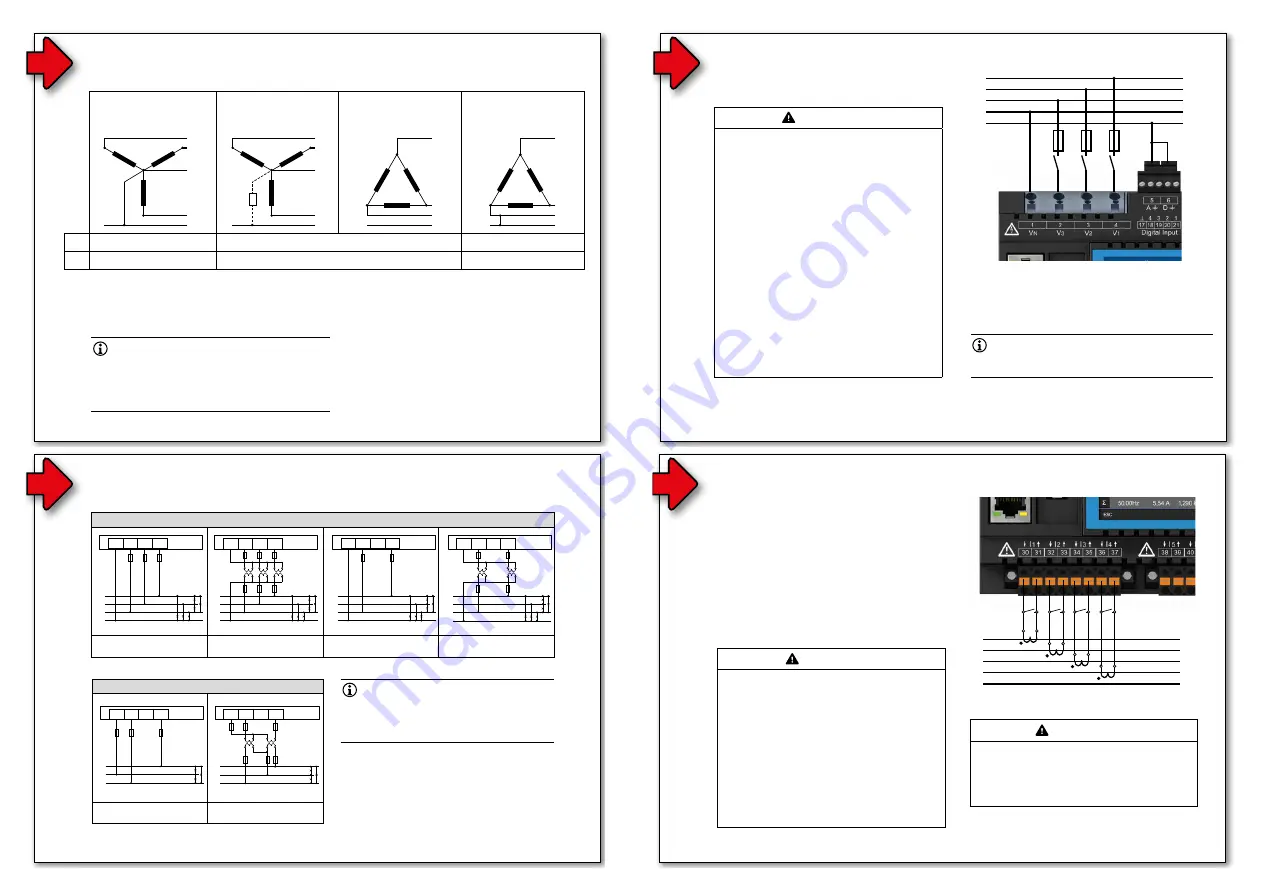
11 / 16
Transformer 1..4
Primary
Secondary
Voltage Transformer
ESC
400 V
400 V
Device
Transformer 1..4
Transformer 5..8
Basic device
Primary
Secondary
Current Transformer
ESC
5 A
5 A
5 A
5 A
Ethernet config. A
Ethernet config. B
Fieldbus
Current Transformer
Voltage Transformer
Configuration
ESC
IP Config.
IP Address
Netmask
Gateway
DHCP
192. 168. 3. 177
192. 168. 3. 4
255. 255. 255. 0
Ethernet (TCP/IP)
ESC
Ethernet config. A
Ethernet config. B
Fieldbus
Current Transformer
Voltage Transformer
Configuration
ESC
Energy
Drag pointer
Multifunctional Channels
Digital I/O Status
Configuration
Menü
General
1
2
Janitza electronics GmbH
Vor dem Polstück 6
D-35633 Lahnau
Support tel. +49 6441 9642-22
Email: [email protected]
www.janitza.de
www
.janitza.de
Doc. no. 2.053.005.4.a 04/2023
Part no. 33.03.376
Power Analyzer
UMG 801
Installation manual
Installation
Device settings
German version:
see r
ear side
2
Safety
Safety information
The installation manual does not represent a
complete set of all safety measures required for
the operation of the device.
Special operating conditions can require addi-
tional measures. The installation manual contains
information which must be observed to ensure
your personal safety and avoid material damage.
Symbols used on the device:
The additional symbol on the de-
vice itself indicates an electrical
danger that can result in serious
injuries or death.
This general warning symbol
draws attention to a possible risk
of injury. Be certain to observe all
of the information listed under this
symbol in order to avoid possible
injury or even death.
Safety measures
When operating electric devices, it is unavoidable
for certain parts of these devices to conduct
hazardous voltage. Consequently, severe bodily
injury or material damage can occur if they are
not handled properly:
• Before making connections to the device,
ground the device by means of the ground
wire connection, if present.
• Hazardous voltages can be present in all
circuitry parts that are connected to the power
supply.
• There can still be hazardous voltages present
in the device even after it has been discon-
nected from the supply voltage (capacitor
storage).
• Do not operate equipment with current trans-
former circuits when open.
• Do not exceed the limit values specified in the
user manual and on the rating plate! This must
also be observed during testing and commis-
sioning!
• Observe the safety information and warning
notices in the usage information associated
with the device and its components!
Qualified personnel
To avoid bodily injury and material damage, only
qualified personnel with electrical training are
permitted to work on the basic device and its
components who have knowledge of:
• The national accident prevention regulations.
• Safety technology standards,
• Installation, commissioning and operation of
the device and the components.
Intended use
The device is:
• Intended only for use in the field of
industrial
controls
.
• Intended for installation in switchboard
cabinets and small distribution boards. The
mounting orientation is arbitrary (Please ob-
serve step 3 "Installation").
• Not intended for installation in vehicles! Use
of the device in non-stationary equipment
constitutes an exceptional environmental
condition and is only permissible by special
agreement.
• Not intended for installation in environments
with harmful oils, acids, gases, vapors, dusts,
radiation, etc.
• Designed as an indoor meter.
Disclaimer
Compliance with the usage information for the
devices is a prerequisite for safe operation and
attaining the stated performance characteristics
and product features. Janitza electronics GmbH
assumes no liability for bodily injury, material
damage or financial losses which result from dis-
regard of the usage information. Ensure that your
informational products are readily accessible in a
legible form.
Further usage information, such as the user man-
ual, can be found on our website www.janitza.de
under Support > Downloads.
Copyright notice
© 2023 - Janitza electronics GmbH - Lahnau.
All rights reserved. Any reproduction, processing,
distribution or other use, in whole or in part, is
prohibited.
Subject to technical alterations.
• Make sure that your device matches the
installation manual.
• First make sure you have read and under-
stood the usage information accompanying
the product.
• Keep the usage information associated with
the product available for the entire service life
and pass it on to any possible subsequent
users.
• Please find out about device revisions and
the associated modifications of the usage
information associated with your product at
www.janitza.de.
Disposal
Please abide by national regulations! Dispose
of individual parts, as applicable, depending on
their composition and existing country-specific
regulations, e.g. as:
• Electronic waste
• Batteries and rechargeable batteries
• Plastics
• Metals
or engage a certified disposal company to handle
scrapping.
Relevant laws,
standards and directive used
Please see the declaration of conformity on our
website (www.janitza.de) for the laws, standards
and directives applied for the device by Janitza
electronics GmbH.
3
Applying the supply voltage
The supply voltage your device requires can be
found on the rating plate. After connecting the
supply voltage, the display becomes active. If
no display appears, check whether the supply
voltage is within the nominal voltage range.
ATTENTION
Material damage due to disregard of the connec-
tion conditions or impermissible overvoltages
Disregard of the connection instructions or exceed-
ing the permissible voltage range can damage or
destroy your device.
Before connecting the device to the supply volt-
age, please note:
· Voltage and frequency must correspond to the
specifications on the rating plate! Observe limit
values as described in the user manual!
· In the building installation, secure the supply volt-
age with a UL/IEC listed line circuit breaker/fuse!
· Observe the following for the isolation device
- Install it close to the device and easily accessi-
ble for the user.
- Mark it for the respective device.
· Do not tap the supply voltage from the voltage
transformers.
· Provide a fuse for the neutral conductor if the
neutral conductor terminal of the source is not
grounded.
Procedure in the event of a malfunction
14
18
9
10
12
13
Ethernet communication
5
Voltage measurement
4
Grid systems
Suitable grid systems and maximum rated voltages (DIN EN 61010-1/A1):
6
Connection variants for voltage measurement
7
Current measurement
8
ATTENTION
Warns of an immediately hazardous situation
which, if not avoided, can result in material or
environmental damage.
Incoming goods inspection
The prerequisites for trouble-free and safe opera-
tion of the devices and their components include
proper transport, storage, setup and assembly,
as well as proper operation and maintenance.
Exercise due caution when unpacking and pack-
ing the device, do not use force and only use
suitable tools.
Check:
• Visually inspect the devices and components
for flawless mechanical condition.
• Check the scope of delivery (see user manual)
for completeness before you begin installing
your devices and components.
If it must be assumed that safe operation is no
longer possible, immediately put the device with
components out of service and secure against
unintentional startup.
It can be assumed that safe operation is no
longer possible, for example, if the device with
components:
• Has visible damage,
• No longer functions despite an intact power
supply.
• Was subjected to extended periods of unfa-
vorable conditions (e.g. storage outside of the
permissible climate thresholds without adjust-
ment to the room climate, condensation, etc.)
or transport stress (e.g. falling from an elevated
position, even without visible external damage,
etc.).
Digital outputs
4 digital outputs, solid state relays, not short-circuit proof.
Switching voltage
Max. 60 V DC
Switching current
max. 50 mAeff DC
Response time
approx. 500 ms
Digital output (energy pulses)
max. 20 Hz
Digital inputs
4 digital inputs, solid state relays, not short-circuit proof.
Maximum counter frequency
20 Hz
Input signal applied
18 V .. 28 V DC
(typical 4 mA)
Input signal not applied
0 .. 5 V DC,
current less than 0.5 mA
Cable length (digital inputs/outputs)
Up to 30 m (32.81 yd)
Unshielded
Greater than 30 m (32.81 yd)
Shielded
User Manual:
15
16
20
Application areas for the device
• 3 and 4-conductor networks (TN, TT and IT
networks).
• Residential and industrial areas.
The device has 4 voltage measurement inputs
and is suitable for various connection variants.
L1
N
PE/FE
L3
L2
Fig. Connection example for “voltage measurement”.
The voltage measurement inputs are designed for
measurements in low-voltage networks in which
nominal voltages occur as described in the
"Technical data".
Fuse
(UL/IEC listed)
Three-phase 4-conductor system
Three-phase 4-conductor sys-
tem without voltage transformer.
Three-phase 4-conductor sys-
tem with voltage transformer.
Three-phase 4-conductor
system (symmetrical load)
Three-phase 4-conductor sys-
tem (asymmetrical load)
Three-phase 3-conductor system
Three-phase 3-conductor sys-
tem (asymmetrical load)
Three-phase 3-conductor sys-
tem with voltage transformer.
Voltage measurement L1, L2, L3 (main measurement)
Voltage measurement
Three-phase 4-conductor
systems with rated volt-
ages up to
480 VLN / 830 VLL (+/-10%) according to IEC
347 VLN / 600 VLL (+/-10%) according to UL
3-phase 3-conductor
systems (grounded) with
rated voltages up to
830 VL-L (+/-10%) according to IEC
600 VL-L (+/-10%) according to UL
3-phase 3-conductor sys-
tems (non-grounded) with
rated voltages up to
690 VL-L (+/-10%) according to IEC
600 VL-L (+/-10%) according to UL
Overvoltage category up
to 2000 m
up to 4000 m
· 1000 V CAT III according to IEC
· 600 V CAT III according to UL
· 600 V CAT IV
according to IEC
· 600 V CAT III according to IEC
Rated surge voltage
8 kV
Protection of the voltage
measurement
1 - 10 A tripping characteristic B(with IEC/
UL approval)
Measuring range L-N
0
1)
.. 720 Veff
(max. overvoltage 1000 Veff)
Measuring range L-L
0
1)
.. 1000 Veff
(max. overvoltage 1000 Veff)
Measuring range N-PE
up to 100 V
Resolution
16 bit
Crest factor
1.6 (referred to measuring range 600 V L-N)
Impedance
4 MΩ/phase
Power consumption
approx. 0.1 VA
Sampling frequency
51.2 kHz
Frequency of
fundamental oscillation
- Resolution
40 Hz .. 70 Hz
0.01 Hz
Harmonics
1 .. 127.
1) ... The meter only measures if at least one voltage measurement
input has an L-N voltage of > 10 Veff
or an L-L voltage of > 18 Veff present.
Current measurement (../1A) (../5A)
Nominal current
5 A
Channels
8
· 2 systems (L1, L2, L3, N)
· Single channels
Measuring range
0.005 .. 6 Aeff
Crest factor
(relative to nominal current)
1.98
Overload for 1 s
120 A (sinusoidal)
Resolution
0.1 mA (color graphic display 0.01 A)
Overvoltage category
300 V CAT II
Rated surge voltage
2.5 kV
Power consumption
approx. 0.2 VA (Ri = 5 m
Ω
)
Sampling frequency
25.6 kHz
Harmonics
1 .. 63.
Residual current measurement (RCM)
Nominal current
30 mAeff
Measuring range
0 .. 40 mAeff
Operating current
50 µA
Resolution
1 µA (color graphic display 0.01 A)
Crest factor
1.414 (relative to 40 mA)
Load
4
Ω
Overload for 20 ms
50 A
The measurement device has 4 optional multifunction channels, for use as
· residual current measurement inputs and/or temperature measure-
ment inputs (mixed),
· Additional system inputs (L1, L2, L3; N)
Temperature measurement
Update time
1 s
Total load
(sensor and cable)
max. 4 k
Ω
Cable
<= 30 m (32.81 yd) not shielded
> 30 m (32.81 yd) shielded
Suitable sensor types
KTY83, KTY84, PT100, PT1000
Analog outputs
1 channel
External power supply
max. 33 V DC
Current
0/4...20 mA DC
Update time
0.2 s
Load
max. 300
Ω
Resolution
10 bit
RS-485 interface
3-wire connection with A, B, GND.
See user manual for recommended cable types.
Protocol
Modbus RTU/Slave
Modbus RTU/Gateway
Transmission rate
9.6 kbps, 19.2 kbps, 38.4 kbps,
57.6 kbps, 115.2 kbps
Termination
DIP switches
Ethernet interfaces
Connection
2 x RJ45 (can be used sep-
arately)
Function
Modbus gateway
Protocols and services
OPC UA, DHCP, Modbus/TCP,
NTP, HTTP(S), FTP(S)
Time synchronization
NTP
Potential isolation and electrical safety of the interfaces
The interfaces (RS-485, Ethernet) have:
• Double insulation to the inputs of the voltage and current
measurement.
• Functional insulation relative to each other, to the supply
voltage, to the measuring inputs for residual current and tem-
perature, to the digital inputs/outputs and to the analog output.
The interfaces of the connected devices require double or
reinforced insulation against mains voltages (according to IEC
61010-1: 2010).
Potential isolation and electrical safety of the
multifunction channels (RCM, Temp.)
The inputs of the multifunction channels have:
• Double insulation to the inputs of the voltage and current
measurement.
• No insulation to each other or to the supply voltage.
• Functional isolation to the Ethernet, RS-485 interfaces, to the
digital inputs/outputs and to the analog output.
External sensors and/or transformers require double insulation
relative to system components with dangerous touch voltages
(according to IEC61010-1:2010).
Potential isolation and electrical safety of the
digital inputs and outputs (I/Os) and the analog output
The digital inputs and outputs as well as the analog output are
equipped with:
• Double insulation to the inputs of the voltage and current
measurement.
• Functional isolation relative to each other, to the supply
voltage, to the Ethernet, RS-485 and multifunction channel
interfaces.
Failure mode
Cause
Remedy
No display
External fuse for the supply voltage has tripped.
Replace fuse.
No current display.
No measured voltage connected.
Connect measured voltage.
No measured current connected.
Connect measured current.
Displayed current is
too great or too small.
Current measurement on the wrong phase.
Check connection and correct if necessary.
Current transformer factor incorrectly programmed.
Read and program the current transformer ratio on
the current transformer.
Current harmonic exceeds current peak value at
measuring input.
Install current transformers with a higher current
transformer ratio.
The current at the measuring input is too low.
Install current transformers with a lower current
transformer ratio.
Displayed voltage is
too high or too low.
Measurement on the wrong phase.
Check connection and correct if necessary.
Voltage transformer programmed incorrectly.
Read the voltage transformer ratio on the voltage
transformer and program.
Displayed voltage
is too low.
Overrange.
Use a voltage transformer.
The voltage peak value at the measuring input was
exceeded due to harmonics current.
Attention!
Make sure that the measuring inputs are
not overloaded.
Despite the above measures,
the device does not function.
Device defective.
Send the device and error description to the manu-
facturer for inspection.
230 VAC
24 VDC
+
-
PELV
(grounded low voltage)
Load
Isolation device
Fig. Connection example for “current measurement”.
L1
N
PE
L3
L2
Load
S1 S2
S1 S2
S1 S2
S1 S2
The device:
· Measures current exclusively via current trans-
formers.
· Allows the connection of current transformers
with a transformer ratio of ../1 A and ../5 A.
· Has a current transformer ratio of 5/5 A (I1 to I8)
as the default setting.
· Does not measure DC currents.
The current transformers require basic insulation
according to IEC 61010-1:2010 for the nominal
voltage of the circuit.
WARNING
Risk of injury due to electric voltage or electric
current!
When handling electric currents or voltages, serious
bodily injury or death can result from:
· Touching bare or stripped leads that are ener-
gized.
· Device inputs that pose a hazard when touched.
Before starting work on your system:
·
Disconnect the supply of power!
·
Secure it against being switched on!
·
Check to be sure it is de-energized!
·
Ground and short circuit!
·
Cover or block off adjacent live parts!
L1
N
WARNING
Risk of injury or damage to the device due to
electrical voltage and improper connection!
Failure to comply with the connection conditions for
the voltage measurement inputs can result in dam-
age to the device or serious injury, including death.
Therefore, please observe the following:
·
Switch off your installation before commenc-
ing work! Secure it against being switched on!
Check to be sure it is de-energized! Ground
and short circuit! Cover or block off adjacent
live parts!
·
Do not apply a DC voltage
-
to the voltage measurement inputs.
-
Equip the voltage measurement inputs with
a suitable, marked fuse and isolation device
(alternatively: line circuit breaker) located
nearby.
-
The voltage measurement inputs are dan-
gerous to touch.
·
Connect voltages that exceed the permissi-
ble nominal network voltages via a voltage
transformer.
·
Measured voltages and currents must origi-
nate from the same network.
DANGER
Warns of an imminent danger which, if not avoided,
results in serious or fatal injury.
CAUTION
Warns of an immediately hazardous situation which,
if not avoided, can result in minor or moderate
injury.
N
L3
L2
L1
N
V1
V2
V3
N
V1
V2
V3
N
V1
V2
V3
N
V1
V2
V3
N
V1
V2
V3
N
L3
L2
L1
N
V1
V2
V3
N
L3
L2
L1
L2
L1
L3
L2
L1
N
V1
V2
V3
L3
L2
L1
L3
L2
L1
N
V1
V2
V3
N
L3
L2
L1
N
L3
L2
L1
N
V1
V2
V3
N
V1
V2
V3
N
V1
V2
V3
N
V1
V2
V3
N
V1
V2
V3
N
L3
L2
L1
N
V1
V2
V3
N
L3
L2
L1
L2
L1
L3
L2
L1
N
V1
V2
V3
L3
L2
L1
L3
L2
L1
N
V1
V2
V3
N
L3
L2
L1
WARNING
Risk of injury due to high currents and high
electrical voltages!
Severe bodily injury or death can result from:
· Touching bare or stripped leads that are ener-
gized.
· Device inputs that pose a hazard when touched.
Therefore, please note for your system:
·
Disconnect the supply of power before start-
ing work!
·
Secure it against being switched on!
·
Check to be sure it is de-energized!
·
Ground and short circuit! Use the ground
connection points with the ground symbol for
grounding!
·
Cover or block off adjacent live parts!
WARNING
Of electrical currents and voltages!
Current transformers operated while exposed on
the secondary side (high voltage peaks) can result
in severe bodily injury or death.
Avoid exposed operation of current transform-
ers and short circuit unloaded transformers!
Operation and button functions
The device is operated via 6 function buttons for
• Selecting measuring displays.
• Navigation within the menus.
• Device configuration.
Function buttons
Fig. UMG 801 standard display - measured values
Display for measured values
and device configuration
After restoration of network power, the device
starts with the measured value display
Home
.
Pressing function button 1
(ESC)
displays the
Menu. (See user manual for description).
Ethernet connection configuration
After restoration of network power, the device
starts with the default display
Home
.
· Press function button 1
ESC
to open the menu.
· Use buttons 2 “
5
” and 5 “
6
” to select the
menu item
Configuration
and confirm with
button 3
Enter
.
· The
Configuration
window appears with the
items
Ethernet Config. A
and
Ethernet
Config. B
.
Configuring current transformers
Communication via OPC UA
1. Press function button 1
ESC
,
to open the menu.
2. Use buttons 2 “
5
” and 5 “
6
” to select the menu
item
Configuration
and confirm with button 3
Enter
.
3. In the
Configuration
window, use buttons 2 “
5
”
and 5 “
6
” to select the menu item
Current trans-
formers
and confirm with button 3
Enter
.
4. The
Current transformers
window appears.
5. In the
Current transformers
window, choose the
item
Basic device
and confirm with button 3
Enter
.
6. The item
Basic device
appears marked in "blue."
In the item
Basic device
, choose between basic
device and up to 10 current measuring modules.
7. Confirm the
Basic device
item with button 3
Enter
.
8. Use button 5 "
6
" to go to the setting for the
Primary side of current transformers 1..4
(current
measurement inputs I1..I4) and press button 3,
Enter
.
