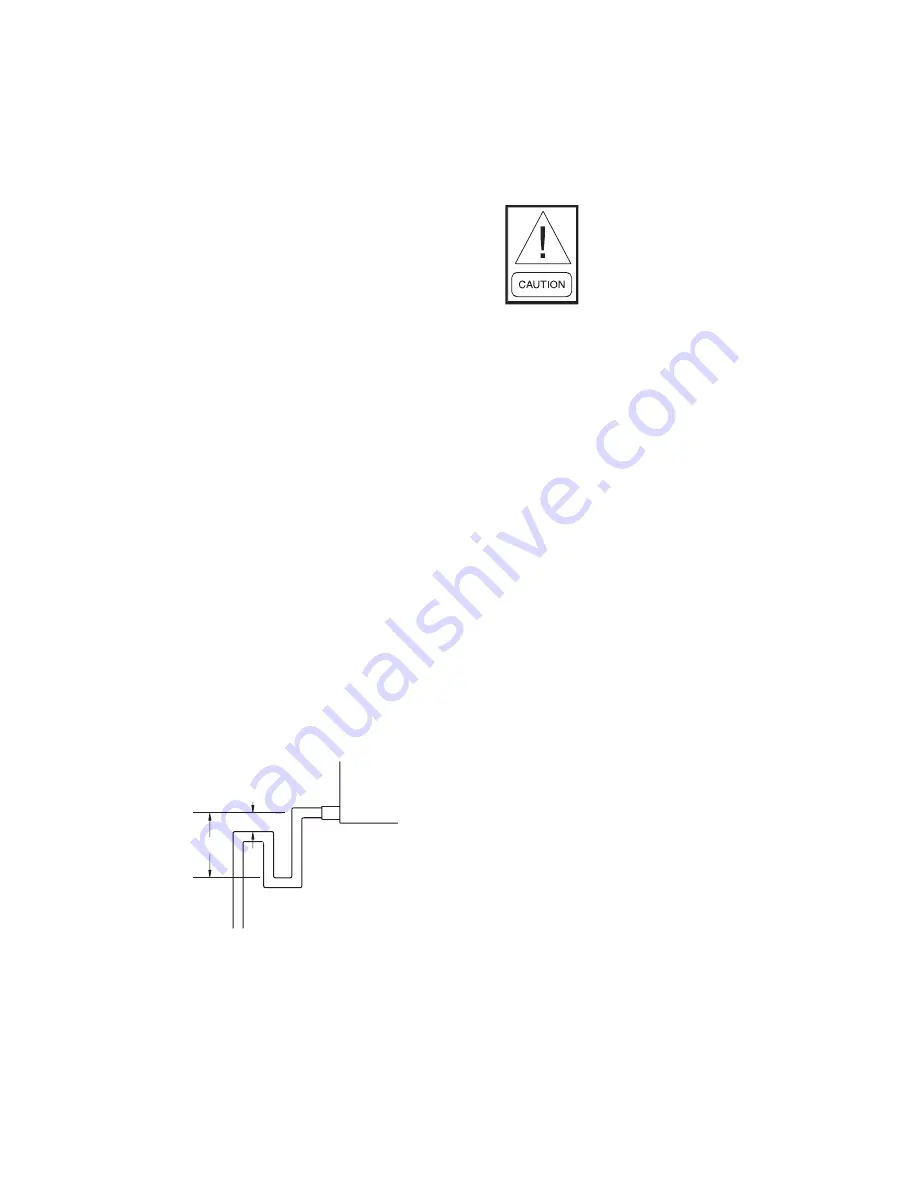
JOHNSON CONTROLS
9
FORM 130.13-NOM8 (1021)
Cooling/Heating Medium Connections
Coils are male sweat connection. Use appropriate
brazing alloy for system temperature and pressure.
Refer to equipment construction submittal drawing for
specific connection size.
MAXIMUM HYDRONIC COIL
OPERATING PRESSURE MUST NOT EXCEED 450
PSIG.
In the event that leaking or defective components are
discovered, the Sales Representative must be notified
BEFORE any repairs are attempted. All leaks should be
repaired before proceeding with the installation.
Valves must be secured and supported to avoid damage
to coil headers. All valves, pipes, and components must
be sufficiently supported to ensure structural integrity
and proper operation of the unit.
After system integrity has been established the piping
should be insulated in accordance with the project
specifications. ALL chilled water and drip pan piping
not located over drip pans must be insulated to prevent
damage from sweating. This includes factory and field
piping inside the unit cabinet.
The drain should always be connected and piped to an
acceptable disposal point. For proper moisture carry-off,
the drain piping should be sloped away from the unit
at least 1/8” per foot. A drain trap may be required by
local codes and it is strongly recommended for odor
containment.
If necessary, you can change hot water coil connection
handing on one and two row coils from left-hand to right-
hand (and vice-versa) by rotating the coil “like a steering
wheel” 180° about its central axis when facing the fins.
NOTE: When the coil is flipped, the vent will no longer
perform in a vent capacity. It is suggested that valve
packages are re-oriented during this process to bring
the valve actuator back to its original position.
Piping Connections
Toxic residues and loose particles
resulting from manufacturing and
field piping techniques such as joint
compounds, soldering flux, and metal
shavings may be present in the unit
and the piping system. Special con
-
sideration must be given to system
cleanliness when connecting to solar,
domestic or potable water systems.
Submittals and Product Catalogs detailing unit
operation, controls, and connections should be
thoroughly reviewed BEFORE beginning the connection
of the various cooling and/or heating mediums to the
unit All accessory valve packages should be installed
as required, and all valves should be checked for proper
operation.
If coil and valve package connections are to be made
with “sweat” or solder joint, care should be taken to
assure that no components in the valve package are
subjected to a high temperature which may damage
seals or other materials. Many two-position electric
control valves, depending on valve operation, are
provided with a manual-opening lever. This lever should
be placed in the “open” position during all soldering or
brazing operations. Valve bodies should be wrapped
with a wet rag to help dissipate heat encountered during
brazing. Use a brazing alloy to make connections. Soft
solder is not recommended.
If the valve package connection at the coil is made with
a union, the coil side of the union must be prevented
from twisting (“backed up”) during tightening to prevent
damage to the coil tubing. Over-tightening must be
avoided to prevent distorting the union seal surface
and destroying the union. In the case of field installed
valves and piping, the chilled water valve cluster should
be installed in such a way that any dripping or sweating
is contained in the auxiliary drip pan or other device.
Valves should be secured or supported to avoid damage
to coil headers.
“H” MUST BE AT LEAST
1 INCH PLUS CASING
STATIC PRESSURE
H
X
“X” MUST BE AT
LEAST 1 INCH
Condensate Trap
Trap detail for positive cabinet
static pressure