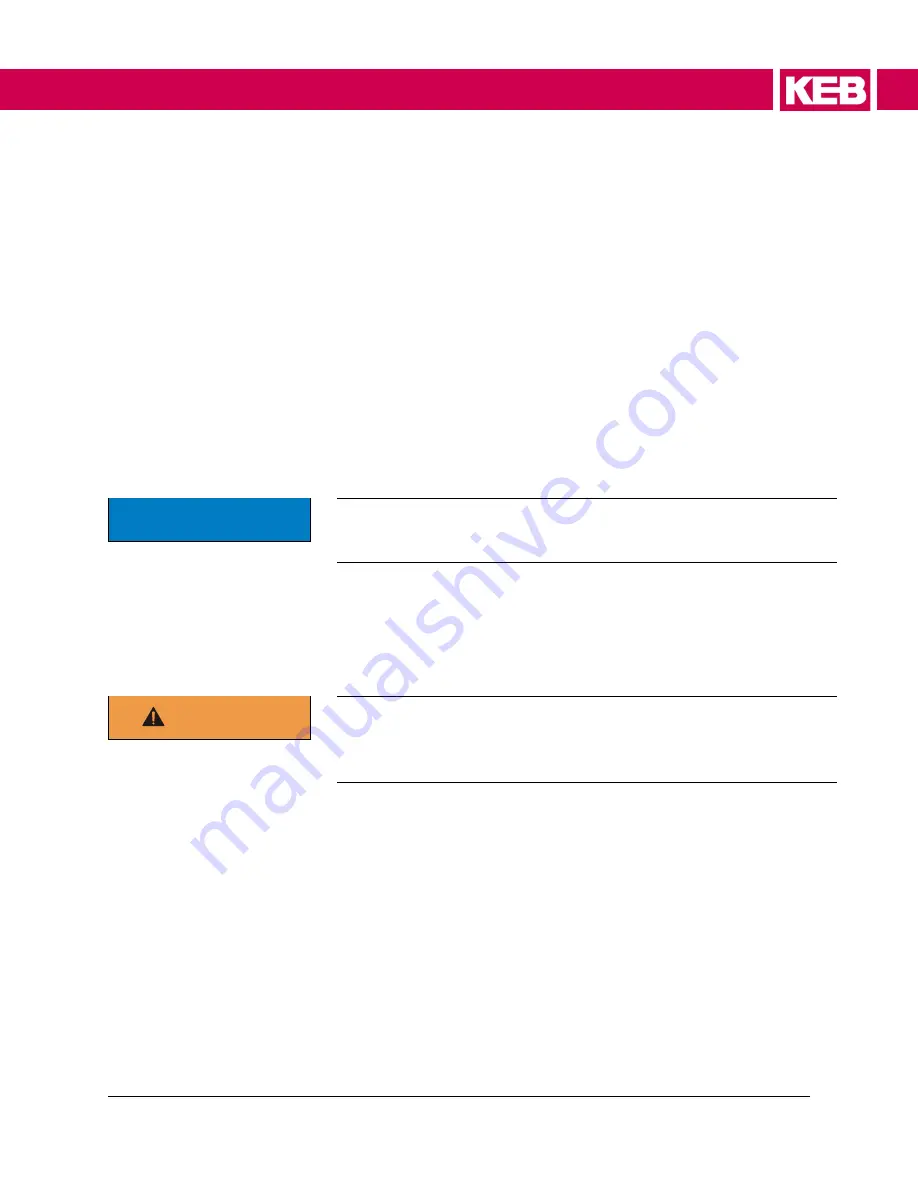
Maintenance and Troubleshooting
©
2021 KEB America, Inc.
33
7.1.2 Adjusting the Air Gap
1.
Use a feeler gauge to test the air gap at several points around
the brake’s
circumference.
a.
If the air gap is larger than X
max
the air gap needs to be adjusted.
2.
Remove the armature and hub (if included) by reversing the installation steps for the
armature assembly.
3.
Adjust the air gap to width X.
a.
For flange-mounted brakes with hubs, adjust the hub position on the shaft until
the air gap is at width X.
b.
For flange-mounted brakes without hubs, adjust customer provided hub until the
air gap is at width X. Adjusting shim washers between the armature (6) and the
mounting surface (7) can be used until the air gap is at width X (see Fig 9).
4.
When adjustment is complete, fasten the armature assembly and hub (if included) to
the shaft or mounting surface.
5.
Use a feeler gauge to test the air gap to ensure the adjustment was performed
correctly. Repeat steps 2-4 if the air gap is not at width X.
NOTICE
Shaft-mounted brakes are shipped with a factory set air gap which
cannot be adjusted. Shaft-mounted brakes require replacement if the
air gap grows beyond the maximum X
max
.
7.1.3 Cleaning the Brake
The COMBINORM brake should be cleaned prior to installation as well as periodically
during regular maintenance. The brake should be disassembled prior to cleaning. Clean
the armature and friction lining with an alcohol based brake cleaner.
WARNING
The friction surfaces must be thoroughly cleaned and dried prior to
returning the brake to operation.
Any remaining cleaning liquid or other foreign contaminants on the
friction surface may result in a loss of braking torque.