9. The item for the primary side of the current
transformers I1..I4 “blinks”.
10. Use buttons 4 (
) and 6 (
) to change the posi-
tion of the digit to be set and buttons 2 (
5
) and
5 (
6
) to change the digit (-1/+1).
11. Confirm your entries with button 3
Enter
or end
the action by pressing button 1
ESC
.
12. Use button 6 (
) to go to the configuration of
the secondary side of the current transformers
I1..I4.
13. Configure the secondary side of the current
transformers I1..I4 in the same way.
14. Confirm your entries with button 3
Enter
or end
the action by pressing button 1
ESC
.
15. When you have finished entering data, press
button 1
ESC
to return to the
Menu
window.
Configure the
current transformer 5..8 (I5..I8)
in
accordance with the current transformer ratios
I1..I4!
Multifunction channels (RCM/Temperature)
0..30 mA
Connection example of multifunction channels for
residual current and temperature measurement
7
8
9 10
2x PT100
11 12
L1
N
PE
L3
L2
Load
13 14
The multifunction channels on the UMG 801 offer the
function options
Residual current measurement
(RCM)
and
Temperature measurement.
The resid-
ual current measurement and temperature measure-
ment share the 4 channels (4 each, 2/2, 3/1 or 1/3).
Multifunction channels for
residual current measurement (RCM)
The UMG 801 with its multifunction channels is
suitable, among other things, for use as a residual
current monitoring device (RCM) for monitoring:
· Alternating current
· Direct current and
· Pulsating direct current.
The UMG 801 measures residual currents according
to IEC/TR 60755 of:
Type A
Type B and B+
(via corresponding current transformers)
WARNING
Hazard due to disregard of warning notices and
safety information!
Disregard of warning notices and safety informa-
tion on the device itself and in the usage informa-
tion for the device and its components can lead to
injuries or even death!
Observe the safety information and warning notic-
es on the device itself and in the usage information
associated with the devices and their components,
such as:
· Installation manual.
· User manual.
· Supplement Safety Information.
Communication via TCP/IP
Considering the Ethernet communication settings (step 10),
the measurement device has 2 types of address assign-
ment for the Ethernet interfaces (TCP/IP) in the
DHCP
mode:
1.
Static (fixed IP address)
The user selects the IP address, netmask and gateway
on the measurement device. Use this mode for simple
networks with no DHCP server.
2.
DHCP
At startup, the measurement device automatically
receives an IP address, netmask and gateway from the
DHCP server.
The default settings of the measurement device for Eth-
ernet interfaces A and B is DHCP!
Connection variants for current measurement
Three-phase 4-conductor system
Current measurement via
3 current transformers in a three-phase
4-conductor system.
Current measurement via
2 current transformers in systems with
the same load.
Current measurement I1 to I4 and I5 to I8
N
L3
L2
L1
N
L3
L2
L1
L3
L2
L1
L2
L1
I
1
30
31
I
1
30
31
I
2
32
33
I
3
34
35
I
4
36
37
N
L3
L2
L1
I
1
30
31
I
2
32
33
I
3
34
35
I
4
36
37
I
2
32
33
I
3
34
35
I
4
36
37
I
1
30
31
I
2
32
33
I
3
34
35
I
4
36
37
I
1
30
31
I
2
32
33
I
3
34
35
I
4
36
37
L3
L2
L1
I
1
30
31
I
2
32
33
I
3
34
35
I
4
36
37
Three-phase 3-conductor system
Current measurement via 2 current
transformers (Aron circuit) in a three-
phase 3-conductor system
Current measurement via 3 current
transformers in a three-phase 3-con-
ductor system
N
L3
L2
L1
N
L3
L2
L1
L3
L2
L1
L2
L1
I
1
30
31
I
1
30
31
I
2
32
33
I
3
34
35
I
4
36
37
N
L3
L2
L1
I
1
30
31
I
2
32
33
I
3
34
35
I
4
36
37
I
2
32
33
I
3
34
35
I
4
36
37
I
1
30
31
I
2
32
33
I
3
34
35
I
4
36
37
I
1
30
31
I
2
32
33
I
3
34
35
I
4
36
37
L3
L2
L1
I
1
30
31
I
2
32
33
I
3
34
35
I
4
36
37
The device is a multifunctional network analyzer
that,
• Measures and calculates electrical quantities
such as voltage, current, frequency, power,
work, harmonics current, etc. in building instal-
lations, at distribution boards, circuit breakers
and busbar trunking systems.
• Displays and stores measurement results and
transmits them via interfaces.
Brief device description and installation
ATTENTION
Material damage due to disregard of the instal-
lation instructions!
Disregard of the installation instructions can dam-
age or destroy your device.
·
Provide adequate air circulation in your instal-
lation environment and cooling, as needed,
when the ambient temperatures are high.
·
More information on device functions, data
and installation as well as the battery used in
the device can be found in the user manual.
Mount the measurement device in a switchboard
cabinet or small distribution board according
to DIN 43880 (any mounting orientation) on a
35 mm (1.38 in) DIN rail (for type, see Technical
Data) as follows:
1. Plug the bus connector included in the scope
of delivery into the sockets on the bottom of the
measurement device.
2. Push your measurement device with the bus
connector sideways onto the DIN rail or press it
frontally onto the DIN rail until the bottom bolt
engages.
Fig. Device with bus connector on DIN rail
Bus connector
DIN rail
Bottom bolt
2.
1.
INFORMATION
Indicates procedures in which there is
no
hazard of
personal injury or material damage.
Recommendation:
Use the GridVis
®
software to configure the trans-
former ratios for residual current transformers.
0..30 mA
Safety information in the installation manual is
marked by a warning triangle and, in dependence
on the degree of hazard, is displayed as follows:
WARNING
Warns of a potentially hazardous situation which, if
not avoided, could result in serious injury or death.
The data transfer using the OPC UA protocol
takes place via the Ethernet interfaces of your
device.
The Ethernet interface and the data transfer using
the OPC UA protocol can be configured conve-
niently in the GridVis
®
software.
Fig. Configuration menu item
Fig. Configuration window
Fig. Configuration window with the
entries Ethernet Config. A and B
(in Dedicated mode).
Fig. Ethernet (TCP/IP) window
Fig. Current transformer window
N
L3
L2
L1
N
V1
V2
V3
N
V1
V2
V3
N
V1
V2
V3
N
V1
V2
V3
N
V1
V2
V3
N
L3
L2
L1
N
V1
V2
V3
N
L3
L2
L1
L2
L1
L3
L2
L1
N
V1
V2
V3
L3
L2
L1
L3
L2
L1
N
V1
V2
V3
N
L3
L2
L1
N
L3
L2
L1
N
L3
L2
L1
L3
L2
L1
L2
L1
I
1
30
31
I
1
30
31
I
2
32
33
I
3
34
35
I
4
36
37
N
L3
L2
L1
I
1
30
31
I
2
32
33
I
3
34
35
I
4
36
37
I
2
32
33
I
3
34
35
I
4
36
37
I
1
30
31
I
2
32
33
I
3
34
35
I
4
36
37
I
1
30
31
I
2
32
33
I
3
34
35
I
4
36
37
L3
L2
L1
I
1
30
31
I
2
32
33
I
3
34
35
I
4
36
37
N
L3
L2
L1
N
L3
L2
L1
L3
L2
L1
L2
L1
I
1
30
31
I
1
30
31
I
2
32
33
I
3
34
35
I
4
36
37
N
L3
L2
L1
I
1
30
31
I
2
32
33
I
3
34
35
I
4
36
37
I
2
32
33
I
3
34
35
I
4
36
37
I
1
30
31
I
2
32
33
I
3
34
35
I
4
36
37
I
1
30
31
I
2
32
33
I
3
34
35
I
4
36
37
L3
L2
L1
I
1
30
31
I
2
32
33
I
3
34
35
I
4
36
37
N
L3
L2
L1
N
V1
V2
V3
N
V1
V2
V3
N
V1
V2
V3
N
V1
V2
V3
N
V1
V2
V3
N
L3
L2
L1
N
V1
V2
V3
N
L3
L2
L1
L2
L1
L3
L2
L1
N
V1
V2
V3
L3
L2
L1
L3
L2
L1
N
V1
V2
V3
N
L3
L2
L1
Connection capacity of the terminals (supply voltage)
Connectible conductors.
Only connect one conductor per terminal point!
Single core, multi-core,
fine-stranded
0.2 - 2.5 mm
2
, AWG 26-12
Wire ferrules (non-insulated)
· Recommended strip length
0.2 - 2.5 mm
2
, AWG 26-12
· 10 mm (0.3937 in)
Wire ferrules (insulated) *
· Recommended strip length **
0.2 - 2.5 mm
2
, AWG 26-12
· 12 mm
(≤1.5 mm
2
), 10 mm
(>1.5 mm
2
) /
0.47 in
(≤1.5 mm
2
), 0.39 in
(>1.5 mm
2
)
Wire ferrules:
Contact sleeve length **
8 - 12 mm (0.31 - 0.47 in)
*
... Applies to wire ferrules with a maximum plastic collar outer
diameter of up to 4.5 mm (0.18 in).
**
.. Depending on the type of wire ferrules used (ferrule
manufacturer).
Connection capacity of the terminals
(digital inputs/outputs, analog output)
Single core, multi-core,
fine-stranded
0.2 - 1.5 mm
2
, AWG 24-16
Wire ferrules (non-insulated)
0.2 - 1.5 mm
2
, AWG 26-16
Wire ferrules (insulated)
0.2 - 1 mm
2
, AWG 26-18
Tightening torque
0.2 - 0.25 Nm (1.77 - 2.21 lbf in)
Strip length
7 mm (0.2756 in)
Connection capacity of the terminals (current measure-
ment)
Connectible conductors.
Only connect one conductor per terminal point!
Single core, multi-core,
fine-stranded
0.2 - 2.5 mm
2
, AWG 26-12
Wire ferrules (non-insulated)
· Recommended strip length
0.2 - 2.5 mm
2
, AWG 26-12
· 10 mm (0.3937 in)
Wire ferrules (insulated) *
· Recommended strip length **
0.2 - 2.5 mm
2
, AWG 26-12
· 12 mm
(≤1.5 mm
2
), 10 mm
(>1.5 mm
2
) /
0.47 in (≤1.5 mm
2
), 0.39 in
(>1.5 mm
2
)
Wire ferrules:
Contact sleeve length **
8 - 12 mm (0.31 - 0.47 in)
Tightening torque
Screw flange
0.2 Nm (1.77 lbf in)
*
... Applies to wire ferrules with a maximum plastic collar outer
diameter of up to 4.5 mm (0.18 in).
**
.. Depending on the type of wire ferrules used (ferrule
manufacturer).
Connection capacity of the terminals (RS-485)
Single core, multi-core,
fine-stranded
0.2 - 1.5 mm
2
, AWG 24-16
Wire ferrules (non-insulated)
0.2 - 1.5 mm
2
, AWG 26-16
Wire ferrules (insulated)
0.2 - 1 mm
2
, AWG 26-18
Tightening torque
0.2 - 0.25 Nm (1.77 - 2.21 lbf in)
Strip length
7 mm (0.2756 in)
Connection capacity of the terminals
(voltage measurement)
Connectible conductors
Only connect one conductor per terminal point!
Single core, multi-core,
fine-stranded
0.08 - 4 mm
2
, AWG 28-12
Wire ferrules
(insulated/non-insulated)
0.25 - 2.5 mm
2
, AWG 24-14
Strip length
8-9 mm (0.3150 - 0.3543 in)
Connection capacity of the terminals -
Multifunction channels (RCM, Temp.)
Connectible conductors.
Only connect one conductor per terminal point!
Single core, multi-core,
fine-stranded
0.2 - 1.5 mm
2
, AWG 24-16
Wire ferrules (non-insulated)
0.2 - 1.5 mm
2
, AWG 26-16
Wire ferrules (insulated)
0.2 - 1 mm
2
, AWG 26-18
Tightening torque
0.2 - 0.25 Nm (1.77 - 2.21 lbf in)
Strip length
7 mm (0.2756 in)
Connection capacity of the terminals (functional earth A/D)
Connectible conductors.
Only connect one conductor per terminal point!
Single core, multi-core,
fine-stranded
0.2 - 4 mm
2
, AWG 24-12
Wire ferrules (non-insulated)
0.2 - 4 mm
2
, AWG 24-12
Wire ferrules (insulated)
0.2 - 2.5 mm
2
, AWG 26-14
Tightening torque
0.4 - 0.5 Nm (3.54 - 4.43 lbf in)
Strip length
7 mm (0.2756 in)
Configure the Ethernet (TCP/IP) settings using the function
buttons as described in step 12 "Operation and button
functions".
Residual current measurement (RCM)
Overload for 1 s
5 A
Permanent overload
1 A
Norm
IEC/TR 60755 (2008-01),
Type A / Type B and B+ (via corre-
sponding current transformers)
Technical data
General
Net weight
420 g (0.926 lb)
Device dimensions
Approx. B = 144 mm (5.67 in), H =
90 mm (3.54 in),
D = 76 mm (2.99 in)
Battery
Type: Lithium CR2032, 3 V
(UL1642 approval)
Integrated memory
4 GB
Backlight service life
40000 h
(50% of the start brightness)
Mounting orientation
As desired
Fastening/mounting -
Suitable DIN rails - 35 mm
(1.38 in)
· TS 35/7.5 according to EN 60715
· TS 35/10
· TS 35/15 x 1.5
Impact resistance
IK07 according to IEC 62262
Transport and storage
The following specifications apply for devices transported and
stored in the original packaging.
Free fall
1 m (39.37 in)
Temperature
-25 °C (-13 °F) to +70 °C (158 °F)
Relative humidity
5 to 95% at 25 °C (77 °F),
no condensation
Environmental conditions during operation
The device:
• Is for weather-protected and stationary use.
• Fulfills operating conditions according to DIN IEC 60721-3-3.
• Has protection class II according to IEC 60536 (VDE 0106,
part 1),
a ground wire connection is not required!
Rated temperature range
-10 °C (14 °F) to +55 °C (131 °F)
Relative humidity
5 to 95% at 25 °C (77 °F),
no condensation
Operating elevation
(for overvoltage categories,
see voltage and current
measurement)
2000 m (6562 ft) above sea level
4000 m (13,124 ft) above sea level
Pollution degree
2
Ventilation
No forced ventilation required.
Protection against foreign
matter and water
IP20 according to EN60529
Supply voltage
Nominal range
DC: 24 V, PELV
Operating range
+/-10% of nominal range
Power consumption
max. 4 W
Maximum power
consumption with 10
modules
12 W (UMG 801 at 4 W plus
10 modules at 0.8 W each)
Recommended overcurrent
protective device for line
protection
2-6 A, (Char. B), IEC/UL approval
19
Configuring voltage transformers
17
1. Press function button 1
ESC
to open
the menu.
2. Use buttons 2 “
5
” and 5 “
6
” to select the
menu item
Configuration
and confirm with
button 3
Enter
.
3. In the
Configuration
window, use buttons 2
“
5
” and 5 “
6
” to select the item
Voltage
transformer
and confirm with button 3
Enter
.
4. The
voltage transformer
window appears.
5. In the
Voltage transformer
window, select the
item
Transformer 1..4
(voltage measurement
inputs L1 to L4) and press button 3,
Enter
.
6. The item for the primary side of the transform-
er 1..4 “blinks”.
7. Use buttons 4 (
) and 6 (
) to change the
position of the digit to be set and buttons 2
(
5
) and 5 (
6
) to change the digit (-1/+1).
8. Confirm your entries with button 3
Enter
or
end the action by pressing button 1
ESC
.
9. Use button 6 (
) to go to the configuration
of the secondary side of the transformer 1..4
(voltage measurement inputs L1 to L4).
10. Configure the secondary side of voltage trans-
formers 1..4 in the same way.
11. Confirm your entries with button 3
Enter
or end
the action by pressing button 1
ESC
.
12. When you have finished entering data, press
button 1
ESC
to return to the
Menu
window.
Fig. Voltage transformer window
ATTENTION
Faulty cross currents, incorrect measure-
ments, and even damage to the device and/or
your system due to lack of galvanic isolation!
A lack of galvanic isolation of active external cur-
rent transformers (or other current sensors) on the
multifunction channels from the supply voltage
of the device can lead to faulty cross currents,
incorrect measurements or even damage to your
device and/or system.
· Do
not
take the auxiliary voltage supply of
active external current transformers (or other
current sensors) on the multifunction channels
from the supply voltage of the device! For each
active current transformer, use galvanically
isolated power supplies (secondary side).
· Do
not
ground passive current transformers on
the multifunction channels! Observe the usage
information of the current transformer manu-
facturer.
N
L3
L2
L1
N
V1
V2
V3
N
V1
V2
V3
N
V1
V2
V3
N
V1
V2
V3
N
V1
V2
V3
N
L3
L2
L1
N
V1
V2
V3
N
L3
L2
L1
L2
L1
L3
L2
L1
N
V1
V2
V3
L3
L2
L1
L3
L2
L1
N
V1
V2
V3
N
L3
L2
L1
N
L3
L2
L1
N
V1
V2
V3
N
V1
V2
V3
N
V1
V2
V3
N
V1
V2
V3
N
V1
V2
V3
N
L3
L2
L1
N
V1
V2
V3
N
L3
L2
L1
L2
L1
L3
L2
L1
N
V1
V2
V3
L3
L2
L1
L3
L2
L1
N
V1
V2
V3
N
L3
L2
L1
Three-phase 4-conductor systems
with grounded neutral conductor
Three-phase 4-conductor
systems
with non-grounded neutral conduc-
tor (IT networks)
Three-phase 3-conductor
systems
ungrounded
Three-phase 3-conductor
systems
with grounded phase
L1
L2
L3
E
E
N
E
L1
L2
L3
E
N
R
L1
L2
L3
E
E
L1
L2
E
E
L
N
E
E
L1
L2
L3
E
E
L1
L2
N
E
E
L1
L2
L3
E
E
N
E
L1
L2
L3
E
N
R
L1
L2
L3
E
E
L1
L2
E
E
L
N
E
E
L1
L2
L3
E
E
L1
L2
N
E
E
L1
L2
L3
E
E
N
E
L1
L2
L3
E
N
R
L1
L2
L3
E
E
L1
L2
E
E
L
N
E
E
L1
L2
L3
E
E
L1
L2
N
E
E
L1
L2
L3
E
E
N
E
L1
L2
L3
E
N
R
L1
L2
L3
E
E
L1
L2
E
E
L
N
E
E
L1
L2
L3
E
E
L1
L2
N
E
E
IEC
UL-N / UL-L: 480 VLN / 830 VLL
UL-L: 690 VLL
UL-L: 830 VLL
UL
UL-N / UL-L: 347 VLN / 600 VLL
UL-L: 600 VLL
UL-L: 600 VLL
Functional earth
INFORMATION
The functional earthing is a functional part and essential
for the regular operation of the electrical system.
INFORMATION
For a PE/N measurement, connect measuring
input A as the functional earth. Do not use a
green-yellow wire for this, as the conductor has
no protective function!
INFORMATION
Before you start with the DIN rail mounting and
cabling of your UMG 801, make sure that the
bus connector is mounted on the bottom of your
UMG 801. Then connect up to 10 modules via bus
connectors.
INFORMATION
Functional earth
·
Connection D
(UMG 801) in TN, TT and IT net-
works must always be connected.
·
Connection A
(UMG 801) only connect in TN and
TT networks (
not in IT networks
)
INFORMATION
· The meter does not have a password (00000000)
ex works.
· For detailed information on configuring a pass-
word, operation, display and button functions of
your device, refer to the user manual.
INFORMATION
Detailed information on all menu items and their
settings can be found in the user manual.
INFORMATION
· The multifunction channels are suitable for con-
necting residual current transformers with a nom-
inal current of up to 30 mA and have the "Current
transformer connection test" function.
· The residual current measurement monitors the
residual currents via external current transformers
and, if a threshold value is exceeded, can trigger
a warning signal. The meter is not an independent
protective device against electric shock!
INFORMATION
Voltage transformer ratios can also be configured in
the device configuration of the GridVis
®
software.
INFORMATION
Optionally configure the current transformer ratios
· in the device configuration of the GridVis
®
software.
· via the measurement device homepage of the basic
device.
INFORMATION
· Consult your network administrator for the correct
Ethernet network settings for your device.
· Descriptions of the communication interfaces can
be found in the user manual.
· Information on the connection and communication
of your device with the software can be found in
the online help for the GridVis
®
software.
INFORMATION
· Consult your network administrator for the correct Ethernet
network settings for your measurement device.
· Descriptions of the communication interfaces can be found
in the user manual.
· Information on the connection and communication of your
measurement device with the software can be found in the
online help for the GridVis
®
software.
Patch cable
Your measurement device has two Ethernet
interfaces (A and B) for communication in Ether-
net networks. There are 2 options to integrate the
measurement device into Ethernet networks:
1.
Measurement device integration in a network
with additional switch function (switched
mode).
The measurement device is automatical-
ly assigned an IP address by a DHCP server in
an IT network via Ethernet interface A, for exam-
ple. Ethernet interface B has a switch function
via which further devices (hardware components)
can be connected in series. The measurement
device also allows the reverse use of the Ether-
net interfaces (e.g. "B" for the IP address from a
network and "A" for further devices)!
2.
Measurement device integration in 2 different
networks (dedicated mode)
.
The Ethernet interfaces A and B of the mea-
surement device are each assigned different IP
addresses by 2 different networks.
Button Function
· Display menu.
· One step back.
· Cancel action
(ESC)
.
· Repeated actuation leads to the menu.
· Select menu item or position
(up, "
5
").
· Change selection (digit +1).
· Confirm selection
(Enter)
· Select position (to the left, "
").
· Select menu item or position
(down, "
6
").
· Change selection (digit -1).
· Select position (to the right “
”).
Ethernet A
Ethernet B
Recommendation:
Use at least CAT5 cable!
Patch cable
INFORMATION
For configuration of the IP addresses on the measure-
ment device, observe step 13 "Configuring the Ethernet
connection" and step 14 "Communication via TCP/IP".
· In the
Configuration
window, use buttons 2 "
5
"
and 5 "
6
" to select the respective entry of the
Ethernet interface to be configured and confirm
with button 3
Enter
.
· The window for configuring the TCP/IP Ethernet
settings appears (see step 13 "Communication
via TCP/IP").
INFORMATION
Detailed technical data can be found in the user man-
ual for the measurement device at www.janitza.de.
INFORMATION
You can configure current transformer
ratios
conveniently via
· The device menu.
· The GridVis
®
software.
For information on programming the current
transformer ratios, refer to the user manual.
INFORMATION
·
The switched and dedicated modes of the mea-
surement device can be configured in the GridVis
®
software.
