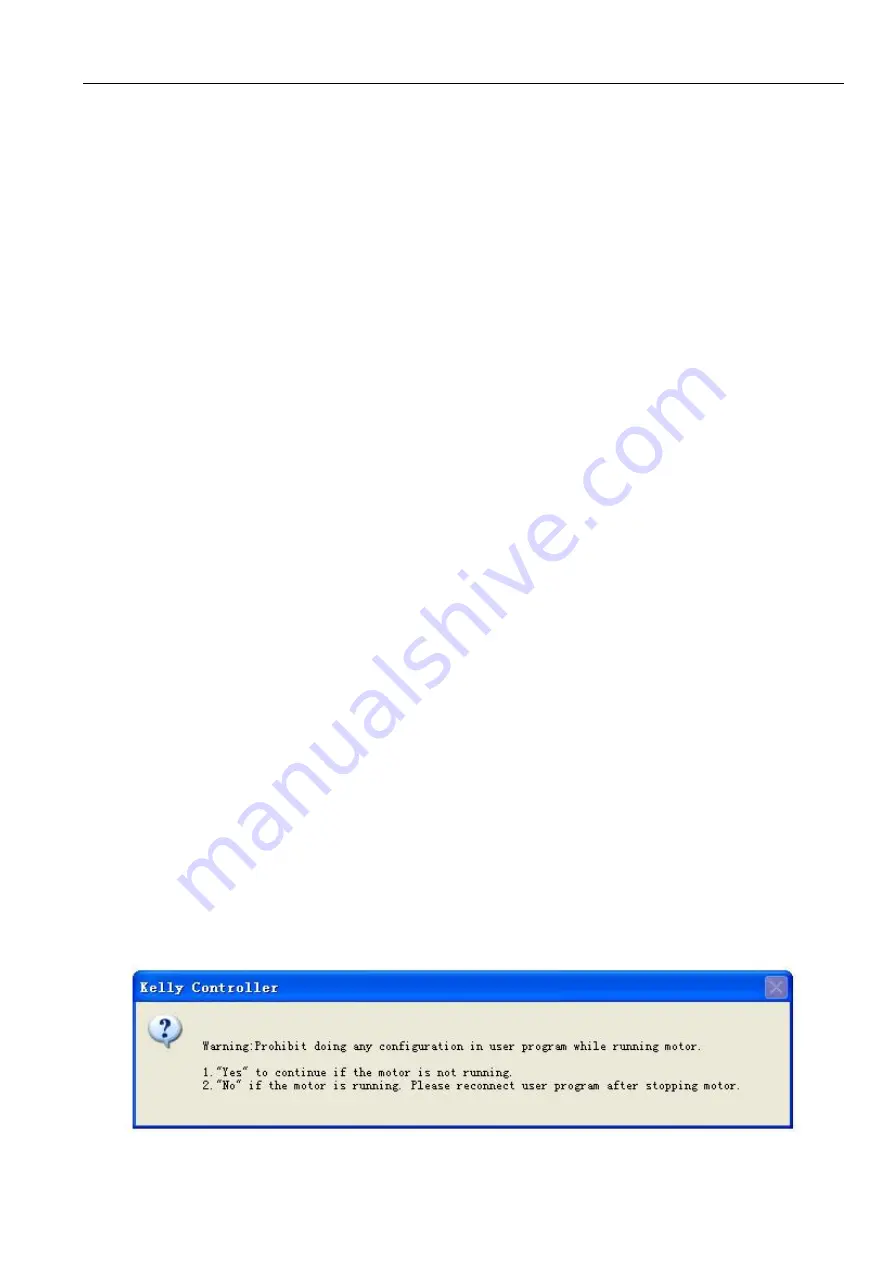
Kelly KHS High Voltage Sine Wave Brushless DC Motor Controller User
’s Manual
V 1.10
2
Chapter
1 Introduction
1.1 Overview
This manual introduces the Kelly KHS high voltage sine wave brushless DC motor
controllers‟ features, their installation and their maintenance. Read the manual carefully and
thoroughly before using the controller. If you have any questions, please contact the support
center of Kelly Controls.
This programmable motor controller provides efficient, smooth and quiet controls for
on-road electric vehicles, and other industrial applications. It is mainly supposed to solve noise
problems of BLDC motor driving application. KHS controller can not support sensorless
brushless motor. Compared with traditional square wave control technology, this technique
based on sinusoidal wave driving technology can reduce the operation noise and 1/3 switching
loss, which will meets the noise reduction and efficiency requirements in the application of DC
brushless motor. It uses high power IGBT
‟s
and, SVPWM and FOC to achieve more efficiency,
up to 99% in most cases. A powerful microprocessor brings in comprehensive and precise
control to the controllers. It also allows users to adjust parameters, conduct tests,
and obtain
diagnostic information quickly and easily. People can program the KHS controller on PC
software and Android App. There is one more choice for customers to program KHS controller
now. The APP software is based on Tablet with Android OS. Customers may add a Z-TEK USB
to RS232 cable for programming KHS controller if they want to use Android Tablet.
Both PC software and Android APP can provide one screen to monitor the controller
parameters. Sometimes people can use a small Android Tablet as display device.
It is designed by opto-isolated technology. We specify 10-30V for power supply
which must be isolated from main battery pack B+/B-.You may use an isolated DCDC
converter or a separate 12V battery for power supply. KHS-I is supposed to work with
BLDC motor with hall sensors. KHS-IPS can work with brushless motor with Sin/Cosin
speed sensors.
As of high voltage controller, people need to do some settings before doing
identification angle operation. It includes a pre-charge circuit board between B+ and +
terminal. Firstly connect a lower volt such as 24V-72V to + terminal, customers must set
0V for pre-charge voltage in user program before doing controller
‟s auto_Identification.
When the identification angle operation is finished successfully, customers need to set
up the pre-charge voltage and pre-charge time in the user program. Then connect high
volt battery positive to B+ to do pre-charge voltage you set up previously.