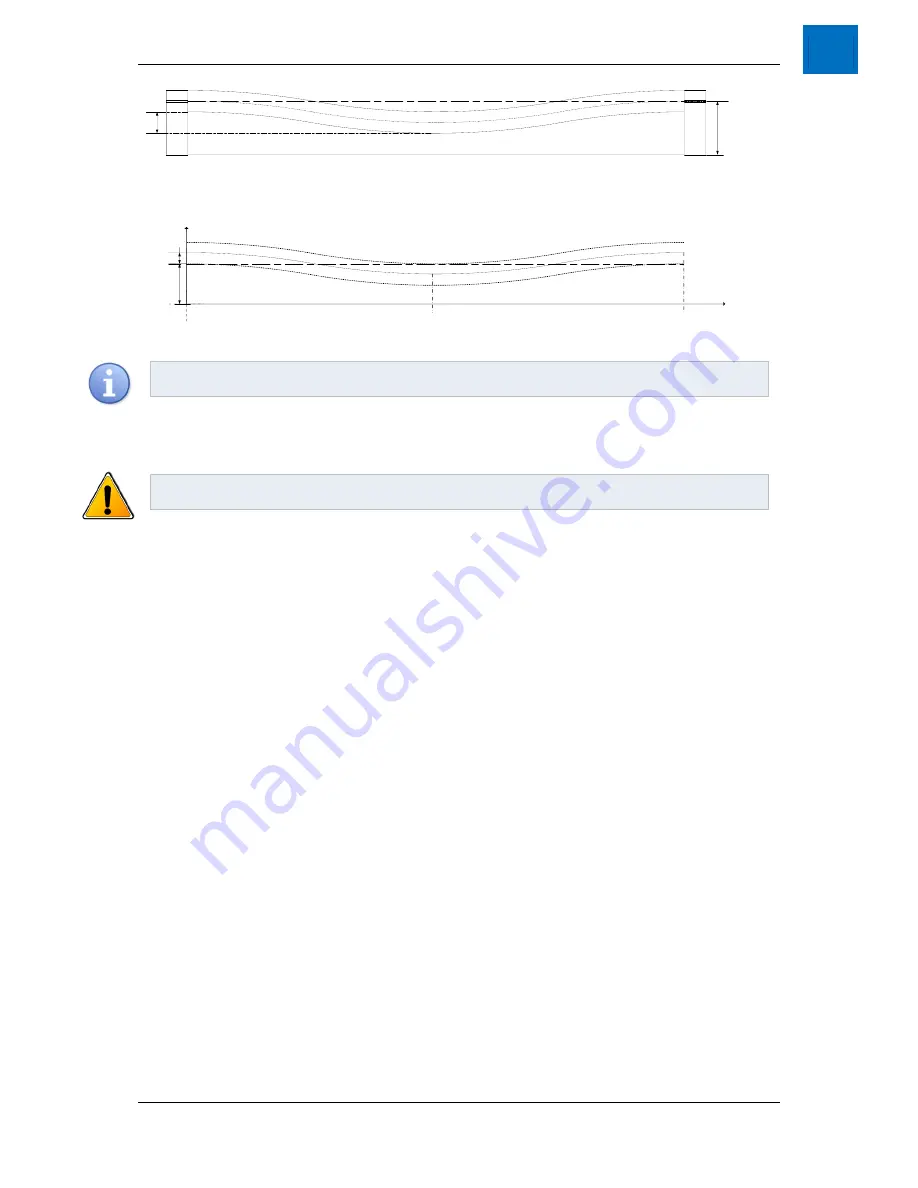
System Design
ANCA Motion
D-000168 Rev 02
13
4
y
a
y/
2
SHAFT
CENTER
HEIGHT
UNSUPPORTED
SHAFT LENGTH
a
Figure 4-4 - Recommended shaft sag compensation method
NOTE:
The recommended method for shaft sag only applies to for sag up to 1.6mm. If the sag exceeds this
value, additional countermeasures should be taken. Please contact ANCA Motion for more information.
Forcer
4.3.2
WARNING:
The shaft is not designed to be a load bearing element. Additional elements must be added to
the forcer to handle any load applied.
As with a ball screw application, the forcer must be supported by a linear bearing or alignment rod system
capable of supporting the forcer and its load. In many cases, the linear bearing or aligning rods are the only
contact point between the moving and stationary components of the axis. Stiffness of the bearings and machine
structure should be considered to minimize deflection between the encoder and the motor. Low friction in the
bearings will result in smoother motion. Due to the high acceleration and velocity capabilities of the linear motors,
the associated bearing capabilities also need to be taken into account.
Cable Carrier
4.3.3
When the forcer is the component moving relative to the servo drive, it is recommended that a cable carrier is
used to guide and protect cables connected to the forcer. Where the machine has a very short stroke, a cable
carrier may not be required. In all cases, strain relief is recommended.
Refer to the cable supplier’s information to
ensure the cable bends and flexes within specification.
Servo Drive
4.4
ANCA Motion provides a range of servo drives that are designed to be used with the LinX cylindrical linear motor
including the AMD2000 and AMD5x series. However, if desired, the LinX cylindrical motor can be used with any 3
phase AC brushless servo drive. Depending on the application, the motor can be controlled in torque, velocity or
position mode with the drive receiving commands from various sources. In most cases, a linear encoder is
required by the servo drive for field orientation and accurate velocity/position feedback.
Appropriate servo drive model selection for the application and selected forcer model is important for optimum
performance. Considerations include maximum current rating, continuous current rating and DC bus voltage.
These factors, in turn, impact the peak force, force duty cycle and maximum velocity of the motor.
Please
Contact ANCA Motion
for more information on the available range of servo drives.
Содержание TUNE600BTNC
Страница 1: ...i D 000168 Rev 02 ANCA Motion LinX Series Linear Motor User Guide D 000168 Rev 02 ...
Страница 2: ...Page intentionally left blank ...
Страница 4: ...LinX Series Linear Motor User Guide iv D 000168 Rev 02 ANCA Motion Page intentionally left blank ...
Страница 8: ......
Страница 26: ...LinX Series Linear Motor User Guide 18 D 000168 Rev 02 ANCA Motion Figure 4 9 Parallel Forcers ...
Страница 34: ...LinX Series Linear Motor User Guide 26 D 000168 Rev 02 ANCA Motion ...