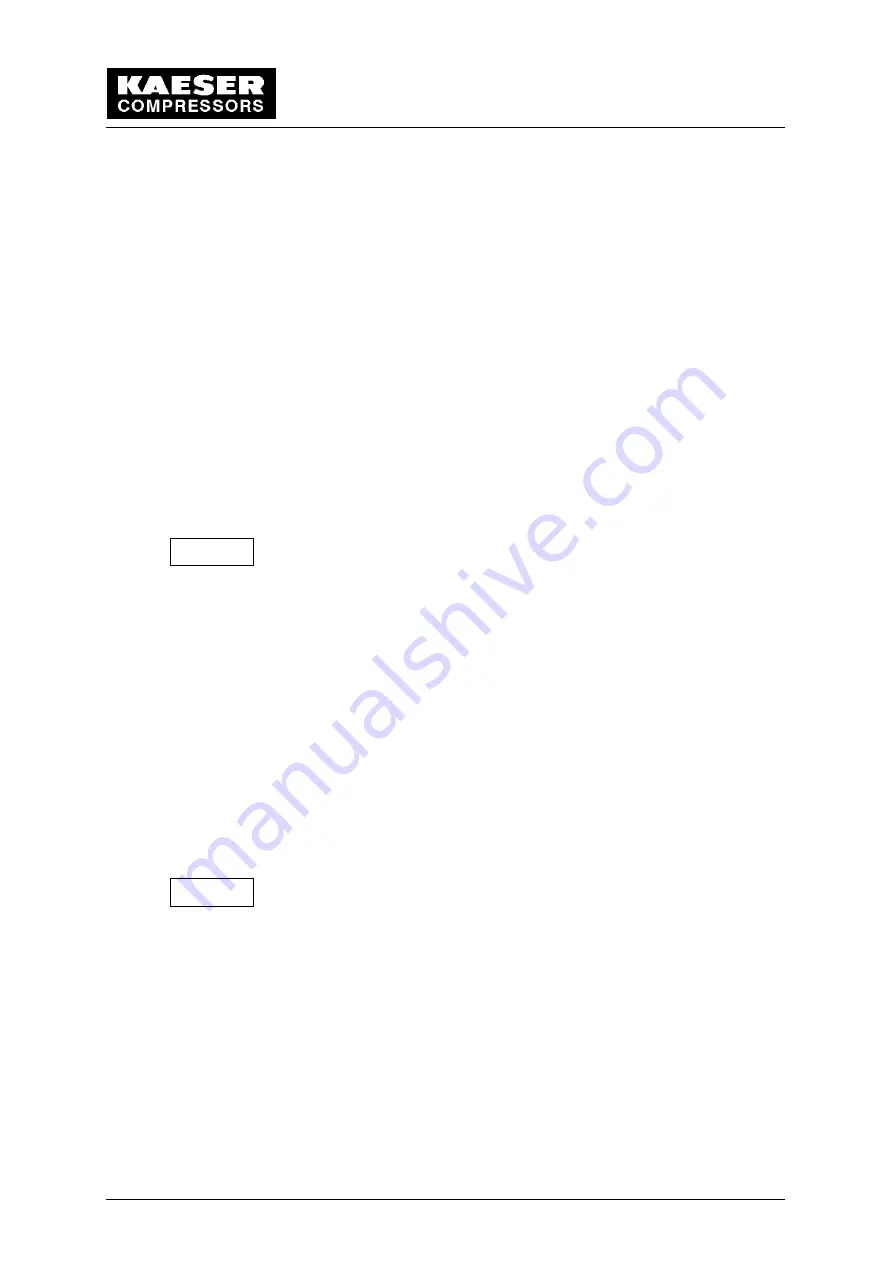
Safety
2 --- 9
-
Carry out oil changes according to the service manual.
-
Use only oils recommended by the manufacturer.
-
Do not mix cooling oils of different types.
-
The operating temperature stipulated must be kept to and checked constantly to avoid
condensate in the oil circulation.
-
If maintenance work is carried out on any part of the oil circulation system, top up the
oil in the oil separator tank to the maximum level afterwards, run the compressor for a
short period and keep it under constant observation. Check the oil level again and top
up with oil to replace the oil taken up by the piping and the cooling system.
-
Use the filter cartridge of the oil separator tank only as long as the pressure drop
across the filter is less than the 14.5 psi specified. Check constantly.
-
This machine is not explosion ---proof.
It may not be operated in areas in which specific requirements with regard to ex-
plosion protection are applied.
2.3
Electrical Power Supply
The main power supply and overcurrent protection must be installed
by a qualified electrician in accordance with NEC, OSHA and any appli-
cable local codes.
Compressor packages must be installed with a lockable main discon-
nect and fuses or other short-- circuit and ground fault protection de-
vice.
For fuse and wire recommendations, see chapter 1.4
Please note that the conductors, fuses and procedure are KAESER’s
recommendations. These recommendations do not supersede other
applicable codes.
2.4
Spare Parts
Safe and reliable operation of the compressor package is guaranteed only with KAESER
original spare parts and KAESER SIGMA cooling oil.
Use only original parts in assemblies subject to pressure.
2.5
Compressed Air System
If a compressed air system is extended or changed, verify that the blowoff pressure and
capacities of the safety relief valves on the air receiver tanks and in the system match the
rating of all the compressor packages installed.
Attention!
Attention!
Содержание SK 19
Страница 10: ...Technical Specification 1 6 ...
Страница 19: ...Construction and Operation 5 15 ...
Страница 20: ...Construction and Operation 5 16 ...
Страница 64: ...Appendix 11 60 11 Appendix 11 1 Wiring Diagram ...
Страница 65: ......
Страница 66: ......
Страница 67: ......
Страница 68: ......
Страница 69: ......
Страница 70: ......
Страница 71: ......
Страница 72: ......
Страница 73: ......
Страница 74: ......
Страница 75: ......
Страница 76: ......
Страница 77: ......
Страница 78: ......
Страница 79: ......
Страница 80: ......
Страница 81: ...Appendix 11 77 11 2 Spare Parts List ...
Страница 82: ......
Страница 83: ......
Страница 84: ......
Страница 85: ......