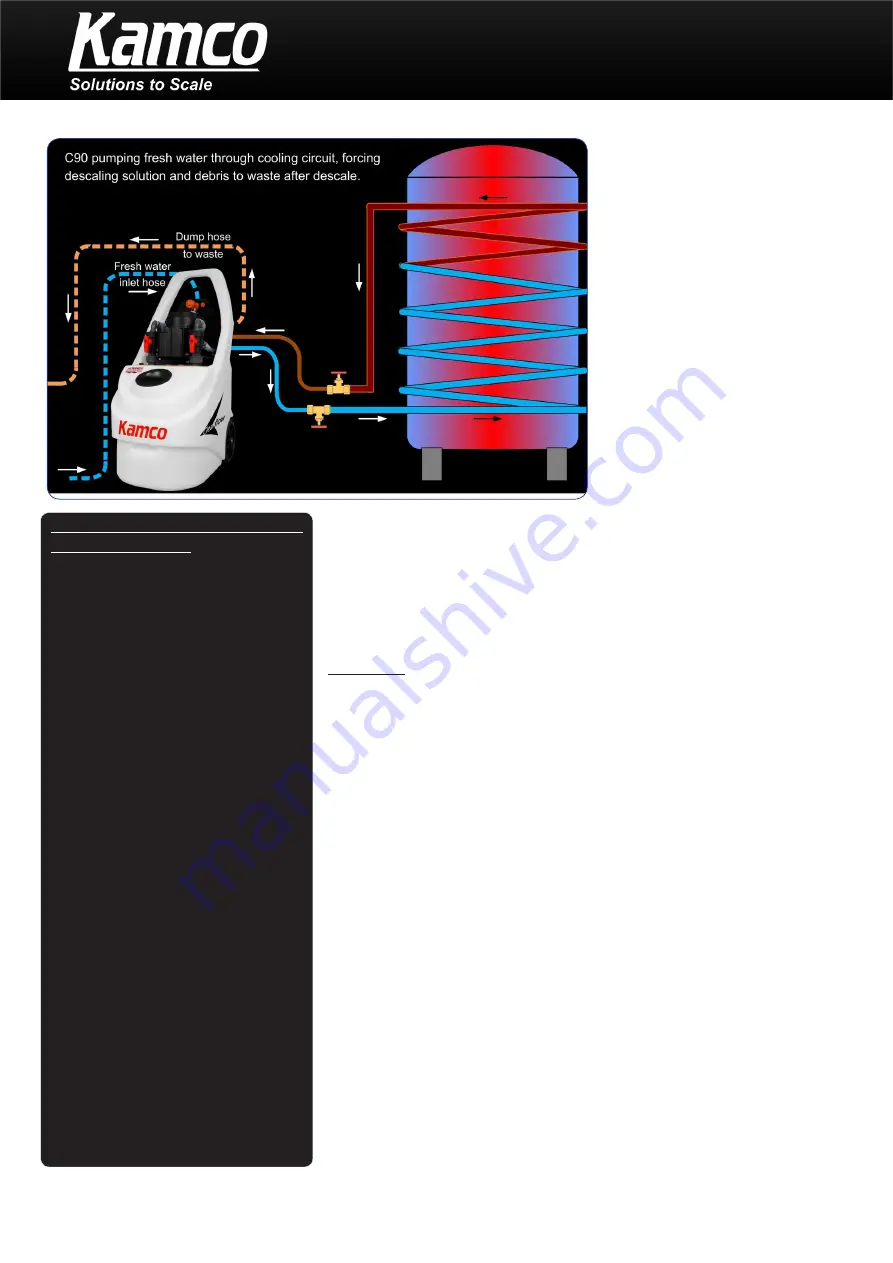
CHOICE OF DESCALING CHEMICAL AND
QUANTITY REQUIRED:
If the cooling coil is made of steel, or
stainless steel, use either SCALEBREAKER
SR or SCALEBREAKER FX, dependent on
the type of fouling. Scalebreaker FX will
remove both hard water deposits and
corrosion deposits, whilst Scalebreaker
SR is effective only on hard water scale.
SCALEBREAKER HD may be used with
copper coils, but should not be left in
circuit for more than two hours.
Do not use SCALEBREAKER HD with
stainless steel.
Calculate the amount of descaling
chemical required. As a guide, if
the volume of water in the cooling
circuit is approximately 100 litres,
use 10 litres descaling chemical (i.e. a
10% solution by volume). A weaker
solution may be used, but will take
longer to remove a given amount of
scale.
Heat may be applied into the coil, if
practicable, or it may be possible to
start descaling when the water in
the coil is still warm, to a maximum
of 50
o
C, and this will speed up
descaling.
NB. When descaling with any acid,
some hydrogen gas may be evolved.
Hydrogen is a flammable gas, and
the working area should be well
ventilated. Avoid smoking nearby,
or any other means of ignition.
PROCEDURE
1. Ensure an adequate water supply
to dilute or neutralise any chemical
leaks, or the spent descaling
chemical, so that disposal does not
contravene local regulations.
2. Isolate water inlet and outlet
connections to the cooling coil,
capping them off if necessary.
3. Couple flow and return hoses from
descaling pump to the water inlet
and outlet of the cooling coil to be
descaled.
4. If it is anticipated that descaling
is to be a routine maintenance
procedure, consider installing valved
tee-pieces in the flow and return
connections to the coil, terminating
in 1/2” or 3/4” BSP male threads. This
will enable immediate coupling of
the descaling pump across the coil
whenever descaling is required.
5. The pump connection to the lowest
connection onto the cooling coil
should be through a valve, as a
precaution. Failing this, if the
descaling pump is mounted below
the coil, power failure to the pump
would result in the head of water
overflowing the pump tank, unless
prevented by closing the valve.
(Scalebreaker FWF models have integral
valves suitable for this.)
6. Connections should be made so that
there is a closed circuit between
the pump output hose, through the
cooling coil to the return hose.
7. Venting of the carbon dioxide gas
evolved during descaling is achieved
through the pump tank filler cap
aperture. The cap should be screwed
on by no more than one quarter of
a turn. This is sufficient to vent the
gas, but at the same time reduces
fumes and prevents splashes.
8. Connect the pump to a suitable
earthed power supply. As the pump
will be used in a damp location, a
residual current circuit breaker plug
should be used.
9. The flow reverser handle points in
the direction of flow of the liquid. If
the handle points towards the hose
connected onto the normal water
inlet connection to the coil, that
will be the direction in which the
descaling pump will pump, and the
other hose will then be the return to
the pump tank.
10. Prior to adding descaling chemical
to pump tank, first ‘prove’ the circuit
with fresh water alone. Add water
to pump tank to approx. 4” (10cm)
above minimum liquid level, switch
on descaling pump, and immediately
Kamco Limited
Unit 9, Curo Park, Frogmore, St Albans. AL2 2DD. United Kingdom
Tel: +44 (0)1727 875020 Fax: +44 (o)1727 875335
E-mail: [email protected] www.kamco.co.uk
Guidance notes on descaling cooling coils