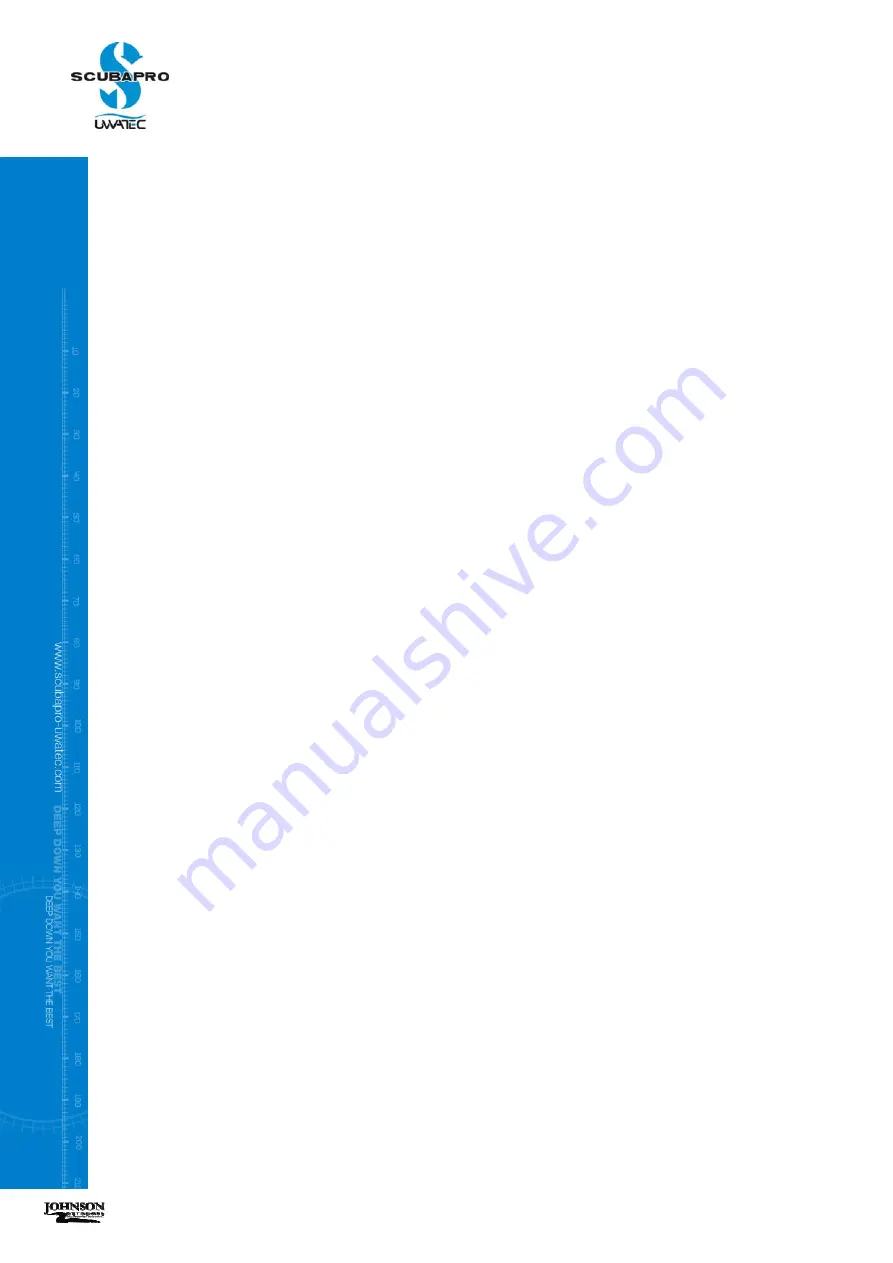
A 700 Maintenance Procedure
- 6 -
2. Make sure that the in halation effort adjustment knob is completely
unscrewed.
3. Connect an appropriate and well adjusted 1st stage to a full tank, connect
the 1st stage to the adjustment tool with the interstage pressure hose and
slowly open the tank valve.
4. Push slowly on the tool adjustment knob to counteract the thrust of the inter
stage pressure. Turn the knob slowly to look for the groove of the
adjustable orifice. As soon as the groove is found, slowly
unscrew
the
adjustable orifice until a small leak is detected, then turn the orifice
clockwise
to just stop the leak without having to turn more than 1/8 of a
turn on the orifice.
Note: 1/16 of a clockwise turn of the adjustment tool acting on the
orifice should stop the leak. If more than ¼ of a turn is required to
stop the leak, it means that the spring compression is too light and
the fine adjustment internal screw has to be screwed as follows: (This
procedure must only be applied to stop the leak described above)
With
the small screwdriver, (proceed by steps of ¼ of a turn at a time) screw the
internal fine spring tension adjustment in order to obtain a sharp stop of the
leak (1/16 of a turn) when adjusting the orifice with the tool. Do not exceed
more than 2 turns of clockwise adjustment on the fine adjustment screw.
Proceed as in paragraph 4.
5. Cycle the 2nd stage about 10 to 15 times by pushing on the purge, then
finalise the adjustment as indicated in paragraph 5.
6. Close the tank valve and purge the 2nd stage. Remove the adjustment tool
from the 2
nd
stage and assemble the hose with the universal tool with
moderate tightening torque. Do not over tighten.
7. Place back the hose sleeve.