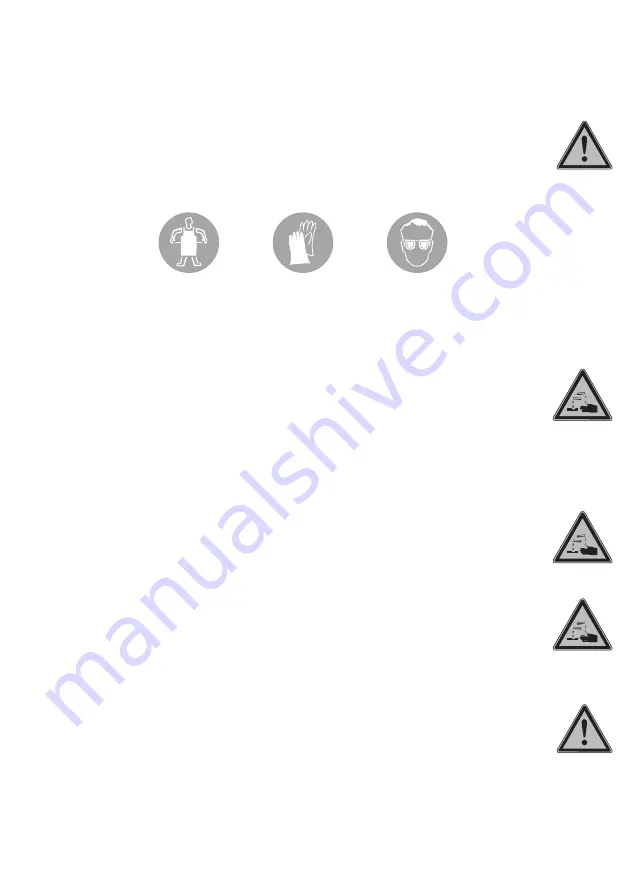
1.10 Impermissible modes of operation
Other usage and modifications in opposition to chapter 2 "Appropriate and intendet use" will lead to the
immediate cancellation of the warranty and any other manufacturer’s liability.
1.11 Dosing of Chemicals
CAUTION!
When working on dosing systems, the accident prevention regulations applicable on site must be observed
and the specified personal protective equipment worn.
The following standard protective clothing is recommended, depending on the hazard associated with the
metered medium:
Protective clothing
Protective gloves
Goggles
All people responsible for installation and maintenance of pumps, piping, hoses and accessories should
wear this protective equipment.
Before working on the dosing pump and plant, disconnect it from the mains supply and protect it against
reconnection.
CAUTION!
Any chemical still present in the dosing head may spray out when the power supply is reconnected. This
may lead to caustic or other burns to the face and hands. Dosing lines must always be connected before
starting the pump again.
The chemical resistance of the pump’s materials of construction must be verified before dosing aggressive
media!
The dosing head of the dosing pump as well as connections and lines of the system may be under pressure.
Working on the dosing plant requires special safety precautions and may only be carried out by instructed
technical personnel:
CAUTION!
Chemical could spray out. This may lead to caustic or other burns. Always relieve the pressure before start-
ing work on the dosing pump.
Before working on the dosing head, valves and connections, flush the dosing pump with a harmless medium
(mainly water) to avoid unintentional contact with the metered medium.
WARNING!
Never look into the open end of a clogged line or valve. Chemical may emerge unexpectedly and cause
caustic or other burns to face and hands.
Before start up, all connections must be inspected for correct tightness and, if necessary, must be tightened
up using appropriate tools.
CAUTION!
If connections at the dosing head are loosened during operation for venting or other reasons, leaking
chemical must be removed professionally. This is the only way to avoid the danger of physical injury and
corrosion at the dosing pump. Leaking chemical may also damage the diaphragm at its mounting points.
| Operation & Maintenance Instructions |
5