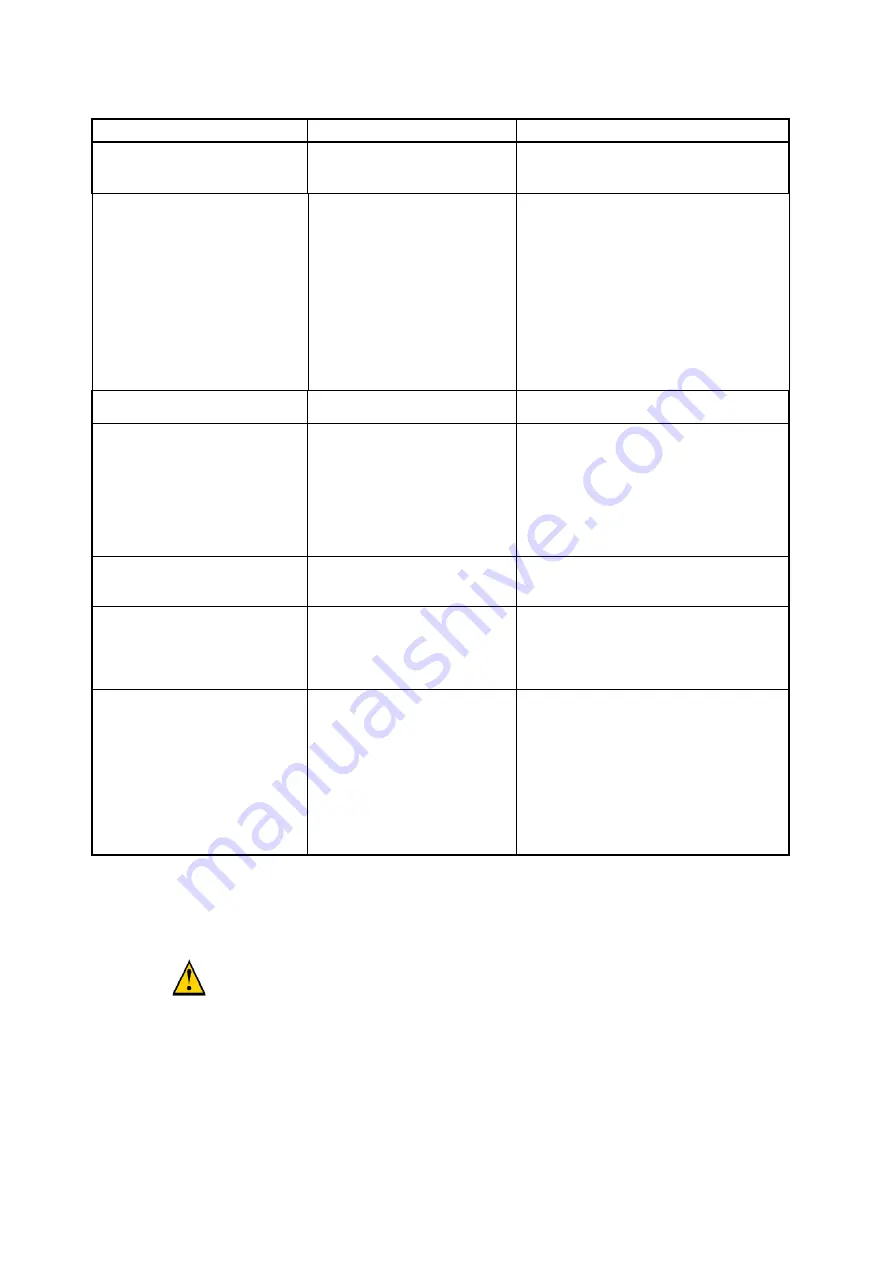
12
6.0 TROUBLESHOOTING
PROBLEM
CAUSE
ACTION
Unit will not start - compressor
does not start; no light in Power
Switch
•
Power Cord not attached
•
No voltage at receptacle /
incorrect voltage
•
Attach Power Cord
•
Verify voltage at Job Site
Compressor will not start
•
Circuit breaker has opened
•
Discharge pressure too high
•
HP Switch has opened
permanently
•
Insufficient pressure to close
LP switch (if fitted)
•
Electronics failure in Motor,
Bridge Rectifier or Filter
Capacitor / Relay
•
Identify cause of breaker activation,
rectify and reset
•
Reduce pressure and rotate V2 to Purge
and back to Recovery
•
Reduce pressure
•
Factory service required
•
Check connection, hoses, valves, gauges,
system may not contain refrigerant
•
Factory service required
•
Thermal cut-out has activated
•
Allow motor to cool. If still not working a
factory service is required
Compressor starts but cuts out
within a few minutes; pressure
indication on HP gauge is high
•
V2 is in Purge position and HP
switch activates
•
V3 not open and HP switch
activates
•
Recovery cylinder valve not
open
•
Blocked discharge hose
•
Air in system/cylinder
•
Rotate V2 to Recovery
•
Rotate V3 to open position
•
Open cylinder valve
•
Check & clear blockage
•
Bleed air from system/cylinder
Compressor stops intermittently
•
Vapour pressure of refrigerant
in cylinder is close to HP trip
point
•
Reduce cylinder temperature
Unit overheats
Excessive head pressure due to:
•
High ambient temperature
•
Restricted discharge hose
•
Air in recovery cylinder
•
Fan not turning
•
Reduce cylinder temperature
•
Check & clear restriction
•
Bleed air from cylinder
•
Factory service required
Recovery process too slow
•
Head pressure too high
•
System refrigerant iced up
•
Compressor seals are worn
•
Inlet filter blocked
•
Reduce cylinder temperature or change
cylinders
•
Throttle gauge manifold valves and V3 to
reduce pressure differential between LP
and HP gauges
•
Interrupt process to allow ice to dissipate
•
Replace compressor - check with
wholesaler for assistance
•
Remove filter and clean/replace cone
screen
7.0
SERVICE
7.0.1 The EVO-OS uses only UL, CSA or TUV recognized electrical components or
components that have been specially designed for this application.
7.0.2
DO NOT CHANGE any of these components as the safety of the machine could be
compromised. All service work must be performed at a Javac approved facility in order
to maintain the safety rating and the Warranty, if applicable.
7.0.3 Technical assistance and service information can be obtained by calling
UK (01642)-232-880 or the Organization where you purchased
the recovery machine
NOTE: Do not return a defective unit directly to the factory. Contact
your Wholesaler or the factory for assistance.