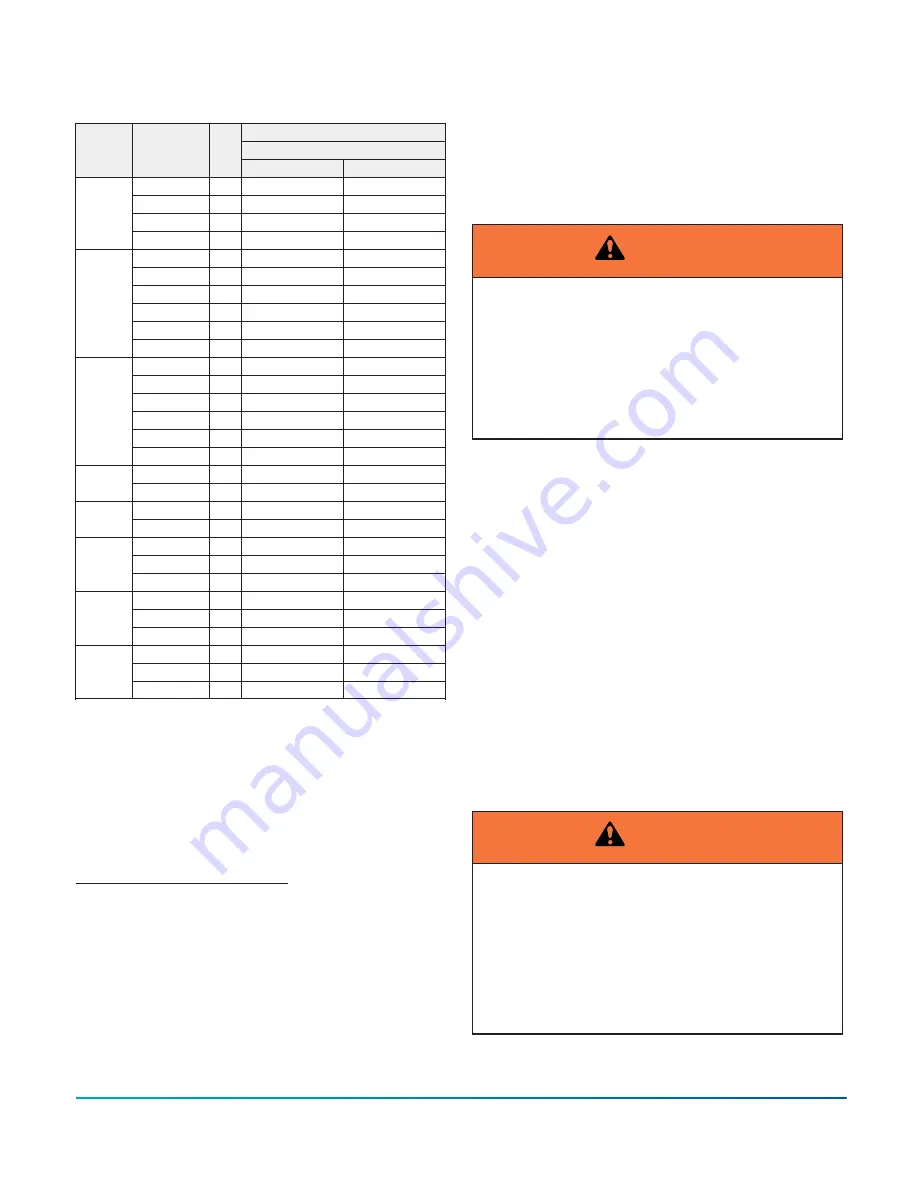
Table 26: Gas Heat Supply Air
Supply Air (CFM)
Heating
Model
(Size)
Gas Heat
Description Opt.
