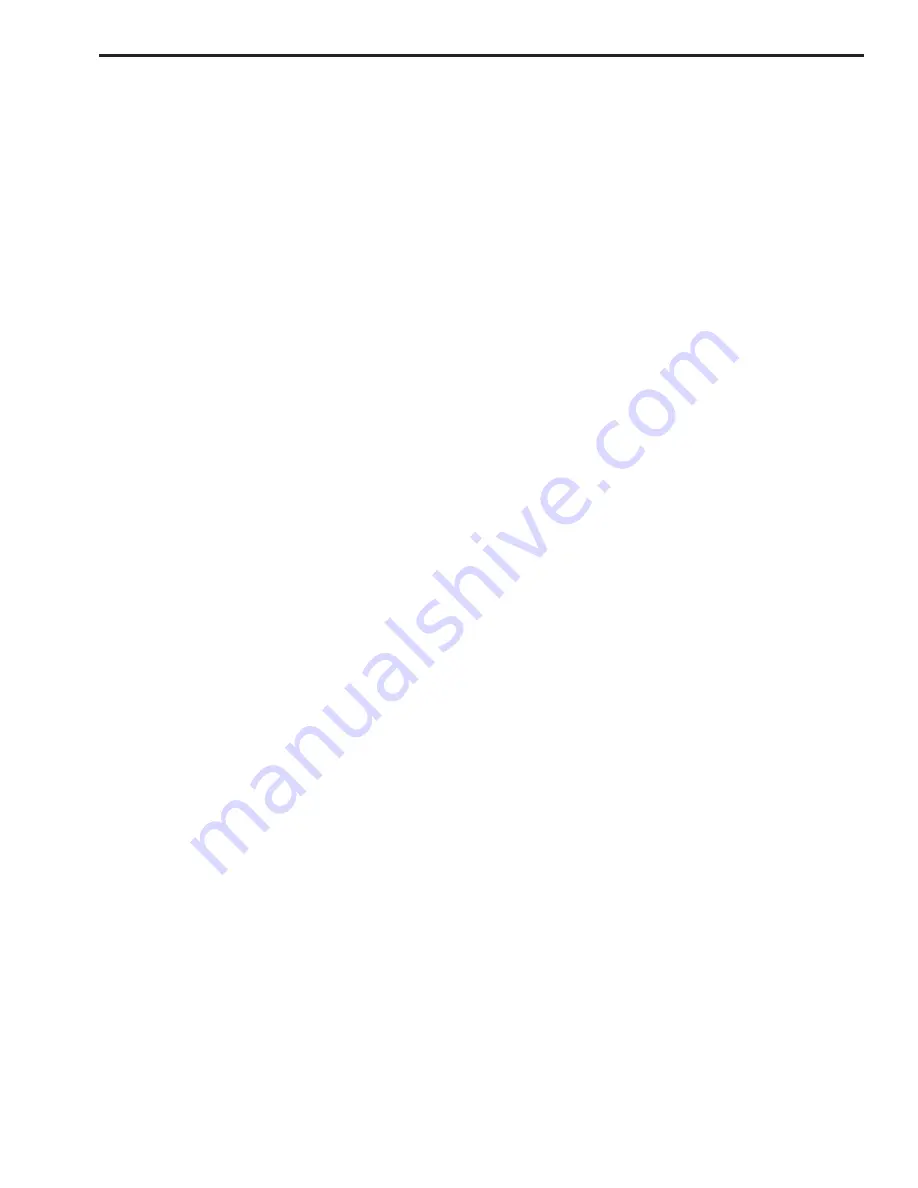
Page 9
Jandy® Pumps
SECTION 8.
Troubleshooting
8.1 Troubleshooting
8.1.1 Jandy strongly recommends that you call a
qualified service technician to perform any
repairs on the filter/pump system. To locate a
qualified technician, chack your local yellow
pages or visit
www.jandy.com
and click on
"Product Support."
8.1.2 The cleaning/circulating system is not working as
well as in the past.
a. Are the skimmer baskets, pump basket
and other screens clean?
b. Has the filter been cleaned recently?
c. Are all the valves adjusted correctly? Too
much equipment on at one time will stop
many cleaners from working (waterfalls, spa
jets, surface returns, etc.).
d. Have you checked the cleaning system
manual to make sure it is adjusted according
to the manufacturer's recommendations.
8.1.3 Are there bubbles present in the pump basket?
a. Check the pool or spa water level to make
sure it is at the proper level and that air is not
being drawn into the suction piping. If the
water is normal, continue with the next step.
b. Turn off the pump. Remove the lid. Check
for debris around the lid o-ring seat, as this
will cause air leaks into the system. Clean
the lid o-ring and place on the lid. Hand
tighten the lid to make an air tight seal. Do
NOT
use any tools to tighten the lid. Turn on
the pump.
8.1.4 If there are still air leaks, check the suction side
piping union.
a. While the pump is running, try to tighten the
union. If this does not stop the air leak,
continue to the next step.
b. Turn off the pump.
c. Loosen both unions and slide the pump out
of the way.
d. Remove, clean and replace both union o-
rings.
e. Reposition the pump next to the piping and
secure the union nuts to the pump. With
clean union o-rings, hand tightening of the
unions should create a seal. If the unions still
do not seal,
gently
tighten with a large pair of
tongue-and-groove pliers.
DO NOT
over
tighten.
8.1.5 If there is no air in the system, but the pressure
is still low.
a. It is possible that debris is caught in the
pump impeller. The impeller is what moves
the water and has vanes that can become
blocked with debris. See "Blocked Impeller"
(Section 9.1) under the "Specialty Service"
section of this manual.
8.1.6 If there is nothing blocking the impeller and the
pressure is still low, there are three other
possible reasons for this:
a. The pump has been in an abrasive
environment for a long period of time, and
the impeller and diffuser are showing signs
of wear. If the problem is normal wear on the
impeller and diffuser, have a qualified
service technician replace them.
b. If this is a relatively new installation, it could
be an electrical problem. This problem can
be easily identified by a qualified service
technician. Have the technician check for
loose electrical connections and check the
voltage at the pump motor while it is in
operation. The voltage must be within 10%
of the motor's data plate rating. If it is not,
then a qualified electrician and/or the power
company needs to get involved to resolve the
problem.
c. Pump seal is leaking air. Have a qualified
service technician replace the seal.
8.1.7 The pump is leaking water between the motor
and pump body.
a. This is caused by a damaged or failed
mechanical seal. To solve this problem, the
seal must be replaced. See "Mechanical Seal
Replacement" (Section 9.4) under "Speciality
Service" section of this manual.
8.1.8 The pump gets hot and shuts off periodically.
a. Make sure the motor has plenty of room to
circulate air and keep cool. Have a qualified
electrician check for loose connections and
check the voltage at the pump motor while it
is in operation. The voltage must be within
10% of the motor's data plate rating. If it is
not, then a qualified electrician and/or the
power company needs to get involved to
resolve the problem.