·
The default setting of the measurement device is
the switched mode.
·
A mode change only takes effect after a hard reset
(disconnect the measurement device from the sup-
ply voltage while observing the safety regulations)!
ATTENTION
Material damage due to security vulnerabilities in
programs, IT networks and protocols.
Security vulnerabilities can lead to data misuse and
faults and even the standstill of your IT infrastructure.
To protect your IT system, network, data commu-
nications and measurement devices:
·
Inform your network administrator and/or IT
representative.
·
Always keep the meter firmware up to date and
protect the communication to the meter with an
external firewall. Close unused ports.
·
Take protective measures against viruses and
cyber attacks from the Internet, e.g. through
firewall solutions, security updates and virus
protection programs.
·
Eliminate security vulnerabilities and update or
renew existing protection for your IT infrastruc-
ture.
ATTENTION
Material damage due to incorrect network
settings.
Incorrect network settings can cause faults in the IT
network!
Consult your network administrator for the cor-
rect network settings for your device.
Connection of the device with a patch cable (Ethernet interface) via
a switch/router to the OPC UA server and the PC.
PC and device require a fixed IP address.
PC
Patch cable
Patch cable
OPC UA-
Server
PC
Switch/
Router
UMG 801
Patch cable
Patch cable
DHCP
Server
PC
Switch/
Router
The DHCP server automatically assigns IP addresses to device
and PC.
UMG 801
UMG 801
PC connections
The most common connection methods for com-
munication of the measurement device with a PC
(with GridVis
®
software installed) are described
below.
1. Connection to a DHCP server and PC. The
DHCP server automatically assigns IP ad-
dresses to the device and the PC.
2. Connection as master device with an
RS-485 bus structure (Modbus RTU) to a PC
and OPC UA client.
3. PC direct connection to the device. PC and
device require a fixed IP address.
Ethernet
Ethernet
Ethernet
Modbus TCP
Ethernet
Modbus TCP
Patch cable
Ethernet
INFORMATION
With regard to the configuration of the IP addresses
on the measurement device, also observe steps 10
and 12 to 15!
PC
DHCP
Server
UMG 801
Ethernet A
Ethernet B
Switch/
Router
PC
Network A
Dedicated mode: Different IP addresses for Ethernet interfaces A
and B for separate networks.
Network B
DHCP
Server
Switch/
Router
Switched mode: Ethernet interface B of the UMG 801 for con-
necting an Ethernet device. The measurement device also allows
the reverse use of the Ethernet interfaces (A for the Ethernet
device and B for an IP address from a network).
PC
DHCP
Server
Switch/
Router
UMG 801
A
B
e.g.
UMG 96PQ-L
"Switched mode" connection option:
"Dedicated mode" connection option
11
RS-485
(Modbus RTU)
Transformer 1..4
Primary
Secondary
Voltage Transformer
ESC
400 V
400 V
Device
Transformer 1..4
Transformer 5..8
Basic device
Primary
Secondary
Current Transformer
ESC
5 A
5 A
5 A
5 A
Ethernet config. A
Ethernet config. B
Fieldbus
Current Transformer
Voltage Transformer
Configuration
ESC
IP Config.
IP Address
Netmask
Gateway
DHCP
192. 168. 3. 177
192. 168. 3. 4
255. 255. 255. 0
Ethernet (TCP/IP)
ESC
Ethernet config. A
Ethernet config. B
Fieldbus
Current Transformer
Voltage Transformer
Configuration
ESC
Energy
Drag pointer
Multifunctional Channels
Digital I/O Status
Configuration
Menü
General
1
2
Janitza electronics GmbH
Vor dem Polstück 6
D-35633 Lahnau
Support tel. +49 6441 9642-22
Email: [email protected]
www.janitza.de
www
.janitza.de
Doc. no. 2.053.005.4.a 04/2023
Part no. 33.03.376
Power Analyzer
UMG 801
Installation manual
Installation
Device settings
German version:
see r
ear side
2
Safety
Safety information
The installation manual does not represent a
complete set of all safety measures required for
the operation of the device.
Special operating conditions can require addi-
tional measures. The installation manual contains
information which must be observed to ensure
your personal safety and avoid material damage.
Symbols used on the device:
The additional symbol on the de-
vice itself indicates an electrical
danger that can result in serious
injuries or death.
This general warning symbol
draws attention to a possible risk
of injury. Be certain to observe all
of the information listed under this
symbol in order to avoid possible
injury or even death.
Safety measures
When operating electric devices, it is unavoidable
for certain parts of these devices to conduct
hazardous voltage. Consequently, severe bodily
injury or material damage can occur if they are
not handled properly:
• Before making connections to the device,
ground the device by means of the ground
wire connection, if present.
• Hazardous voltages can be present in all
circuitry parts that are connected to the power
supply.
• There can still be hazardous voltages present
in the device even after it has been discon-
nected from the supply voltage (capacitor
storage).
• Do not operate equipment with current trans-
former circuits when open.
• Do not exceed the limit values specified in the
user manual and on the rating plate! This must
also be observed during testing and commis-
sioning!
• Observe the safety information and warning
notices in the usage information associated
with the device and its components!
Qualified personnel
To avoid bodily injury and material damage, only
qualified personnel with electrical training are
permitted to work on the basic device and its
components who have knowledge of:
• The national accident prevention regulations.
• Safety technology standards,
• Installation, commissioning and operation of
the device and the components.
Intended use
The device is:
• Intended only for use in the field of
industrial
controls
.
• Intended for installation in switchboard
cabinets and small distribution boards. The
mounting orientation is arbitrary (Please ob-
serve step 3 "Installation").
• Not intended for installation in vehicles! Use
of the device in non-stationary equipment
constitutes an exceptional environmental
condition and is only permissible by special
agreement.
• Not intended for installation in environments
with harmful oils, acids, gases, vapors, dusts,
radiation, etc.
• Designed as an indoor meter.
Disclaimer
Compliance with the usage information for the
devices is a prerequisite for safe operation and
attaining the stated performance characteristics
and product features. Janitza electronics GmbH
assumes no liability for bodily injury, material
damage or financial losses which result from dis-
regard of the usage information. Ensure that your
informational products are readily accessible in a
legible form.
Further usage information, such as the user man-
ual, can be found on our website www.janitza.de
under Support > Downloads.
Copyright notice
© 2023 - Janitza electronics GmbH - Lahnau.
All rights reserved. Any reproduction, processing,
distribution or other use, in whole or in part, is
prohibited.
Subject to technical alterations.
• Make sure that your device matches the
installation manual.
• First make sure you have read and under-
stood the usage information accompanying
the product.
• Keep the usage information associated with
the product available for the entire service life
and pass it on to any possible subsequent
users.
• Please find out about device revisions and
the associated modifications of the usage
information associated with your product at
www.janitza.de.
Disposal
Please abide by national regulations! Dispose
of individual parts, as applicable, depending on
their composition and existing country-specific
regulations, e.g. as:
• Electronic waste
• Batteries and rechargeable batteries
• Plastics
• Metals
or engage a certified disposal company to handle
scrapping.
Relevant laws,
standards and directive used
Please see the declaration of conformity on our
website (www.janitza.de) for the laws, standards
and directives applied for the device by Janitza
electronics GmbH.
3
Applying the supply voltage
The supply voltage your device requires can be
found on the rating plate. After connecting the
supply voltage, the display becomes active. If
no display appears, check whether the supply
voltage is within the nominal voltage range.
ATTENTION
Material damage due to disregard of the connec-
tion conditions or impermissible overvoltages
Disregard of the connection instructions or exceed-
ing the permissible voltage range can damage or
destroy your device.
Before connecting the device to the supply volt-
age, please note:
· Voltage and frequency must correspond to the
specifications on the rating plate! Observe limit
values as described in the user manual!
· In the building installation, secure the supply volt-
age with a UL/IEC listed line circuit breaker/fuse!
· Observe the following for the isolation device
- Install it close to the device and easily accessi-
ble for the user.
- Mark it for the respective device.
· Do not tap the supply voltage from the voltage
transformers.
· Provide a fuse for the neutral conductor if the
neutral conductor terminal of the source is not
grounded.
Procedure in the event of a malfunction
14
18
9
10
12
13
Ethernet communication
5
Voltage measurement
4
Grid systems
Suitable grid systems and maximum rated voltages (DIN EN 61010-1/A1):
6
Connection variants for voltage measurement
7
Current measurement
8
ATTENTION
Warns of an immediately hazardous situation
which, if not avoided, can result in material or
environmental damage.
Incoming goods inspection
The prerequisites for trouble-free and safe opera-
tion of the devices and their components include
proper transport, storage, setup and assembly,
as well as proper operation and maintenance.
Exercise due caution when unpacking and pack-
ing the device, do not use force and only use
suitable tools.
Check:
• Visually inspect the devices and components
for flawless mechanical condition.
• Check the scope of delivery (see user manual)
for completeness before you begin installing
your devices and components.
If it must be assumed that safe operation is no
longer possible, immediately put the device with
components out of service and secure against
unintentional startup.
It can be assumed that safe operation is no
longer possible, for example, if the device with
components:
• Has visible damage,
• No longer functions despite an intact power
supply.
• Was subjected to extended periods of unfa-
vorable conditions (e.g. storage outside of the
permissible climate thresholds without adjust-
ment to the room climate, condensation, etc.)
or transport stress (e.g. falling from an elevated
position, even without visible external damage,
etc.).
Digital outputs
4 digital outputs, solid state relays, not short-circuit proof.
Switching voltage
Max. 60 V DC
Switching current
max. 50 mAeff DC
Response time
approx. 500 ms
Digital output (energy pulses)
max. 20 Hz
Digital inputs
4 digital inputs, solid state relays, not short-circuit proof.
Maximum counter frequency
20 Hz
Input signal applied
18 V .. 28 V DC
(typical 4 mA)
Input signal not applied
0 .. 5 V DC,
current less than 0.5 mA
Cable length (digital inputs/outputs)
Up to 30 m (32.81 yd)
Unshielded
Greater than 30 m (32.81 yd)
Shielded
User Manual:
15
16
20
Application areas for the device
• 3 and 4-conductor networks (TN, TT and IT
networks).
• Residential and industrial areas.
The device has 4 voltage measurement inputs
and is suitable for various connection variants.
L1
N
PE/FE
L3
L2
Fig. Connection example for “voltage measurement”.
The voltage measurement inputs are designed for
measurements in low-voltage networks in which
nominal voltages occur as described in the
"Technical data".
Fuse
(UL/IEC listed)
Three-phase 4-conductor system
Three-phase 4-conductor sys-
tem without voltage transformer.
Three-phase 4-conductor sys-
tem with voltage transformer.
Three-phase 4-conductor
system (symmetrical load)
Three-phase 4-conductor sys-
tem (asymmetrical load)
Three-phase 3-conductor system
Three-phase 3-conductor sys-
tem (asymmetrical load)
Three-phase 3-conductor sys-
tem with voltage transformer.
Voltage measurement L1, L2, L3 (main measurement)
Voltage measurement
Three-phase 4-conductor
systems with rated volt-
ages up to
480 VLN / 830 VLL (+/-10%) according to IEC
347 VLN / 600 VLL (+/-10%) according to UL
3-phase 3-conductor
systems (grounded) with
rated voltages up to
830 VL-L (+/-10%) according to IEC
600 VL-L (+/-10%) according to UL
3-phase 3-conductor sys-
tems (non-grounded) with
rated voltages up to
690 VL-L (+/-10%) according to IEC
600 VL-L (+/-10%) according to UL
Overvoltage category up
to 2000 m
up to 4000 m
· 1000 V CAT III according to IEC
· 600 V CAT III according to UL
· 600 V CAT IV
according to IEC
· 600 V CAT III according to IEC
Rated surge voltage
8 kV
Protection of the voltage
measurement
1 - 10 A tripping characteristic B(with IEC/
UL approval)
Measuring range L-N
0
1)
.. 720 Veff
(max. overvoltage 1000 Veff)
Measuring range L-L
0
1)
.. 1000 Veff
(max. overvoltage 1000 Veff)
Measuring range N-PE
up to 100 V
Resolution
16 bit
Crest factor
1.6 (referred to measuring range 600 V L-N)
Impedance
4 MΩ/phase
Power consumption
approx. 0.1 VA
Sampling frequency
51.2 kHz
Frequency of
fundamental oscillation
- Resolution
40 Hz .. 70 Hz
0.01 Hz
Harmonics
1 .. 127.
1) ... The meter only measures if at least one voltage measurement
input has an L-N voltage of > 10 Veff
or an L-L voltage of > 18 Veff present.
Current measurement (../1A) (../5A)
Nominal current
5 A
Channels
8
· 2 systems (L1, L2, L3, N)
· Single channels
Measuring range
0.005 .. 6 Aeff
Crest factor
(relative to nominal current)
1.98
Overload for 1 s
120 A (sinusoidal)
Resolution
0.1 mA (color graphic display 0.01 A)
Overvoltage category
300 V CAT II
Rated surge voltage
2.5 kV
Power consumption
approx. 0.2 VA (Ri = 5 m
Ω
)
Sampling frequency
25.6 kHz
Harmonics
1 .. 63.
Residual current measurement (RCM)
Nominal current
30 mAeff
Measuring range
0 .. 40 mAeff
Operating current
50 µA
Resolution
1 µA (color graphic display 0.01 A)
Crest factor
1.414 (relative to 40 mA)
Load
4
Ω
Overload for 20 ms
50 A
The measurement device has 4 optional multifunction channels, for use as
· residual current measurement inputs and/or temperature measure-
ment inputs (mixed),
· Additional system inputs (L1, L2, L3; N)
Temperature measurement
Update time
1 s
Total load
(sensor and cable)
max. 4 k
Ω
Cable
<= 30 m (32.81 yd) not shielded
> 30 m (32.81 yd) shielded
Suitable sensor types
KTY83, KTY84, PT100, PT1000
Analog outputs
1 channel
External power supply
max. 33 V DC
Current
0/4...20 mA DC
Update time
0.2 s
Load
max. 300
Ω
Resolution
10 bit
RS-485 interface
3-wire connection with A, B, GND.
See user manual for recommended cable types.
Protocol
Modbus RTU/Slave
Modbus RTU/Gateway
Transmission rate
9.6 kbps, 19.2 kbps, 38.4 kbps,
57.6 kbps, 115.2 kbps
Termination
DIP switches
Ethernet interfaces
Connection
2 x RJ45 (can be used sep-
arately)
Function
Modbus gateway
Protocols and services
OPC UA, DHCP, Modbus/TCP,
NTP, HTTP(S), FTP(S)
Time synchronization
NTP
Potential isolation and electrical safety of the interfaces
The interfaces (RS-485, Ethernet) have:
• Double insulation to the inputs of the voltage and current
measurement.
• Functional insulation relative to each other, to the supply
voltage, to the measuring inputs for residual current and tem-
perature, to the digital inputs/outputs and to the analog output.
The interfaces of the connected devices require double or
reinforced insulation against mains voltages (according to IEC
61010-1: 2010).
Potential isolation and electrical safety of the
multifunction channels (RCM, Temp.)
The inputs of the multifunction channels have:
• Double insulation to the inputs of the voltage and current
measurement.
• No insulation to each other or to the supply voltage.
• Functional isolation to the Ethernet, RS-485 interfaces, to the
digital inputs/outputs and to the analog output.
External sensors and/or transformers require double insulation
relative to system components with dangerous touch voltages
(according to IEC61010-1:2010).
Potential isolation and electrical safety of the
digital inputs and outputs (I/Os) and the analog output
The digital inputs and outputs as well as the analog output are
equipped with:
• Double insulation to the inputs of the voltage and current
measurement.
• Functional isolation relative to each other, to the supply
voltage, to the Ethernet, RS-485 and multifunction channel
interfaces.
Failure mode
Cause
Remedy
No display
External fuse for the supply voltage has tripped.
Replace fuse.
No current display.
No measured voltage connected.
Connect measured voltage.
No measured current connected.
Connect measured current.
Displayed current is
too great or too small.
Current measurement on the wrong phase.
Check connection and correct if necessary.
Current transformer factor incorrectly programmed.
Read and program the current transformer ratio on
the current transformer.
Current harmonic exceeds current peak value at
measuring input.
Install current transformers with a higher current
transformer ratio.
The current at the measuring input is too low.
Install current transformers with a lower current
transformer ratio.
Displayed voltage is
too high or too low.
Measurement on the wrong phase.
Check connection and correct if necessary.
Voltage transformer programmed incorrectly.
Read the voltage transformer ratio on the voltage
transformer and program.
Displayed voltage
is too low.
Overrange.
Use a voltage transformer.
The voltage peak value at the measuring input was
exceeded due to harmonics current.
Attention!
Make sure that the measuring inputs are
not overloaded.
Despite the above measures,
the device does not function.
Device defective.
Send the device and error description to the manu-
facturer for inspection.
230 VAC
24 VDC
+
-
PELV
(grounded low voltage)
Load
Isolation device
Fig. Connection example for “current measurement”.
L1
N
PE
L3
L2
Load
S1 S2
S1 S2
S1 S2
S1 S2
The device:
· Measures current exclusively via current trans-
formers.
· Allows the connection of current transformers
with a transformer ratio of ../1 A and ../5 A.
· Has a current transformer ratio of 5/5 A (I1 to I8)
as the default setting.
· Does not measure DC currents.
The current transformers require basic insulation
according to IEC 61010-1:2010 for the nominal
voltage of the circuit.
WARNING
Risk of injury due to electric voltage or electric
current!
When handling electric currents or voltages, serious
bodily injury or death can result from:
· Touching bare or stripped leads that are ener-
gized.
· Device inputs that pose a hazard when touched.
Before starting work on your system:
·
Disconnect the supply of power!
·
Secure it against being switched on!
·
Check to be sure it is de-energized!
·
Ground and short circuit!
·
Cover or block off adjacent live parts!
L1
N
WARNING
Risk of injury or damage to the device due to
electrical voltage and improper connection!
Failure to comply with the connection conditions for
the voltage measurement inputs can result in dam-
age to the device or serious injury, including death.
Therefore, please observe the following:
·
Switch off your installation before commenc-
ing work! Secure it against being switched on!
Check to be sure it is de-energized! Ground
and short circuit! Cover or block off adjacent
live parts!
·
Do not apply a DC voltage
-
to the voltage measurement inputs.
-
Equip the voltage measurement inputs with
a suitable, marked fuse and isolation device
(alternatively: line circuit breaker) located
nearby.
-
The voltage measurement inputs are dan-
gerous to touch.
·
Connect voltages that exceed the permissi-
ble nominal network voltages via a voltage
transformer.
·
Measured voltages and currents must origi-
nate from the same network.
DANGER
Warns of an imminent danger which, if not avoided,
results in serious or fatal injury.
CAUTION
Warns of an immediately hazardous situation which,
if not avoided, can result in minor or moderate
injury.
N
L3
L2
L1
N
V1
V2
V3
N
V1
V2
V3
N
V1
V2
V3
N
V1
V2
V3
N
V1
V2
V3
N
L3
L2
L1
N
V1
V2
V3
N
L3
L2
L1
L2
L1
L3
L2
L1
N
V1
V2
V3
L3
L2
L1
L3
L2
L1
N
V1
V2
V3
N
L3
L2
L1
N
L3
L2
L1
N
V1
V2
V3
N
V1
V2
V3
N
V1
V2
V3
N
V1
V2
V3
N
V1
V2
V3
N
L3
L2
L1
N
V1
V2
V3
N
L3
L2
L1
L2
L1
L3
L2
L1
N
V1
V2
V3
L3
L2
L1
L3
L2
L1
N
V1
V2
V3
N
L3
L2
L1
WARNING
Risk of injury due to high currents and high
electrical voltages!
Severe bodily injury or death can result from:
· Touching bare or stripped leads that are ener-
gized.
· Device inputs that pose a hazard when touched.
Therefore, please note for your system:
·
Disconnect the supply of power before start-
ing work!
·
Secure it against being switched on!
·
Check to be sure it is de-energized!
·
Ground and short circuit! Use the ground
connection points with the ground symbol for
grounding!
·
Cover or block off adjacent live parts!
WARNING
Of electrical currents and voltages!
Current transformers operated while exposed on
the secondary side (high voltage peaks) can result
in severe bodily injury or death.
Avoid exposed operation of current transform-
ers and short circuit unloaded transformers!
Operation and button functions
The device is operated via 6 function buttons for
• Selecting measuring displays.
• Navigation within the menus.
• Device configuration.
Function buttons
Fig. UMG 801 standard display - measured values
Display for measured values
and device configuration
After restoration of network power, the device
starts with the measured value display
Home
.
Pressing function button 1
(ESC)
displays the
Menu. (See user manual for description).
Ethernet connection configuration
After restoration of network power, the device
starts with the default display
Home
.
· Press function button 1
ESC
to open the menu.
· Use buttons 2 “
5
” and 5 “
6
” to select the
menu item
Configuration
and confirm with
button 3
Enter
.
· The
Configuration
window appears with the
items
Ethernet Config. A
and
Ethernet
Config. B
.
Configuring current transformers
Communication via OPC UA
1. Press function button 1
ESC
,
to open the menu.
2. Use buttons 2 “
5
” and 5 “
6
” to select the menu
item
Configuration
and confirm with button 3
Enter
.
3. In the
Configuration
window, use buttons 2 “
5
”
and 5 “
6
” to select the menu item
Current trans-
formers
and confirm with button 3
Enter
.
4. The
Current transformers
window appears.
5. In the
Current transformers
window, choose the
item
Basic device
and confirm with button 3
Enter
.
6. The item
Basic device
appears marked in "blue."
In the item
Basic device
, choose between basic
device and up to 10 current measuring modules.
7. Confirm the
Basic device
item with button 3
Enter
.
8. Use button 5 "
6
" to go to the setting for the
Primary side of current transformers 1..4
(current
measurement inputs I1..I4) and press button 3,
Enter
.
9. The item for the primary side of the current
transformers I1..I4 “blinks”.
10. Use buttons 4 (
) and 6 (
) to change the posi-
tion of the digit to be set and buttons 2 (
5
) and
5 (
6
) to change the digit (-1/+1).
11. Confirm your entries with button 3
Enter
or end
the action by pressing button 1
ESC
.
12. Use button 6 (
) to go to the configuration of
the secondary side of the current transformers
I1..I4.
13. Configure the secondary side of the current
transformers I1..I4 in the same way.
14. Confirm your entries with button 3
Enter
or end
the action by pressing button 1
ESC
.
15. When you have finished entering data, press
button 1
ESC
to return to the
Menu
window.
Configure the
current transformer 5..8 (I5..I8)
in
accordance with the current transformer ratios
I1..I4!
