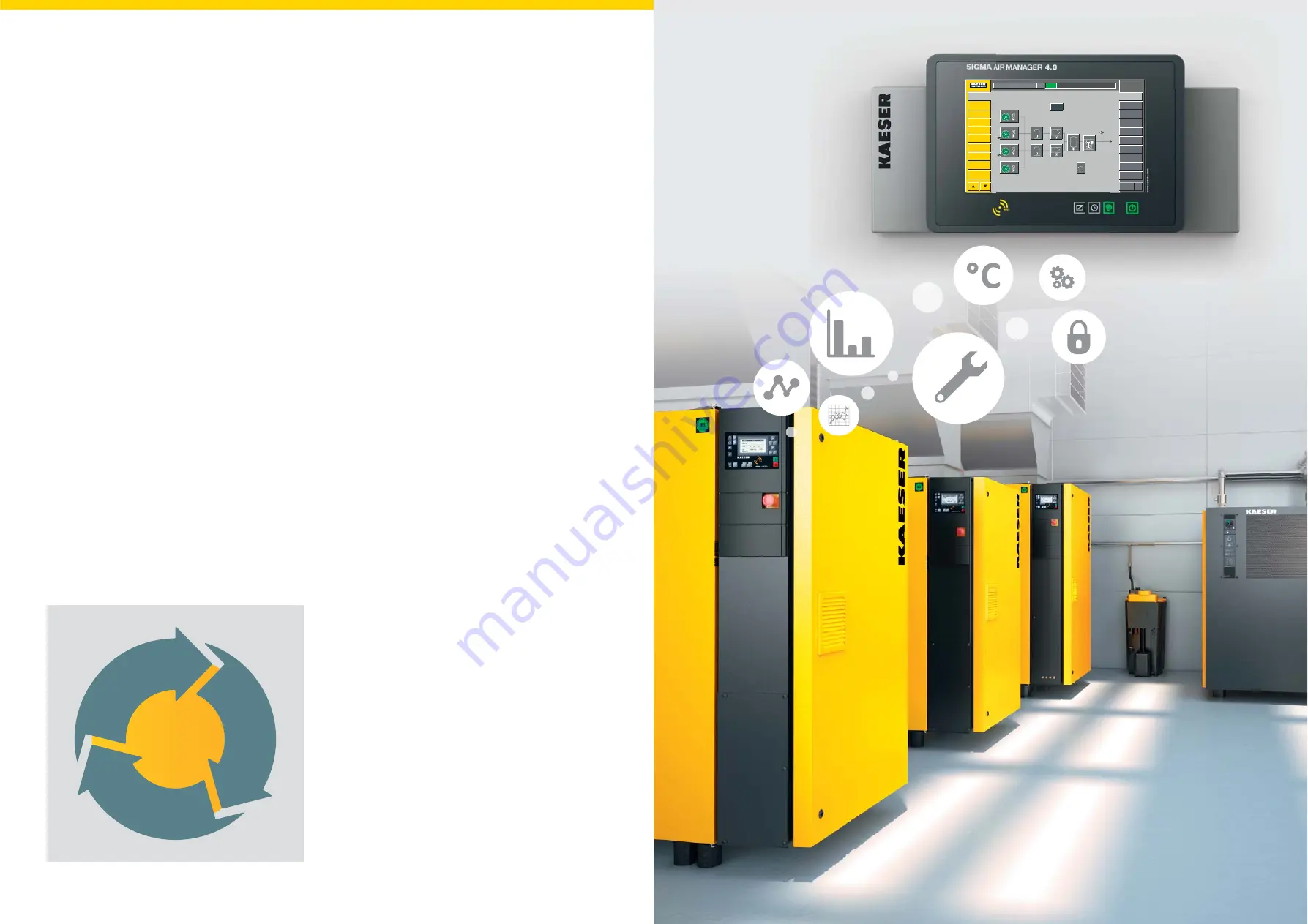
3D
advanced
Control
C
on
tro
l effic
iency
P
re
ss
ur
e f
lexi
bility
Sw
itc
hin
g
e
ffi
cie
nc
y
i
Status
Messages
Monitoring
Energy & costs
Control
SAM 4.0 Logic
Time control
Initial start-up
Con
fi
guration
Contact
Compressors
C1 - BSD 75
C2 - BSD 75
C3 - BSD 75
C4 - CSD 105 SFC
Dryer
Filter
Air receiver
Condensate
treatment
Station
SIGMA
AIR MANAGER
4.0
4
Automatic 10.04
bar
Maintenance
C1
C2
C3
C4
D1
D2
F1
F2
R1
DHS1
CT1
165.51
27.60
Power
Volumetric
fl
ow rate
kW
m³/min
Station
Industry 4.0
– that’s the key phrase to describe the 4th industrial revolution. In addition to the focus on “individualised
production processes” and “product-related information exchange”, a further factor is becoming increasingly important:
time – because time is money.
