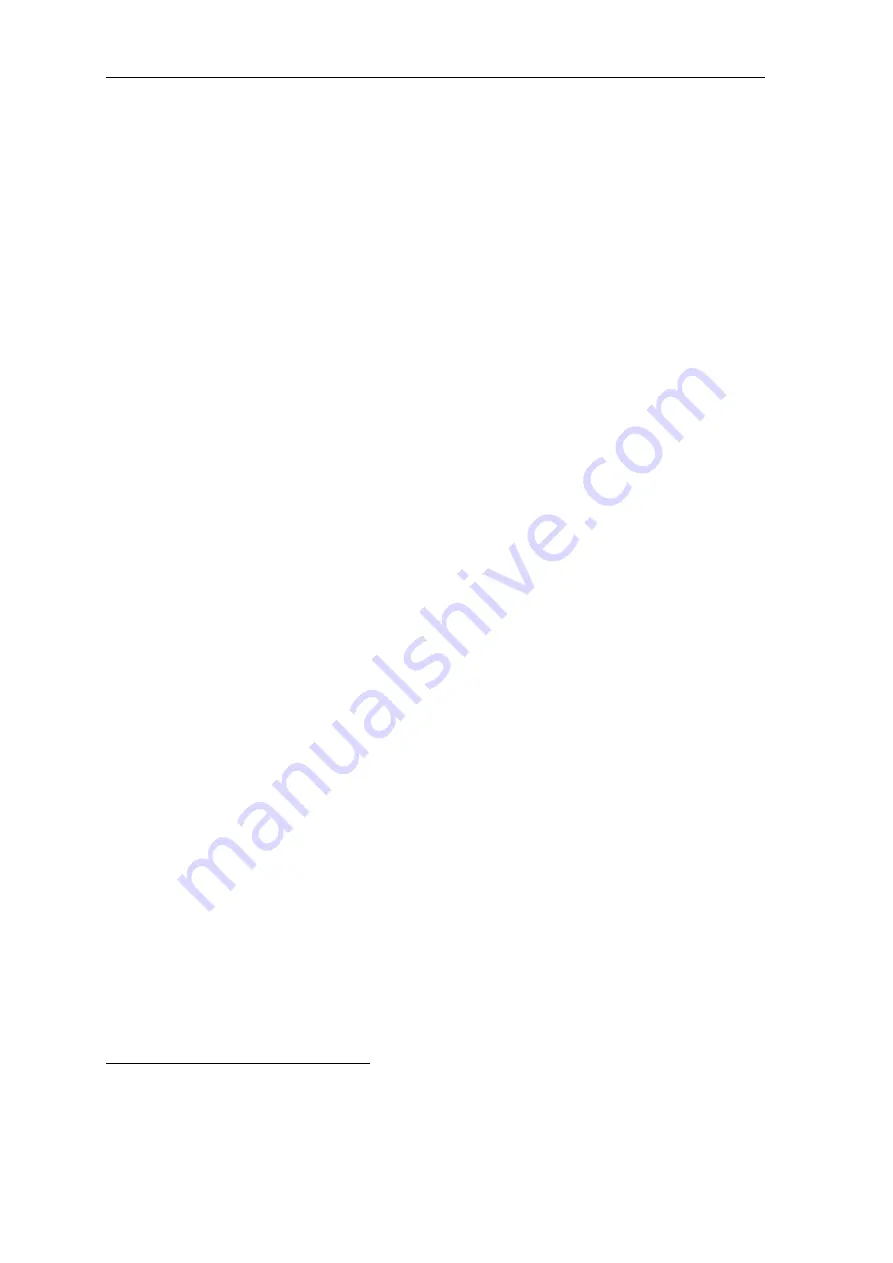
Nesis
— User’s Manual
1.2
Principles of the Operation
The magnetic field sensors are used to measure the magnetic field vector. This vector
is needed to determine the airplane magnetic and true heading. The later also needs
magnetic declination, which is automatically calculated from the world magnetic model
2
when airplane position is known. Note that the magnetic field sensor is optional and
Nesis works well without it.
Assuming coordinated flight we calculate the referencing attitude from the gravity vector and
heading. These values are then compared with the short-term prediction of the attitude. Non-
linear Kalman filters are used to combine the short-term prediction and referencing attitude
solution into one most probable solution. This is what you see on the attitude indicator.
In a very similar way, short-term inertial position prediction is compared with the GPS
position. Again, Kalman filtering is used to obtain the final solution.
1.2.2
Engine Sensors
Engine related sensors are connected to the engine monitoring unit (Daqu). Daqu is designed
to be installed on the engine side of the firewall. This has two advantages:
Since the unit is close to the engine, all cables are short and no extensions are needed.
This means less weight and makes installation simpler, too.
We need only one tiny hole trough the firewall for the CAN bus cable. The cable
transfers all the information and provides the power supply for Daqu.
Daqu is designed to monitor engine sensors for various engines up to six cylinders (e.g. Rotax,
Jabiru, Lycoming). When an engine is equipped with proper sensors, it can measure engine
RPM, cylinder head temperature (CHT), exhaust gas temperature (EGT), oil pressure, oil
temperature, fuel pressure, fuel flow, fuel level, manifold pressure, carburetor air temperatue,
voltage, battery current, alternator current, coolant temperature and more. In the case of
gyrocopter or helicopter installation, it also reads the rotor RPM sensor. The results of all
these measurements are then transmitted on the CAN bus, where all other units are able to
read them.
1.2.3
Sensor Calibration
Almost all MEMS sensors have one common problem – they are sensitive to the temperature
change. This means that each unit must be calibrated individually. Each sensor of every
unit is measured at different temperatures and compared with reference values. Results
are optimized mathematically in order to minimise the sensor errors. Resulting calibration
coefficients are written into flash memory of the microcontroller. This procedure can be done
in our lab only, since some special tools and machinery are needed.
The compass calibration, however, is an exception. Although the electronic compass (Magu)
is carefully calibrated in our lab, it needs to be recalibrated in your airplane. Practically every
airplane has some magnetic material present in the compass surroundings. Such material
locally disturbs Earth magnetic field and compass must take this disturbances into account.
Please refer to section 6.5 on page 38 for more details.
2
The world magnetic model is maintained and updated by National Geophysic Data Center,
http://www.
ngdc.noaa.gov/geomag/
Version 2.0
8
©
Kanardia
2011