Multifunction channels (RCM/Temperature)
0..30 mA
Connection example of multifunction channels for
residual current and temperature measurement
7
8
9 10
2x PT100
11 12
L1
N
PE
L3
L2
Load
13 14
The multifunction channels on the UMG 801 offer the
function options
Residual current measurement
(RCM)
and
Temperature measurement.
The resid-
ual current measurement and temperature measure-
ment share the 4 channels (4 each, 2/2, 3/1 or 1/3).
Multifunction channels for
residual current measurement (RCM)
The UMG 801 with its multifunction channels is
suitable, among other things, for use as a residual
current monitoring device (RCM) for monitoring:
· Alternating current
· Direct current and
· Pulsating direct current.
The UMG 801 measures residual currents according
to IEC/TR 60755 of:
Type A
Type B and B+
(via corresponding current transformers)
WARNING
Hazard due to disregard of warning notices and
safety information!
Disregard of warning notices and safety informa-
tion on the device itself and in the usage informa-
tion for the device and its components can lead to
injuries or even death!
Observe the safety information and warning notic-
es on the device itself and in the usage information
associated with the devices and their components,
such as:
· Installation manual.
· User manual.
· Supplement Safety Information.
Communication via TCP/IP
Considering the Ethernet communication settings (step 10),
the measurement device has 2 types of address assign-
ment for the Ethernet interfaces (TCP/IP) in the
DHCP
mode:
1.
Static (fixed IP address)
The user selects the IP address, netmask and gateway
on the measurement device. Use this mode for simple
networks with no DHCP server.
2.
DHCP
At startup, the measurement device automatically
receives an IP address, netmask and gateway from the
DHCP server.
The default settings of the measurement device for Eth-
ernet interfaces A and B is DHCP!
Connection variants for current measurement
Three-phase 4-conductor system
Current measurement via
3 current transformers in a three-phase
4-conductor system.
Current measurement via
2 current transformers in systems with
the same load.
Current measurement I1 to I4 and I5 to I8
N
L3
L2
L1
N
L3
L2
L1
L3
L2
L1
L2
L1
I
1
30
31
I
1
30
31
I
2
32
33
I
3
34
35
I
4
36
37
N
L3
L2
L1
I
1
30
31
I
2
32
33
I
3
34
35
I
4
36
37
I
2
32
33
I
3
34
35
I
4
36
37
I
1
30
31
I
2
32
33
I
3
34
35
I
4
36
37
I
1
30
31
I
2
32
33
I
3
34
35
I
4
36
37
L3
L2
L1
I
1
30
31
I
2
32
33
I
3
34
35
I
4
36
37
Three-phase 3-conductor system
Current measurement via 2 current
transformers (Aron circuit) in a three-
phase 3-conductor system
Current measurement via 3 current
transformers in a three-phase 3-con-
ductor system
N
L3
L2
L1
N
L3
L2
L1
L3
L2
L1
L2
L1
I
1
30
31
I
1
30
31
I
2
32
33
I
3
34
35
I
4
36
37
N
L3
L2
L1
I
1
30
31
I
2
32
33
I
3
34
35
I
4
36
37
I
2
32
33
I
3
34
35
I
4
36
37
I
1
30
31
I
2
32
33
I
3
34
35
I
4
36
37
I
1
30
31
I
2
32
33
I
3
34
35
I
4
36
37
L3
L2
L1
I
1
30
31
I
2
32
33
I
3
34
35
I
4
36
37
The device is a multifunctional network analyzer
that,
• Measures and calculates electrical quantities
such as voltage, current, frequency, power,
work, harmonics current, etc. in building instal-
lations, at distribution boards, circuit breakers
and busbar trunking systems.
• Displays and stores measurement results and
transmits them via interfaces.
Brief device description and installation
ATTENTION
Material damage due to disregard of the instal-
lation instructions!
Disregard of the installation instructions can dam-
age or destroy your device.
·
Provide adequate air circulation in your instal-
lation environment and cooling, as needed,
when the ambient temperatures are high.
·
More information on device functions, data
and installation as well as the battery used in
the device can be found in the user manual.
Mount the measurement device in a switchboard
cabinet or small distribution board according
to DIN 43880 (any mounting orientation) on a
35 mm (1.38 in) DIN rail (for type, see Technical
Data) as follows:
1. Plug the bus connector included in the scope
of delivery into the sockets on the bottom of the
measurement device.
2. Push your measurement device with the bus
connector sideways onto the DIN rail or press it
frontally onto the DIN rail until the bottom bolt
engages.
Fig. Device with bus connector on DIN rail
Bus connector
DIN rail
Bottom bolt
2.
1.
INFORMATION
Indicates procedures in which there is
no
hazard of
personal injury or material damage.
Recommendation:
Use the GridVis
®
software to configure the trans-
former ratios for residual current transformers.
0..30 mA
Safety information in the installation manual is
marked by a warning triangle and, in dependence
on the degree of hazard, is displayed as follows:
WARNING
Warns of a potentially hazardous situation which, if
not avoided, could result in serious injury or death.
The data transfer using the OPC UA protocol
takes place via the Ethernet interfaces of your
device.
The Ethernet interface and the data transfer using
the OPC UA protocol can be configured conve-
niently in the GridVis
®
software.
Fig. Configuration menu item
Fig. Configuration window
Fig. Configuration window with the
entries Ethernet Config. A and B
(in Dedicated mode).
Fig. Ethernet (TCP/IP) window
Fig. Current transformer window
N
L3
L2
L1
N
V1
V2
V3
N
V1
V2
V3
N
V1
V2
V3
N
V1
V2
V3
N
V1
V2
V3
N
L3
L2
L1
N
V1
V2
V3
N
L3
L2
L1
L2
L1
L3
L2
L1
N
V1
V2
V3
L3
L2
L1
L3
L2
L1
N
V1
V2
V3
N
L3
L2
L1
N
L3
L2
L1
N
L3
L2
L1
L3
L2
L1
L2
L1
I
1
30
31
I
1
30
31
I
2
32
33
I
3
34
35
I
4
36
37
N
L3
L2
L1
I
1
30
31
I
2
32
33
I
3
34
35
I
4
36
37
I
2
32
33
I
3
34
35
I
4
36
37
I
1
30
31
I
2
32
33
I
3
34
35
I
4
36
37
I
1
30
31
I
2
32
33
I
3
34
35
I
4
36
37
L3
L2
L1
I
1
30
31
I
2
32
33
I
3
34
35
I
4
36
37
N
L3
L2
L1
N
L3
L2
L1
L3
L2
L1
L2
L1
I
1
30
31
I
1
30
31
I
2
32
33
I
3
34
35
I
4
36
37
N
L3
L2
L1
I
1
30
31
I
2
32
33
I
3
34
35
I
4
36
37
I
2
32
33
I
3
34
35
I
4
36
37
I
1
30
31
I
2
32
33
I
3
34
35
I
4
36
37
I
1
30
31
I
2
32
33
I
3
34
35
I
4
36
37
L3
L2
L1
I
1
30
31
I
2
32
33
I
3
34
35
I
4
36
37
N
L3
L2
L1
N
V1
V2
V3
N
V1
V2
V3
N
V1
V2
V3
N
V1
V2
V3
N
V1
V2
V3
N
L3
L2
L1
N
V1
V2
V3
N
L3
L2
L1
L2
L1
L3
L2
L1
N
V1
V2
V3
L3
L2
L1
L3
L2
L1
N
V1
V2
V3
N
L3
L2
L1
Connection capacity of the terminals (supply voltage)
Connectible conductors.
Only connect one conductor per terminal point!
Single core, multi-core,
fine-stranded
0.2 - 2.5 mm
2
, AWG 26-12
Wire ferrules (non-insulated)
· Recommended strip length
0.2 - 2.5 mm
2
, AWG 26-12
· 10 mm (0.3937 in)
Wire ferrules (insulated) *
· Recommended strip length **
0.2 - 2.5 mm
2
, AWG 26-12
· 12 mm
(≤1.5 mm
2
), 10 mm
(>1.5 mm
2
) /
0.47 in
(≤1.5 mm
2
), 0.39 in
(>1.5 mm
2
)
Wire ferrules:
Contact sleeve length **
8 - 12 mm (0.31 - 0.47 in)
*
... Applies to wire ferrules with a maximum plastic collar outer
diameter of up to 4.5 mm (0.18 in).
**
.. Depending on the type of wire ferrules used (ferrule
manufacturer).
Connection capacity of the terminals
(digital inputs/outputs, analog output)
Single core, multi-core,
fine-stranded
0.2 - 1.5 mm
2
, AWG 24-16
Wire ferrules (non-insulated)
0.2 - 1.5 mm
2
, AWG 26-16
Wire ferrules (insulated)
0.2 - 1 mm
2
, AWG 26-18
Tightening torque
0.2 - 0.25 Nm (1.77 - 2.21 lbf in)
Strip length
7 mm (0.2756 in)
Connection capacity of the terminals (current measure-
ment)
Connectible conductors.
Only connect one conductor per terminal point!
Single core, multi-core,
fine-stranded
0.2 - 2.5 mm
2
, AWG 26-12
Wire ferrules (non-insulated)
· Recommended strip length
0.2 - 2.5 mm
2
, AWG 26-12
· 10 mm (0.3937 in)
Wire ferrules (insulated) *
· Recommended strip length **
0.2 - 2.5 mm
2
, AWG 26-12
· 12 mm
(≤1.5 mm
2
), 10 mm
(>1.5 mm
2
) /
0.47 in (≤1.5 mm
2
), 0.39 in
(>1.5 mm
2
)
Wire ferrules:
Contact sleeve length **
8 - 12 mm (0.31 - 0.47 in)
Tightening torque
Screw flange
0.2 Nm (1.77 lbf in)
*
... Applies to wire ferrules with a maximum plastic collar outer
diameter of up to 4.5 mm (0.18 in).
**
.. Depending on the type of wire ferrules used (ferrule
manufacturer).
Connection capacity of the terminals (RS-485)
Single core, multi-core,
fine-stranded
0.2 - 1.5 mm
2
, AWG 24-16
Wire ferrules (non-insulated)
0.2 - 1.5 mm
2
, AWG 26-16
Wire ferrules (insulated)
0.2 - 1 mm
2
, AWG 26-18
Tightening torque
0.2 - 0.25 Nm (1.77 - 2.21 lbf in)
Strip length
7 mm (0.2756 in)
Connection capacity of the terminals
(voltage measurement)
Connectible conductors
Only connect one conductor per terminal point!
Single core, multi-core,
fine-stranded
0.08 - 4 mm
2
, AWG 28-12
Wire ferrules
(insulated/non-insulated)
0.25 - 2.5 mm
2
, AWG 24-14
Strip length
8-9 mm (0.3150 - 0.3543 in)
Connection capacity of the terminals -
Multifunction channels (RCM, Temp.)
Connectible conductors.
Only connect one conductor per terminal point!
Single core, multi-core,
fine-stranded
0.2 - 1.5 mm
2
, AWG 24-16
Wire ferrules (non-insulated)
0.2 - 1.5 mm
2
, AWG 26-16
Wire ferrules (insulated)
0.2 - 1 mm
2
, AWG 26-18
Tightening torque
0.2 - 0.25 Nm (1.77 - 2.21 lbf in)
Strip length
7 mm (0.2756 in)
Connection capacity of the terminals (functional earth A/D)
Connectible conductors.
Only connect one conductor per terminal point!
Single core, multi-core,
fine-stranded
0.2 - 4 mm
2
, AWG 24-12
Wire ferrules (non-insulated)
0.2 - 4 mm
2
, AWG 24-12
Wire ferrules (insulated)
0.2 - 2.5 mm
2
, AWG 26-14
Tightening torque
0.4 - 0.5 Nm (3.54 - 4.43 lbf in)
Strip length
7 mm (0.2756 in)
Configure the Ethernet (TCP/IP) settings using the function
buttons as described in step 12 "Operation and button
functions".
Residual current measurement (RCM)
Overload for 1 s
5 A
Permanent overload
1 A
Norm
IEC/TR 60755 (2008-01),
Type A / Type B and B+ (via corre-
sponding current transformers)
Technical data
General
Net weight
420 g (0.926 lb)
Device dimensions
Approx. B = 144 mm (5.67 in), H =
90 mm (3.54 in),
D = 76 mm (2.99 in)
Battery
Type: Lithium CR2032, 3 V
(UL1642 approval)
Integrated memory
4 GB
Backlight service life
40000 h
(50% of the start brightness)
Mounting orientation
As desired
Fastening/mounting -
Suitable DIN rails - 35 mm
(1.38 in)
· TS 35/7.5 according to EN 60715
· TS 35/10
· TS 35/15 x 1.5
Impact resistance
IK07 according to IEC 62262
Transport and storage
The following specifications apply for devices transported and
stored in the original packaging.
Free fall
1 m (39.37 in)
Temperature
-25 °C (-13 °F) to +70 °C (158 °F)
Relative humidity
5 to 95% at 25 °C (77 °F),
no condensation
Environmental conditions during operation
The device:
• Is for weather-protected and stationary use.
• Fulfills operating conditions according to DIN IEC 60721-3-3.
• Has protection class II according to IEC 60536 (VDE 0106,
part 1),
a ground wire connection is not required!
Rated temperature range
-10 °C (14 °F) to +55 °C (131 °F)
Relative humidity
5 to 95% at 25 °C (77 °F),
no condensation
Operating elevation
(for overvoltage categories,
see voltage and current
measurement)
2000 m (6562 ft) above sea level
4000 m (13,124 ft) above sea level
Pollution degree
2
Ventilation
No forced ventilation required.
Protection against foreign
matter and water
IP20 according to EN60529
Supply voltage
Nominal range
DC: 24 V, PELV
Operating range
+/-10% of nominal range
Power consumption
max. 4 W
Maximum power
consumption with 10
modules
12 W (UMG 801 at 4 W plus
10 modules at 0.8 W each)
Recommended overcurrent
protective device for line
protection
2-6 A, (Char. B), IEC/UL approval
19
Configuring voltage transformers
17
1. Press function button 1
ESC
to open
the menu.
2. Use buttons 2 “
5
” and 5 “
6
” to select the
menu item
Configuration
and confirm with
button 3
Enter
.
3. In the
Configuration
window, use buttons 2
“
5
” and 5 “
6
” to select the item
Voltage
transformer
and confirm with button 3
Enter
.
4. The
voltage transformer
window appears.
5. In the
Voltage transformer
window, select the
item
Transformer 1..4
(voltage measurement
inputs L1 to L4) and press button 3,
Enter
.
6. The item for the primary side of the transform-
er 1..4 “blinks”.
7. Use buttons 4 (
) and 6 (
) to change the
position of the digit to be set and buttons 2
(
5
) and 5 (
6
) to change the digit (-1/+1).
8. Confirm your entries with button 3
Enter
or
end the action by pressing button 1
ESC
.
9. Use button 6 (
) to go to the configuration
of the secondary side of the transformer 1..4
(voltage measurement inputs L1 to L4).
10. Configure the secondary side of voltage trans-
formers 1..4 in the same way.
11. Confirm your entries with button 3
Enter
or end
the action by pressing button 1
ESC
.
12. When you have finished entering data, press
button 1
ESC
to return to the
Menu
window.
Fig. Voltage transformer window
ATTENTION
Faulty cross currents, incorrect measure-
ments, and even damage to the device and/or
your system due to lack of galvanic isolation!
A lack of galvanic isolation of active external cur-
rent transformers (or other current sensors) on the
multifunction channels from the supply voltage
of the device can lead to faulty cross currents,
incorrect measurements or even damage to your
device and/or system.
· Do
not
take the auxiliary voltage supply of
active external current transformers (or other
current sensors) on the multifunction channels
from the supply voltage of the device! For each
active current transformer, use galvanically
isolated power supplies (secondary side).
· Do
not
ground passive current transformers on
the multifunction channels! Observe the usage
information of the current transformer manu-
facturer.
N
L3
L2
L1
N
V1
V2
V3
N
V1
V2
V3
N
V1
V2
V3
N
V1
V2
V3
N
V1
V2
V3
N
L3
L2
L1
N
V1
V2
V3
N
L3
L2
L1
L2
L1
L3
L2
L1
N
V1
V2
V3
L3
L2
L1
L3
L2
L1
N
V1
V2
V3
N
L3
L2
L1
N
L3
L2
L1
N
V1
V2
V3
N
V1
V2
V3
N
V1
V2
V3
N
V1
V2
V3
N
V1
V2
V3
N
L3
L2
L1
N
V1
V2
V3
N
L3
L2
L1
L2
L1
L3
L2
L1
N
V1
V2
V3
L3
L2
L1
L3
L2
L1
N
V1
V2
V3
N
L3
L2
L1
Three-phase 4-conductor systems
with grounded neutral conductor
Three-phase 4-conductor
systems
with non-grounded neutral conduc-
tor (IT networks)
Three-phase 3-conductor
systems
ungrounded
Three-phase 3-conductor
systems
with grounded phase
L1
L2
L3
E
E
N
E
L1
L2
L3
E
N
R
L1
L2
L3
E
E
L1
L2
E
E
L
N
E
E
L1
L2
L3
E
E
L1
L2
N
E
E
L1
L2
L3
E
E
N
E
L1
L2
L3
E
N
R
L1
L2
L3
E
E
L1
L2
E
E
L
N
E
E
L1
L2
L3
E
E
L1
L2
N
E
E
L1
L2
L3
E
E
N
E
L1
L2
L3
E
N
R
L1
L2
L3
E
E
L1
L2
E
E
L
N
E
E
L1
L2
L3
E
E
L1
L2
N
E
E
L1
L2
L3
E
E
N
E
L1
L2
L3
E
N
R
L1
L2
L3
E
E
L1
L2
E
E
L
N
E
E
L1
L2
L3
E
E
L1
L2
N
E
E
IEC
UL-N / UL-L: 480 VLN / 830 VLL
UL-L: 690 VLL
UL-L: 830 VLL
UL
UL-N / UL-L: 347 VLN / 600 VLL
UL-L: 600 VLL
UL-L: 600 VLL
Functional earth
INFORMATION
The functional earthing is a functional part and essential
for the regular operation of the electrical system.
INFORMATION
For a PE/N measurement, connect measuring
input A as the functional earth. Do not use a
green-yellow wire for this, as the conductor has
no protective function!
INFORMATION
Before you start with the DIN rail mounting and
cabling of your UMG 801, make sure that the
bus connector is mounted on the bottom of your
UMG 801. Then connect up to 10 modules via bus
connectors.
INFORMATION
Functional earth
·
Connection D
(UMG 801) in TN, TT and IT net-
works must always be connected.
·
Connection A
(UMG 801) only connect in TN and
TT networks (
not in IT networks
)
INFORMATION
· The meter does not have a password (00000000)
ex works.
· For detailed information on configuring a pass-
word, operation, display and button functions of
your device, refer to the user manual.
INFORMATION
Detailed information on all menu items and their
settings can be found in the user manual.
INFORMATION
· The multifunction channels are suitable for con-
necting residual current transformers with a nom-
inal current of up to 30 mA and have the "Current
transformer connection test" function.
· The residual current measurement monitors the
residual currents via external current transformers
and, if a threshold value is exceeded, can trigger
a warning signal. The meter is not an independent
protective device against electric shock!
INFORMATION
Voltage transformer ratios can also be configured in
the device configuration of the GridVis
®
software.
INFORMATION
Optionally configure the current transformer ratios
· in the device configuration of the GridVis
®
software.
· via the measurement device homepage of the basic
device.
INFORMATION
· Consult your network administrator for the correct
Ethernet network settings for your device.
· Descriptions of the communication interfaces can
be found in the user manual.
· Information on the connection and communication
of your device with the software can be found in
the online help for the GridVis
®
software.
INFORMATION
· Consult your network administrator for the correct Ethernet
network settings for your measurement device.
· Descriptions of the communication interfaces can be found
in the user manual.
· Information on the connection and communication of your
measurement device with the software can be found in the
online help for the GridVis
®
software.
Patch cable
Your measurement device has two Ethernet
interfaces (A and B) for communication in Ether-
net networks. There are 2 options to integrate the
measurement device into Ethernet networks:
1.
Measurement device integration in a network
with additional switch function (switched
mode).
The measurement device is automatical-
ly assigned an IP address by a DHCP server in
an IT network via Ethernet interface A, for exam-
ple. Ethernet interface B has a switch function
via which further devices (hardware components)
can be connected in series. The measurement
device also allows the reverse use of the Ether-
net interfaces (e.g. "B" for the IP address from a
network and "A" for further devices)!
2.
Measurement device integration in 2 different
networks (dedicated mode)
.
The Ethernet interfaces A and B of the mea-
surement device are each assigned different IP
addresses by 2 different networks.
Button Function
· Display menu.
· One step back.
· Cancel action
(ESC)
.
· Repeated actuation leads to the menu.
· Select menu item or position
(up, "
5
").
· Change selection (digit +1).
· Confirm selection
(Enter)
· Select position (to the left, "
").
· Select menu item or position
(down, "
6
").
· Change selection (digit -1).
· Select position (to the right “
”).
Ethernet A
Ethernet B
Recommendation:
Use at least CAT5 cable!
Patch cable
INFORMATION
For configuration of the IP addresses on the measure-
ment device, observe step 13 "Configuring the Ethernet
connection" and step 14 "Communication via TCP/IP".
· In the
Configuration
window, use buttons 2 "
5
"
and 5 "
6
" to select the respective entry of the
Ethernet interface to be configured and confirm
with button 3
Enter
.
· The window for configuring the TCP/IP Ethernet
settings appears (see step 13 "Communication
via TCP/IP").
INFORMATION
Detailed technical data can be found in the user man-
ual for the measurement device at www.janitza.de.
INFORMATION
You can configure current transformer
ratios
conveniently via
· The device menu.
· The GridVis
®
software.
For information on programming the current
transformer ratios, refer to the user manual.
INFORMATION
·
The switched and dedicated modes of the mea-
surement device can be configured in the GridVis
®
software.
·
The default setting of the measurement device is
the switched mode.
·
A mode change only takes effect after a hard reset
(disconnect the measurement device from the sup-
ply voltage while observing the safety regulations)!
ATTENTION
Material damage due to security vulnerabilities in
programs, IT networks and protocols.
Security vulnerabilities can lead to data misuse and
faults and even the standstill of your IT infrastructure.
To protect your IT system, network, data commu-
nications and measurement devices:
·
Inform your network administrator and/or IT
representative.
·
Always keep the meter firmware up to date and
protect the communication to the meter with an
external firewall. Close unused ports.
·
Take protective measures against viruses and
cyber attacks from the Internet, e.g. through
firewall solutions, security updates and virus
protection programs.
·
Eliminate security vulnerabilities and update or
renew existing protection for your IT infrastruc-
ture.
ATTENTION
Material damage due to incorrect network
settings.
