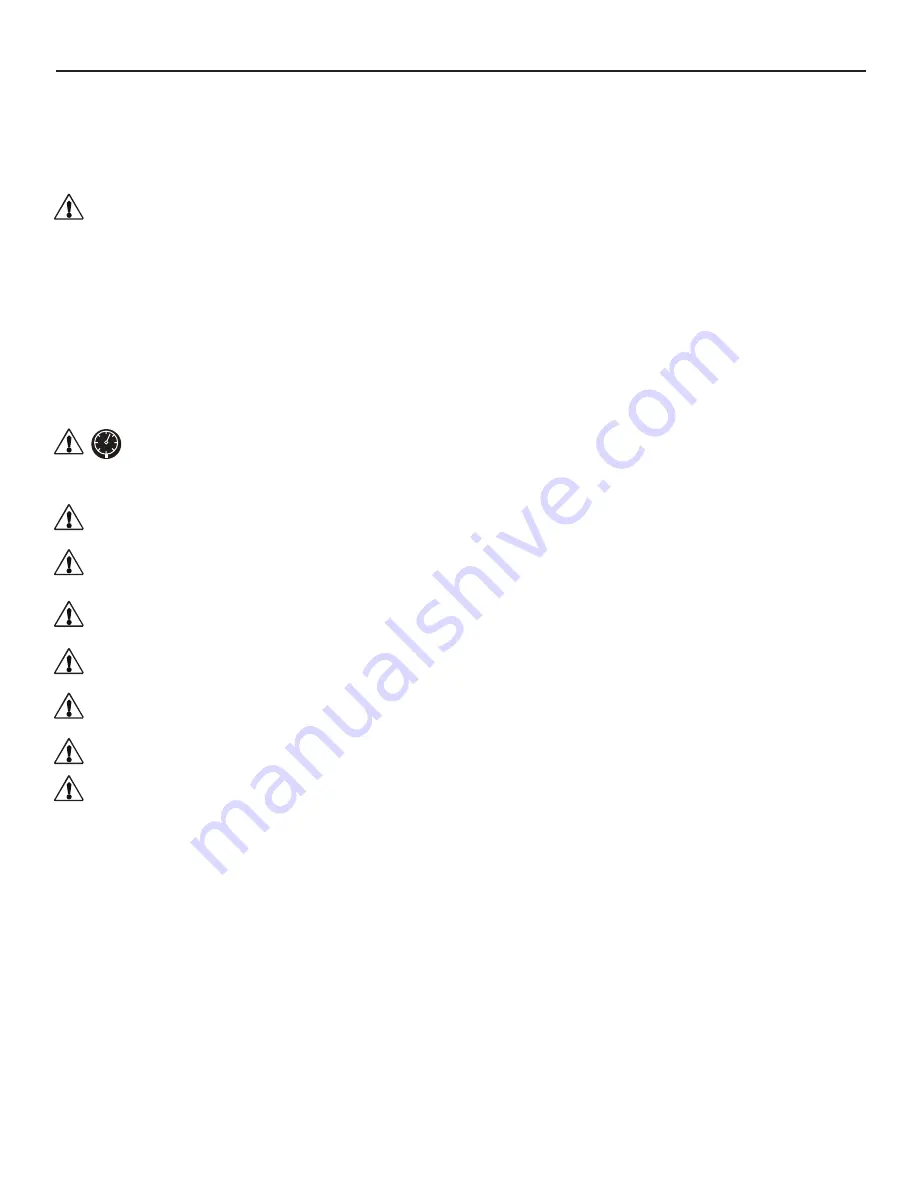
11
I
nStallatIon
Getting Started
The following procedures have been developed to assist during the installation of your KineticoPRO Filter.
ALL STATE AND LOCAL PLUMBING CODES MUST BE MET
, including, but not limited to:
Distances that equipment should be placed from the main panel box and electrical outlets.
Air gaps that must be provided for all drain lines.
Pre-installation Review
Before beginning the installation of the KineticoPRO system, confirm system configuration to be installed and
components that have been ordered. Please review KineticoPRO system specification sheets on pages 8-10 that include
required components.
Review of the customer’s facility is also recommended, especially critical operating data that could affect the operation
of the system:
Water pressure to the KineticoPRO system affects the performance during regeneration. The KineticoPRO
system will not operate properly if the inlet pressure fluctuates below a dynamic pressure of 25 psi. This
minimum pressure must be maintained to the system at all times. Should the pressure fluctuate below this
level, a booster pump may be required.
Do not use on water pressure that exceeds 125 psi or water temperature that exceeds 120°F.
Do not install the KineticoPRO Filter in an area where the temperature can cause the unit to freeze. Damage to
the system will result.
It is recommended that a WQA certified installer perform the installation. Failure to install the system as
instructed will void the limited warranty.
Proper ventilation must be provided when using PVC cleaner or glue.
A ladder should be used for all work over head that would be beyond your natural reach. If working continuously
at a height of six feet or more, the appropriate safety devices must be employed.
An appliance dolly should be used when transporting equipment on stairways.
When soldering, the following MUST be met and followed:
• LEAD FREE solder must be used.
• PVC containers and other flammable materials must be closed or removed to prevent fire or explosions.
• Loose clothing (ie: shirt tails, sleeves, etc.) should not be worn or should be addressed before using a torch
for soldering.
• The customer must be notified if you will be disabling smoke alarm(s) during installation. Be sure to
reconnect the smoke alarm(s).
• A scorch pad must be used to protect any surface that may be exposed to a torch flame or excessive heat.
Wear protective eyewear while installing to prevent eye injury caused by splattering soldering materials or
metal/plastic shavings.
• Do not solder brass adapters while inserted in the module main base. Damage to the plastic and rubber
parts may occur due to the heat and may result in water damage.
• The materials used in the soldering process may attack certain types of plastics. Care should be taken during
the installation process to assure that solder and flux do not come in contact with media tanks, the control
module and related plastic components.
• Clear an area along wall where PVC drain line will be run to floor drain. KineticoPRO does not recommend
running flexible tubing across the floor or along walls, as it may be kicked out of discharge point at floor
drain, or line may become pinched resulting in improper back washing.