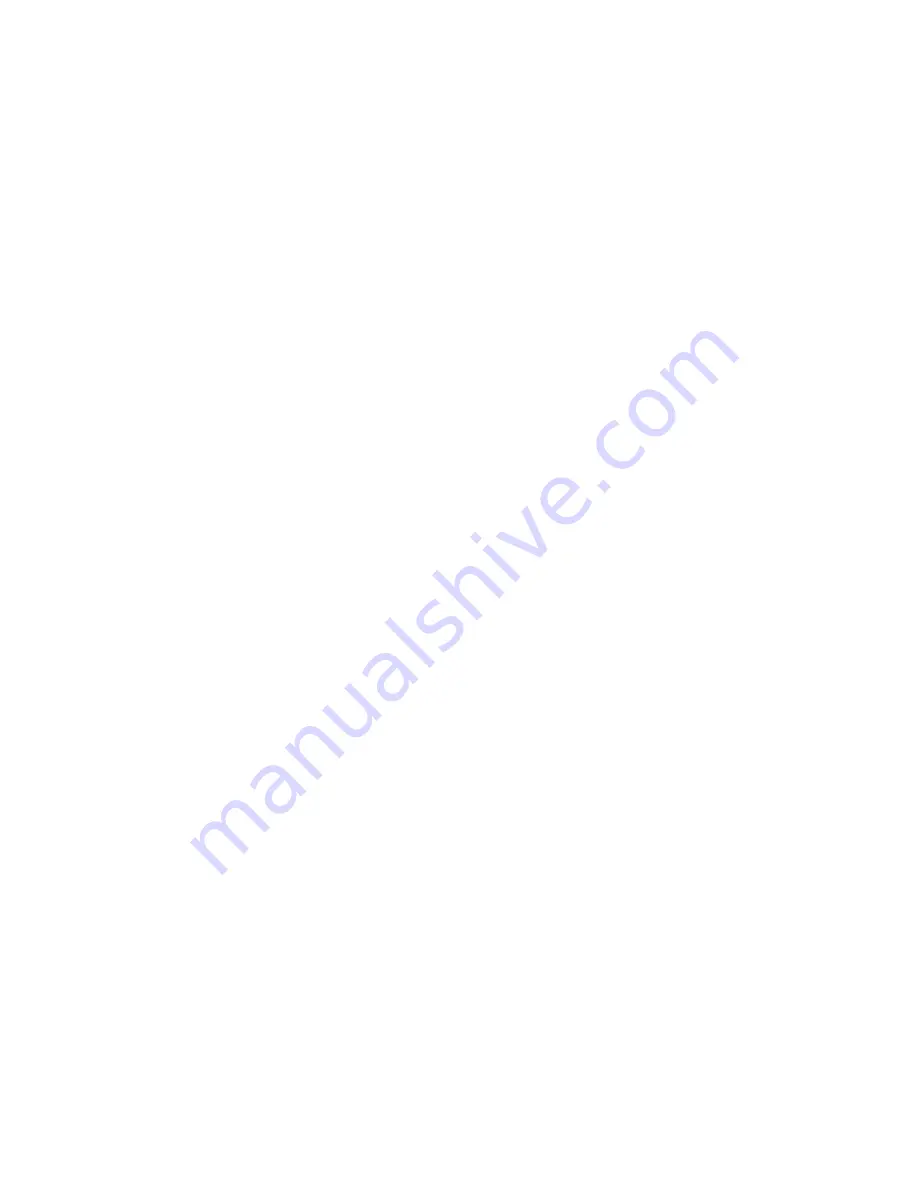
Annex F
Improved Accuracy Measurement Sub-System
The original measurement sub-system, whilst sufficient for general purpose indications of the
voltage, current and power output of the transceiver, did not completely capitalise on the
inherent accuracy available from a 12-bit A-D convertor.
The designers chose to optimise the speed of the main processing loop in the software, and
used calibration constants and factors that lent themselves to easy integer manipulation,
avoiding the use of floating point mathematics. With further analysis, it would seem that there
was sufficient processing capability available that using a more comprehensive set of
algorithms could significantly enhance the accuracy of the measurement sub-system with
little impact on speed.
Voltage Measurement
The voltage measurement system uses a precision potential divider comprising resistors R27
(33k / 1%) and R28 (10k / 1%) placed across the system bus. At a nominal input voltage of
13.8V, the output from this potential divider will therefore be:
13.8 * 10 / (33 + 10)
= 3.2093V
The A-D convertor is a 12-bit device, and uses the main 5V logic supply as the reference.
Assuming for the moment that this reference voltage is exactly 5.000V, this gives a
quantisation step of:
5000 / 2^12
= 1.2207mV
The scale factor for the voltage measurement is therefore:
10 / 43
= 0.23256
which gives a quantisation step for the voltage measurement system of:
1.2207 / 0.23256
= 5.249mV
Thus, in principle, it should be possible to adjust the calibration of the voltage measurement
system to have an overall accuracy of about ±5.25mV
39