Incorrect network settings can cause faults in the IT
network!
Consult your network administrator for the cor-
rect network settings for your device.
Connection of the device with a patch cable (Ethernet interface) via
a switch/router to the OPC UA server and the PC.
PC and device require a fixed IP address.
PC
Patch cable
Patch cable
OPC UA-
Server
PC
Switch/
Router
UMG 801
Patch cable
Patch cable
DHCP
Server
PC
Switch/
Router
The DHCP server automatically assigns IP addresses to device
and PC.
UMG 801
UMG 801
PC connections
The most common connection methods for com-
munication of the measurement device with a PC
(with GridVis
®
software installed) are described
below.
1. Connection to a DHCP server and PC. The
DHCP server automatically assigns IP ad-
dresses to the device and the PC.
2. Connection as master device with an
RS-485 bus structure (Modbus RTU) to a PC
and OPC UA client.
3. PC direct connection to the device. PC and
device require a fixed IP address.
Ethernet
Ethernet
Ethernet
Modbus TCP
Ethernet
Modbus TCP
Patch cable
Ethernet
INFORMATION
With regard to the configuration of the IP addresses
on the measurement device, also observe steps 10
and 12 to 15!
PC
DHCP
Server
UMG 801
Ethernet A
Ethernet B
Switch/
Router
PC
Network A
Dedicated mode: Different IP addresses for Ethernet interfaces A
and B for separate networks.
Network B
DHCP
Server
Switch/
Router
Switched mode: Ethernet interface B of the UMG 801 for con-
necting an Ethernet device. The measurement device also allows
the reverse use of the Ethernet interfaces (A for the Ethernet
device and B for an IP address from a network).
PC
DHCP
Server
Switch/
Router
UMG 801
A
B
e.g.
UMG 96PQ-L
"Switched mode" connection option:
"Dedicated mode" connection option
11
RS-485
(Modbus RTU)
Transformer 1..4
Primary
Secondary
Voltage Transformer
ESC
400 V
400 V
Device
Transformer 1..4
Transformer 5..8
Basic device
Primary
Secondary
Current Transformer
ESC
5 A
5 A
5 A
5 A
Ethernet config. A
Ethernet config. B
Fieldbus
Current Transformer
Voltage Transformer
Configuration
ESC
IP Config.
IP Address
Netmask
Gateway
DHCP
192. 168. 3. 177
192. 168. 3. 4
255. 255. 255. 0
Ethernet (TCP/IP)
ESC
Ethernet config. A
Ethernet config. B
Fieldbus
Current Transformer
Voltage Transformer
Configuration
ESC
Energy
Drag pointer
Multifunctional Channels
Digital I/O Status
Configuration
Menü
General
1
2
Janitza electronics GmbH
Vor dem Polstück 6
D-35633 Lahnau
Support tel. +49 6441 9642-22
Email: [email protected]
www.janitza.de
www
.janitza.de
Doc. no. 2.053.005.4.a 04/2023
Part no. 33.03.376
Power Analyzer
UMG 801
Installation manual
Installation
Device settings
German version:
see r
ear side
2
Safety
Safety information
The installation manual does not represent a
complete set of all safety measures required for
the operation of the device.
Special operating conditions can require addi-
tional measures. The installation manual contains
information which must be observed to ensure
your personal safety and avoid material damage.
Symbols used on the device:
The additional symbol on the de-
vice itself indicates an electrical
danger that can result in serious
injuries or death.
This general warning symbol
draws attention to a possible risk
of injury. Be certain to observe all
of the information listed under this
symbol in order to avoid possible
injury or even death.
Safety measures
When operating electric devices, it is unavoidable
for certain parts of these devices to conduct
hazardous voltage. Consequently, severe bodily
injury or material damage can occur if they are
not handled properly:
• Before making connections to the device,
ground the device by means of the ground
wire connection, if present.
• Hazardous voltages can be present in all
circuitry parts that are connected to the power
supply.
• There can still be hazardous voltages present
in the device even after it has been discon-
nected from the supply voltage (capacitor
storage).
• Do not operate equipment with current trans-
former circuits when open.
• Do not exceed the limit values specified in the
user manual and on the rating plate! This must
also be observed during testing and commis-
sioning!
• Observe the safety information and warning
notices in the usage information associated
with the device and its components!
Qualified personnel
To avoid bodily injury and material damage, only
qualified personnel with electrical training are
permitted to work on the basic device and its
components who have knowledge of:
• The national accident prevention regulations.
• Safety technology standards,
• Installation, commissioning and operation of
the device and the components.
Intended use
The device is:
• Intended only for use in the field of
industrial
controls
.
• Intended for installation in switchboard
cabinets and small distribution boards. The
mounting orientation is arbitrary (Please ob-
serve step 3 "Installation").
• Not intended for installation in vehicles! Use
of the device in non-stationary equipment
constitutes an exceptional environmental
condition and is only permissible by special
agreement.
• Not intended for installation in environments
with harmful oils, acids, gases, vapors, dusts,
radiation, etc.
• Designed as an indoor meter.
Disclaimer
Compliance with the usage information for the
devices is a prerequisite for safe operation and
attaining the stated performance characteristics
and product features. Janitza electronics GmbH
assumes no liability for bodily injury, material
damage or financial losses which result from dis-
regard of the usage information. Ensure that your
informational products are readily accessible in a
legible form.
Further usage information, such as the user man-
ual, can be found on our website www.janitza.de
under Support > Downloads.
Copyright notice
© 2023 - Janitza electronics GmbH - Lahnau.
All rights reserved. Any reproduction, processing,
distribution or other use, in whole or in part, is
prohibited.
Subject to technical alterations.
• Make sure that your device matches the
installation manual.
• First make sure you have read and under-
stood the usage information accompanying
the product.
• Keep the usage information associated with
the product available for the entire service life
and pass it on to any possible subsequent
users.
• Please find out about device revisions and
the associated modifications of the usage
information associated with your product at
www.janitza.de.
Disposal
Please abide by national regulations! Dispose
of individual parts, as applicable, depending on
their composition and existing country-specific
regulations, e.g. as:
• Electronic waste
• Batteries and rechargeable batteries
• Plastics
• Metals
or engage a certified disposal company to handle
scrapping.
Relevant laws,
standards and directive used
Please see the declaration of conformity on our
website (www.janitza.de) for the laws, standards
and directives applied for the device by Janitza
electronics GmbH.
3
Applying the supply voltage
The supply voltage your device requires can be
found on the rating plate. After connecting the
supply voltage, the display becomes active. If
no display appears, check whether the supply
voltage is within the nominal voltage range.
ATTENTION
Material damage due to disregard of the connec-
tion conditions or impermissible overvoltages
Disregard of the connection instructions or exceed-
ing the permissible voltage range can damage or
destroy your device.
Before connecting the device to the supply volt-
age, please note:
· Voltage and frequency must correspond to the
specifications on the rating plate! Observe limit
values as described in the user manual!
· In the building installation, secure the supply volt-
age with a UL/IEC listed line circuit breaker/fuse!
· Observe the following for the isolation device
- Install it close to the device and easily accessi-
ble for the user.
- Mark it for the respective device.
· Do not tap the supply voltage from the voltage
transformers.
· Provide a fuse for the neutral conductor if the
neutral conductor terminal of the source is not
grounded.
Procedure in the event of a malfunction
14
18
9
10
12
13
Ethernet communication
5
Voltage measurement
4
Grid systems
Suitable grid systems and maximum rated voltages (DIN EN 61010-1/A1):
6
Connection variants for voltage measurement
7
Current measurement
8
ATTENTION
Warns of an immediately hazardous situation
which, if not avoided, can result in material or
environmental damage.
Incoming goods inspection
The prerequisites for trouble-free and safe opera-
tion of the devices and their components include
proper transport, storage, setup and assembly,
as well as proper operation and maintenance.
Exercise due caution when unpacking and pack-
ing the device, do not use force and only use
suitable tools.
Check:
• Visually inspect the devices and components
for flawless mechanical condition.
• Check the scope of delivery (see user manual)
for completeness before you begin installing
your devices and components.
If it must be assumed that safe operation is no
longer possible, immediately put the device with
components out of service and secure against
unintentional startup.
It can be assumed that safe operation is no
longer possible, for example, if the device with
components:
• Has visible damage,
• No longer functions despite an intact power
supply.
• Was subjected to extended periods of unfa-
vorable conditions (e.g. storage outside of the
permissible climate thresholds without adjust-
ment to the room climate, condensation, etc.)
or transport stress (e.g. falling from an elevated
position, even without visible external damage,
etc.).
Digital outputs
4 digital outputs, solid state relays, not short-circuit proof.
Switching voltage
Max. 60 V DC
Switching current
max. 50 mAeff DC
Response time
approx. 500 ms
Digital output (energy pulses)
max. 20 Hz
Digital inputs
4 digital inputs, solid state relays, not short-circuit proof.
Maximum counter frequency
20 Hz
Input signal applied
18 V .. 28 V DC
(typical 4 mA)
Input signal not applied
0 .. 5 V DC,
current less than 0.5 mA
Cable length (digital inputs/outputs)
Up to 30 m (32.81 yd)
Unshielded
Greater than 30 m (32.81 yd)
Shielded
User Manual:
15
16
20
Application areas for the device
• 3 and 4-conductor networks (TN, TT and IT
networks).
• Residential and industrial areas.
The device has 4 voltage measurement inputs
and is suitable for various connection variants.
L1
N
PE/FE
L3
L2
Fig. Connection example for “voltage measurement”.
The voltage measurement inputs are designed for
measurements in low-voltage networks in which
nominal voltages occur as described in the
"Technical data".
Fuse
(UL/IEC listed)
Three-phase 4-conductor system
Three-phase 4-conductor sys-
tem without voltage transformer.
Three-phase 4-conductor sys-
tem with voltage transformer.
Three-phase 4-conductor
system (symmetrical load)
Three-phase 4-conductor sys-
tem (asymmetrical load)
Three-phase 3-conductor system
Three-phase 3-conductor sys-
tem (asymmetrical load)
Three-phase 3-conductor sys-
tem with voltage transformer.
Voltage measurement L1, L2, L3 (main measurement)
Voltage measurement
Three-phase 4-conductor
systems with rated volt-
ages up to
480 VLN / 830 VLL (+/-10%) according to IEC
347 VLN / 600 VLL (+/-10%) according to UL
3-phase 3-conductor
systems (grounded) with
rated voltages up to
830 VL-L (+/-10%) according to IEC
600 VL-L (+/-10%) according to UL
3-phase 3-conductor sys-
tems (non-grounded) with
rated voltages up to
690 VL-L (+/-10%) according to IEC
600 VL-L (+/-10%) according to UL
Overvoltage category up
to 2000 m
up to 4000 m
· 1000 V CAT III according to IEC
· 600 V CAT III according to UL
· 600 V CAT IV
according to IEC
· 600 V CAT III according to IEC
Rated surge voltage
8 kV
Protection of the voltage
measurement
1 - 10 A tripping characteristic B(with IEC/
UL approval)
Measuring range L-N
0
1)
.. 720 Veff
(max. overvoltage 1000 Veff)
Measuring range L-L
0
1)
.. 1000 Veff
(max. overvoltage 1000 Veff)
Measuring range N-PE
up to 100 V
Resolution
16 bit
Crest factor
1.6 (referred to measuring range 600 V L-N)
Impedance
4 MΩ/phase
Power consumption
approx. 0.1 VA
Sampling frequency
51.2 kHz
Frequency of
fundamental oscillation
- Resolution
40 Hz .. 70 Hz
0.01 Hz
Harmonics
1 .. 127.
1) ... The meter only measures if at least one voltage measurement
input has an L-N voltage of > 10 Veff
or an L-L voltage of > 18 Veff present.
Current measurement (../1A) (../5A)
Nominal current
5 A
Channels
8
· 2 systems (L1, L2, L3, N)
· Single channels
Measuring range
0.005 .. 6 Aeff
Crest factor
(relative to nominal current)
1.98
Overload for 1 s
120 A (sinusoidal)
Resolution
0.1 mA (color graphic display 0.01 A)
Overvoltage category
300 V CAT II
Rated surge voltage
2.5 kV
Power consumption
approx. 0.2 VA (Ri = 5 m
Ω
)
Sampling frequency
25.6 kHz
Harmonics
1 .. 63.
Residual current measurement (RCM)
Nominal current
30 mAeff
Measuring range
0 .. 40 mAeff
Operating current
50 µA
Resolution
1 µA (color graphic display 0.01 A)
Crest factor
1.414 (relative to 40 mA)
Load
4
Ω
Overload for 20 ms
50 A
The measurement device has 4 optional multifunction channels, for use as
· residual current measurement inputs and/or temperature measure-
ment inputs (mixed),
· Additional system inputs (L1, L2, L3; N)
Temperature measurement
Update time
1 s
Total load
(sensor and cable)
max. 4 k
Ω
Cable
<= 30 m (32.81 yd) not shielded
> 30 m (32.81 yd) shielded
Suitable sensor types
KTY83, KTY84, PT100, PT1000
Analog outputs
1 channel
External power supply
max. 33 V DC
Current
0/4...20 mA DC
Update time
0.2 s
Load
max. 300
Ω
Resolution
10 bit
RS-485 interface
3-wire connection with A, B, GND.
See user manual for recommended cable types.
Protocol
Modbus RTU/Slave
Modbus RTU/Gateway
Transmission rate
9.6 kbps, 19.2 kbps, 38.4 kbps,
57.6 kbps, 115.2 kbps
Termination
DIP switches
Ethernet interfaces
Connection
2 x RJ45 (can be used sep-
arately)
Function
Modbus gateway
Protocols and services
OPC UA, DHCP, Modbus/TCP,
NTP, HTTP(S), FTP(S)
Time synchronization
NTP
Potential isolation and electrical safety of the interfaces
The interfaces (RS-485, Ethernet) have:
• Double insulation to the inputs of the voltage and current
measurement.
• Functional insulation relative to each other, to the supply
voltage, to the measuring inputs for residual current and tem-
perature, to the digital inputs/outputs and to the analog output.
The interfaces of the connected devices require double or
reinforced insulation against mains voltages (according to IEC
61010-1: 2010).
Potential isolation and electrical safety of the
multifunction channels (RCM, Temp.)
The inputs of the multifunction channels have:
• Double insulation to the inputs of the voltage and current
measurement.
• No insulation to each other or to the supply voltage.
• Functional isolation to the Ethernet, RS-485 interfaces, to the
digital inputs/outputs and to the analog output.
External sensors and/or transformers require double insulation
relative to system components with dangerous touch voltages
(according to IEC61010-1:2010).
Potential isolation and electrical safety of the
digital inputs and outputs (I/Os) and the analog output
The digital inputs and outputs as well as the analog output are
equipped with:
• Double insulation to the inputs of the voltage and current
measurement.
• Functional isolation relative to each other, to the supply
voltage, to the Ethernet, RS-485 and multifunction channel
interfaces.
Failure mode
Cause
Remedy
No display
External fuse for the supply voltage has tripped.
Replace fuse.
No current display.
No measured voltage connected.
Connect measured voltage.
No measured current connected.
Connect measured current.
Displayed current is
too great or too small.
Current measurement on the wrong phase.
Check connection and correct if necessary.
Current transformer factor incorrectly programmed.
Read and program the current transformer ratio on
the current transformer.
Current harmonic exceeds current peak value at
measuring input.
Install current transformers with a higher current
transformer ratio.
The current at the measuring input is too low.
Install current transformers with a lower current
transformer ratio.
Displayed voltage is
too high or too low.
Measurement on the wrong phase.
Check connection and correct if necessary.
Voltage transformer programmed incorrectly.
Read the voltage transformer ratio on the voltage
transformer and program.
Displayed voltage
is too low.
Overrange.
Use a voltage transformer.
The voltage peak value at the measuring input was
exceeded due to harmonics current.
Attention!
Make sure that the measuring inputs are
not overloaded.
Despite the above measures,
the device does not function.
Device defective.
Send the device and error description to the manu-
facturer for inspection.
230 VAC
24 VDC
+
-
PELV
(grounded low voltage)
Load
Isolation device
Fig. Connection example for “current measurement”.
L1
N
PE
L3
L2
Load
S1 S2
S1 S2
S1 S2
S1 S2
The device:
· Measures current exclusively via current trans-
formers.
· Allows the connection of current transformers
with a transformer ratio of ../1 A and ../5 A.
· Has a current transformer ratio of 5/5 A (I1 to I8)
as the default setting.
· Does not measure DC currents.
The current transformers require basic insulation
according to IEC 61010-1:2010 for the nominal
voltage of the circuit.
WARNING
Risk of injury due to electric voltage or electric
current!
When handling electric currents or voltages, serious
bodily injury or death can result from:
· Touching bare or stripped leads that are ener-
gized.
· Device inputs that pose a hazard when touched.
Before starting work on your system:
·
Disconnect the supply of power!
·
Secure it against being switched on!
·
Check to be sure it is de-energized!
·
Ground and short circuit!
·
Cover or block off adjacent live parts!
L1
N
WARNING
Risk of injury or damage to the device due to
electrical voltage and improper connection!
Failure to comply with the connection conditions for
the voltage measurement inputs can result in dam-
age to the device or serious injury, including death.
Therefore, please observe the following:
·
Switch off your installation before commenc-
ing work! Secure it against being switched on!
Check to be sure it is de-energized! Ground
and short circuit! Cover or block off adjacent
live parts!
·
Do not apply a DC voltage
-
to the voltage measurement inputs.
-
Equip the voltage measurement inputs with
a suitable, marked fuse and isolation device
(alternatively: line circuit breaker) located
nearby.
-
The voltage measurement inputs are dan-
gerous to touch.
·
Connect voltages that exceed the permissi-
ble nominal network voltages via a voltage
transformer.
·
Measured voltages and currents must origi-
nate from the same network.
DANGER
Warns of an imminent danger which, if not avoided,
results in serious or fatal injury.
CAUTION
Warns of an immediately hazardous situation which,
if not avoided, can result in minor or moderate
injury.
N
L3
L2
L1
N
V1
V2
V3
N
V1
V2
V3
N
V1
V2
V3
N
V1
V2
V3
N
V1
V2
V3
N
L3
L2
L1
N
V1
V2
V3
N
L3
L2
L1
L2
L1
L3
L2
L1
N
V1
V2
V3
L3
L2
L1
L3
L2
L1
N
V1
V2
V3
N
L3
L2
L1
N
L3
L2
L1
N
V1
V2
V3
N
V1
V2
V3
N
V1
V2
V3
N
V1
V2
V3
N
V1
V2
V3
N
L3
L2
L1
N
V1
V2
V3
N
L3
L2
L1
L2
L1
L3
L2
L1
N
V1
V2
V3
L3
L2
L1
L3
L2
L1
N
V1
V2
V3
N
L3
L2
L1
WARNING
Risk of injury due to high currents and high
electrical voltages!
Severe bodily injury or death can result from:
· Touching bare or stripped leads that are ener-
gized.
· Device inputs that pose a hazard when touched.
Therefore, please note for your system:
·
Disconnect the supply of power before start-
ing work!
·
Secure it against being switched on!
·
Check to be sure it is de-energized!
·
Ground and short circuit! Use the ground
connection points with the ground symbol for
grounding!
·
Cover or block off adjacent live parts!
WARNING
Of electrical currents and voltages!
Current transformers operated while exposed on
the secondary side (high voltage peaks) can result
in severe bodily injury or death.
Avoid exposed operation of current transform-
ers and short circuit unloaded transformers!
Operation and button functions
The device is operated via 6 function buttons for
• Selecting measuring displays.
• Navigation within the menus.
• Device configuration.
Function buttons
Fig. UMG 801 standard display - measured values
Display for measured values
and device configuration
After restoration of network power, the device
starts with the measured value display
Home
.
Pressing function button 1
(ESC)
displays the
Menu. (See user manual for description).
Ethernet connection configuration
After restoration of network power, the device
starts with the default display
Home
.
· Press function button 1
ESC
to open the menu.
· Use buttons 2 “
5
” and 5 “
6
” to select the
menu item
Configuration
and confirm with
button 3
Enter
.
· The
Configuration
window appears with the
items
Ethernet Config. A
and
Ethernet
Config. B
.
Configuring current transformers
Communication via OPC UA
1. Press function button 1
ESC
,
to open the menu.
2. Use buttons 2 “
5
” and 5 “
6
” to select the menu
item
Configuration
and confirm with button 3
Enter
.
3. In the
Configuration
window, use buttons 2 “
5
”
and 5 “
6
” to select the menu item
Current trans-
formers
and confirm with button 3
Enter
.
4. The
Current transformers
window appears.
5. In the
Current transformers
window, choose the
item
Basic device
and confirm with button 3
Enter
.
6. The item
Basic device
appears marked in "blue."
In the item
Basic device
, choose between basic
device and up to 10 current measuring modules.
7. Confirm the
Basic device
item with button 3
Enter
.
8. Use button 5 "
6
" to go to the setting for the
Primary side of current transformers 1..4
(current
measurement inputs I1..I4) and press button 3,
Enter
.
9. The item for the primary side of the current
transformers I1..I4 “blinks”.
10. Use buttons 4 (
) and 6 (
) to change the posi-
tion of the digit to be set and buttons 2 (
5
) and
5 (
6
) to change the digit (-1/+1).
11. Confirm your entries with button 3
Enter
or end
the action by pressing button 1
ESC
.
12. Use button 6 (
) to go to the configuration of
the secondary side of the current transformers
I1..I4.
13. Configure the secondary side of the current
transformers I1..I4 in the same way.
14. Confirm your entries with button 3
Enter
or end
the action by pressing button 1
ESC
.
15. When you have finished entering data, press
button 1
ESC
to return to the
Menu
window.
Configure the
current transformer 5..8 (I5..I8)
in
accordance with the current transformer ratios
I1..I4!
Multifunction channels (RCM/Temperature)
0..30 mA
Connection example of multifunction channels for
residual current and temperature measurement
7
8
9 10
2x PT100
11 12
L1
N
PE
L3
L2
Load
13 14
The multifunction channels on the UMG 801 offer the
function options
Residual current measurement
(RCM)
and
Temperature measurement.
The resid-
ual current measurement and temperature measure-
ment share the 4 channels (4 each, 2/2, 3/1 or 1/3).
Multifunction channels for
residual current measurement (RCM)
The UMG 801 with its multifunction channels is
suitable, among other things, for use as a residual
current monitoring device (RCM) for monitoring:
· Alternating current
· Direct current and
· Pulsating direct current.
The UMG 801 measures residual currents according
to IEC/TR 60755 of:
Type A
Type B and B+
(via corresponding current transformers)
WARNING
Hazard due to disregard of warning notices and
safety information!
Disregard of warning notices and safety informa-
tion on the device itself and in the usage informa-
tion for the device and its components can lead to
injuries or even death!
