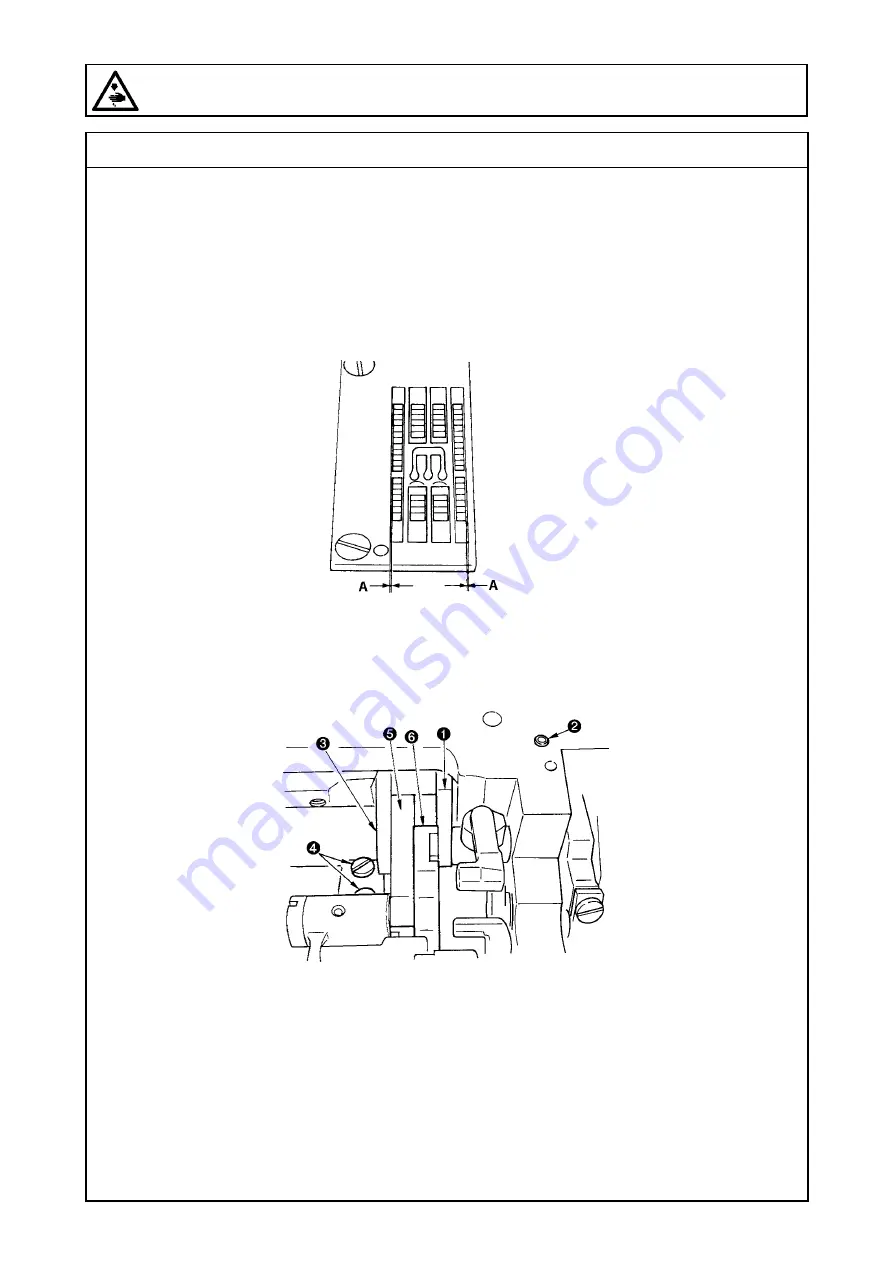
– 34 –
WARNING :
Turn OFF the power before starting the work so as to prevent accidents caused by abrupt start of the
sewing machine.
Standard adjustment
3. Lateral position of the feed dog
It is the standard of the lateral position of the feed dog that the left and right clearances A of the feed
dog in terms of the slots of the throat plate are parallel and equal.