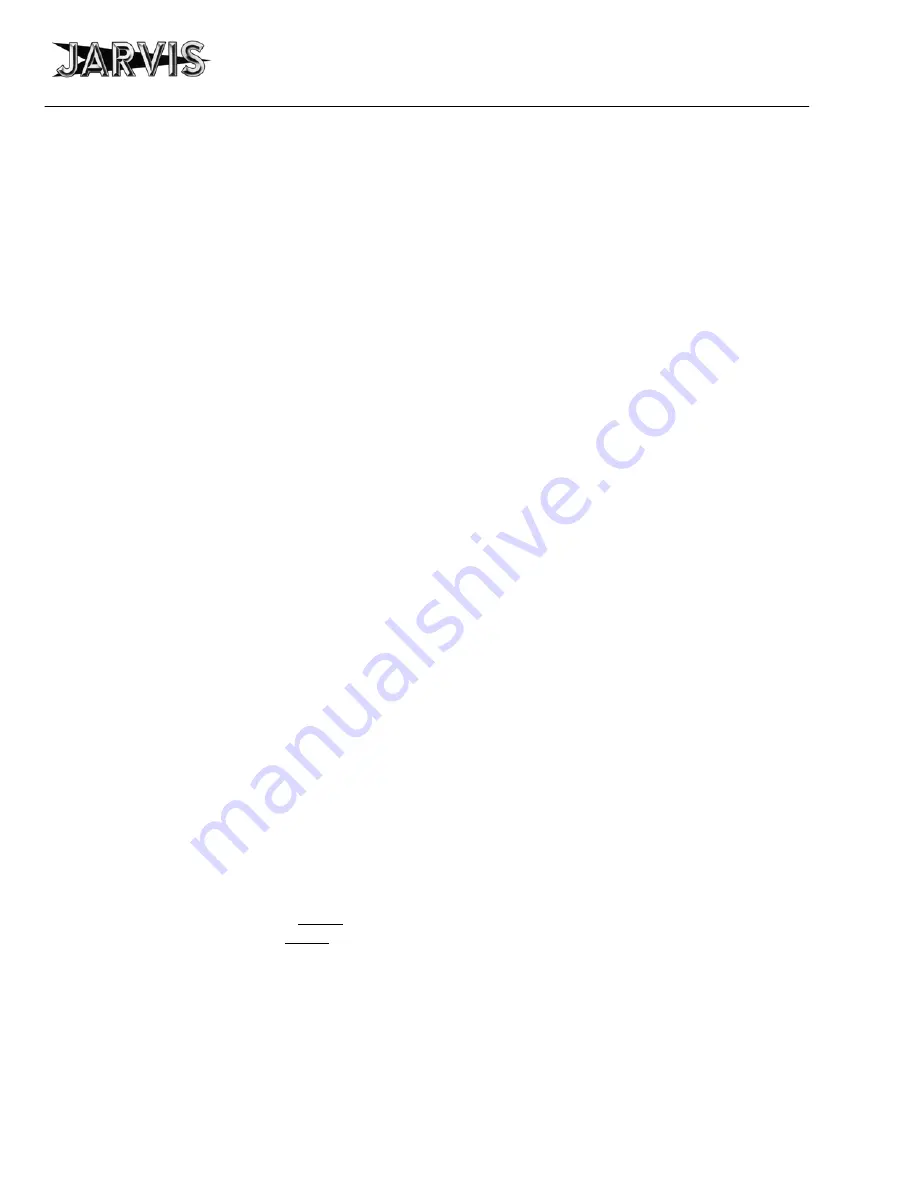
operation and
maintenance instructions
Model ERS--1
page 8 of 12
JARVIS
PRODUCTS CORPORATION
33 ANDERSON ROAD, MIDDLETOWN, CONNECTICUT 06457-4926
UNITED STATES OF AMERICA E--MAIL
TEL. 860-347-7271 FAX. 860-347-6978 WWW
.jarvisproducts.com
6205013.
®
4.3 Saw through the tail bone (use the knife mark as
a guide).
4.3.1 The front end of the ERS--1 should be point-
ing upward while sawing through the tail
bone.
4.4 When the tail bone hits the housing of the ERS--1,
saw until the tail bone breaks apart and the ERS--1
is allowed to continue its path down the back bone
of the carcass.
4.4.1 The motor end of the ERS--1 can be lower
than the front end or in a horizontal position
while sawing through the back bone.
4.5 After the tail and aitch bones have been split, saw
through the loin area.
4.5.1 The ERS--1 should be in a horizontal posi-
tion during this cut.
4.6 Saw through the shoulder and neck of the carcass.
4.6.1 The front end of the ERS--1 should be point-
ing downward while sawing through the
shoulder and neck.
MAINTENANCE INSTRUCTIONS
Refer to Figures A, B and C on pages 4 and 5 for refer-
enced items.
IMPORTANT: ALWAYS DISCONNECT THE ELEC-
TRIC POWER SUPPLY IN ACCORDANCE WITH
OSHA’S LOCKOUT/TAGOUT PROCEDURES (29
CFR 1910.147) BEFORE INSTALLING OR RE-
MOVING A BLADE. ALWAYS DISCONNECT THE
ELECTRIC POWER SUPPLY IN ACCORDANCE
WITH OSHA’S LOCKOUT/TAGOUT PROCE-
DURES (29 CFR 1910.147) BEFORE PERFORM-
ING ANY MAINTENANCE OR REPAIRS.
1 PRIOR TO USE OR DAILY:
1.1 Make sure the control trigger is working correctly.
Depress
the trigger and the tool should start.
Re-
lease
the trigger and the tool should stop.
If the
tool malfunctions, repair or remove it from service
immediately.
The electric power supply must be connected to per-
form the above operation only. Always use two hands
when starting and stopping the tool. Continue hold-
ing the tool firmly with both hands until the saw blade
comes to a complete stop.
1.2 Apply
Jarvis
1315 White Grease
to grease fittings
(items 26 and 33). The fittings can be reached by
inserting a grease gun through two of the three ac-
cess holes in crankcase cover (item 27) when the
blade is in either the extreme forward or back
position.
1.3 Check all electrical plugs and cords (over their en-
tire lengths) for cuts and abrasions. Replace if
necessary.
2 MONTHLY:
2.1 Inspect for wear on blade guides (items 38, 51, 55
and 59), ram (item 39) and side wear plate (item
58). Replace if necessary.
2.2 Tighten all fasteners.
3 BLADE REMOVAL:
Wear cut protective gloves when changing blade.
3.1 Loosen wing nut (item 30) and raise door (item
29) to remove hex head screw (item 49).
3.2 Slide blade out through front guide (item 59).
3.3 Inspect for wear. Sharpen or replace as necessary.
4 BLADE INSTALLATION:
4.1 Reverse steps and procedures outlined in section
3.
5 CRANK DISASSEMBLY:
5.1 Remove (7) flat head screws (item 28) and crank-
case cover (item 27).
5.2 Remove blade (item 48).
Refer to steps and pro-
cedures outlined in section 3.
5.3 Wedge a hard wood block between crank (item
19) and motor and crank housing (item 11) to pre-
vent crank from rotating.
5.4 Remove threaded cap (item 25), hex head screw
item (24), washer (item 23) and connecting rod as-
sembly (items 21, 22 and 33--35).
5.5 Remove (3) cheese head screws (item 1) and end
cap (item 2) to access hex socket in end of rotor
(item 5).