Min
Max
Low, NOx
L
900
1480
Low
D
890
1480
Med, NOx
M
900
1520
ZY04 (3)
Med
E
1060
1510
Low, NOx
L
1190
1980
Low
D
1210
1990
Med, NOx
M
1190
2020
Med
E
1200
2020
High, NOx
N
1200
1990
ZY05 (4)
High
F
1390
2190
Low, NOx
L
1480
2440
Low
D
1480
2470
Med, NOx
M
1520
2470
Med
E
1510
2510
High, NOx
N
1510
2500
ZY06 (5)
High
F
1490
2500
Med
E
1820
2990
ZY07 (6)
High
F
1790
3000
Med
E
1820
2990
ZYA7 (6)
High
F
1790
3000
Low
D
2260
3700
Med
E
2260
3700
ZY08
(7.5)
High
F
2260
3790
Low
D
2570
4210
Med
E
2560
4300
ZY09
(8.5)
High
F
2550
4290
Low
D
3030
4940
Med
E
3020
4940
ZY12 (10)
High
F
2990
5010
Gas connection
About this task:
The gas supply line can be routed within the
space and roof curb, exiting through the unit’s
basepan. Refer to Figure 11 through Figure 15 for
the gas piping inlet location. Typical supply piping
arrangements are shown in Figure 24. All pipe
nipples, fittings, and the gas cock are field supplied.
Gas piping recommendations:
1. A drip leg and a ground joint union must be
installed in the gas piping.
2. Where required by local codes, a manual shut-
off valve must be installed outside of the unit.
3. Use wrought iron or steel pipe for all gas lines.
Pipe dope should be applied sparingly to male
threads only. If local codes allow the use of a
flexible gas appliance connector, always use a
new listed connector. Do not use a connector
which has previously serviced another gas
appliance.
WARNING
Natural gas may contain some propane. Propane is
an excellent solvent and will quickly dissolve white
lead and most standard commercial compounds. A
special pipe dope must be used when assembling
wrought iron or steel pipe. Shellac based compounds
such as Gaskolac or Stalastic, and compounds such
as Rectorseal #5, Clydes’s or John Crane may be
used.
4. All piping should be cleaned of dirt and scale
by hammering on the outside of the pipe
and blowing out loose particles. Before initial
start-up, be sure that all gas lines external to
the unit have been purged of air.
5. The gas supply should be a separate line and
installed in accordance with all safety codes as
prescribed under “Limitations”.
6. A 1/8-inch NPT plugged tapping, accessible
for test gauge connection, must be installed
immediately upstream of the gas supply
connection to the unit.
7. After the gas connections have been
completed, open the main shut-off valve
admitting
normal gas pressure
to the mains.
Check all joints for leaks with soap solution or
other material suitable for the purpose.
NEVER
USE A FLAME.
WARNING
FIRE OR EXPLOSION HAZARD
Failure to follow the safety warning exactly could
result in serious injury, death or property damage.
Never test for gas leaks with an open flame. Use
a commercially available soap solution made
specifically for the detection of leaks to check all
connections. A fire or explosion may result causing
property damage, personal injury or loss of life.
INSTALLATION MANUAL ZY SERIES 3 - 10 ton 60 Hertz R-410A
79
Johnson Controls Ducted Systems
Содержание ZY Series
Страница 2: ...2 INSTALLATION MANUAL ZY SERIES 3 10 ton 60 Hertz R 410A Johnson Controls Ducted Systems ...
Страница 8: ...Nomenclature INSTALLATION MANUAL ZY SERIES 3 10 ton 60 Hertz R 410A 8 Johnson Controls Ducted Systems ...
Страница 139: ...Start Up Sheet INSTALLATION MANUAL ZY SERIES 3 10 ton 60 Hertz R 410A 139 Johnson Controls Ducted Systems ...
Страница 140: ...INSTALLATION MANUAL ZY SERIES 3 10 ton 60 Hertz R 410A 140 Johnson Controls Ducted Systems ...
Страница 141: ...INSTALLATION MANUAL ZY SERIES 3 10 ton 60 Hertz R 410A 141 Johnson Controls Ducted Systems ...
Страница 142: ...INSTALLATION MANUAL ZY SERIES 3 10 ton 60 Hertz R 410A 142 Johnson Controls Ducted Systems ...
Страница 143: ...INSTALLATION MANUAL ZY SERIES 3 10 ton 60 Hertz R 410A 143 Johnson Controls Ducted Systems ...