Observe the safety information and warning notic-
es on the device itself and in the usage information
associated with the devices and their components,
such as:
· Installation manual.
· User manual.
· Supplement Safety Information.
Communication via TCP/IP
Considering the Ethernet communication settings (step 10),
the measurement device has 2 types of address assign-
ment for the Ethernet interfaces (TCP/IP) in the
DHCP
mode:
1.
Static (fixed IP address)
The user selects the IP address, netmask and gateway
on the measurement device. Use this mode for simple
networks with no DHCP server.
2.
DHCP
At startup, the measurement device automatically
receives an IP address, netmask and gateway from the
DHCP server.
The default settings of the measurement device for Eth-
ernet interfaces A and B is DHCP!
Connection variants for current measurement
Three-phase 4-conductor system
Current measurement via
3 current transformers in a three-phase
4-conductor system.
Current measurement via
2 current transformers in systems with
the same load.
Current measurement I1 to I4 and I5 to I8
N
L3
L2
L1
N
L3
L2
L1
L3
L2
L1
L2
L1
I
1
30
31
I
1
30
31
I
2
32
33
I
3
34
35
I
4
36
37
N
L3
L2
L1
I
1
30
31
I
2
32
33
I
3
34
35
I
4
36
37
I
2
32
33
I
3
34
35
I
4
36
37
I
1
30
31
I
2
32
33
I
3
34
35
I
4
36
37
I
1
30
31
I
2
32
33
I
3
34
35
I
4
36
37
L3
L2
L1
I
1
30
31
I
2
32
33
I
3
34
35
I
4
36
37
Three-phase 3-conductor system
Current measurement via 2 current
transformers (Aron circuit) in a three-
phase 3-conductor system
Current measurement via 3 current
transformers in a three-phase 3-con-
ductor system
N
L3
L2
L1
N
L3
L2
L1
L3
L2
L1
L2
L1
I
1
30
31
I
1
30
31
I
2
32
33
I
3
34
35
I
4
36
37
N
L3
L2
L1
I
1
30
31
I
2
32
33
I
3
34
35
I
4
36
37
I
2
32
33
I
3
34
35
I
4
36
37
I
1
30
31
I
2
32
33
I
3
34
35
I
4
36
37
I
1
30
31
I
2
32
33
I
3
34
35
I
4
36
37
L3
L2
L1
I
1
30
31
I
2
32
33
I
3
34
35
I
4
36
37
The device is a multifunctional network analyzer
that,
• Measures and calculates electrical quantities
such as voltage, current, frequency, power,
work, harmonics current, etc. in building instal-
lations, at distribution boards, circuit breakers
and busbar trunking systems.
• Displays and stores measurement results and
transmits them via interfaces.
Brief device description and installation
ATTENTION
Material damage due to disregard of the instal-
lation instructions!
Disregard of the installation instructions can dam-
age or destroy your device.
·
Provide adequate air circulation in your instal-
lation environment and cooling, as needed,
when the ambient temperatures are high.
·
More information on device functions, data
and installation as well as the battery used in
the device can be found in the user manual.
Mount the measurement device in a switchboard
cabinet or small distribution board according
to DIN 43880 (any mounting orientation) on a
35 mm (1.38 in) DIN rail (for type, see Technical
Data) as follows:
1. Plug the bus connector included in the scope
of delivery into the sockets on the bottom of the
measurement device.
2. Push your measurement device with the bus
connector sideways onto the DIN rail or press it
frontally onto the DIN rail until the bottom bolt
engages.
Fig. Device with bus connector on DIN rail
Bus connector
DIN rail
Bottom bolt
2.
1.
INFORMATION
Indicates procedures in which there is
no
hazard of
personal injury or material damage.
Recommendation:
Use the GridVis
®
software to configure the trans-
former ratios for residual current transformers.
0..30 mA
Safety information in the installation manual is
marked by a warning triangle and, in dependence
on the degree of hazard, is displayed as follows:
WARNING
Warns of a potentially hazardous situation which, if
not avoided, could result in serious injury or death.
The data transfer using the OPC UA protocol
takes place via the Ethernet interfaces of your
device.
The Ethernet interface and the data transfer using
the OPC UA protocol can be configured conve-
niently in the GridVis
®
software.
Fig. Configuration menu item
Fig. Configuration window
Fig. Configuration window with the
entries Ethernet Config. A and B
(in Dedicated mode).
Fig. Ethernet (TCP/IP) window
Fig. Current transformer window
N
L3
L2
L1
N
V1
V2
V3
N
V1
V2
V3
N
V1
V2
V3
N
V1
V2
V3
N
V1
V2
V3
N
L3
L2
L1
N
V1
V2
V3
N
L3
L2
L1
L2
L1
L3
L2
L1
N
V1
V2
V3
L3
L2
L1
L3
L2
L1
N
V1
V2
V3
N
L3
L2
L1
N
L3
L2
L1
N
L3
L2
L1
L3
L2
L1
L2
L1
I
1
30
31
I
1
30
31
I
2
32
33
I
3
34
35
I
4
36
37
N
L3
L2
L1
I
1
30
31
I
2
32
33
I
3
34
35
I
4
36
37
I
2
32
33
I
3
34
35
I
4
36
37
I
1
30
31
I
2
32
33
I
3
34
35
I
4
36
37
I
1
30
31
I
2
32
33
I
3
34
35
I
4
36
37
L3
L2
L1
I
1
30
31
I
2
32
33
I
3
34
35
I
4
36
37
N
L3
L2
L1
N
L3
L2
L1
L3
L2
L1
L2
L1
I
1
30
31
I
1
30
31
I
2
32
33
I
3
34
35
I
4
36
37
N
L3
L2
L1
I
1
30
31
I
2
32
33
I
3
34
35
I
4
36
37
I
2
32
33
I
3
34
35
I
4
36
37
I
1
30
31
I
2
32
33
I
3
34
35
I
4
36
37
I
1
30
31
I
2
32
33
I
3
34
35
I
4
36
37
L3
L2
L1
I
1
30
31
I
2
32
33
I
3
34
35
I
4
36
37
N
L3
L2
L1
N
V1
V2
V3
N
V1
V2
V3
N
V1
V2
V3
N
V1
V2
V3
N
V1
V2
V3
N
L3
L2
L1
N
V1
V2
V3
N
L3
L2
L1
L2
L1
L3
L2
L1
N
V1
V2
V3
L3
L2
L1
L3
L2
L1
N
V1
V2
V3
N
L3
L2
L1
Connection capacity of the terminals (supply voltage)
Connectible conductors.
Only connect one conductor per terminal point!
Single core, multi-core,
fine-stranded
0.2 - 2.5 mm
2
, AWG 26-12
Wire ferrules (non-insulated)
· Recommended strip length
0.2 - 2.5 mm
2
, AWG 26-12
· 10 mm (0.3937 in)
Wire ferrules (insulated) *
· Recommended strip length **
0.2 - 2.5 mm
2
, AWG 26-12
· 12 mm
(≤1.5 mm
2
), 10 mm
(>1.5 mm
2
) /
0.47 in
(≤1.5 mm
2
), 0.39 in
(>1.5 mm
2
)
Wire ferrules:
Contact sleeve length **
8 - 12 mm (0.31 - 0.47 in)
*
... Applies to wire ferrules with a maximum plastic collar outer
diameter of up to 4.5 mm (0.18 in).
**
.. Depending on the type of wire ferrules used (ferrule
manufacturer).
Connection capacity of the terminals
(digital inputs/outputs, analog output)
Single core, multi-core,
fine-stranded
0.2 - 1.5 mm
2
, AWG 24-16
Wire ferrules (non-insulated)
0.2 - 1.5 mm
2
, AWG 26-16
Wire ferrules (insulated)
0.2 - 1 mm
2
, AWG 26-18
Tightening torque
0.2 - 0.25 Nm (1.77 - 2.21 lbf in)
Strip length
7 mm (0.2756 in)
Connection capacity of the terminals (current measure-
ment)
Connectible conductors.
Only connect one conductor per terminal point!
Single core, multi-core,
fine-stranded
0.2 - 2.5 mm
2
, AWG 26-12
Wire ferrules (non-insulated)
· Recommended strip length
0.2 - 2.5 mm
2
, AWG 26-12
· 10 mm (0.3937 in)
Wire ferrules (insulated) *
· Recommended strip length **
0.2 - 2.5 mm
2
, AWG 26-12
· 12 mm
(≤1.5 mm
2
), 10 mm
(>1.5 mm
2
) /
0.47 in (≤1.5 mm
2
), 0.39 in
(>1.5 mm
2
)
Wire ferrules:
Contact sleeve length **
8 - 12 mm (0.31 - 0.47 in)
Tightening torque
Screw flange
0.2 Nm (1.77 lbf in)
*
... Applies to wire ferrules with a maximum plastic collar outer
diameter of up to 4.5 mm (0.18 in).
**
.. Depending on the type of wire ferrules used (ferrule
manufacturer).
Connection capacity of the terminals (RS-485)
Single core, multi-core,
fine-stranded
0.2 - 1.5 mm
2
, AWG 24-16
Wire ferrules (non-insulated)
0.2 - 1.5 mm
2
, AWG 26-16
Wire ferrules (insulated)
0.2 - 1 mm
2
, AWG 26-18
Tightening torque
0.2 - 0.25 Nm (1.77 - 2.21 lbf in)
Strip length
7 mm (0.2756 in)
Connection capacity of the terminals
(voltage measurement)
Connectible conductors
Only connect one conductor per terminal point!
Single core, multi-core,
fine-stranded
0.08 - 4 mm
2
, AWG 28-12
Wire ferrules
(insulated/non-insulated)
0.25 - 2.5 mm
2
, AWG 24-14
Strip length
8-9 mm (0.3150 - 0.3543 in)
Connection capacity of the terminals -
Multifunction channels (RCM, Temp.)
Connectible conductors.
Only connect one conductor per terminal point!
Single core, multi-core,
fine-stranded
0.2 - 1.5 mm
2
, AWG 24-16
Wire ferrules (non-insulated)
0.2 - 1.5 mm
2
, AWG 26-16
Wire ferrules (insulated)
0.2 - 1 mm
2
, AWG 26-18
Tightening torque
0.2 - 0.25 Nm (1.77 - 2.21 lbf in)
Strip length
7 mm (0.2756 in)
Connection capacity of the terminals (functional earth A/D)
Connectible conductors.
Only connect one conductor per terminal point!
Single core, multi-core,
fine-stranded
0.2 - 4 mm
2
, AWG 24-12
Wire ferrules (non-insulated)
0.2 - 4 mm
2
, AWG 24-12
Wire ferrules (insulated)
0.2 - 2.5 mm
2
, AWG 26-14
Tightening torque
0.4 - 0.5 Nm (3.54 - 4.43 lbf in)
Strip length
7 mm (0.2756 in)
Configure the Ethernet (TCP/IP) settings using the function
buttons as described in step 12 "Operation and button
functions".
Residual current measurement (RCM)
Overload for 1 s
5 A
Permanent overload
1 A
Norm
IEC/TR 60755 (2008-01),
Type A / Type B and B+ (via corre-
sponding current transformers)
Technical data
General
Net weight
420 g (0.926 lb)
Device dimensions
Approx. B = 144 mm (5.67 in), H =
90 mm (3.54 in),
D = 76 mm (2.99 in)
Battery
Type: Lithium CR2032, 3 V
(UL1642 approval)
Integrated memory
4 GB
Backlight service life
40000 h
(50% of the start brightness)
Mounting orientation
As desired
Fastening/mounting -
Suitable DIN rails - 35 mm
(1.38 in)
· TS 35/7.5 according to EN 60715
· TS 35/10
· TS 35/15 x 1.5
Impact resistance
IK07 according to IEC 62262
Transport and storage
The following specifications apply for devices transported and
stored in the original packaging.
Free fall
1 m (39.37 in)
Temperature
-25 °C (-13 °F) to +70 °C (158 °F)
Relative humidity
5 to 95% at 25 °C (77 °F),
no condensation
Environmental conditions during operation
The device:
• Is for weather-protected and stationary use.
• Fulfills operating conditions according to DIN IEC 60721-3-3.
• Has protection class II according to IEC 60536 (VDE 0106,
part 1),
a ground wire connection is not required!
Rated temperature range
-10 °C (14 °F) to +55 °C (131 °F)
Relative humidity
5 to 95% at 25 °C (77 °F),
no condensation
Operating elevation
(for overvoltage categories,
see voltage and current
measurement)
2000 m (6562 ft) above sea level
4000 m (13,124 ft) above sea level
Pollution degree
2
Ventilation
No forced ventilation required.
Protection against foreign
matter and water
IP20 according to EN60529
Supply voltage
Nominal range
DC: 24 V, PELV
Operating range
+/-10% of nominal range
Power consumption
max. 4 W
Maximum power
consumption with 10
modules
12 W (UMG 801 at 4 W plus
10 modules at 0.8 W each)
Recommended overcurrent
protective device for line
protection
2-6 A, (Char. B), IEC/UL approval
19
Configuring voltage transformers
17
1. Press function button 1
ESC
to open
the menu.
2. Use buttons 2 “
5
” and 5 “
6
” to select the
menu item
Configuration
and confirm with
button 3
Enter
.
3. In the
Configuration
window, use buttons 2
“
5
” and 5 “
6
” to select the item
Voltage
transformer
and confirm with button 3
Enter
.
4. The
voltage transformer
window appears.
5. In the
Voltage transformer
window, select the
item
Transformer 1..4
(voltage measurement
inputs L1 to L4) and press button 3,
Enter
.
6. The item for the primary side of the transform-
er 1..4 “blinks”.
7. Use buttons 4 (
) and 6 (
) to change the
position of the digit to be set and buttons 2
(
5
) and 5 (
6
) to change the digit (-1/+1).
8. Confirm your entries with button 3
Enter
or
end the action by pressing button 1
ESC
.
9. Use button 6 (
) to go to the configuration
of the secondary side of the transformer 1..4
(voltage measurement inputs L1 to L4).
10. Configure the secondary side of voltage trans-
formers 1..4 in the same way.
11. Confirm your entries with button 3
Enter
or end
the action by pressing button 1
ESC
.
12. When you have finished entering data, press
button 1
ESC
to return to the
Menu
window.
Fig. Voltage transformer window
ATTENTION
Faulty cross currents, incorrect measure-
ments, and even damage to the device and/or
your system due to lack of galvanic isolation!
A lack of galvanic isolation of active external cur-
rent transformers (or other current sensors) on the
multifunction channels from the supply voltage
of the device can lead to faulty cross currents,
incorrect measurements or even damage to your
device and/or system.
· Do
not
take the auxiliary voltage supply of
active external current transformers (or other
current sensors) on the multifunction channels
from the supply voltage of the device! For each
active current transformer, use galvanically
isolated power supplies (secondary side).
· Do
not
ground passive current transformers on
the multifunction channels! Observe the usage
information of the current transformer manu-
facturer.
N
L3
L2
L1
N
V1
V2
V3
N
V1
V2
V3
N
V1
V2
V3
N
V1
V2
V3
N
V1
V2
V3
N
L3
L2
L1
N
V1
V2
V3
N
L3
L2
L1
L2
L1
L3
L2
L1
N
V1
V2
V3
L3
L2
L1
L3
L2
L1
N
V1
V2
V3
N
L3
L2
L1
N
L3
L2
L1
N
V1
V2
V3
N
V1
V2
V3
N
V1
V2
V3
N
V1
V2
V3
N
V1
V2
V3
N
L3
L2
L1
N
V1
V2
V3
N
L3
L2
L1
L2
L1
L3
L2
L1
N
V1
V2
V3
L3
L2
L1
L3
L2
L1
N
V1
V2
V3
N
L3
L2
L1
Three-phase 4-conductor systems
with grounded neutral conductor
Three-phase 4-conductor
systems
with non-grounded neutral conduc-
tor (IT networks)
Three-phase 3-conductor
systems
ungrounded
Three-phase 3-conductor
systems
with grounded phase
L1
L2
L3
E
E
N
E
L1
L2
L3
E
N
R
L1
L2
L3
E
E
L1
L2
E
E
L
N
E
E
L1
L2
L3
E
E
L1
L2
N
E
E
L1
L2
L3
E
E
N
E
L1
L2
L3
E
N
R
L1
L2
L3
E
E
L1
L2
E
E
L
N
E
E
L1
L2
L3
E
E
L1
L2
N
E
E
L1
L2
L3
E
E
N
E
L1
L2
L3
E
N
R
L1
L2
L3
E
E
L1
L2
E
E
L
N
E
E
L1
L2
L3
E
E
L1
L2
N
E
E
L1
L2
L3
E
E
N
E
L1
L2
L3
E
N
R
L1
L2
L3
E
E
L1
L2
E
E
L
N
E
E
L1
L2
L3
E
E
L1
L2
N
E
E
IEC
UL-N / UL-L: 480 VLN / 830 VLL
UL-L: 690 VLL
UL-L: 830 VLL
UL
UL-N / UL-L: 347 VLN / 600 VLL
UL-L: 600 VLL
UL-L: 600 VLL
Functional earth
INFORMATION
The functional earthing is a functional part and essential
for the regular operation of the electrical system.
INFORMATION
For a PE/N measurement, connect measuring
input A as the functional earth. Do not use a
green-yellow wire for this, as the conductor has
no protective function!
INFORMATION
Before you start with the DIN rail mounting and
cabling of your UMG 801, make sure that the
bus connector is mounted on the bottom of your
UMG 801. Then connect up to 10 modules via bus
connectors.
INFORMATION
Functional earth
·
Connection D
(UMG 801) in TN, TT and IT net-
works must always be connected.
·
Connection A
(UMG 801) only connect in TN and
TT networks (
not in IT networks
)
INFORMATION
· The meter does not have a password (00000000)
ex works.
· For detailed information on configuring a pass-
word, operation, display and button functions of
your device, refer to the user manual.
INFORMATION
Detailed information on all menu items and their
settings can be found in the user manual.
INFORMATION
· The multifunction channels are suitable for con-
necting residual current transformers with a nom-
inal current of up to 30 mA and have the "Current
transformer connection test" function.
· The residual current measurement monitors the
residual currents via external current transformers
and, if a threshold value is exceeded, can trigger
a warning signal. The meter is not an independent
protective device against electric shock!
INFORMATION
Voltage transformer ratios can also be configured in
the device configuration of the GridVis
®
software.
INFORMATION
Optionally configure the current transformer ratios
· in the device configuration of the GridVis
®
software.
· via the measurement device homepage of the basic
device.
INFORMATION
· Consult your network administrator for the correct
Ethernet network settings for your device.
· Descriptions of the communication interfaces can
be found in the user manual.
· Information on the connection and communication
of your device with the software can be found in
the online help for the GridVis
®
software.
INFORMATION
· Consult your network administrator for the correct Ethernet
network settings for your measurement device.
· Descriptions of the communication interfaces can be found
in the user manual.
· Information on the connection and communication of your
measurement device with the software can be found in the
online help for the GridVis
®
software.
Patch cable
Your measurement device has two Ethernet
interfaces (A and B) for communication in Ether-
net networks. There are 2 options to integrate the
measurement device into Ethernet networks:
1.
Measurement device integration in a network
with additional switch function (switched
mode).
The measurement device is automatical-
ly assigned an IP address by a DHCP server in
an IT network via Ethernet interface A, for exam-
ple. Ethernet interface B has a switch function
via which further devices (hardware components)
can be connected in series. The measurement
device also allows the reverse use of the Ether-
net interfaces (e.g. "B" for the IP address from a
network and "A" for further devices)!
2.
Measurement device integration in 2 different
networks (dedicated mode)
.
The Ethernet interfaces A and B of the mea-
surement device are each assigned different IP
addresses by 2 different networks.
Button Function
· Display menu.
· One step back.
· Cancel action
(ESC)
.
· Repeated actuation leads to the menu.
· Select menu item or position
(up, "
5
").
· Change selection (digit +1).
· Confirm selection
(Enter)
· Select position (to the left, "
").
· Select menu item or position
(down, "
6
").
· Change selection (digit -1).
· Select position (to the right “
”).
Ethernet A
Ethernet B
Recommendation:
Use at least CAT5 cable!
Patch cable
INFORMATION
For configuration of the IP addresses on the measure-
ment device, observe step 13 "Configuring the Ethernet
connection" and step 14 "Communication via TCP/IP".
· In the
Configuration
window, use buttons 2 "
5
"
and 5 "
6
" to select the respective entry of the
Ethernet interface to be configured and confirm
with button 3
Enter
.
· The window for configuring the TCP/IP Ethernet
settings appears (see step 13 "Communication
via TCP/IP").
INFORMATION
Detailed technical data can be found in the user man-
ual for the measurement device at www.janitza.de.
INFORMATION
You can configure current transformer
ratios
conveniently via
· The device menu.
· The GridVis
®
software.
For information on programming the current
transformer ratios, refer to the user manual.
INFORMATION
·
The switched and dedicated modes of the mea-
surement device can be configured in the GridVis
®
software.
·
The default setting of the measurement device is
the switched mode.
·
A mode change only takes effect after a hard reset
(disconnect the measurement device from the sup-
ply voltage while observing the safety regulations)!
ATTENTION
Material damage due to security vulnerabilities in
programs, IT networks and protocols.
Security vulnerabilities can lead to data misuse and
faults and even the standstill of your IT infrastructure.
To protect your IT system, network, data commu-
nications and measurement devices:
·
Inform your network administrator and/or IT
representative.
·
Always keep the meter firmware up to date and
protect the communication to the meter with an
external firewall. Close unused ports.
·
Take protective measures against viruses and
cyber attacks from the Internet, e.g. through
firewall solutions, security updates and virus
protection programs.
·
Eliminate security vulnerabilities and update or
renew existing protection for your IT infrastruc-
ture.
ATTENTION
Material damage due to incorrect network
settings.
Incorrect network settings can cause faults in the IT
network!
Consult your network administrator for the cor-
rect network settings for your device.
Connection of the device with a patch cable (Ethernet interface) via
a switch/router to the OPC UA server and the PC.
PC and device require a fixed IP address.
PC
Patch cable
Patch cable
OPC UA-
Server
PC
Switch/
Router
UMG 801
Patch cable
Patch cable
DHCP
Server
PC
Switch/
Router
The DHCP server automatically assigns IP addresses to device
and PC.
UMG 801
UMG 801
PC connections
The most common connection methods for com-
munication of the measurement device with a PC
(with GridVis
®
software installed) are described
below.
1. Connection to a DHCP server and PC. The
DHCP server automatically assigns IP ad-
dresses to the device and the PC.
2. Connection as master device with an
RS-485 bus structure (Modbus RTU) to a PC
and OPC UA client.
3. PC direct connection to the device. PC and
device require a fixed IP address.
