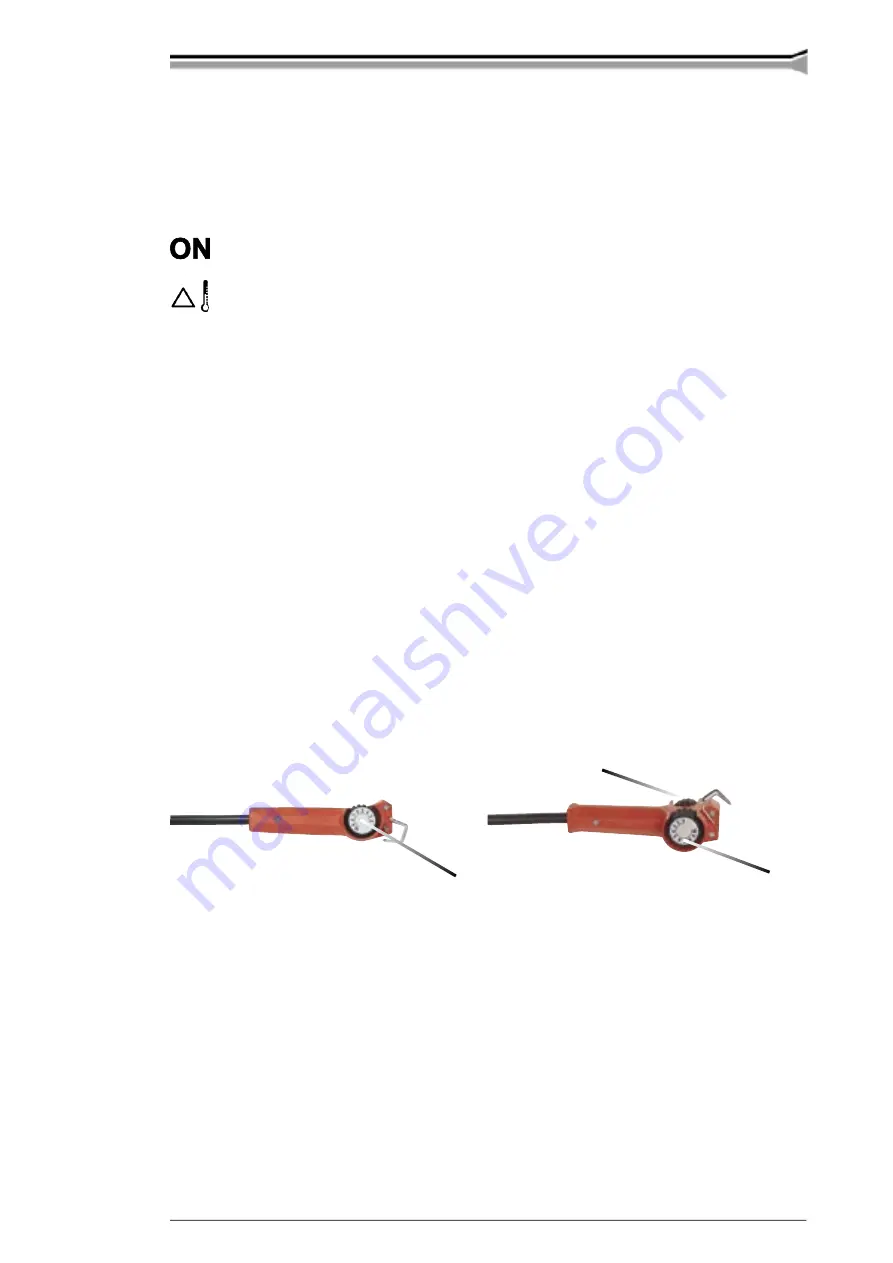
R61
R62
R61
3.2. LOCAL/REMOTE CONTROL OF WELDING CURRENT
You can control the welding current either from local control R11 of the machine or from a
control which is connected to the remote control unit, the switch S12 should be in the remote
control units: C 100C, and C 100D, see page 3
Pilot lamps
The pilot lamps of the machine report about the electric operation:
The green pilot lamp H11 for readiness for use is always on, when the machine is
connected to mains supply and the main switch is in I-position.
The yellow pilot lamp H12 of the thermal shield is on, when the thermostat has released
due to overheating of the machine. The cooling fan is cooling down the machine and by
blacking out of the pilot lamp the readiness for welding is automatically returned.
3.3. ADJUSTMENT FOR MMA DYNAMICS
On the rear of the MASTER there is a tool-controlled adjustment for MMA dynamics. With this
control you can adjust behaviour of the arc according to electrode type and your own likings.
The adjustment has influence on behaviour of the machine in drop short circuits.
Adjustment in minimum: Welding at its softest, arc pressure low
Adjustment in maximum: Welding at its roughest, arc pressure high
Recommendable initial adjustment is in the middle of the scale
3.4. ELECTRODES TO BE WELDED
By the MASTER power sources you can use all electrodes designed for DC or AC welding
within the current limits of the machine in question.
The MASTER power sources are not suitable for carbon arc gouging or cutting.
3.5. REMOTE CONTROL DEVICES AND CABLES
C 100C
Control of MMA/TIG welding current (R61), memory scale 1-10.
C 100D
Rough control (R61), memory scale 1-10, and fine c/- (R62) for MMA/TIG welding
current.
16c Extension cable for remote control 4 poles
20 Return current cable
21 Cable for MMA welding
C 100C, C 100D Remote control devices, see also pages 3 and 6
MASTER 2200/0530 – 7
© KEMPPI OY