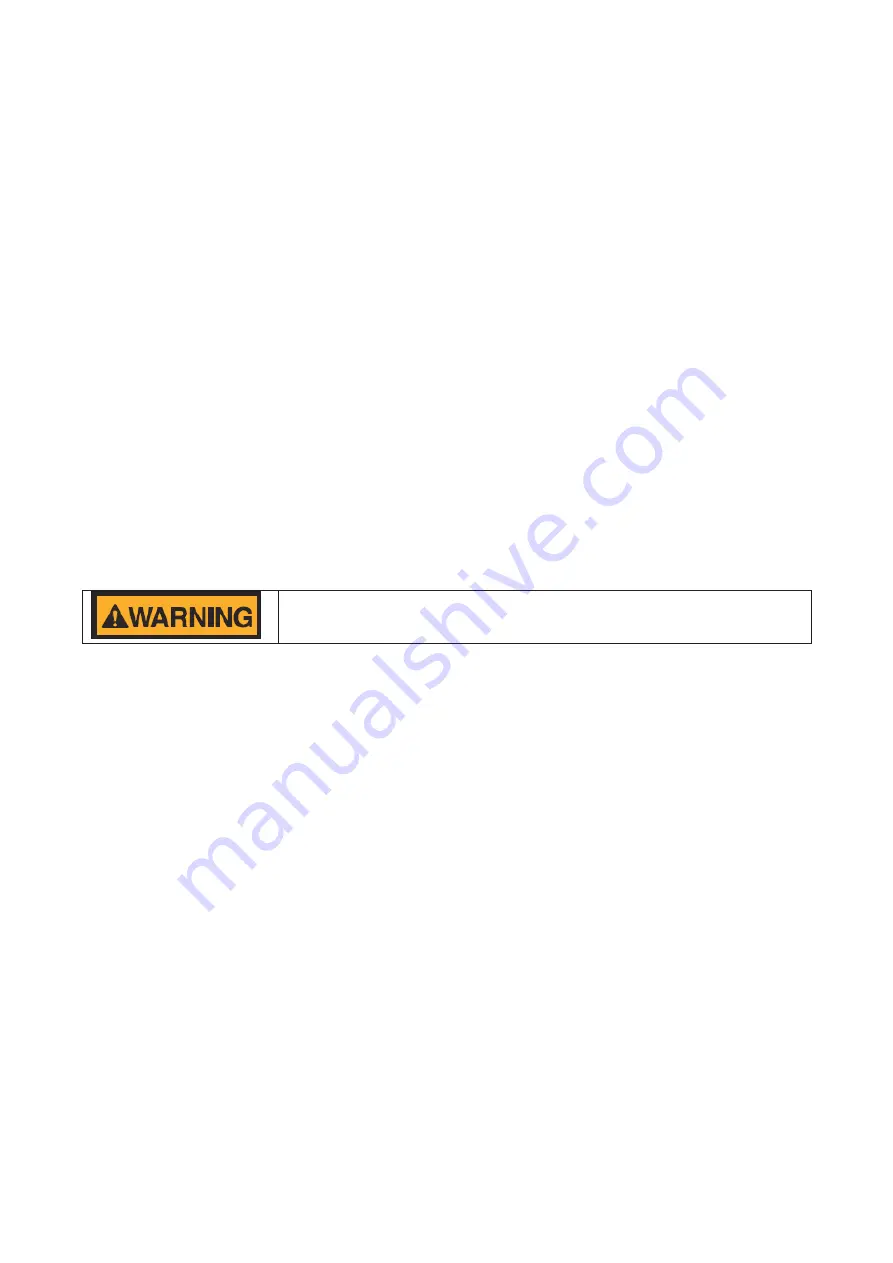
5
P5415467
●
Do not position the condensate pipe for the indoor unit near any sanitary sewers where corrosive
gases may be present. If you do, toxic gases can seep into breathable air spaces and can cause
respiratory injuries. If the condensate pipe is installed incorrectly, water leakage and damage to the
ceiling, floor, furniture, or other possessions may result. If condensate piping becomes clogged,
moisture can back up and can drip from the indoor unit. Do not install the indoor unit where such
dripping can cause moisture damage or uneven locations: Use a raised concrete pad or concrete
blocks to provide a solid, level foundation for the unit to prevent water damage and abnormal
vibration.
