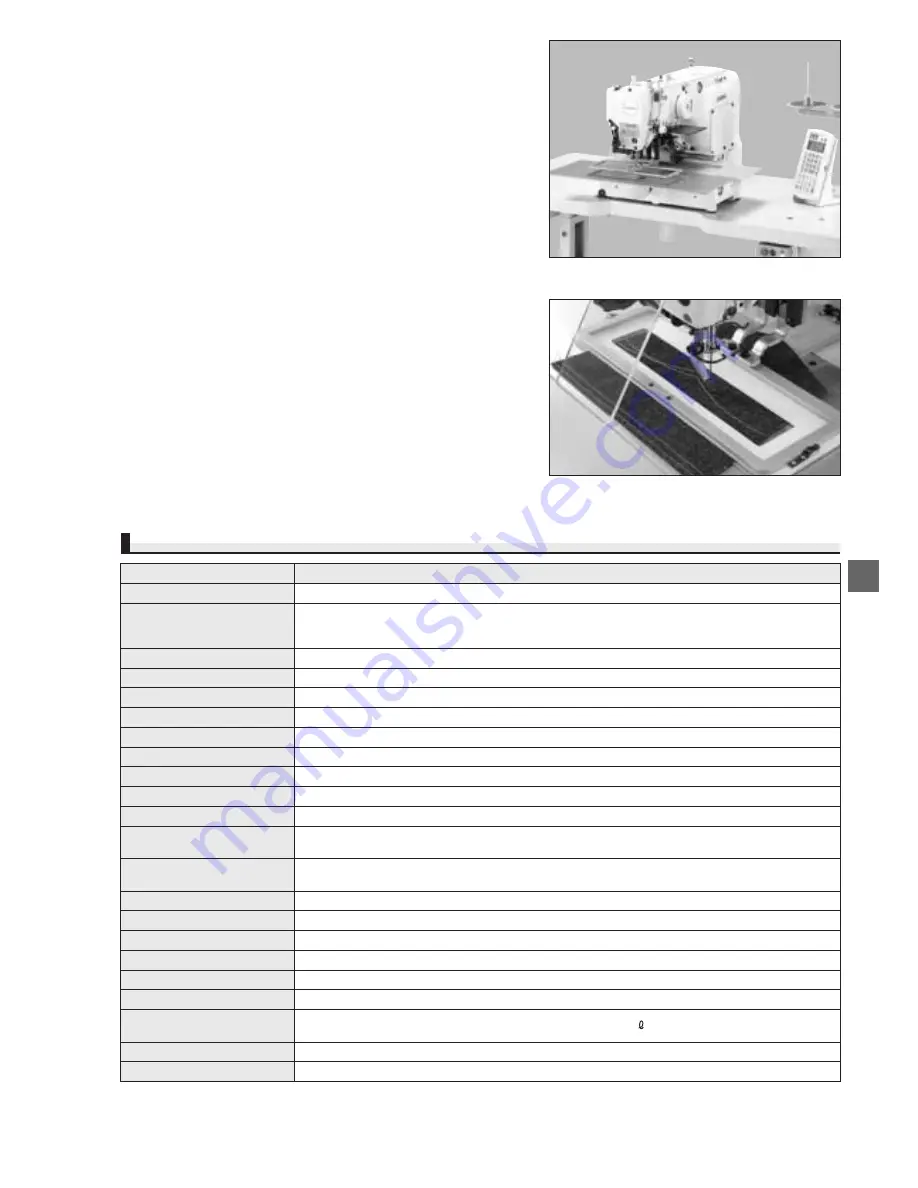
AMS-210DHL6100SZ (June, 2001) 1/2
AMS-210DHL6100SZ
〈
Sewing area: 60mm(L)
×
220mm(W)
〉
Computer-controlled Cycle Machine with an Input Function
for Topstitching Jean Pockets
SPECIFICATIONS
Model name
Sewing area
Max. sewing speed
Stitch length
Needle bar stroke
Lift of the feeding frame
Lift of the intermediate presser
Stroke of intermediate presser
Needle (at the time of delivery)
Thread
Hook
Memory medium
Number of stitches that
can be stored in memory
Number of patterns that
can be input
Enlarging/Reducing facility
Bobbin thread counter
Sewing machine motor
Power consumption
Lubrication
Lubricating oil
Compressed air and
air consumption
Total weight
Dimensions
AMS-210DHL6100SZ
60mm (L)
×
220mm (W)
2,500rpm (when stitch length is set to 0.1
〜
3.0mm)
2,300rpm (when stitch length is set to 3.1
〜
3.8mm)
2,000rpm (when stitch length is set to 3.9
〜
4.0mm)
0.1
〜
12.7mm
41.2mm
Standard 25mm (Max. 30mm)
20mm
Standard 4mm (0.5
〜
10mm)
DP
×
17 (#18), For JE: 135
×
17 (Nm110)
#50
〜
#2, B33
〜
B207, Nm=120/3
〜
10/3
Double-capacity shuttle hook
2DD/2HD 3.5" micro-floppy disk
Max. 360,000 stitches (max. 20,000 stitches/pattern)
Max. 691 patterns (2DD)/999 patterns (2HD)
1
〜
400% (0.1% step), by increasing/decreasing the stitch length or the number of stitches
Provided as standard
400W compact AC servomotor (direct-drive system)
Single-phase, 3-phase 600VA
Automatic
JUKI New Defrix Oil No.2 (equivalent to ISO VG32)
0.5
〜
0.55MPa (5
〜
5.5kgf/cm
2
), 1.8N /min
120kg
710mm (L)
×
1,200mm (W)
×
1,200mm (H)
AMS-210DHL6100SZ
●
Developed based on AMS-210D, the machine provides excellent
sewing capabilities and operability, with an expanded sewing area is
best suited for the "topstitching of hip pockets on jeans."
*
The AMS-210DHL6100SZ cannot be remodeled from the AMS-210D.
●
The machine achieves a maximum sewing speed of 2,500rpm,
substantially upgrading productivity(when the stitch length is equal to
or shorter than 3mm). In addition, the machine inherits outstanding
features of the AMS-210D such as one-touch calling of a sewing
pattern, easier workpiece placement with the increased lift of the
feeding frame, accurate workpiece positioning by the pneumatic
monolithic feeding frame, and reduced bobbin-thread replacement
with the newly adopted double-capacity shuttle hook.
11