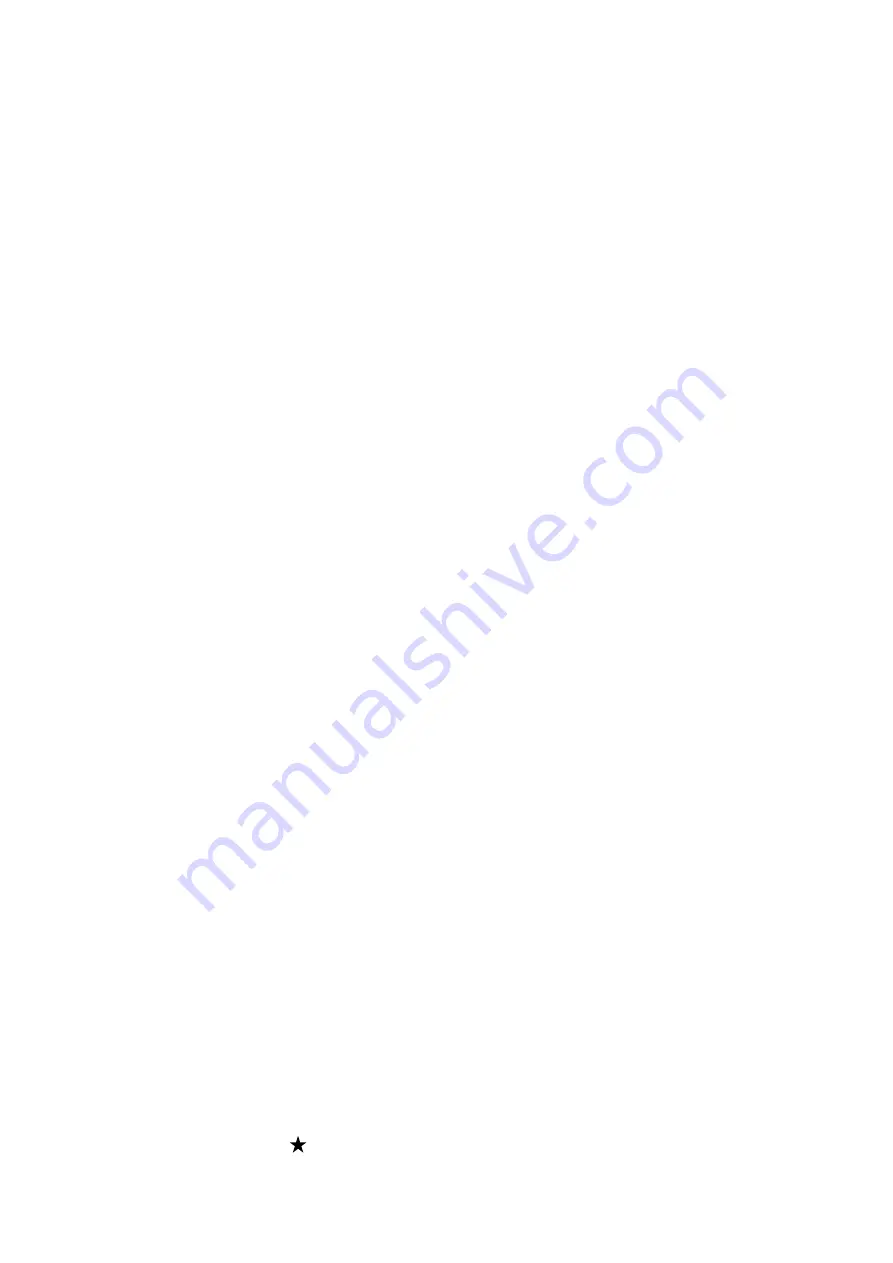
Service hotline
:
+86 523-84385453
- 5 -
±
2℃. The inlet & outlet water tubing should be connected according to
the labels on the spindle. No leaking at the joint. Make sure the cooling
liquid flows smoothly.
⑹、
Water prevention and shielding measures should be taken for the
power cables. It’s better no more than 200cm long of the distance
between the spindle motor and inverter. High frequency should be
prevented to avoid the interference on CNC machine controlling system.
⑺、
Set up the parameters of inverter correctly. The inverter’s voltage
and frequency should accord with those of the spindle motor. (If the
inverter is not purchased from us, the rated frequency is usually made
50HZ. If directly running without any settings on the inverter, the spindle
will be burnt at once due to the high current). During the inverter setting,
its rated frequency (corner frequency), maximum frequency, maximum
voltage should correspond with those of the spindle graphs respectively.
Overload current is set 120% of the rated current. Overload protection
time is set 8s. Speed up & down is set 10~12s. Prolong the speed-up time
if the starting time exceeds the rated current.
⑻ 、
Respectively connect U, V, W of the inverter with three thick
cables of the spindle. Another two thin wires are for thermistor. After
power on, inch the inverter. Observe if the spindle rotates in the same
direction as the arrow direction shown on the spindle. If not, stop the
spindle immediately, and then exchange any two of the three power
cables. In this way, the connection is surely correct. No allowing running
the spindle in the wrong direction.
⑼、
Check if the pressure of air supply is 0.6~0.8 mpa. And filter the
output air at the accuracy 25μm.
⑽ 、
Before starting the spindle, ensure the valve of “air sealed” is
turned on normally at the pressure 0.1~0.15 mpa. From the beginning to