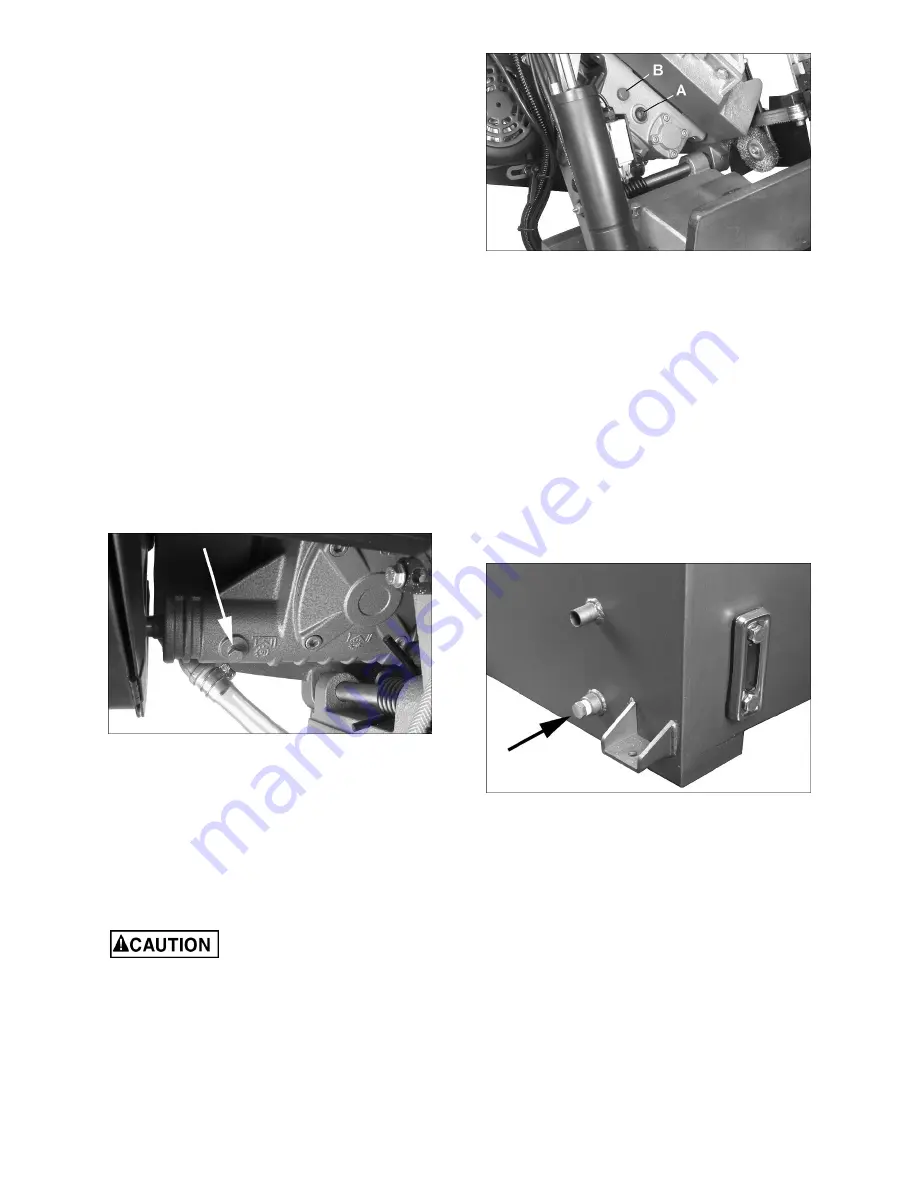
16
11.1
Lubrication
See
sect. 11.4,
Table 3, for lubrication chart.
Blade guide ball bearings are permanently
lubricated and sealed; they require no further
lubrication.
Apply a light coat of machine oil to moving parts as
needed.
Periodically apply light coat of machine oil to
exposed metal surfaces, such as vise bed, to
prohibit rust.
11.1.1
Gear box oil change
Drain and refill gear box according to Table 3
recommendations.
To check gear box oil level, place bow in down
position and wait a few moments for oil to settle.
Check level in sight glass on side of gear casing (A,
Figure 11-2). Oil level must be above red dot in
middle of sight glass.
To change gear box oil:
1. Raise bow to highest position.
2. Unscrew drain plug (Figure 11-1), and allow oil
to drain completely. Follow local regulations for
proper disposal of used oil.
Figure 11-1: gear box drain
3. Reinstall drain plug. Use pipe thread sealant on
plug threads.
4. Remove fill plug (B, Figure 11-2) and insert
approximately 850 mL (1/4 gal.) of Mobil
®
SHC
Gear Oil 460, or equivalent.
5. Reinstall fill plug.
6. Lower bow. Recheck sight glass, top off if
needed.
Oil level in sight glass should
not fall below the red dot. Insufficient oil will
result in overheating and eventual gear damage.
Figure 11-2: gear box fill hole and sight glass
11.1.2
Servicing cutting fluid
Pour cutting fluid or coolant mixture into chip tray so
that it drains through strainer into basin. The sight
glass is located on front of base, at lower left.
Many cutting fluids on the market are formulated for
special applications. Consult your local distributor
for details if you have a long range production task
or are required to cut more exotic materials. Refer
to the cutting fluid provider’s instructions for mixing
recommendations and fluid life span.
To drain cutting fluid, unscrew drain plug located at
bottom left of stand (Figure 11-3). Use pipe thread
sealant on drain plug threads when reinstalling.
Follow local regulations for disposal of used
machine fluids.
Figure 11-3: base drain plug
11.2
Sheave alignment
Periodically check alignment of sheaves.
Misalignment can cause rubbing and premature
wear of the belt. To adjust, loosen set screw in motor
sheave and slide sheave into alignment. Retighten
set screw.
11.3
Additional servicing
Any additional servicing should be performed by
authorized service personnel.
Содержание HBS-916EVS
Страница 20: ...20 14 1 1 HBS 916EVS 1018EVS Bed and Base Assembly Exploded View...
Страница 21: ...21 14 1 2 HBS 916EVS Bow Assembly Exploded View...
Страница 22: ...22 14 1 3 HBS 1018EVS Bow Assembly Exploded View...
Страница 29: ...29 14 2 1 HBS 916EVS 1018EVS Gear Speed Reducing Box Exploded View...
Страница 31: ...31 15 0 Electrical Connections HBS 916EVS 1018EVS...