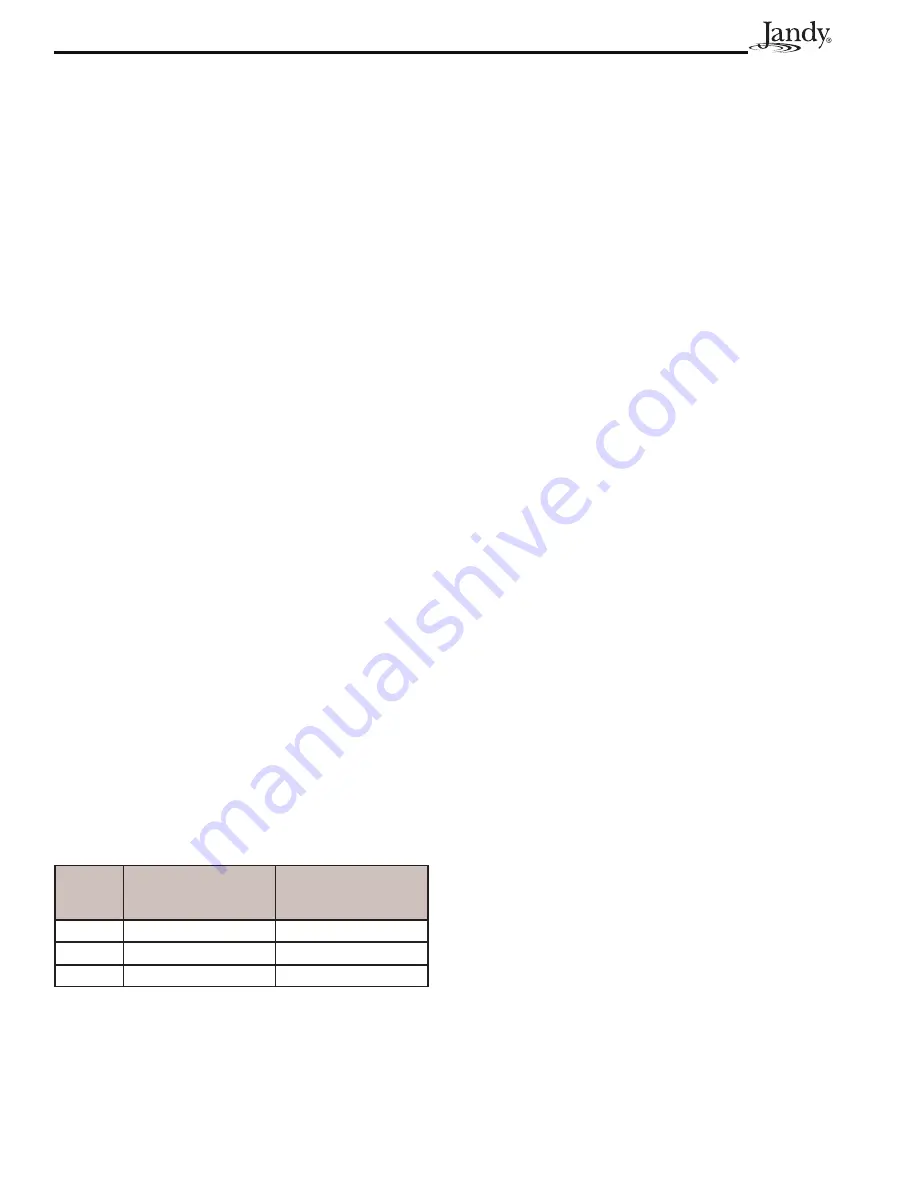
Page 10
FloPro Series Pumps Installation and Operation Manual
3.1.4 Pipe Sizing
3.1.3.1 Suction
Pipe
When the pump is located up to 50 feet from the
pool, the recommended
Schedule 40
minimum pipe size
for the suction side of the pump is 1
½
" for
.75
HP and
2" for
1
to 2 HP. For 2
.5
HP pumps, the recommended
pipe size is 2½".
