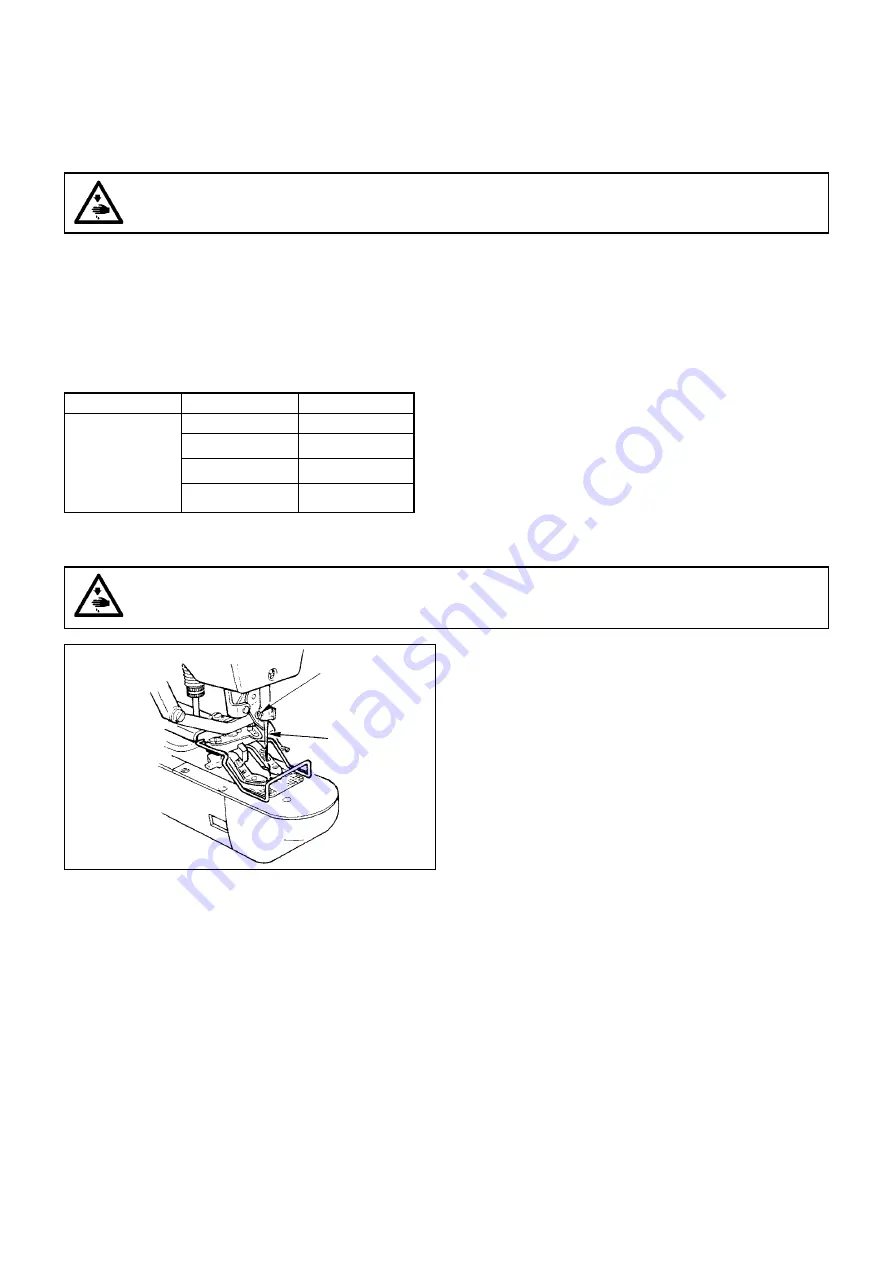
−
4
−
2. Needle and thread
Needle and thread will vary in accordance with the sewing
conditions. When using the needle and the thread, select
them referring to the left table. Cotton thread and spun thread
are recommended.
III. INSTALLATION OF THE SEWING MACHINE AND PREPARATION OF THE
OPERATION
As for the descriptions other than those described in the following items, refer to the Instruction Manual for the LK-1900B.
1. Installation of the table and stand
(Caution) 1. Be sure to install the table and stand on a flat place.
2. After the installation, be sure to fix the table and stand by locking the casters or adjusting the
adjuster.
3. When adjusting the height of the table, perform the work by two persons or more so as not to drop
the table.
Needle
Needle thread
Bobbin thread
#60
#80
#50
#60
#40
#60
#60
#60
DP x 17 #14
WARNING :
Turn OFF the power before starting the work so as to prevent accidents caused by abrupt start of the
sewing machine.
3. Attaching the needle
To attach the needle, loosen screw
❶
, insert needle
❷
fully
into the needle bar hole with the long groove facing toward
you, then tighten screw
❶
.
WARNING :
Turn OFF the power before starting the work so as to prevent accidents caused by abrupt start of the
sewing machine.
❶
❷
Содержание LK1903B-311
Страница 1: ...LK 1903B BR35 INSTRUCTION MANUAL ...