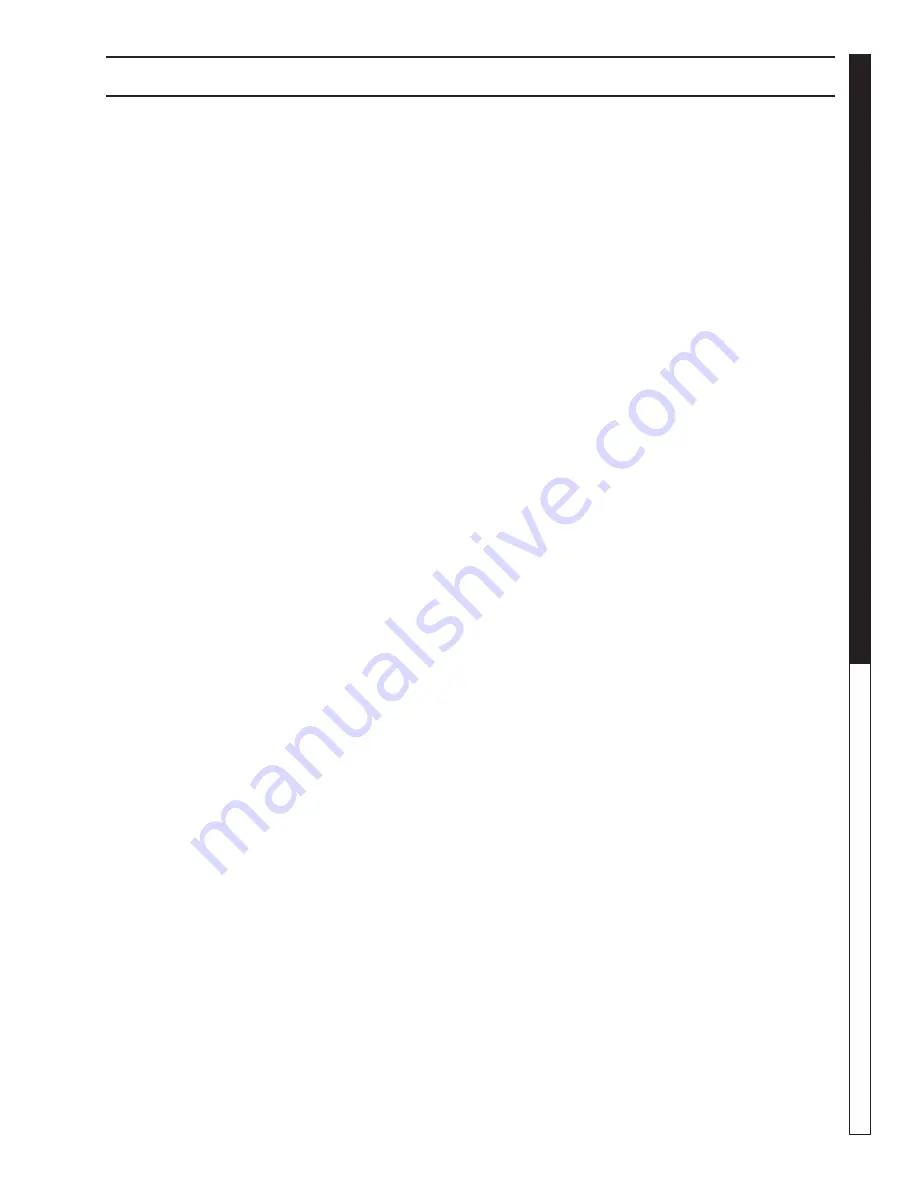
620-622 • 9.800-187.0 • Rev. 9/10
11
PRESSURE WASHER
OPERATOR’S MANUAL
Deliming Coils:
Periodic flushing of coils is recommended.
Step 1 Fill the float tank with 4 gallons of water,
then add 1 lb. of deliming powder.
Mix thoroughly.
Step 2 Remove nozzle from the wand assembly
and put the wand and spray gun into float
tank. Attach a nylon stocking to the end of
the wand to collect debris.
Step 3 Turn pump switch on, allowing solution to
be pumped through coils and back into the
float tank. Solution should be allowed to
circulate 2 - 4 hours.
Step 4 After circulating solution, clean and drain
float tank and flush entire system with fresh
water. Replace nozzle in wand.
Spray Nozzles:
Each machine is equipped with four spray nozzles.
Different spray nozzles are calibrated for each
machine depending on the flow and pressure of
that particular model. Spray nozzles vary in bore
size and angle of spray. Popular spray angles are
0°, 15°, 25°, 40°. When ordering, please specify size
and angle of nozzle. Nozzle size for each machine
is located on the serial plate.
Unloader Valve:
The unloader valve traps pressure in the line when
the spray gun is closed. Machines with unloader
valves are preset and tested at the factory before
shipping.
Tampering with the factory setting may cause per-
sonal injury and/or property damage and will void
the manufacturer's warranty.
Winterizing Procedure:
Damage due to freezing is not covered by warranty.
Adhere to the following cold weather procedures when-
ever the washer must be stored or operated outdoors
under freezing conditions.
During winter months, when temperatures drop
below 32°F, protecting your machine against freezing is
necessary. Siphoning a small amount of antifreeze into
the system is recommended. This is done by pouring a
50/50 mix of antifreeze and water into the float tank and
then siphoning 100% antifreeze through the detergent
line with the pump on. If compressed air is available,
an air fitting can be screwed into float tank strainer
fitting and, by injecting compressed air, all water will
be blown out of the system.
Low Pressure Diagnosis:
Refer to Troubleshooting Chart for low pressure. If, by
referring to the chart, the trouble is found to be either
the unloader or pump, your next step is to determine
which is the problem. This can be done by eliminat-
ing the unloader from the system and attaching the
discharge hose directly to the pump. If high pressure
is present, then the unloader needs repairing.
CAUTION: When using this procedure to test com-
ponents, keep spray gun open at all times.
Removal of Soot and Heating Coil:
In the heating process, fuel residue in the form of soot
deposits may develop between the heating coil pipe
and block air flow which will affect burner combustion.
When soot has been detected on visual observation,
the soot on the coil must be washed off after following
the coil removal steps which follow.
Coil Removal:
Removal of the coil, because of freeze breakage or
to clean soot from it, can be done quickly and easily.
1. Disconnect hose from pump to inlet side of
the coil.
2. Carefully disconnect thermostat sensor,
making sure you do not crimp capillary tube.
3. Remove all the fittings from the inlet and
discharge side of coil.
4. Remove the burner assembly from the
combustion chamber.
5. Remove the 3-3/8" bolts from each side of coil
and tank assembly (these bolts are used to
fasten tank and handles to chassis).
6. Remove the two bolts which are underneath the
bottom wrap (to keep the coil from moving).
7. Remove tank top wrap exposing insulation
and coil.
8. Bend back insulation tabs.
9. Carefully fold back the insulation and remove
insulation retainer plates and coil.
1 0. Replace or repair any insulation found to
be torn or broken.
1 1. To reinstall new or cleaned coil, reverse
steps 9 through 1.
PREVENTATIVE MAINTENANCE & SERVICE