Based on advanced digital information technology
, Industry 4.0
interconnects man and machine, equipment and compo-
nents. This technological revolution is also about real-time information exchange – about data that can be transferred and
analysed in real-time. It is this capability that provides the decisive competitive advantage! This technology also opens up
new value added-potential by ensuring permanent utility and availability, for example, of important industrial equipment.
Identify, analyse, react: in real-time
The SIGMA AIR MANAGER 4.0 is the heart of the SIGMA
NETWORK and is key technology in the advanced world
of Industry 4.0. As the central mastermind, it controls the
entire compressed air supply system and – via the ‘Internet
of Things’ – is responsible for data streaming to a future
centralised application called KAESER SIGMA SMART
AIR. Process data from the compressed air system is
transmitted in real-time. Continuous analysis is subse-
quently performed with help from specialised algorithms in
order to make use of the gathered data, e.g. for Predictive
Maintenance purposes.
Centralised compressed air system monitoring (for Pre-
dictive Maintenance) is carried out in the KAESER DATA
CENTER, together with permanent energy management,
to ensure maximum effectiveness of the compressed air
supply system throughout its entire life-cycle.
KAESER SIGMA SMART AIR:
Predictive Maintenance
The SIGMA AIR MANAGER 4.0 provides the basis for
this future service, and, together with future use of the
SIGMA SMART AIR service, the following will be possible:
The combination of remote diagnostics and needs-based,
preventative maintenance helps assure maximum com-
pressed air supply dependability. Through availability of
compressed air system process data and the resulting
analysis, it is possible to identify the perfect point in the
future when your compressed air supply system should
be maintained and serviced. This prevents costly peri-
ods of downtime, increases energy ef
fi
ciency (thanks to
monitoring of key parameters) and allows compressed air
system performance to be precisely matched according to
demand throughout the entire life-cycle of the system.
This combination of remote diagnostics and demand-ori-
ented preventative maintenance ensures maximum availa-
bility and potentially reduces service costs by up to 30%.
Compressed air control technology 4.0 from KAESER
SIGMA AIR MANAGER 4.0
Innovative:
The Adaptive 3-D
advanced
Control
The algorithms in the Adaptive 3-D
advanced
Control orches-
trate interplay between all components and equipment in
your KAESER compressed air systems. As a result, just
the right amount of compressed air power is provided to
suit the speci
fi
c needs of the application, which in turn
assures maximum energy ef
fi
ciency at all times.
The unique Adaptive 3-D
advanced
Control continuously
analyses the relationship between various parameters
(e.g. switching and control ef
fi
ciency), and proactively
calculates the optimum combination from a range of many
in order to achieve optimum ef
fi
ciency. Not only are starts
and stops taken into consideration, but so too are idling
and frequency converter losses, along with pressure
fl
exibility. Moreover, the compressed air system’s pressure
performance value is optimised and average pressure is
reduced.
3
2