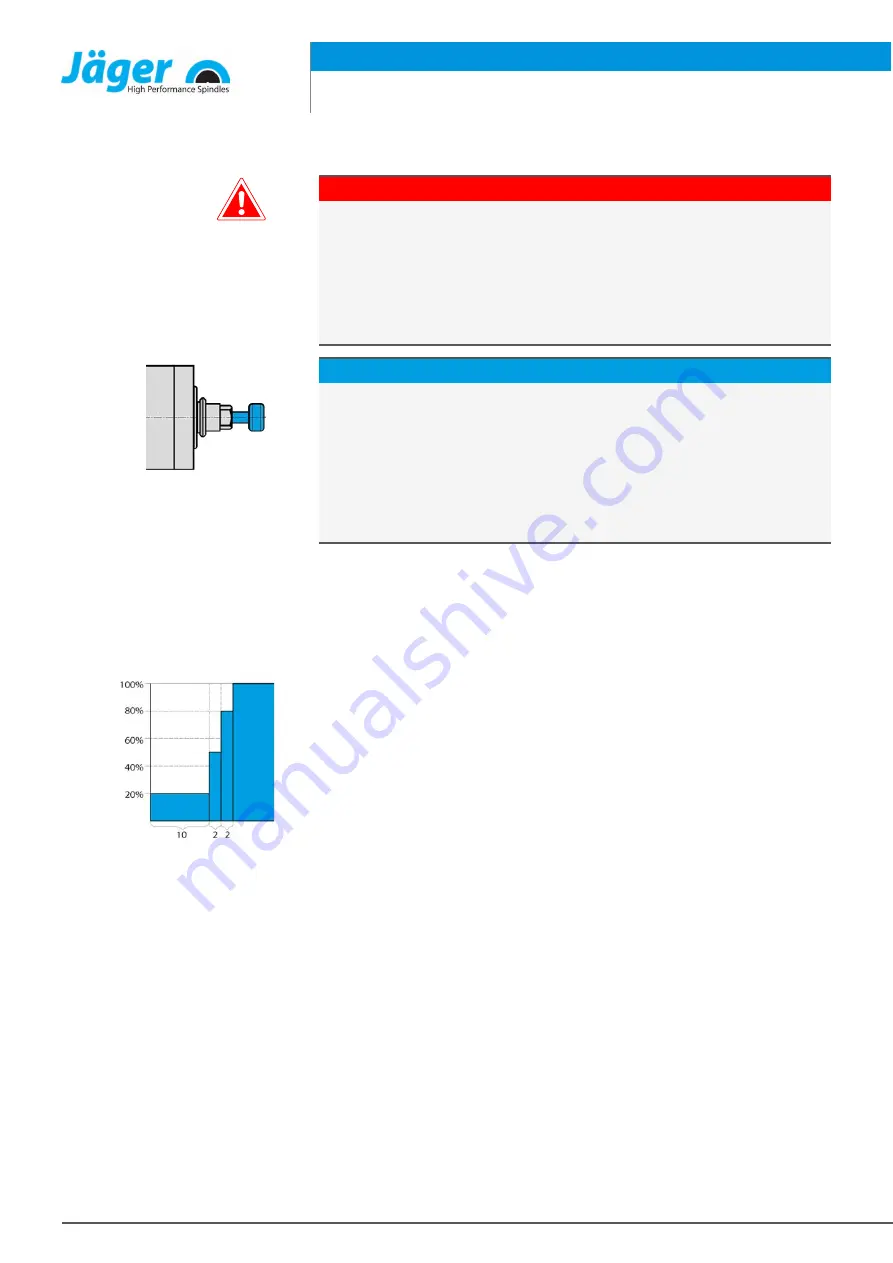
Commissioning
Item no. 10206007, Revision 00
32 ( 44 )
9
Commissioning
DANGER: Due to flying parts.
If the speed is selected incorrectly, the HF spindle or the tool may be de-
stroyed and their fragments may be flung out.
u
Note the maximum speed for the selected tool.
u
Note the maximum speed for the HF spindle.
u
The maximum permissible speed of the HF spindle for commissioning /
processing is always the
lowest
specified speed.
Example of design: Inserting the
shank
Note: Ensure functionality.
u
Never operate the HF spindle without a clamped tool shank.
If no tool shank is clamped:
q
The clamping system is damaged by the centrifugal forces.
q
The clamping system is shifted.
q
The balance of the HF spindle is affected.
q
The bearing is damaged.
Ü
Turn the shaft of the spindle at least ten times by hand.
Ü
Before storing and before commissioning only clean the cooling duct with
compressed air.
9.1
Running-in schedule
Duration of load (minutes)
Max. load (%)
Ü
Put the HF spindle into operation with a clamped tool (without machining)
for approx. 10 minutes.
Ü
The speed in this case should be no more than 20% of the maximum per-
missible speed for the HF spindle.
Ä
See definition: Max. permissible speed
Ü
Allow the HF spindle to run for approx. 2 minutes at a maximum of 50% of
the maximum permissible speed.
Ü
Operate the HF spindle for approx. 2 more minutes at a maximum of 80%
of the maximum permissible speed.
The HF spindle is now ready for operation.
9.2
Daily start-up
Proceed as follows to preheat the grease lubrication of the bearing and to
protect it:
Ü
Operate the HF spindle with a clamped tool (without machining).
Ä
Approx. 2 minutes.
Ä
At maximum 50 % of the maximum permissible speed.
(See Commissioning
section)
This brings the HF spindle to its operating temperature.
9.3
Shutdown signal
Use the option on the frequency converter of detecting the shutdown signal
from the shaft and forwarding this to the machine controller for evaluation.