3.1.3.2 Discharge
Pipe
When the pump is located up to 50 feet from the
pool, the recommended Schedule 40 minimum pipe size
for the discharge side of the pump is 1
½
" for .75 HP and
2" for
1
to 2 HP. For 2
.5
HP pumps, the recommended
pipe size is 2½".
NOTE All pipe sizes (Schedule 40) are able to
withstand the pressures the pump will deliver,
but not necessarily the flow. If the pipe is too
small for the pump, or if the pump is elevated
above water, the maximum gallons per minute
(GPM) may not be delivered. If this happens,
the pump will develop an air pocket (cavitation)
that will make noise, and the life of the pump
may be shortened.
3.1.3.3 Installation
Recommendations
1.
If the pump is located below water level, isolation
valves
must
be installed on both sides of the pump
to prevent the back flow of pool water during any
routine or required servicing.
2.
To help prevent difficulty in priming, install the
suction pipe without high points, which can trap
air. (High points are inverted ‘U’s above the inlet
of a pump. In plumbing, they are commonly
referred to as airlocks.) For installations of
equipment up to 100 feet from the water, refer to
the pipe sizing chart in Table 2. For installations of
equipment more than 100 feet from the water, the
recommended pipe size must be increased to the
next size.
Table 2.
Pipe Sizing Chart for Schedule 40 PVC
Pipe
Size
Maximum Flow
Suction
(8 feet per second)
Maximum Flow
Discharge
(10 feet per second)
1½"
50 GPM (189 LPM)
65 GPM (246 LPM)
2"
85 GPM (322 LPM)
105 GPM (397 LPM)
2½"
120 GPM (454 LPM)
149 GPM (564 LPM)
3.
FHP Pumps come equipped with unions on
both the suction and discharge ports. This
feature simplifies installation and service, and
it eliminates the possibility of leaks at threaded
adapters.
4.
The FHP Pump must be connected to at least two
(2) main drains (suction outlets) for each pool
pump suction line. Each drain must be provided
with covers that are listed or certified to the latest
published version of ANSI/ASME A112.19.8.
The suction outlets of the main drains must be at
least 3 feet apart or at different planes. The suction
outlets can be a drain and skimmer, two (2) drains,
two (2) skimmers, or a skimmer with an equalizer
line installed. For additional details and guidelines,
refer to ANSI/APSP 7, the standard for
Suction
Entrapment Avoidance in Swimming Pools,
Wading Pools, Spas, Hot Tubs, and Catch Basins
.
Check the local codes for proper installation
requirements. Applicable local codes will take
precedence over other codes.
NOTE To prevent entrapment, the system must be
built so that it cannot operate with the pump
drawing water from only one (1) main drain. At
least two (2) main drains
must
be connected
to the pump when it is in operation. However,
if two (2) main drains run into a single suction
line, the single suction line may be equipped
with a valve that will shut off both main drains
from the pump.
5.
The piping must be well supported and not forced
together in places where constant stress will be
experienced.
6.
Always use properly sized valves. Jandy Diverter
Valves and Jandy Ball Valves typically have the
best flow capabilities.
7.
Use the fewest fittings possible. Every additional
fitting has the effect of moving the equipment
farther away from the water.
NOTE If more than 10 suction fittings are needed, the
pipe size must be increased.
8.
Every new installation must be pressure tested
according to local codes. See
Section 3.3, Pressure
Testing.
3.2 Electrical
Installation
3.2.1 Voltage Checks
The correct voltage, as specified on the pump data
plate, is necessary for proper performance and long
motor life. The incorrect voltage will decrease the
pump’s ability to perform and can cause overheating,
reduce the motor life, and result in higher electric bills.
It is the responsibility of the electrical installer
to provide data plate operating voltage to the pump
by ensuring proper circuit sizes and wire sizes for the
specific application.
Содержание FHPM FloPro Series
Страница 2: ......