Ethernet
Ethernet
Ethernet
Modbus TCP
Ethernet
Modbus TCP
Patch cable
Ethernet
INFORMATION
With regard to the configuration of the IP addresses
on the measurement device, also observe steps 10
and 12 to 15!
PC
DHCP
Server
UMG 801
Ethernet A
Ethernet B
Switch/
Router
PC
Network A
Dedicated mode: Different IP addresses for Ethernet interfaces A
and B for separate networks.
Network B
DHCP
Server
Switch/
Router
Switched mode: Ethernet interface B of the UMG 801 for con-
necting an Ethernet device. The measurement device also allows
the reverse use of the Ethernet interfaces (A for the Ethernet
device and B for an IP address from a network).
PC
DHCP
Server
Switch/
Router
UMG 801
A
B
e.g.
UMG 96PQ-L
"Switched mode" connection option:
"Dedicated mode" connection option
11
RS-485
(Modbus RTU)
Transformer 1..4
Primary
Secondary
Voltage Transformer
ESC
400 V
400 V
Device
Transformer 1..4
Transformer 5..8
Basic device
Primary
Secondary
Current Transformer
ESC
5 A
5 A
5 A
5 A
Ethernet config. A
Ethernet config. B
Fieldbus
Current Transformer
Voltage Transformer
Configuration
ESC
IP Config.
IP Address
Netmask
Gateway
DHCP
192. 168. 3. 177
192. 168. 3. 4
255. 255. 255. 0
Ethernet (TCP/IP)
ESC
Ethernet config. A
Ethernet config. B
Fieldbus
Current Transformer
Voltage Transformer
Configuration
ESC
Energy
Drag pointer
Multifunctional Channels
Digital I/O Status
Configuration
Menü
General
1
2
Janitza electronics GmbH
Vor dem Polstück 6
D-35633 Lahnau
Support tel. +49 6441 9642-22
Email: [email protected]
www.janitza.de
www
.janitza.de
Doc. no. 2.053.005.4.a 04/2023
Part no. 33.03.376
Power Analyzer
UMG 801
Installation manual
Installation
Device settings
German version:
see r
ear side
2
Safety
Safety information
The installation manual does not represent a
complete set of all safety measures required for
the operation of the device.
Special operating conditions can require addi-
tional measures. The installation manual contains
information which must be observed to ensure
your personal safety and avoid material damage.
Symbols used on the device:
The additional symbol on the de-
vice itself indicates an electrical
danger that can result in serious
injuries or death.
This general warning symbol
draws attention to a possible risk
of injury. Be certain to observe all
of the information listed under this
symbol in order to avoid possible
injury or even death.
Safety measures
When operating electric devices, it is unavoidable
for certain parts of these devices to conduct
hazardous voltage. Consequently, severe bodily
injury or material damage can occur if they are
not handled properly:
• Before making connections to the device,
ground the device by means of the ground
wire connection, if present.
• Hazardous voltages can be present in all
circuitry parts that are connected to the power
supply.
• There can still be hazardous voltages present
in the device even after it has been discon-
nected from the supply voltage (capacitor
storage).
• Do not operate equipment with current trans-
former circuits when open.
• Do not exceed the limit values specified in the
user manual and on the rating plate! This must
also be observed during testing and commis-
sioning!
• Observe the safety information and warning
notices in the usage information associated
with the device and its components!
Qualified personnel
To avoid bodily injury and material damage, only
qualified personnel with electrical training are
permitted to work on the basic device and its
components who have knowledge of:
• The national accident prevention regulations.
• Safety technology standards,
• Installation, commissioning and operation of
the device and the components.
Intended use
The device is:
• Intended only for use in the field of
industrial
controls
.
• Intended for installation in switchboard
cabinets and small distribution boards. The
mounting orientation is arbitrary (Please ob-
serve step 3 "Installation").
• Not intended for installation in vehicles! Use
of the device in non-stationary equipment
constitutes an exceptional environmental
condition and is only permissible by special
agreement.
• Not intended for installation in environments
with harmful oils, acids, gases, vapors, dusts,
radiation, etc.
• Designed as an indoor meter.
Disclaimer
Compliance with the usage information for the
devices is a prerequisite for safe operation and
attaining the stated performance characteristics
and product features. Janitza electronics GmbH
assumes no liability for bodily injury, material
damage or financial losses which result from dis-
regard of the usage information. Ensure that your
informational products are readily accessible in a
legible form.
Further usage information, such as the user man-
ual, can be found on our website www.janitza.de
under Support > Downloads.
Copyright notice
© 2023 - Janitza electronics GmbH - Lahnau.
All rights reserved. Any reproduction, processing,
distribution or other use, in whole or in part, is
prohibited.
Subject to technical alterations.
• Make sure that your device matches the
installation manual.
• First make sure you have read and under-
stood the usage information accompanying
the product.
• Keep the usage information associated with
the product available for the entire service life
and pass it on to any possible subsequent
users.
• Please find out about device revisions and
the associated modifications of the usage
information associated with your product at
www.janitza.de.
Disposal
Please abide by national regulations! Dispose
of individual parts, as applicable, depending on
their composition and existing country-specific
regulations, e.g. as:
• Electronic waste
• Batteries and rechargeable batteries
• Plastics
• Metals
or engage a certified disposal company to handle
scrapping.
Relevant laws,
standards and directive used
Please see the declaration of conformity on our
website (www.janitza.de) for the laws, standards
and directives applied for the device by Janitza
electronics GmbH.
3
Applying the supply voltage
The supply voltage your device requires can be
found on the rating plate. After connecting the
supply voltage, the display becomes active. If
no display appears, check whether the supply
voltage is within the nominal voltage range.
ATTENTION
Material damage due to disregard of the connec-
tion conditions or impermissible overvoltages
Disregard of the connection instructions or exceed-
ing the permissible voltage range can damage or
destroy your device.
Before connecting the device to the supply volt-
age, please note:
· Voltage and frequency must correspond to the
specifications on the rating plate! Observe limit
values as described in the user manual!
· In the building installation, secure the supply volt-
age with a UL/IEC listed line circuit breaker/fuse!
· Observe the following for the isolation device
- Install it close to the device and easily accessi-
ble for the user.
- Mark it for the respective device.
· Do not tap the supply voltage from the voltage
transformers.
· Provide a fuse for the neutral conductor if the
neutral conductor terminal of the source is not
grounded.
Procedure in the event of a malfunction
14
18
9
10
12
13
Ethernet communication
5
Voltage measurement
4
Grid systems
Suitable grid systems and maximum rated voltages (DIN EN 61010-1/A1):
6
Connection variants for voltage measurement
7
Current measurement
8
ATTENTION
Warns of an immediately hazardous situation
which, if not avoided, can result in material or
environmental damage.
Incoming goods inspection
The prerequisites for trouble-free and safe opera-
tion of the devices and their components include
proper transport, storage, setup and assembly,
as well as proper operation and maintenance.
Exercise due caution when unpacking and pack-
ing the device, do not use force and only use
suitable tools.
Check:
• Visually inspect the devices and components
for flawless mechanical condition.
• Check the scope of delivery (see user manual)
for completeness before you begin installing
your devices and components.
If it must be assumed that safe operation is no
longer possible, immediately put the device with
components out of service and secure against
unintentional startup.
It can be assumed that safe operation is no
longer possible, for example, if the device with
components:
• Has visible damage,
• No longer functions despite an intact power
supply.
• Was subjected to extended periods of unfa-
vorable conditions (e.g. storage outside of the
permissible climate thresholds without adjust-
ment to the room climate, condensation, etc.)
or transport stress (e.g. falling from an elevated
position, even without visible external damage,
etc.).
Digital outputs
4 digital outputs, solid state relays, not short-circuit proof.
Switching voltage
Max. 60 V DC
Switching current
max. 50 mAeff DC
Response time
approx. 500 ms
Digital output (energy pulses)
max. 20 Hz
Digital inputs
4 digital inputs, solid state relays, not short-circuit proof.
Maximum counter frequency
20 Hz
Input signal applied
18 V .. 28 V DC
(typical 4 mA)
Input signal not applied
0 .. 5 V DC,
current less than 0.5 mA
Cable length (digital inputs/outputs)
Up to 30 m (32.81 yd)
Unshielded
Greater than 30 m (32.81 yd)
Shielded
User Manual:
15
16
20
Application areas for the device
• 3 and 4-conductor networks (TN, TT and IT
networks).
• Residential and industrial areas.
The device has 4 voltage measurement inputs
and is suitable for various connection variants.
L1
N
PE/FE
L3
L2
Fig. Connection example for “voltage measurement”.
The voltage measurement inputs are designed for
measurements in low-voltage networks in which
nominal voltages occur as described in the
"Technical data".
Fuse
(UL/IEC listed)
Three-phase 4-conductor system
Three-phase 4-conductor sys-
tem without voltage transformer.
Three-phase 4-conductor sys-
tem with voltage transformer.
Three-phase 4-conductor
system (symmetrical load)
Three-phase 4-conductor sys-
tem (asymmetrical load)
Three-phase 3-conductor system
Three-phase 3-conductor sys-
tem (asymmetrical load)
Three-phase 3-conductor sys-
tem with voltage transformer.
Voltage measurement L1, L2, L3 (main measurement)
Voltage measurement
Three-phase 4-conductor
systems with rated volt-
ages up to
480 VLN / 830 VLL (+/-10%) according to IEC
347 VLN / 600 VLL (+/-10%) according to UL
3-phase 3-conductor
systems (grounded) with
rated voltages up to
830 VL-L (+/-10%) according to IEC
600 VL-L (+/-10%) according to UL
3-phase 3-conductor sys-
tems (non-grounded) with
rated voltages up to
690 VL-L (+/-10%) according to IEC
600 VL-L (+/-10%) according to UL
Overvoltage category up
to 2000 m
up to 4000 m
· 1000 V CAT III according to IEC
· 600 V CAT III according to UL
· 600 V CAT IV
according to IEC
· 600 V CAT III according to IEC
Rated surge voltage
8 kV
Protection of the voltage
measurement
1 - 10 A tripping characteristic B(with IEC/
UL approval)
Measuring range L-N
0
1)
.. 720 Veff
(max. overvoltage 1000 Veff)
Measuring range L-L
0
1)
.. 1000 Veff
(max. overvoltage 1000 Veff)
Measuring range N-PE
up to 100 V
Resolution
16 bit
Crest factor
1.6 (referred to measuring range 600 V L-N)
Impedance
4 MΩ/phase
Power consumption
approx. 0.1 VA
Sampling frequency
51.2 kHz
Frequency of
fundamental oscillation
- Resolution
40 Hz .. 70 Hz
0.01 Hz
Harmonics
1 .. 127.
1) ... The meter only measures if at least one voltage measurement
input has an L-N voltage of > 10 Veff
or an L-L voltage of > 18 Veff present.
Current measurement (../1A) (../5A)
Nominal current
5 A
Channels
8
· 2 systems (L1, L2, L3, N)
· Single channels
Measuring range
0.005 .. 6 Aeff
Crest factor
(relative to nominal current)
1.98
Overload for 1 s
120 A (sinusoidal)
Resolution
0.1 mA (color graphic display 0.01 A)
Overvoltage category
300 V CAT II
Rated surge voltage
2.5 kV
Power consumption
approx. 0.2 VA (Ri = 5 m
Ω
)
Sampling frequency
25.6 kHz
Harmonics
1 .. 63.
Residual current measurement (RCM)
Nominal current
30 mAeff
Measuring range
0 .. 40 mAeff
Operating current
50 µA
Resolution
1 µA (color graphic display 0.01 A)
Crest factor
1.414 (relative to 40 mA)
Load
4
Ω
Overload for 20 ms
50 A
The measurement device has 4 optional multifunction channels, for use as
· residual current measurement inputs and/or temperature measure-
ment inputs (mixed),
· Additional system inputs (L1, L2, L3; N)
Temperature measurement
Update time
1 s
Total load
(sensor and cable)
max. 4 k
Ω
Cable
<= 30 m (32.81 yd) not shielded
> 30 m (32.81 yd) shielded
Suitable sensor types
KTY83, KTY84, PT100, PT1000
Analog outputs
1 channel
External power supply
max. 33 V DC
Current
0/4...20 mA DC
Update time
0.2 s
Load
max. 300
Ω
Resolution
10 bit
RS-485 interface
3-wire connection with A, B, GND.
See user manual for recommended cable types.
Protocol
Modbus RTU/Slave
Modbus RTU/Gateway
Transmission rate
9.6 kbps, 19.2 kbps, 38.4 kbps,
57.6 kbps, 115.2 kbps
Termination
DIP switches
Ethernet interfaces
Connection
2 x RJ45 (can be used sep-
arately)
Function
Modbus gateway
Protocols and services
OPC UA, DHCP, Modbus/TCP,
NTP, HTTP(S), FTP(S)
Time synchronization
NTP
Potential isolation and electrical safety of the interfaces
The interfaces (RS-485, Ethernet) have:
• Double insulation to the inputs of the voltage and current
measurement.
• Functional insulation relative to each other, to the supply
voltage, to the measuring inputs for residual current and tem-
perature, to the digital inputs/outputs and to the analog output.
The interfaces of the connected devices require double or
reinforced insulation against mains voltages (according to IEC
61010-1: 2010).
Potential isolation and electrical safety of the
multifunction channels (RCM, Temp.)
The inputs of the multifunction channels have:
• Double insulation to the inputs of the voltage and current
measurement.
• No insulation to each other or to the supply voltage.
• Functional isolation to the Ethernet, RS-485 interfaces, to the
digital inputs/outputs and to the analog output.
External sensors and/or transformers require double insulation
relative to system components with dangerous touch voltages
(according to IEC61010-1:2010).
Potential isolation and electrical safety of the
digital inputs and outputs (I/Os) and the analog output
The digital inputs and outputs as well as the analog output are
equipped with:
• Double insulation to the inputs of the voltage and current
measurement.
• Functional isolation relative to each other, to the supply
voltage, to the Ethernet, RS-485 and multifunction channel
interfaces.
Failure mode
Cause
Remedy
No display
External fuse for the supply voltage has tripped.
Replace fuse.
No current display.
No measured voltage connected.
Connect measured voltage.
No measured current connected.
Connect measured current.
Displayed current is
too great or too small.
Current measurement on the wrong phase.
Check connection and correct if necessary.
Current transformer factor incorrectly programmed.
Read and program the current transformer ratio on
the current transformer.
Current harmonic exceeds current peak value at
measuring input.
Install current transformers with a higher current
transformer ratio.
The current at the measuring input is too low.
Install current transformers with a lower current
transformer ratio.
Displayed voltage is
too high or too low.
Measurement on the wrong phase.
Check connection and correct if necessary.
Voltage transformer programmed incorrectly.
Read the voltage transformer ratio on the voltage
transformer and program.
Displayed voltage
is too low.
Overrange.
Use a voltage transformer.
The voltage peak value at the measuring input was
exceeded due to harmonics current.
Attention!
Make sure that the measuring inputs are
not overloaded.
Despite the above measures,
the device does not function.
Device defective.
Send the device and error description to the manu-
facturer for inspection.
230 VAC
24 VDC
+
-
PELV
(grounded low voltage)
Load
Isolation device
Fig. Connection example for “current measurement”.
L1
N
PE
L3
L2
Load
S1 S2
S1 S2
S1 S2
S1 S2
The device:
· Measures current exclusively via current trans-
formers.
· Allows the connection of current transformers
with a transformer ratio of ../1 A and ../5 A.
· Has a current transformer ratio of 5/5 A (I1 to I8)
as the default setting.
· Does not measure DC currents.
The current transformers require basic insulation
according to IEC 61010-1:2010 for the nominal
voltage of the circuit.
WARNING
Risk of injury due to electric voltage or electric
current!
When handling electric currents or voltages, serious
bodily injury or death can result from:
· Touching bare or stripped leads that are ener-
gized.
· Device inputs that pose a hazard when touched.
Before starting work on your system:
·
Disconnect the supply of power!
·
Secure it against being switched on!
·
Check to be sure it is de-energized!
·
Ground and short circuit!
·
Cover or block off adjacent live parts!
L1
N
WARNING
Risk of injury or damage to the device due to
electrical voltage and improper connection!
Failure to comply with the connection conditions for
the voltage measurement inputs can result in dam-
age to the device or serious injury, including death.
Therefore, please observe the following:
·
Switch off your installation before commenc-
ing work! Secure it against being switched on!
Check to be sure it is de-energized! Ground
and short circuit! Cover or block off adjacent
live parts!
·
Do not apply a DC voltage
-
to the voltage measurement inputs.
-
Equip the voltage measurement inputs with
a suitable, marked fuse and isolation device
(alternatively: line circuit breaker) located
nearby.
-
The voltage measurement inputs are dan-
gerous to touch.
·
Connect voltages that exceed the permissi-
ble nominal network voltages via a voltage
transformer.
·
Measured voltages and currents must origi-
nate from the same network.
DANGER
Warns of an imminent danger which, if not avoided,
results in serious or fatal injury.
CAUTION
Warns of an immediately hazardous situation which,
if not avoided, can result in minor or moderate
injury.
N
L3
L2
L1
N
V1
V2
V3
N
V1
V2
V3
N
V1
V2
V3
N
V1
V2
V3
N
V1
V2
V3
N
L3
L2
L1
N
V1
V2
V3
N
L3
L2
L1
L2
L1
L3
L2
L1
N
V1
V2
V3
L3
L2
L1
L3
L2
L1
N
V1
V2
V3
N
L3
L2
L1
N
L3
L2
L1
N
V1
V2
V3
N
V1
V2
V3
N
V1
V2
V3
N
V1
V2
V3
N
V1
V2
V3
N
L3
L2
L1
N
V1
V2
V3
N
L3
L2
L1
L2
L1
L3
L2
L1
N
V1
V2
V3
L3
L2
L1
L3
L2
L1
N
V1
V2
V3
N
L3
L2
L1
WARNING
Risk of injury due to high currents and high
electrical voltages!
Severe bodily injury or death can result from:
· Touching bare or stripped leads that are ener-
gized.
· Device inputs that pose a hazard when touched.
Therefore, please note for your system:
·
Disconnect the supply of power before start-
ing work!
·
Secure it against being switched on!
·
Check to be sure it is de-energized!
·
Ground and short circuit! Use the ground
connection points with the ground symbol for
grounding!
·
Cover or block off adjacent live parts!
WARNING
Of electrical currents and voltages!
Current transformers operated while exposed on
the secondary side (high voltage peaks) can result
in severe bodily injury or death.
Avoid exposed operation of current transform-
ers and short circuit unloaded transformers!
Operation and button functions
The device is operated via 6 function buttons for
• Selecting measuring displays.
• Navigation within the menus.
• Device configuration.
Function buttons
Fig. UMG 801 standard display - measured values
Display for measured values
and device configuration
After restoration of network power, the device
starts with the measured value display
Home
.
Pressing function button 1
(ESC)
displays the
Menu. (See user manual for description).
Ethernet connection configuration
After restoration of network power, the device
starts with the default display
Home
.
· Press function button 1
ESC
to open the menu.
· Use buttons 2 “
5
” and 5 “
6
” to select the
menu item
Configuration
and confirm with
button 3
Enter
.
· The
Configuration
window appears with the
items
Ethernet Config. A
and
Ethernet
Config. B
.
Configuring current transformers
Communication via OPC UA
1. Press function button 1
ESC
,
to open the menu.
2. Use buttons 2 “
5
” and 5 “
6
” to select the menu
item
Configuration
and confirm with button 3
Enter
.
3. In the
Configuration
window, use buttons 2 “
5
”
and 5 “
6
” to select the menu item
Current trans-
formers
and confirm with button 3
Enter
.
4. The
Current transformers
window appears.
5. In the
Current transformers
window, choose the
item
Basic device
and confirm with button 3
Enter
.
6. The item
Basic device
appears marked in "blue."
In the item
Basic device
, choose between basic
device and up to 10 current measuring modules.
7. Confirm the
Basic device
item with button 3
Enter
.
8. Use button 5 "
6
" to go to the setting for the
Primary side of current transformers 1..4
(current
measurement inputs I1..I4) and press button 3,
Enter
.
9. The item for the primary side of the current
transformers I1..I4 “blinks”.
10. Use buttons 4 (
) and 6 (
) to change the posi-
tion of the digit to be set and buttons 2 (
5
) and
5 (
6
) to change the digit (-1/+1).
11. Confirm your entries with button 3
Enter
or end
the action by pressing button 1
ESC
.
12. Use button 6 (
) to go to the configuration of
the secondary side of the current transformers
I1..I4.
13. Configure the secondary side of the current
transformers I1..I4 in the same way.
14. Confirm your entries with button 3
Enter
or end
the action by pressing button 1
ESC
.
15. When you have finished entering data, press
button 1
ESC
to return to the
Menu
window.
Configure the
current transformer 5..8 (I5..I8)
in
accordance with the current transformer ratios
I1..I4!
Multifunction channels (RCM/Temperature)
0..30 mA
Connection example of multifunction channels for
residual current and temperature measurement
7
8
9 10
2x PT100
11 12
L1
N
PE
L3
L2
Load
13 14
The multifunction channels on the UMG 801 offer the
function options
Residual current measurement
(RCM)
and
Temperature measurement.
The resid-
ual current measurement and temperature measure-
ment share the 4 channels (4 each, 2/2, 3/1 or 1/3).
Multifunction channels for
residual current measurement (RCM)
The UMG 801 with its multifunction channels is
suitable, among other things, for use as a residual
current monitoring device (RCM) for monitoring:
· Alternating current
· Direct current and
· Pulsating direct current.
The UMG 801 measures residual currents according
to IEC/TR 60755 of:
Type A
Type B and B+
(via corresponding current transformers)
WARNING
Hazard due to disregard of warning notices and
safety information!
Disregard of warning notices and safety informa-
tion on the device itself and in the usage informa-
tion for the device and its components can lead to
injuries or even death!
Observe the safety information and warning notic-
es on the device itself and in the usage information
associated with the devices and their components,
such as:
· Installation manual.
· User manual.
· Supplement Safety Information.
Communication via TCP/IP
Considering the Ethernet communication settings (step 10),
the measurement device has 2 types of address assign-
ment for the Ethernet interfaces (TCP/IP) in the
DHCP
mode:
1.
Static (fixed IP address)
The user selects the IP address, netmask and gateway
on the measurement device. Use this mode for simple
networks with no DHCP server.
2.
DHCP
At startup, the measurement device automatically
receives an IP address, netmask and gateway from the
DHCP server.
The default settings of the measurement device for Eth-
ernet interfaces A and B is DHCP!
Connection variants for current measurement
Three-phase 4-conductor system
Current measurement via
3 current transformers in a three-phase
4-conductor system.
Current measurement via
2 current transformers in systems with
the same load.