●
Before performing any brazing work, be sure that there are no flammable materials or open
flames nearby.
●
Perform a run test to ensure normal operation. Safety guards, shields, barriers, covers, and protective
devices must be in place while the compressor/unit is operating. During the test run, keep fingers and
clothing away from any moving parts.
●
Clean up the site when finished, remembering to check that no metal scraps or bits of wiring have
been left inside the unit being installed.
●
During transportation, do not allow the backrest of the forklift to make contact with the unit,
otherwise, it may cause damage to the heat exchanger and also may cause injury when
stopped or started suddenly.
●
Remove gas inside the closing pipe when the brazing work is performed. If the brazing filler metal is
melted with remaining gas inside, the pipes will be blown off and it may cause injury.
●
Be sure to use nitrogen gas for an airtight test. If other gases such as oxygen gas, acetylene gas or
fluorocarbon gas are accidentally used, it may cause explosion or gas intoxication.
After installation work for the system has been completed, explain the “Safety Precautions,” the proper use
and maintenance of the unit to the customer according to the information in all manuals that came with the
system. All manuals and warranty information must be given to the user or left near the Indoor Unit.
Refrigerant Precautions
To reduce the risk of serious injury or death, the following refrigerant
precautions must be followed.
●
As originally manufactured, this unit contains refrigerant installed by Johnson Controls. Johnson
Controls uses only refrigerants that have been approved for use in the unit’s intended home country
or market. Johnson Controls distributors similarly are only authorized to provide refrigerants that
have been approved for use in the countries or markets they serve. The refrigerant used in this unit
is identified on the unit’s faceplate and/or in the associated manuals. Any additions of refrigerant into
this unit must comply with the country’s requirements with regard to refrigerant use and should be
obtained from Johnson Controls distributors. Use of any non-approved refrigerant substitutes will void
the warranty and will increase the potential risk of injury or death.
●
If installed in a small room, take measures to prevent the refrigerant from exceeding the maximum
allowable concentration in the event that refrigerant gases should escape. Refrigerant gases can
cause asphyxiation (0.42 kg/m3 based on ISO 5149 for R410A). Consult with your distributor for
countermeasures (ventilation system and so on). If refrigerant gas has leaked during the installation
work, ventilate the room immediately.
●
The design pressure for this product is 601 psi (4.15MPa). The pressure of R410A refrigerant is 1.4
times higher than that of the refrigerant R22. Therefore, the refrigerant piping for R410A shall be
thicker than that for R22. Make sure to use the specified refrigerant piping. If not, the refrigerant
piping
may r
u
pture due to an excessive refrigerant pressure. Besides, pay attention to the piping
thickness when using copper refrigerant piping. The thickness of copper refrigerant piping differs
depending on its material.
●
The refrigerant R410A is adopted. The refrigerant oil tends to be affected by foreign matters such
as moisture, oxide film, (or fat). Perform the installation work with care to prevent moisture, dust, or
different refrigerant from entering the refrigerant cycle. Foreign matter can be introduced into the
cycle from such parts as expansion valve and the operation may be unavailable.
●
To avoid the possibility of different refrigerant or refrigerant oil being introduced into the cycle, the
sizes of the charging connections have been changed from R407C type and R22 type. It is necessary
to prepare the appropriate tools before performing the installation work.
●
Use refrigerant pipes and joints which are approved for use with R410A.
●
A compressor/unit comprises a pressurized system. Never loosen threaded joints while the system is
iii
Содержание DHMW24NKB21S
Страница 27: ...19 ...