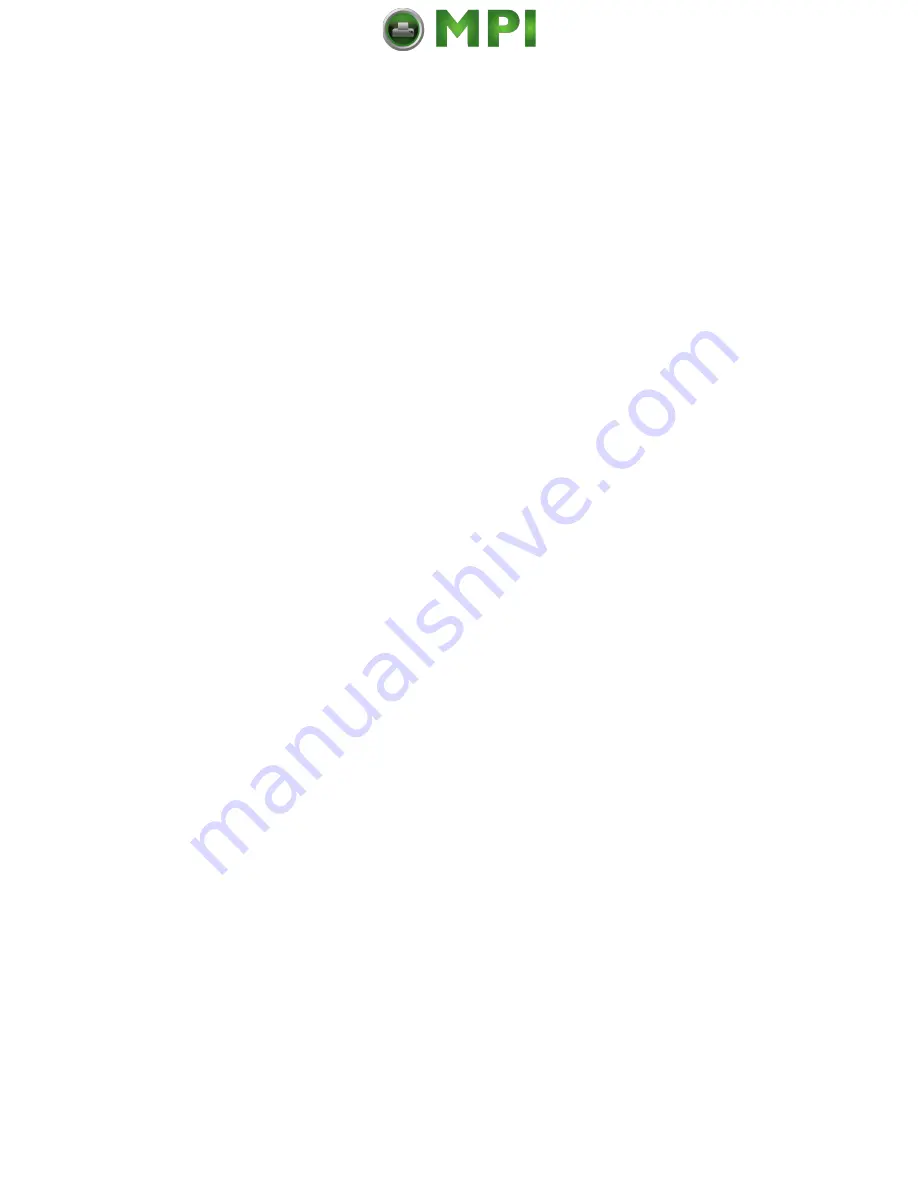
40
4.27
DC Distribution CCA replacement
TOOLS REQUIRED
3 mm hex driver
#1 Philips screwdriver
1.
Power down the printer and remove the power cord from the power
source. Remove the printer back panel.
2.
Check that the leads are all properly labeled before removing.
Carefully remove the quick connect terminals watching their labels for
reassembly. Disconnect J14 and J45 connectors.
3.
Using the #1 Philips screwdriver remove the four screws in the
corners of the distribution board and remove the board.
4.
Remount the new board with all four screws.
5.
Reconnect J14 and J45.
6.
Reconnect the lugs to the board confirm each connector is on its
proper terminal before powering up the printer.
7.
Reconnect the printer to power source and power up the printer.
Verify proper operation with short print run from console. Disconnect
the printer from the power source.
8.
Replace the printer back panel. Reconnect the printer to the power
source. Return the printer to service.
4.28
Bus board replacement
TOOLS REQUIRED
3 mm hex driver
1.
Power down the printer and remove the power cord from the power
source. Remove the printer back panel.
2.
Disconnect the three connectors from the Microprocessor board and
remove the Microprocessor board.
3.
Verify that all connectors are properly labeled. Disconnect the P7, P8,
P9, P10, P11, P12, and P13 from the bus board. Remove the power
connectors from terminals E3, E6, and E7.
4.
Using the 3 mm hex driver remove the six screws securing the cage
to the central panel and remove the card cage. Remove the bus
board from the printer.
5.
Place the new bus board into the printer. Reconnect the P7, P8, P9,
P10, P11, P12 and P13 connectors. Reconnect the E3, E6, E7 and
power connectors.