Current measurement I1 to I4 and I5 to I8
N
L3
L2
L1
N
L3
L2
L1
L3
L2
L1
L2
L1
I
1
30
31
I
1
30
31
I
2
32
33
I
3
34
35
I
4
36
37
N
L3
L2
L1
I
1
30
31
I
2
32
33
I
3
34
35
I
4
36
37
I
2
32
33
I
3
34
35
I
4
36
37
I
1
30
31
I
2
32
33
I
3
34
35
I
4
36
37
I
1
30
31
I
2
32
33
I
3
34
35
I
4
36
37
L3
L2
L1
I
1
30
31
I
2
32
33
I
3
34
35
I
4
36
37
Three-phase 3-conductor system
Current measurement via 2 current
transformers (Aron circuit) in a three-
phase 3-conductor system
Current measurement via 3 current
transformers in a three-phase 3-con-
ductor system
N
L3
L2
L1
N
L3
L2
L1
L3
L2
L1
L2
L1
I
1
30
31
I
1
30
31
I
2
32
33
I
3
34
35
I
4
36
37
N
L3
L2
L1
I
1
30
31
I
2
32
33
I
3
34
35
I
4
36
37
I
2
32
33
I
3
34
35
I
4
36
37
I
1
30
31
I
2
32
33
I
3
34
35
I
4
36
37
I
1
30
31
I
2
32
33
I
3
34
35
I
4
36
37
L3
L2
L1
I
1
30
31
I
2
32
33
I
3
34
35
I
4
36
37
The device is a multifunctional network analyzer
that,
• Measures and calculates electrical quantities
such as voltage, current, frequency, power,
work, harmonics current, etc. in building instal-
lations, at distribution boards, circuit breakers
and busbar trunking systems.
• Displays and stores measurement results and
transmits them via interfaces.
Brief device description and installation
ATTENTION
Material damage due to disregard of the instal-
lation instructions!
Disregard of the installation instructions can dam-
age or destroy your device.
·
Provide adequate air circulation in your instal-
lation environment and cooling, as needed,
when the ambient temperatures are high.
·
More information on device functions, data
and installation as well as the battery used in
the device can be found in the user manual.
Mount the measurement device in a switchboard
cabinet or small distribution board according
to DIN 43880 (any mounting orientation) on a
35 mm (1.38 in) DIN rail (for type, see Technical
Data) as follows:
1. Plug the bus connector included in the scope
of delivery into the sockets on the bottom of the
measurement device.
2. Push your measurement device with the bus
connector sideways onto the DIN rail or press it
frontally onto the DIN rail until the bottom bolt
engages.
Fig. Device with bus connector on DIN rail
Bus connector
DIN rail
Bottom bolt
2.
1.
INFORMATION
Indicates procedures in which there is
no
hazard of
personal injury or material damage.
Recommendation:
Use the GridVis
®
software to configure the trans-
former ratios for residual current transformers.
0..30 mA
Safety information in the installation manual is
marked by a warning triangle and, in dependence
on the degree of hazard, is displayed as follows:
WARNING
Warns of a potentially hazardous situation which, if
not avoided, could result in serious injury or death.
The data transfer using the OPC UA protocol
takes place via the Ethernet interfaces of your
device.
The Ethernet interface and the data transfer using
the OPC UA protocol can be configured conve-
niently in the GridVis
®
software.
Fig. Configuration menu item
Fig. Configuration window
Fig. Configuration window with the
entries Ethernet Config. A and B
(in Dedicated mode).
Fig. Ethernet (TCP/IP) window
Fig. Current transformer window
N
L3
L2
L1
N
V1
V2
V3
N
V1
V2
V3
N
V1
V2
V3
N
V1
V2
V3
N
V1
V2
V3
N
L3
L2
L1
N
V1
V2
V3
N
L3
L2
L1
L2
L1
L3
L2
L1
N
V1
V2
V3
L3
L2
L1
L3
L2
L1
N
V1
V2
V3
N
L3
L2
L1
N
L3
L2
L1
N
L3
L2
L1
L3
L2
L1
L2
L1
I
1
30
31
I
1
30
31
I
2
32
33
I
3
34
35
I
4
36
37
N
L3
L2
L1
I
1
30
31
I
2
32
33
I
3
34
35
I
4
36
37
I
2
32
33
I
3
34
35
I
4
36
37
I
1
30
31
I
2
32
33
I
3
34
35
I
4
36
37
I
1
30
31
I
2
32
33
I
3
34
35
I
4
36
37
L3
L2
L1
I
1
30
31
I
2
32
33
I
3
34
35
I
4
36
37
N
L3
L2
L1
N
L3
L2
L1
L3
L2
L1
L2
L1
I
1
30
31
I
1
30
31
I
2
32
33
I
3
34
35
I
4
36
37
N
L3
L2
L1
I
1
30
31
I
2
32
33
I
3
34
35
I
4
36
37
I
2
32
33
I
3
34
35
I
4
36
37
I
1
30
31
I
2
32
33
I
3
34
35
I
4
36
37
I
1
30
31
I
2
32
33
I
3
34
35
I
4
36
37
L3
L2
L1
I
1
30
31
I
2
32
33
I
3
34
35
I
4
36
37
N
L3
L2
L1
N
V1
V2
V3
N
V1
V2
V3
N
V1
V2
V3
N
V1
V2
V3
N
V1
V2
V3
N
L3
L2
L1
N
V1
V2
V3
N
L3
L2
L1
L2
L1
L3
L2
L1
N
V1
V2
V3
L3
L2
L1
L3
L2
L1
N
V1
V2
V3
N
L3
L2
L1
Connection capacity of the terminals (supply voltage)
Connectible conductors.
Only connect one conductor per terminal point!
Single core, multi-core,
fine-stranded
0.2 - 2.5 mm
2
, AWG 26-12
Wire ferrules (non-insulated)
· Recommended strip length
0.2 - 2.5 mm
2
, AWG 26-12
· 10 mm (0.3937 in)
Wire ferrules (insulated) *
· Recommended strip length **
0.2 - 2.5 mm
2
, AWG 26-12
· 12 mm
(≤1.5 mm
2
), 10 mm
(>1.5 mm
2
) /
0.47 in
(≤1.5 mm
2
), 0.39 in
(>1.5 mm
2
)
Wire ferrules:
Contact sleeve length **
8 - 12 mm (0.31 - 0.47 in)
*
... Applies to wire ferrules with a maximum plastic collar outer
diameter of up to 4.5 mm (0.18 in).
**
.. Depending on the type of wire ferrules used (ferrule
manufacturer).
Connection capacity of the terminals
(digital inputs/outputs, analog output)
Single core, multi-core,
fine-stranded
0.2 - 1.5 mm
2
, AWG 24-16
Wire ferrules (non-insulated)
0.2 - 1.5 mm
2
, AWG 26-16
Wire ferrules (insulated)
0.2 - 1 mm
2
, AWG 26-18
Tightening torque
0.2 - 0.25 Nm (1.77 - 2.21 lbf in)
Strip length
7 mm (0.2756 in)
Connection capacity of the terminals (current measure-
ment)
Connectible conductors.
Only connect one conductor per terminal point!
Single core, multi-core,
fine-stranded
0.2 - 2.5 mm
2
, AWG 26-12
Wire ferrules (non-insulated)
· Recommended strip length
0.2 - 2.5 mm
2
, AWG 26-12
· 10 mm (0.3937 in)
Wire ferrules (insulated) *
· Recommended strip length **
0.2 - 2.5 mm
2
, AWG 26-12
· 12 mm
(≤1.5 mm
2
), 10 mm
(>1.5 mm
2
) /
0.47 in (≤1.5 mm
2
), 0.39 in
(>1.5 mm
2
)
Wire ferrules:
Contact sleeve length **
8 - 12 mm (0.31 - 0.47 in)
Tightening torque
Screw flange
0.2 Nm (1.77 lbf in)
*
... Applies to wire ferrules with a maximum plastic collar outer
diameter of up to 4.5 mm (0.18 in).
**
.. Depending on the type of wire ferrules used (ferrule
manufacturer).
Connection capacity of the terminals (RS-485)
Single core, multi-core,
fine-stranded
0.2 - 1.5 mm
2
, AWG 24-16
Wire ferrules (non-insulated)
0.2 - 1.5 mm
2
, AWG 26-16
Wire ferrules (insulated)
0.2 - 1 mm
2
, AWG 26-18
Tightening torque
0.2 - 0.25 Nm (1.77 - 2.21 lbf in)
Strip length
7 mm (0.2756 in)
Connection capacity of the terminals
(voltage measurement)
Connectible conductors
Only connect one conductor per terminal point!
Single core, multi-core,
fine-stranded
0.08 - 4 mm
2
, AWG 28-12
Wire ferrules
(insulated/non-insulated)
0.25 - 2.5 mm
2
, AWG 24-14
Strip length
8-9 mm (0.3150 - 0.3543 in)
Connection capacity of the terminals -
Multifunction channels (RCM, Temp.)
Connectible conductors.
Only connect one conductor per terminal point!
Single core, multi-core,
fine-stranded
0.2 - 1.5 mm
2
, AWG 24-16
Wire ferrules (non-insulated)
0.2 - 1.5 mm
2
, AWG 26-16
Wire ferrules (insulated)
0.2 - 1 mm
2
, AWG 26-18
Tightening torque
0.2 - 0.25 Nm (1.77 - 2.21 lbf in)
Strip length
7 mm (0.2756 in)
Connection capacity of the terminals (functional earth A/D)
Connectible conductors.
Only connect one conductor per terminal point!
Single core, multi-core,
fine-stranded
0.2 - 4 mm
2
, AWG 24-12
Wire ferrules (non-insulated)
0.2 - 4 mm
2
, AWG 24-12
Wire ferrules (insulated)
0.2 - 2.5 mm
2
, AWG 26-14
Tightening torque
0.4 - 0.5 Nm (3.54 - 4.43 lbf in)
Strip length
7 mm (0.2756 in)
Configure the Ethernet (TCP/IP) settings using the function
buttons as described in step 12 "Operation and button
functions".
Residual current measurement (RCM)
Overload for 1 s
5 A
Permanent overload
1 A
Norm
IEC/TR 60755 (2008-01),
Type A / Type B and B+ (via corre-
sponding current transformers)
Technical data
General
Net weight
420 g (0.926 lb)
Device dimensions
Approx. B = 144 mm (5.67 in), H =
90 mm (3.54 in),
D = 76 mm (2.99 in)
Battery
Type: Lithium CR2032, 3 V
(UL1642 approval)
Integrated memory
4 GB
Backlight service life
40000 h
(50% of the start brightness)
Mounting orientation
As desired
Fastening/mounting -
Suitable DIN rails - 35 mm
(1.38 in)
· TS 35/7.5 according to EN 60715
· TS 35/10
· TS 35/15 x 1.5
Impact resistance
IK07 according to IEC 62262
Transport and storage
The following specifications apply for devices transported and
stored in the original packaging.
Free fall
1 m (39.37 in)
Temperature
-25 °C (-13 °F) to +70 °C (158 °F)
Relative humidity
5 to 95% at 25 °C (77 °F),
no condensation
Environmental conditions during operation
The device:
• Is for weather-protected and stationary use.
• Fulfills operating conditions according to DIN IEC 60721-3-3.
• Has protection class II according to IEC 60536 (VDE 0106,
part 1),
a ground wire connection is not required!
Rated temperature range
-10 °C (14 °F) to +55 °C (131 °F)
Relative humidity
5 to 95% at 25 °C (77 °F),
no condensation
Operating elevation
(for overvoltage categories,
see voltage and current
measurement)
2000 m (6562 ft) above sea level
4000 m (13,124 ft) above sea level
Pollution degree
2
Ventilation
No forced ventilation required.
Protection against foreign
matter and water
IP20 according to EN60529
Supply voltage
Nominal range
DC: 24 V, PELV
Operating range
+/-10% of nominal range
Power consumption
max. 4 W
Maximum power
consumption with 10
modules
12 W (UMG 801 at 4 W plus
10 modules at 0.8 W each)
Recommended overcurrent
protective device for line
protection
2-6 A, (Char. B), IEC/UL approval
19
Configuring voltage transformers
17
1. Press function button 1
ESC
to open
the menu.
2. Use buttons 2 “
5
” and 5 “
6
” to select the
menu item
Configuration
and confirm with
button 3
Enter
.
3. In the
Configuration
window, use buttons 2
“
5
” and 5 “
6
” to select the item
Voltage
transformer
and confirm with button 3
Enter
.
4. The
voltage transformer
window appears.
5. In the
Voltage transformer
window, select the
item
Transformer 1..4
(voltage measurement
inputs L1 to L4) and press button 3,
Enter
.
6. The item for the primary side of the transform-
er 1..4 “blinks”.
7. Use buttons 4 (
) and 6 (
) to change the
position of the digit to be set and buttons 2
(
5
) and 5 (
6
) to change the digit (-1/+1).
8. Confirm your entries with button 3
Enter
or
end the action by pressing button 1
ESC
.
9. Use button 6 (
) to go to the configuration
of the secondary side of the transformer 1..4
(voltage measurement inputs L1 to L4).
10. Configure the secondary side of voltage trans-
formers 1..4 in the same way.
11. Confirm your entries with button 3
Enter
or end
the action by pressing button 1
ESC
.
12. When you have finished entering data, press
button 1
ESC
to return to the
Menu
window.
Fig. Voltage transformer window
ATTENTION
Faulty cross currents, incorrect measure-
ments, and even damage to the device and/or
your system due to lack of galvanic isolation!
A lack of galvanic isolation of active external cur-
rent transformers (or other current sensors) on the
multifunction channels from the supply voltage
of the device can lead to faulty cross currents,
incorrect measurements or even damage to your
device and/or system.
· Do
not
take the auxiliary voltage supply of
active external current transformers (or other
current sensors) on the multifunction channels
from the supply voltage of the device! For each
active current transformer, use galvanically
isolated power supplies (secondary side).
· Do
not
ground passive current transformers on
the multifunction channels! Observe the usage
information of the current transformer manu-
facturer.
N
L3
L2
L1
N
V1
V2
V3
N
V1
V2
V3
N
V1
V2
V3
N
V1
V2
V3
N
V1
V2
V3
N
L3
L2
L1
N
V1
V2
V3
N
L3
L2
L1
L2
L1
L3
L2
L1
N
V1
V2
V3
L3
L2
L1
L3
L2
L1
N
V1
V2
V3
N
L3
L2
L1
N
L3
L2
L1
N
V1
V2
V3
N
V1
V2
V3
N
V1
V2
V3
N
V1
V2
V3
N
V1
V2
V3
N
L3
L2
L1
N
V1
V2
V3
N
L3
L2
L1
L2
L1
L3
L2
L1
N
V1
V2
V3
L3
L2
L1
L3
L2
L1
N
V1
V2
V3
N
L3
L2
L1
Three-phase 4-conductor systems
with grounded neutral conductor
Three-phase 4-conductor
systems
with non-grounded neutral conduc-
tor (IT networks)
Three-phase 3-conductor
systems
ungrounded
Three-phase 3-conductor
systems
with grounded phase
L1
L2
L3
E
E
N
E
L1
L2
L3
E
N
R
L1
L2
L3
E
E
L1
L2
E
E
L
N
E
E
L1
L2
L3
E
E
L1
L2
N
E
E
L1
L2
L3
E
E
N
E
L1
L2
L3
E
N
R
L1
L2
L3
E
E
L1
L2
E
E
L
N
E
E
L1
L2
L3
E
E
L1
L2
N
E
E
L1
L2
L3
E
E
N
E
L1
L2
L3
E
N
R
L1
L2
L3
E
E
L1
L2
E
E
L
N
E
E
L1
L2
L3
E
E
L1
L2
N
E
E
L1
L2
L3
E
E
N
E
L1
L2
L3
E
N
R
L1
L2
L3
E
E
L1
L2
E
E
L
N
E
E
L1
L2
L3
E
E
L1
L2
N
E
E
IEC
UL-N / UL-L: 480 VLN / 830 VLL
UL-L: 690 VLL
UL-L: 830 VLL
UL
UL-N / UL-L: 347 VLN / 600 VLL
UL-L: 600 VLL
UL-L: 600 VLL
Functional earth
INFORMATION
The functional earthing is a functional part and essential
for the regular operation of the electrical system.
INFORMATION
For a PE/N measurement, connect measuring
input A as the functional earth. Do not use a
green-yellow wire for this, as the conductor has
no protective function!
INFORMATION
Before you start with the DIN rail mounting and
cabling of your UMG 801, make sure that the
bus connector is mounted on the bottom of your
UMG 801. Then connect up to 10 modules via bus
connectors.
INFORMATION
Functional earth
·
Connection D
(UMG 801) in TN, TT and IT net-
works must always be connected.
·
Connection A
(UMG 801) only connect in TN and
TT networks (
not in IT networks
)
INFORMATION
· The meter does not have a password (00000000)
ex works.
· For detailed information on configuring a pass-
word, operation, display and button functions of
your device, refer to the user manual.
INFORMATION
Detailed information on all menu items and their
settings can be found in the user manual.
INFORMATION
· The multifunction channels are suitable for con-
necting residual current transformers with a nom-
inal current of up to 30 mA and have the "Current
transformer connection test" function.
· The residual current measurement monitors the
residual currents via external current transformers
and, if a threshold value is exceeded, can trigger
a warning signal. The meter is not an independent
protective device against electric shock!
INFORMATION
Voltage transformer ratios can also be configured in
the device configuration of the GridVis
®
software.
INFORMATION
Optionally configure the current transformer ratios
· in the device configuration of the GridVis
®
software.
· via the measurement device homepage of the basic
device.
INFORMATION
· Consult your network administrator for the correct
Ethernet network settings for your device.
· Descriptions of the communication interfaces can
be found in the user manual.
· Information on the connection and communication
of your device with the software can be found in
the online help for the GridVis
®
software.
INFORMATION
· Consult your network administrator for the correct Ethernet
network settings for your measurement device.
· Descriptions of the communication interfaces can be found
in the user manual.
· Information on the connection and communication of your
measurement device with the software can be found in the
online help for the GridVis
®
software.
Patch cable
Your measurement device has two Ethernet
interfaces (A and B) for communication in Ether-
net networks. There are 2 options to integrate the
measurement device into Ethernet networks:
1.
Measurement device integration in a network
with additional switch function (switched
mode).
The measurement device is automatical-
ly assigned an IP address by a DHCP server in
an IT network via Ethernet interface A, for exam-
ple. Ethernet interface B has a switch function
via which further devices (hardware components)
can be connected in series. The measurement
device also allows the reverse use of the Ether-
net interfaces (e.g. "B" for the IP address from a
network and "A" for further devices)!
2.
Measurement device integration in 2 different
networks (dedicated mode)
.
The Ethernet interfaces A and B of the mea-
surement device are each assigned different IP
addresses by 2 different networks.
Button Function
· Display menu.
· One step back.
· Cancel action
(ESC)
.
· Repeated actuation leads to the menu.
· Select menu item or position
(up, "
5
").
· Change selection (digit +1).
· Confirm selection
(Enter)
· Select position (to the left, "
").
· Select menu item or position
(down, "
6
").
· Change selection (digit -1).
· Select position (to the right “
”).
Ethernet A
Ethernet B
Recommendation:
Use at least CAT5 cable!
Patch cable
INFORMATION
For configuration of the IP addresses on the measure-
ment device, observe step 13 "Configuring the Ethernet
connection" and step 14 "Communication via TCP/IP".
· In the
Configuration
window, use buttons 2 "
5
"
and 5 "
6
" to select the respective entry of the
Ethernet interface to be configured and confirm
with button 3
Enter
.
· The window for configuring the TCP/IP Ethernet
settings appears (see step 13 "Communication
via TCP/IP").
INFORMATION
Detailed technical data can be found in the user man-
ual for the measurement device at www.janitza.de.
INFORMATION
You can configure current transformer
ratios
conveniently via
· The device menu.
· The GridVis
®
software.
For information on programming the current
transformer ratios, refer to the user manual.
INFORMATION
·
The switched and dedicated modes of the mea-
surement device can be configured in the GridVis
®
software.
·
The default setting of the measurement device is
the switched mode.
·
A mode change only takes effect after a hard reset
(disconnect the measurement device from the sup-
ply voltage while observing the safety regulations)!
ATTENTION
Material damage due to security vulnerabilities in
programs, IT networks and protocols.
Security vulnerabilities can lead to data misuse and
faults and even the standstill of your IT infrastructure.
To protect your IT system, network, data commu-
nications and measurement devices:
·
Inform your network administrator and/or IT
representative.
·
Always keep the meter firmware up to date and
protect the communication to the meter with an
external firewall. Close unused ports.
·
Take protective measures against viruses and
cyber attacks from the Internet, e.g. through
firewall solutions, security updates and virus
protection programs.
·
Eliminate security vulnerabilities and update or
renew existing protection for your IT infrastruc-
ture.
ATTENTION
Material damage due to incorrect network
settings.
Incorrect network settings can cause faults in the IT
network!
Consult your network administrator for the cor-
rect network settings for your device.
Connection of the device with a patch cable (Ethernet interface) via
a switch/router to the OPC UA server and the PC.
PC and device require a fixed IP address.
PC
Patch cable
Patch cable
OPC UA-
Server
PC
Switch/
Router
UMG 801
Patch cable
Patch cable
DHCP
Server
PC
Switch/
Router
The DHCP server automatically assigns IP addresses to device
and PC.
UMG 801
UMG 801
PC connections
The most common connection methods for com-
munication of the measurement device with a PC
(with GridVis
®
software installed) are described
below.
1. Connection to a DHCP server and PC. The
DHCP server automatically assigns IP ad-
dresses to the device and the PC.
2. Connection as master device with an
RS-485 bus structure (Modbus RTU) to a PC
and OPC UA client.
3. PC direct connection to the device. PC and
device require a fixed IP address.
Ethernet
Ethernet
Ethernet
Modbus TCP
Ethernet
Modbus TCP
Patch cable
Ethernet
INFORMATION
With regard to the configuration of the IP addresses
on the measurement device, also observe steps 10
and 12 to 15!
PC
DHCP
Server
UMG 801
Ethernet A
Ethernet B
Switch/
Router
PC
Network A
Dedicated mode: Different IP addresses for Ethernet interfaces A
and B for separate networks.
Network B
DHCP
Server
Switch/
Router
Switched mode: Ethernet interface B of the UMG 801 for con-
necting an Ethernet device. The measurement device also allows
the reverse use of the Ethernet interfaces (A for the Ethernet
device and B for an IP address from a network).
PC
DHCP
Server
Switch/
Router
UMG 801
A
B
e.g.
UMG 96PQ-L
"Switched mode" connection option:
"Dedicated mode" connection option
11
RS-485
(Modbus RTU)