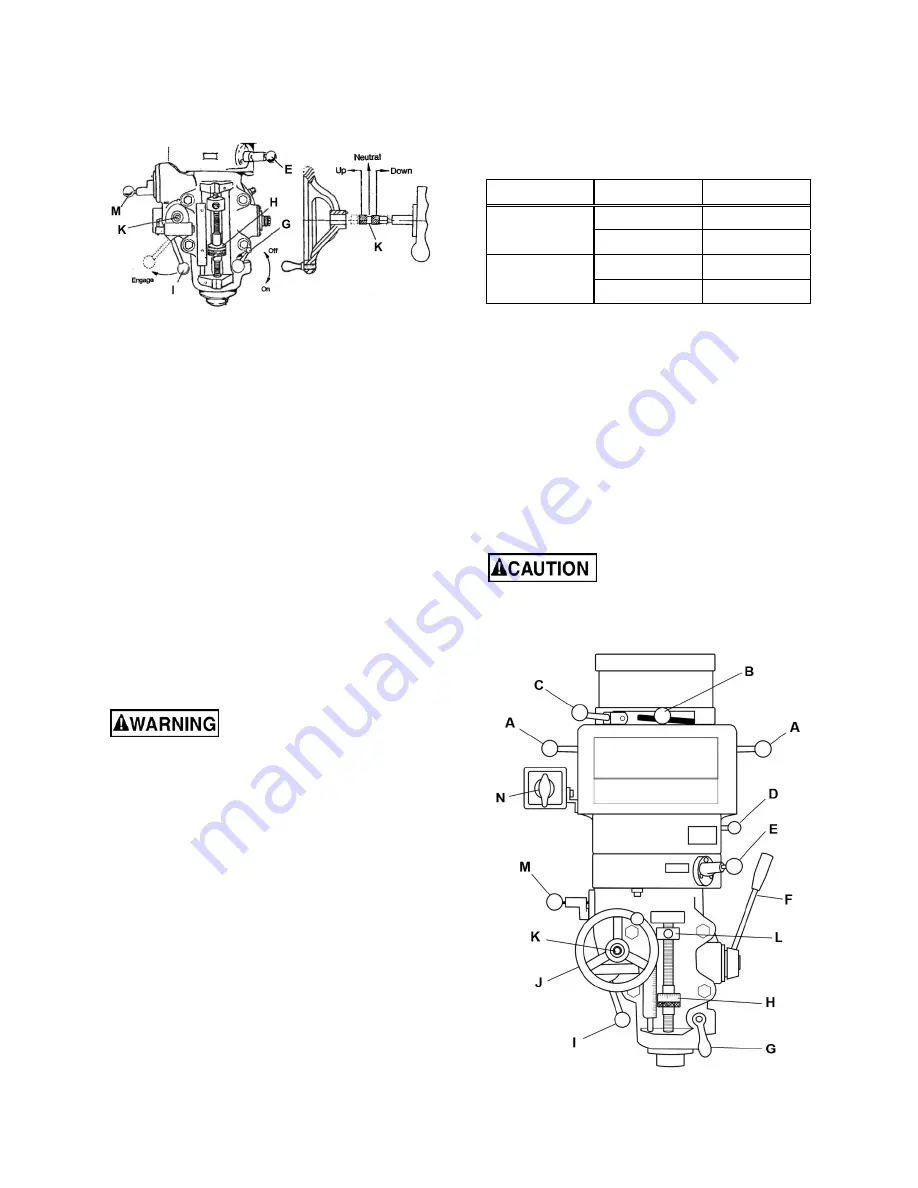
14
2. Position feed reversing knob (K) in the center
at neutral position.
3. Engage feed trip lever (I) by pulling away from
head assembly.
Figure 7
11.5
Setting up for automatic feed
Refer to Figure 8:
1. Ensure quill lock (G, Figure 8) is loosened by
rotating counterclockwise.
2. Set micrometer dial (H) to desired depth.
3. Engage auto quill feed lever (D) by pulling out
lock knob and moving lever to left hole.
4. Select feed rate (M).
5. Select feed direction (K).
6. Engage feed trip lever (I) by pulling away from
head assembly.
11.6
Power feed operation
Establish the point at which the quill will reset
during power feed operations, as follows.
Refer to Figure 8:
Verify that manual fine feed
handwheel (J, Figure 8) has
been removed for power feeding. Failure to
comply may cause injury.
1. Loosen knurled lock nut on micrometer nut
(H).
2. Use Coarse Feed Handle
(F) to advance quill
to the point where the feed should stop.
3. Engage Feed Trip Lever (I) by pulling it away
from head assembly.
4. Adjust Micrometer Adjusting Nut (H) against
Quill Stop (L).
5. Continue turning Micrometer Adjusting Nut (H)
until Feed Trip Lever (I) trips.
6. Tighten
Locknut
(H).
7. Disengage Quill Lock (G) by rotating
counterclockwise.
8. Start spindle by turning switch (N).
9. Set Feed Rate Lever (M) to the feed rate
required for the tooling and material used.
10. Place Quill Feed Engagement Lever (E) in the
Engaged position.
11. Select feed direction by setting the
Feed
Direction Knob
(K) position per Table 2:
Spindle Dir.
Feed Dir. Knob
Pos.
CW
Down In
Up Out
CCW
Down Out
Up In
Table 2
38. Engage
Feed Trip Cam Lever
(I) by pulling
away from head assembly.
Note:
Due to variables in tool diameter, coatings,
coolant, and materials, no specific spindle speed or
feed rate recommendations are provided. Use
general shop manuals that have data applicable to
the milling and drilling operations being performed;
or contact the supplier of the tooling, coolant, and
material for specific recommendations.
IMPORTANT:
The power feed can be used for
drills up to 3/8” in diameter (mild steel). Use
manual feed for drills larger than 3/8”.
The overload clutch is factory
set to hold up to 200 lb. downfeed pressure on
the quill (accommodates drills up to 3/8”). Do
not attempt to adjust clutch pressure.
Figure 8
Содержание JTM-1
Страница 6: ...6 5 0 JTM 1 JTM 2 installation layout Figure 1 ...
Страница 21: ...21 15 1 1 Upper Head Assembly Exploded View ...
Страница 24: ...24 15 2 1 Head Assembly Exploded View ...
Страница 28: ...28 15 3 1 Base Assembly Exploded View ...
Страница 33: ...33 16 0 Electrical Connections ...
Страница 34: ...34 This page intentionally left blank ...
Страница 35: ...35 This page intentionally left blank ...
Страница 36: ...36 427 New Sanford Road LaVergne Tennessee 37086 Phone 800 274 6848 www jettools com ...